C channel roll forming machines are a critical component of the manufacturing industry, used to produce a wide range of products from automotive parts to construction materials. As with any industrial equipment, regular maintenance is essential to ensure that these machines operate safely and efficiently. In this post, we will explore the importance of regular maintenance for C channel roll forming machines and discuss the benefits of a well-maintained machine. So let’s delve into the world of industrial maintenance and learn how proper maintenance can improve the safety, efficiency, and longevity of these essential machines.
Importance of Regular Maintenance for C channel roll forming machines
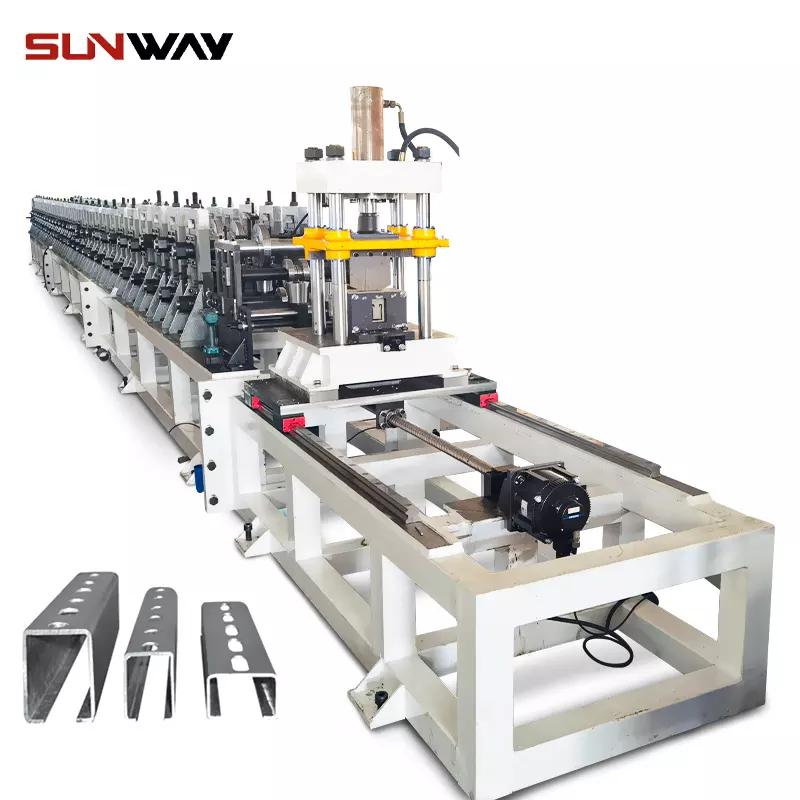
Regular maintenance is critical to ensuring the longevity, safety, and efficiency of C channel roll forming machines. Here are some of the key reasons why regular maintenance is so important:
- Extending the Lifespan of the Machine: Regular maintenance can help to extend the lifespan of the machine by reducing wear and tear on critical components. This can help to reduce the need for costly repairs and replacements, as well as improve the overall performance and reliability of the machine.
- Preventing Breakdowns: Regular maintenance can help to prevent breakdowns by identifying potential issues before they become major problems. This can help to reduce downtime and increase productivity, as well as reduce the risk of damage to the machine.
- Reducing Downtime: Downtime can be costly for manufacturers, both in terms of lost productivity and repair costs. Regular maintenance can help to reduce downtime by keeping the machine running smoothly and preventing unexpected breakdowns.
- Improving Safety: Regular maintenance can help to improve the safety of C channel roll forming machines by identifying and addressing potential safety hazards. This can help to reduce the risk of accidents or injuries in the workplace, protecting both workers and the machine itself.
Overall, regular maintenance is critical to ensuring the longevity, safety, and efficiency of C channel roll forming machines. By investing in regular maintenance, manufacturers can save money on repairs and replacements, increase productivity, and improve the safety of their workplace.
Maintenance Checklist on C channel roll forming machines
Here is a checklist of the maintenance tasks that should be performed regularly on C channel roll forming machines:
- Cleaning: Regular cleaning of the machine is essential to prevent dirt, debris, and other contaminants from accumulating on critical components. This can include wiping down the machine, cleaning out the cutting tool, and removing debris from the rollers.
- Lubrication: Lubrication is essential to prevent friction and wear on critical components of the machine. This can include oiling the bearings, lubricating the rollers, and greasing the drive chains.
- Checking for Wear and Tear: Regularly checking for wear and tear on the machine can help to identify potential issues before they become major problems. This can include inspecting the belts, gears, and rollers for signs of wear, and replacing any worn components.
- Inspections: Regular inspections of the machine can help to identify potential safety hazards and other issues. This can include checking for loose bolts, inspecting the electrical wiring, and ensuring that all safety guards and covers are in place.
- Calibration: Calibrating the machine is essential to ensure that it is producing parts to the correct specifications. This can include checking the accuracy of the cutting tool, adjusting the rollers, and ensuring that the machine is producing parts to the correct tolerances.
By following this maintenance checklist, manufacturers can help to ensure that their C channel roll forming machines are operating safely and efficiently, reducing the risk of downtime and other issues, and extending the lifespan of the machine.
Common Maintenance Issues with C channel roll forming machines
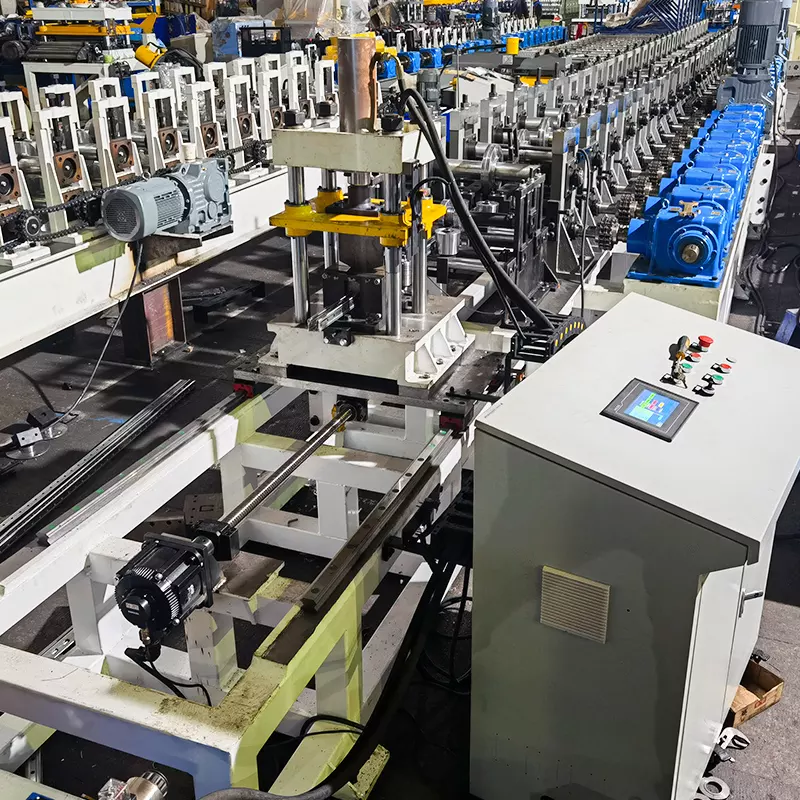
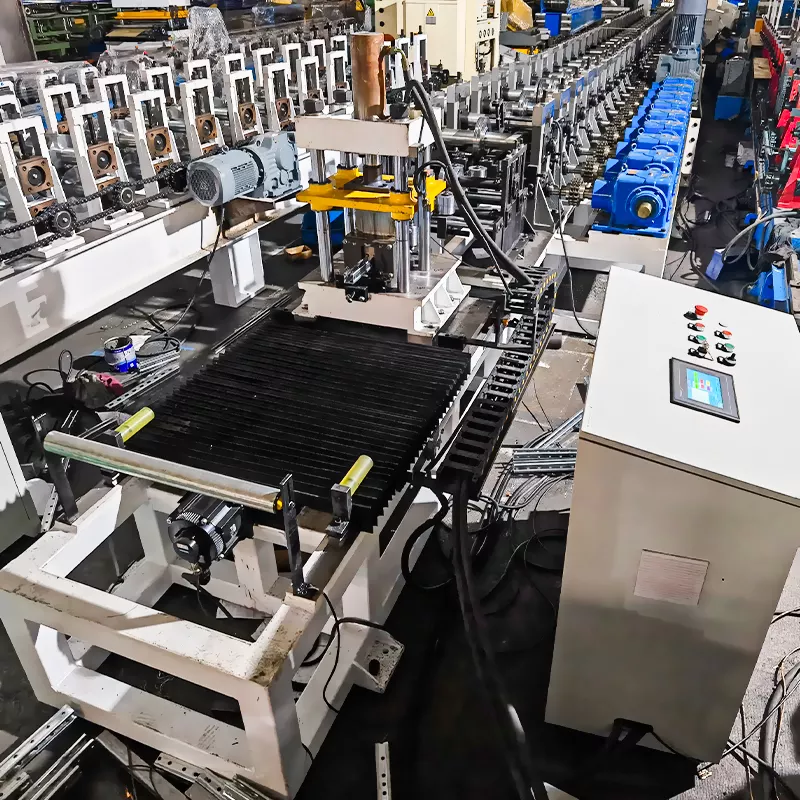
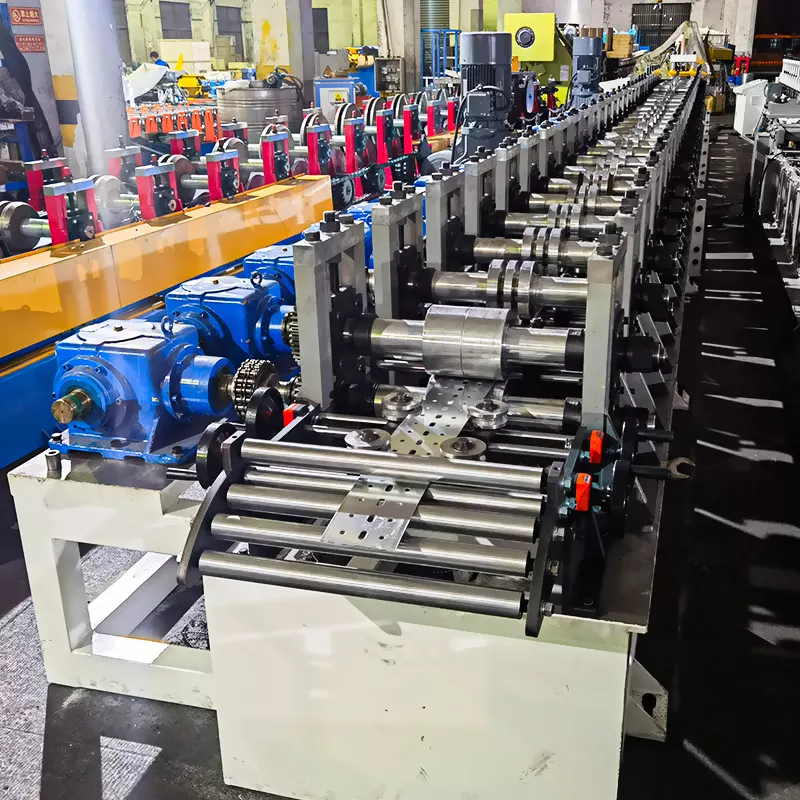
There are several common maintenance issues that can occur with C channel roll forming machines. Here are some examples of these issues and how they can be prevented and addressed through regular maintenance:
- Loose Belts: Over time, belts can become loose or worn, which can cause the machine to operate less efficiently or even break down. Regular inspection and adjustment of the belts can help to prevent this issue.
- Worn Gears: Gears can become worn or damaged over time, which can cause the machine to produce parts that are out of tolerance or to break down entirely. Regular inspection and replacement of worn gears can help to prevent this issue.
- Damaged Rollers: Rollers can become damaged or misaligned, which can cause the machine to produce parts that are out of tolerance or to break down. Regular inspection and replacement of damaged rollers can help to prevent this issue.
- Dirty or Clogged Cutting Tool: The cutting tool can become dirty or clogged with debris, which can cause the machine to produce parts that are out of tolerance or to break down. Regular cleaning and maintenance of the cutting tool can help to prevent this issue.
- Electrical Issues: Electrical issues, such as loose wiring or damaged components, can cause the machine to malfunction or break down entirely. Regular inspection and maintenance of the electrical system can help to prevent this issue.
Overall, regular maintenance can help to prevent these and other common maintenance issues with C channel roll forming machines. By identifying and addressing potential issues before they become major problems, manufacturers can ensure that their machines operate safely and efficiently, reducing downtime and other issues, and extending the lifespan of the machine.
Cost-Benefit Analysis of regular maintenance for C channel roll forming machines
Performing regular maintenance on C channel roll forming machines can provide significant cost savings and benefits for manufacturers. Here is a cost-benefit analysis of regular maintenance for these machines:
Costs of Maintenance:
Cost of maintenance personnel, supplies, and equipment.
Benefits of Maintenance:
- Reduced Downtime: Regular maintenance can help to prevent unexpected breakdowns, reducing the amount of downtime required for repairs and maintenance.
- Increased Efficiency: Regular maintenance ensures that the machine is operating at optimal efficiency, reducing the amount of time required to produce each part and increasing overall productivity.
- Longer Lifespan: Regular maintenance can help to extend the lifespan of the machine, reducing the need for costly repairs and replacements and ultimately saving money in the long run.
- Improved Safety: Regular maintenance can help to identify and address potential safety hazards, reducing the risk of accidents and injuries in the workplace.
Cost Savings:
- Reduced Downtime: By reducing downtime, manufacturers can save money on lost productivity, missed deadlines, and other related costs.
- Increased Efficiency: By increasing efficiency, manufacturers can produce more parts in less time, reducing labor costs and increasing revenue.
- Longer Lifespan: By extending the lifespan of the machine, manufacturers can save money on repairs and replacements, as well as reduce the need for new capital expenditures.
- Improved Safety: By improving safety, manufacturers can reduce the risk of accidents and injuries, reducing the costs associated with worker’s compensation claims and lawsuits.
Overall, the cost-benefit analysis of regular maintenance for C channel roll forming machines indicates that the benefits of maintenance far outweigh the costs. By investing in regular maintenance, manufacturers can save money on repairs, reduce downtime, increase efficiency, and improve the safety of their workplace.
Regular maintenance is crucial for the longevity, safety, and efficiency of C channel roll forming machines. By following a maintenance checklist, addressing common maintenance issues, and conducting cost-benefit analysis, manufacturers can ensure that their machines operate safely and efficiently, reducing downtime and other issues, and extending the lifespan of the machine.