Overview of High-Speed Roll Forming Machines
Roll forming machines have revolutionized the manufacturing industry by allowing for the efficient and precise shaping of metal. High-speed roll forming machines take this a step further by combining speed with accuracy, making them indispensable in industries requiring high volumes of metal parts. Whether you are in automotive, construction, or appliance manufacturing, understanding the capabilities and benefits of high-speed roll forming machines can significantly enhance your production processes.
High-speed roll forming machines are designed to handle complex profiles and long production runs with minimal downtime. They excel in producing consistent, high-quality metal profiles at impressive speeds. This guide will delve into the specifics of these machines, including their types, working processes, key components, applications, installation, operation, and maintenance. We’ll also cover how to choose the right supplier and provide a detailed comparison of advantages and limitations.
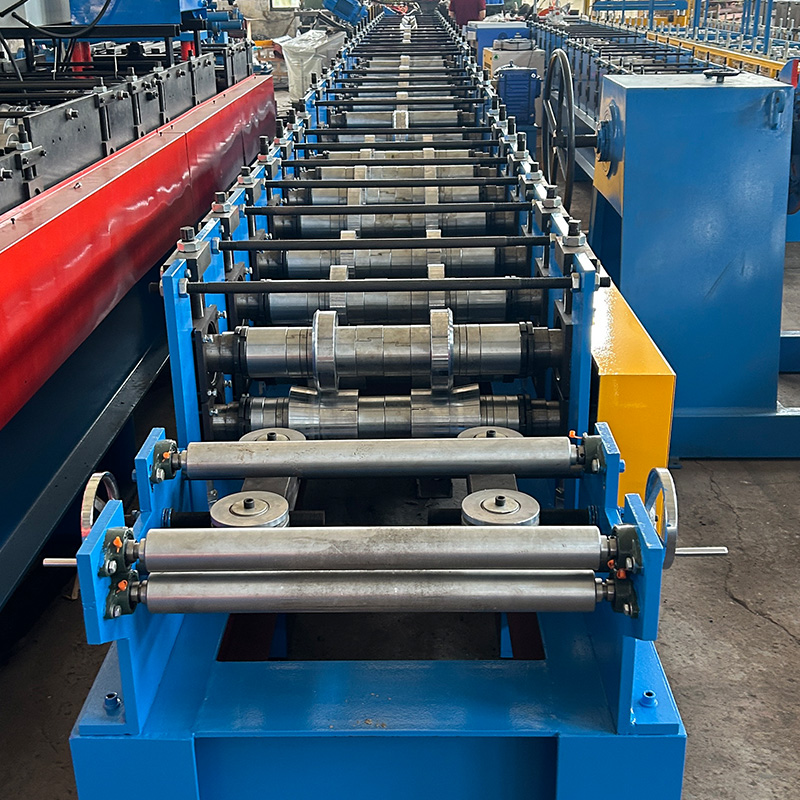
Types of High-Speed Roll Forming Machines
High-speed roll forming machines come in various types, each suited for different applications and materials. Here’s a detailed table of the different types available:
Type of Roll Forming Machine | Description |
---|---|
Single-Head Roll Forming Machine | Ideal for small-scale production, offering flexibility and ease of use. |
Multi-Head Roll Forming Machine | Suitable for large-scale production, providing high speed and efficiency. |
Inline Roll Forming Machine | Integrates with other manufacturing processes for seamless production. |
Stand-Alone Roll Forming Machine | Operates independently, perfect for customized production needs. |
Pre-Punch Roll Forming Machine | Includes punching operations before forming, enhancing precision and functionality. |
Post-Punch Roll Forming Machine | Punches holes after the forming process, ensuring accuracy in the final product. |
Duplex Roll Forming Machine | Features two sets of roll formers, doubling production capacity. |
Hybrid Roll Forming Machine | Combines features of different types for versatile manufacturing solutions. |
Variable Speed Roll Forming Machine | Allows adjustment of speed for different materials and production requirements. |
Precision Roll Forming Machine | Designed for high-precision applications, ensuring tight tolerances. |
Working Process of High-Speed Roll Forming Machines
The operation of a high-speed roll forming machine involves several stages, each crucial for the final product’s quality and consistency. Here’s a step-by-step breakdown:
- Material Loading: Metal coils are loaded onto the decoiler, which feeds the material into the machine.
- Straightening: The material passes through a straightener to remove any initial coil set and ensure it’s flat.
- Feeding: The straightened material is fed into the roll forming machine, where it undergoes a series of consecutive bending operations.
- Forming: Through a series of precisely positioned rollers, the metal is gradually shaped into the desired profile. The speed and pressure of the rollers are controlled to maintain quality.
- Cutting: Once the metal profile is formed, it is cut to the required length using a flying cutoff mechanism that works synchronously with the roll forming process.
- Final Processing: Additional operations such as punching, notching, or embossing can be performed either inline or post-forming.
- Unloading: The finished product is unloaded and collected for further inspection and packaging.
Key Components, Machine Speed, Efficiency, and Customization
High-speed roll forming machines comprise various components, each playing a pivotal role in the machine’s performance and output. Here’s a detailed table highlighting these aspects:
Component | Description |
---|---|
डेकोइलर | Holds and feeds the metal coil into the machine. |
Straightener | Ensures the metal is flat and ready for forming. |
Roll Forming Stands | Houses the rollers that shape the metal. |
Rollers | Gradually bend the metal into the desired profile. |
Cutoff System | Cuts the formed metal to the required length. |
नियंत्रण प्रणाली | Manages the machine’s operations, speed, and precision. |
Hydraulic System | Powers the various mechanical components, ensuring smooth operation. |
Punching Unit | Adds holes or other features to the metal profile during or after forming. |
Speed | Can range from 20 meters per minute to over 100 meters per minute. |
Efficiency | High-speed machines can significantly reduce production time and increase output. |
अनुकूलन | Machines can be tailored to specific production needs, including profile shape and additional processing capabilities. |
-
नालीदार पैनल रोल बनाने की मशीन
-
लाइट गेज स्टील रोल बनाने की मशीन
-
सी सेक्शन ब्रेसिंग ओमेगा स्टोरेज रैक अपराइट पोस्ट रोल बनाने की मशीन
-
स्टील बॉक्स प्लेट रोल बनाने की मशीन बनाना
-
शेल्फ कॉलम के लिए बॉक्स बीम स्टील रोल बनाने की मशीन
-
पैलेट रैकिंग स्टेप बीम पी बीम रोल बनाने की मशीन
-
गोदाम शेल्फ ईमानदार रोल बनाने की मशीन
-
दीन रेल रोल बनाने की मशीन
-
ओमेगा शहतीर रोल बनाने की मशीन
Applications and Uses
High-speed roll forming machines are versatile and find applications across various industries. Here’s a detailed look at where these machines are most beneficial:
Industry | आवेदन |
---|---|
Automotive | Manufacturing of structural components, chassis parts, and trim profiles. |
Construction | Production of roofing, wall panels, gutters, and framing components. |
Appliances | Fabrication of refrigerator panels, washing machine components, and oven frames. |
Aerospace | Creation of lightweight structural parts and support beams. |
Furniture | Shaping metal parts for frames, supports, and decorative elements. |
Electrical | Forming of conduits, cable trays, and enclosures. |
Agriculture | Manufacturing of machinery components, fencing, and storage structures. |
Energy | Production of solar panel frames, wind turbine components, and pipeline supports. |
Logistics | Fabrication of shelving, racks, and storage systems. |
Transportation | Creation of components for trains, buses, and trucks. |
Installation, Operation, and Maintenance
Proper installation, operation, and maintenance are critical for maximizing the efficiency and lifespan of high-speed roll forming machines. Here’s a comprehensive guide:
Aspect | विवरण |
---|---|
Installation | Ensure a stable foundation, correct alignment, and proper electrical connections. |
Initial Setup | Calibrate the machine, set the rollers, and test with initial runs to ensure accuracy. |
Operation | Train operators on the control system, safety protocols, and troubleshooting. |
Routine Maintenance | Regularly check and lubricate moving parts, inspect rollers, and clean the machine. |
Periodic Inspections | Conduct thorough inspections to identify wear and tear, replace damaged components. |
Software Updates | Keep the control system software up to date to enhance performance and security. |
Safety Checks | Ensure all safety mechanisms are functional, including emergency stops and guards. |
Documentation | Maintain detailed records of maintenance, repairs, and inspections. |
Supplier Support | Utilize supplier resources for troubleshooting, parts replacement, and technical support. |
Suppliers and Price Range Details
Choosing the right supplier is crucial for acquiring a high-quality roll forming machine that meets your needs. Here’s a table with some of the leading suppliers and their price ranges:
Supplier | Price Range | Description |
---|---|---|
सैमको मशीनरी | $100,000 – $500,000 | Offers a wide range of high-speed roll forming machines with custom solutions. |
Dreistern GmbH & Co. KG | $150,000 – $600,000 | Known for high precision and durable machines suited for various industries. |
फॉर्मटेक ग्रुप | $120,000 – $550,000 | Provides machines with advanced automation and customization options. |
Bradbury Group | $130,000 – $580,000 | Specializes in high-speed and high-efficiency roll forming machines. |
Zeman Bauelemente | $140,000 – $600,000 | Offers robust machines with a focus on construction applications. |
Jupiter Roll Forming | $110,000 – $520,000 | Delivers versatile machines with a strong emphasis on customer support. |
T&H Lemont | $125,000 – $570,000 | Provides durable and high-performance roll forming equipment. |
Metform International | $135,000 – $590,000 | Known for innovative designs and reliable machines. |
Yoder Manufacturing | $145,000 – $610,000 | Offers a wide range of machines tailored to specific industrial needs. |
Foshan Hongxin Machinery | $100,000 – $450,000 | Provides cost-effective solutions with reliable performance. |
How to Choose the Right Supplier
Selecting the right supplier involves several considerations. Here’s a detailed table on how to evaluate potential suppliers:
Criteria | Description |
---|---|
Reputation | Research the supplier’s reputation in the industry, including reviews and testimonials. |
अनुभव | Consider the supplier’s experience and track record with high-speed roll forming machines. |
Customization Options | Ensure the supplier can customize the machine to meet your specific needs. |
Technical Support | Evaluate the availability and quality of technical support and after-sales service. |
गुणवत्ता आश्वासन | Check for quality certifications and standards compliance. |
Delivery Time | Assess the supplier’s ability to deliver the machine within your required timeline. |
Training and Installation | Determine if the supplier offers training for operators and installation services. |
Cost and Value | Compare the cost with the features and benefits offered to ensure good value for money. |
Warranty and Maintenance | Review the warranty terms and maintenance services provided by the supplier. |
Innovative Features | Look for suppliers who offer innovative features that can enhance productivity and efficiency. |
Comparing Pros and Cons, Advantages and Limitations
When choosing a high-speed roll forming machine, it’s essential to understand the pros and cons of each option. Here’s a detailed comparison:
Aspect | Advantages | Limitations |
---|---|---|
Speed | High production rates, reduced manufacturing time. | Increased wear and tear, higher maintenance needs. |
Precision | Consistent and accurate profiles, minimal waste. | Requires precise setup and calibration. |
अनुकूलन | Tailored solutions for specific applications. | Higher initial cost for customized features. |
Durability | Robust construction, long lifespan. | May require significant initial investment. |
Versatility | Suitable for a wide range of materials and profiles. | Complex setup for different profiles. |
Automation | Reduced labor costs, increased efficiency. | High upfront cost for automated systems. |
Quality Control | Enhanced product quality, reduced defects. | Requires regular maintenance and monitoring. |
Energy Efficiency | Modern machines are designed to be energy-efficient. | Initial cost may be higher for energy-efficient models. |
Flexibility | Ability to integrate with other processes and equipment. | Integration can be complex and require expert installation. |
Cost-Effectiveness | Lower long-term costs due to reduced labor and waste. | Higher initial purchase price compared to manual or slower machines. |
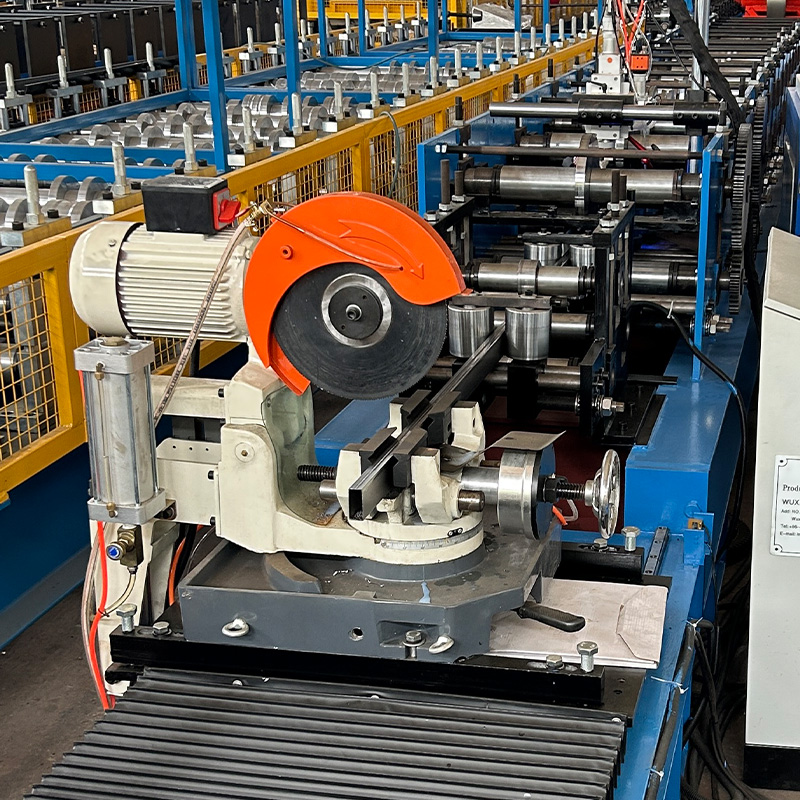
FAQs
To address common questions, here’s an FAQ section:
Question | Answer |
---|---|
What materials can be processed with roll forming machines? | Most metals, including steel, aluminum, and copper, can be processed. |
How does the speed of a roll forming machine impact production? | Higher speeds lead to increased production rates but may require more frequent maintenance. |
Can roll forming machines handle complex profiles? | Yes, high-speed roll forming machines are designed to handle intricate and complex profiles. |
What is the typical lifespan of a high-speed roll forming machine? | With proper maintenance, these machines can last several decades. |
How do I maintain my roll forming machine? | Regular lubrication, inspections, and timely replacement of worn parts are essential for maintenance. |
Is training required to operate these machines? | Yes, proper training is crucial for safe and efficient operation. |
What are the benefits of automation in roll forming? | Automation increases efficiency, reduces labor costs, and enhances precision. |
Can roll forming machines be customized? | Yes, machines can be tailored to specific production requirements and profiles. |
What is the difference between pre-punch and post-punch roll forming machines? | Pre-punch machines punch holes before forming, while post-punch machines do so after forming. |
How do I choose the right roll forming machine for my needs? | Consider factors like production volume, material type, profile complexity, and budget. |