ए heavy duty cable tray roll forming machine is an essential equipment for electricians and electrical contractors to create customized cable trays. This guide provides a comprehensive overview of heavy duty cable tray roll forming machines, including working principles, types, materials, design, customization options, suppliers, installation, operation, maintenance and more.
Overview of Heavy Duty Cable Tray Roll Forming Machines
- Heavy duty cable tray roll forming machines form metal coils into cable trays through a series of progressive bending and forming stations.
- They allow quick, automated and continuous production of cable trays as per customized specifications.
- These machines can handle thick gauge metal coils and form trays up to 1000 mm width, suited for heavy duty applications.
- Key benefits include high production efficiency, consistency, customization flexibility, and ability to work with various materials like steel, stainless steel and aluminum.
- Main applications are in power transmission, telecom, solar farms, warehouses, factories, mines and marine installations.
- Choosing the right heavy duty cable tray forming machine depends on output rate, material type, thickness, tray sizes needed and budget.
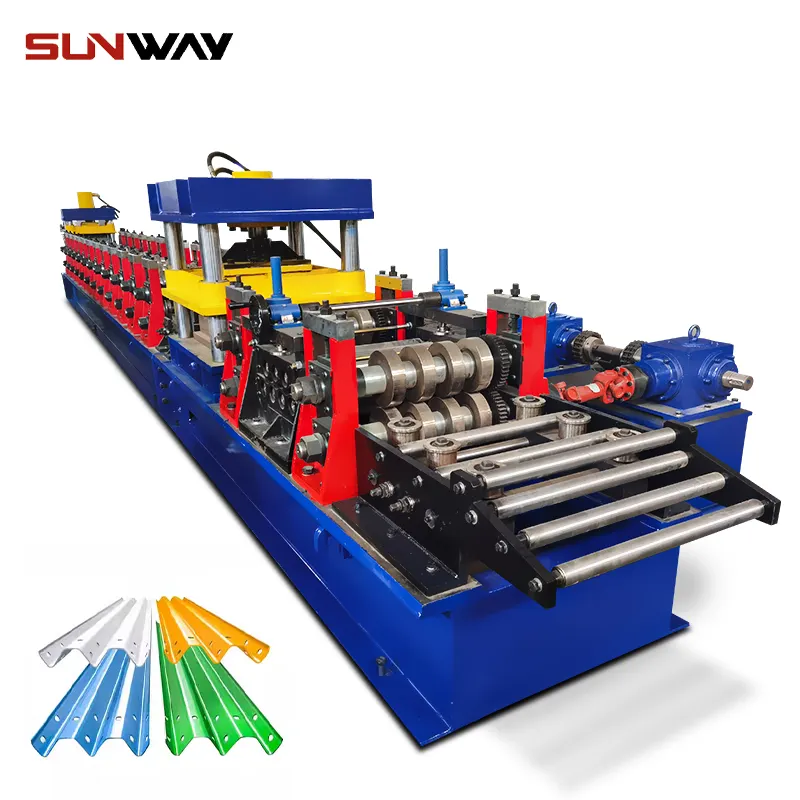
Working Principle of Cable Tray Roll Forming Machines
Cable tray roll forming relies on the continuous bending and gradual shaping of metal coil strip into desired tray profiles through a series of progressions. The key processes involved are:
- Material Feeding: Coiled metal strips are loaded at the unwinding station and fed into the machine.
- Forming: The strip passes through a series of roll forming stands each with 2-3 rollers. The rollers progressively bend the metal to the designed shape.
- Design and Sizing: The roller dies are customized to form trays of required size, depth, width and features like side hooks.
- Slicing: Cutting blades slice the continuously formed metal strip at set lengths to create straight tray sections as per specified.
- अनुकूलन: Additional stations can create holes, emboss patterns, apply surface finishes etc.
- Output: Formed cable tray sections are offloaded for further processes like welding, surface treatment and installation.
The key to quality outcomes is precision roller design, accurate feeding, synchronized forming and cutting actions, with monitoring at each stage.
Types of Heavy Duty Cable Tray Roll Forming Machines
Heavy duty cable tray roll forming machines can be categorized based on structure, forming capability and automation level:
Machine Type | Description |
---|---|
Caged | Roller stations enclosed within a cage-like frame for safety |
Open | Rollers openly accessible for easy maintenance |
Fixed | Fixed size rollers, manual roller change for new profiles |
Quick Change | Roller cassettes or cartridges for fast profile changes |
Semi-Auto | Manual material feeding and offloading |
Fully Auto | Automated loading, forming, cutting and unloading |
Selecting the right type depends on production needs, changeover frequency, level of operator skill, and budgets. Fully automated machines offer the highest productivity but have higher cost.
Key Materials Used in Cable Tray Production
Cable trays can be produced from different metals using heavy duty roll forming machines:
Material | विशेषताएँ |
---|---|
Mild Steel | Economical, strong |
Stainless Steel | Corrosion resistance |
Aluminum | Lightweight, conductive |
Galvanized Steel | Rust resistance |
Mild steel is the most common due to its strength, durability and cost effectiveness. Stainless steel and aluminum provide specialized properties like weather resistance or light weight, but are more expensive.
Roll Formed Cable Tray Design Considerations
Proper design of the roller tooling and dies is crucial for forming quality cable trays. Key parameters include:
- Tray width and depth
- Metal thickness and properties
- Longitudinal stiffeners if needed
- Roller diameters
- Number and size of internal radii
- Horizontal, vertical, inclined sections
- Side hook design
- Embossing and hole patterns
Advanced 3D modeling and simulation helps optimize the progressive die design before manufacturing the roller sets.
Customization of Roll Formed Cable Trays
Heavy duty roll forming lines offer various customization features:
- Tray dimensions – width, depth, metal gauge as needed
- Hook design – width, shape and size
- Holes and Cutouts – size, shape and pattern
- Embossing – logos, labels, texts
- Finishing – powder coating, wet paint, hot dip galvanizing
This allows creating specialized cable trays for different capacity, strength, accessories mounting and aesthetic needs.
Leading Manufacturers of Cable Tray Roll Forming Machines
There are many reputable global suppliers of heavy duty cable tray roll forming machines. Some major manufacturers are:
कंपनी | Location |
---|---|
Dingtek | China |
Jouanel | फ्रांस |
FD China | China |
Formtek | Taiwan |
Erdemtaş | Turkey |
When selecting a machine, key factors to consider are technical expertise, manufacturing capability, quality, service support in the region, machine cost, and production output versus needs.
Price Range of Heavy Duty Cable Tray Roll Forming Machines
The price range for industrial grade heavy duty cable tray roll forming machines is:
- Semi-automatic – $8000 to $15000
- Fully Automatic – $15000 to $35000
The cost varies based on:
- Automation level
- Maximum strip width capacity
- Production speed and power
- Quick change capability
- Material thickness capacity
- Additional features like decoilers, straighteners etc.
Budget machines from unknown brands often compromise on quality and output. It is advisable to invest in renowned industrial grade machines for demanding production environments.
Installation and Operation of Cable Tray Roll Forming Machines
Proper installation and operation ensures optimum performance and safety:
- Mount the machine on a level surface and anchor it properly.
- Provide enough space around for material loading and formed tray unloading.
- Install electrical connections as per specifications.
- Feed thick gauge metal coils of widths suitable for the machine capacity.
- Set strip feeding, roller progression and cut-off as per the tray size.
- Monitor strip flow, lubrication, sensors and safety mechanisms.
- Control speed and production flow to prevent jamming and defects.
- Periodically inspect and maintain rollers, cutters, sensors as required.
- Ensure the work area is clear and operators are trained adequately.
Maintenance Practices for Cable Tray Roll Forming Machines
Regular maintenance enhances productivity and longevity:
Activity | Frequency | Method |
---|---|---|
Inspect rollers and bearings | Daily | Check surface wear, smooth rotation |
Verify sensors | Daily | Confirm correct signals |
Monitor lubrication | Weekly | Top up oil levels, grease roller bearings |
Examine electricals | Monthly | Check connections, wear of contact points |
Test emergency stops | Monthly | Verify machine halts immediately |
Adjust drive mechanisms | As needed | Tension chains, belts and gears |
Replace worn rollers and cutters | As needed | Replace with same profile components |
Thorough cleaning | Quarterly | Clean dust, metal debris across machine sections |
Maintenance schedules must be adhered to closely on heavy use machinery for maximum uptime.
Choosing the Right Cable Tray Roll Forming Machine Supplier
Important factors for choosing a roll forming machine supplier are:
- Proven experience – Years in business, reputation, customer reviews
- Technical expertise – Knowledge to provide optimal solution as per needs
- Manufacturing capabilities – Use of high grade components and quality control
- Customization skills – Flexibility to design profiles and tooling as per requirements
- Responsiveness – Quick problem resolution and technical support
- प्रशिक्षण – Operator training on usage, maintenance and safety
- Delivery – Ability to deliver on time as per committed schedule
- Location – Preferably close by for installation support and service
- Pricing – Competitive pricing in line with features and capabilities
- After-sales support – Maintenance, spare parts supply and upgrades when required
Taking the time to evaluate suppliers on these parameters helps select the right partner for long term success.
Pros and Cons of Cable Tray Roll Forming Machines
Pros | Cons |
---|---|
Fast, continuous production | High initial investment cost |
Highly consistent output | Complex design and setup |
Automated process needs few operators | Rollers require periodic replacement |
Flexible production from coils | Limited to roll-formable shapes |
Ideal for mass customization | Not suited for low volume production |
Compact, safe operation | Specialized skill needed for maintenance |
Advantages of Using Roll Formed Cable Trays
Roll formed cable trays have many benefits over other fabrication methods:
- Speed -automated mass production from coils compared to slow manual welding or bending
- Consistency – uniform dimensions with no human errors
- Material savings – up to 20% lower weight versus welded cable trays
- अनुकूलन – ability to form any required size and design
- Strength – excellent structural durability from the metal forming
- Quality – flawless surfaces free of welds, joints or defects
- Safety – no sharp edges or snapping hazards like cut metal
- Aesthetics – tidy professional appearance from machine production
The advantages make roll formed cable trays ideal for large projects in infrastructure and industry.
Limitations of Roll Forming Process
Roll forming does have some inherent limitations to be aware of:
- Only long, longitudinal profiles possible, no enclosures.
- Size limits based on machine capacity.
- Certain extreme shapes may not be achievable.
- Design expertise needed for tooling and dies.
- Not economical for very low volume production.
- Initial cost for tooling design and manufacture.
- Inflexible process with high changeover time between profiles.
For short runs, small sizes or unusual shapes, alternate methods like welding, bending or laser cutting may be better suited.
Applications and Use Cases of Roll Formed Cable Trays
Heavy duty cable tray roll forming machines cater to a wide range of industrial applications:
Power Infrastructure
- Power plants
- Transmission substations
- Solar farms
- Wind energy
Telecom Infrastructure
- Server rooms
- Switch rooms
- Routing cellular network cables
Manufacturing Facilities
- Data centers
- Automotive plants
- Consumer goods factories
- Chemical facilities
Commercial Buildings
- High-rises
- Shopping malls
- Airports
- Stadiums
Material Handling
- Warehouses
- Logistics centers
- Goods distribution hubs
Resources Industry
- Mines
- Offshore rigs
- Oil and gas platforms
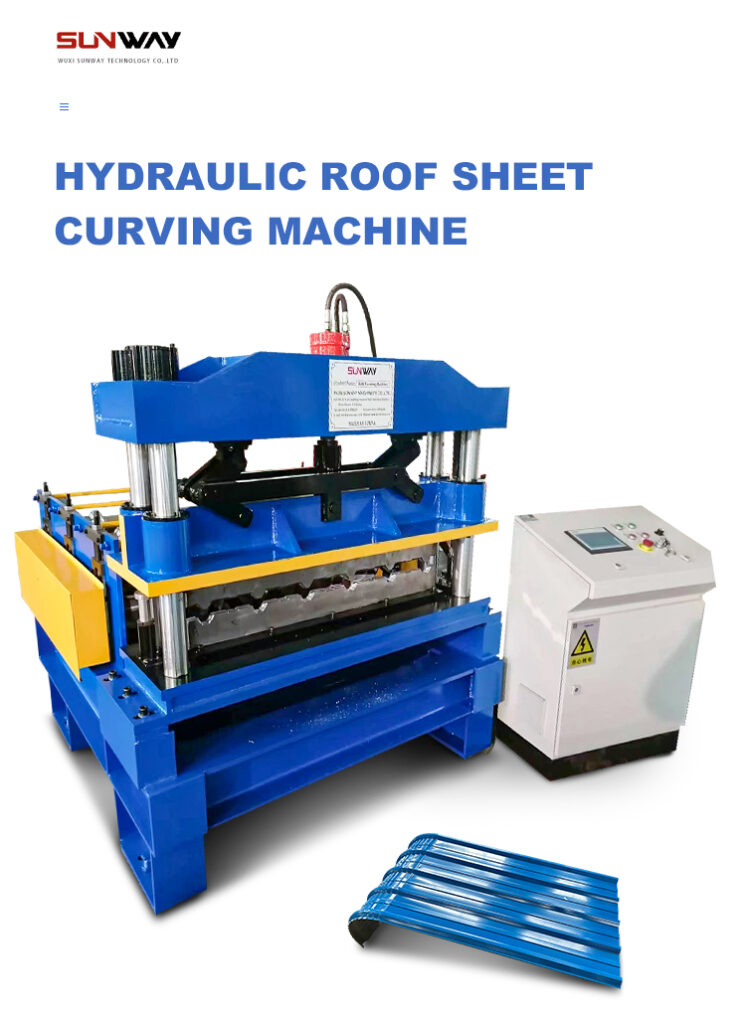
सामान्य प्रश्न
Q: What are the key components of a roll forming machine for cable trays?
A: The main components are an decoiler for sheet feed, forming stations with rollers, punch and emboss stations if needed, hydraulic power system, control panel, cutting station, and a completed parts exit.
Q: Can a roll former make bends and turns in cable trays?
A: No, a roll forming machine can only make longitudinal straight sections. Bends require separate fabrication. The straight sections can be welded or mechanically joined to form turns.
Q: What safety aspects are important for cable tray roll forming operations?
A: Machine must have proper safeguards like sensors, shields and e-stops. Operators should wear protective gear, be trained on safety procedures and keep work area clear. Proper installation, maintenance and supervision are essential.
Q: What is the production rate of heavy duty cable tray roll forming machines?
A: Production speed depends on width capacity and automation level, but is typically 10-20 meters per minute. Advanced machines can reach up to 40 meters per minute.
Q: Can galvanized coils be roll formed into cable trays?
A: Yes, galvanized steel coils are commonly used in cable tray production as they provide superior corrosion resistance for outdoor and industrial applications.
Q: What are common defects in roll formed cable trays?
A: Defects like twisting, warping, irregular bends indicate issues with feed alignment, worn tooling or improper roller adjustment. These require troubleshooting and maintenance of the forming sections.
Q: What is the lifespan of roller dies in cable tray production?
A: With proper use and maintenance, quality roller dies can consistently form around 1 million meters length of cable trays before needing replacement.
Q: Can PVC coatings be applied to roll formed cable trays?
A: Yes, powder coating stations can be integrated in the roll forming line to automatically apply customized PVC coatings for insulation and aesthetics.
निष्कर्ष
Heavy duty cable tray roll forming machines enable efficient mass production of customized cable trays. This guide has provided a detailed overview of working principles, types, configurations, features, applications and selection factors for these versatile metal forming systems. With proper machine selection, operation and maintenance, manufacturers can leverage roll forming for scalable, high-quality cable tray fabrication to meet demanding project needs.