half round gutter roll forming machine are used to produce continuous metal profiles with custom cross-sections by progressive bending of sheet or coil material as it passes through a series of roller dies. Half round gutter making machines create rainwater drainage products for residential and commercial buildings.
This comprehensive guide covers everything related to half round gutter roll formers including:
Overview of half round gutter roll forming machine
Half round gutter making machines, also called half round rain gutter machines or demi-circle gutter roll formers, transform metal coil/strips into curved U-shaped profiles used as roof drainage systems.
They create half cylinder shaped gutters by roll forming the sheet material through a series of roller dies that progressively bend the strip into the desired contour. The formed metal gutters collect and drain rainwater from rooftops preventing water damage.
Benefits of half round gutter roll forming:
- Continuous, automated production of long gutter lengths
- High output rate up to 18 m/min
- Uniform profile and smooth surface
- Cost-effective versus other methods
- Easy customization of dimensions
- Reduced labor compared to manual bending
Drawbacks:
- High initial capital expenditure
- Regular maintenance required
- Limited profile shapes
Half round gutter making machines allow efficient, high-volume production of rainwater collection products for houses, garages, greenhouses etc.
This guide provides a comprehensive overview of half round gutter roll formers covering: working principle, types, components, processes, customization options, installation, operation and maintenance procedures.
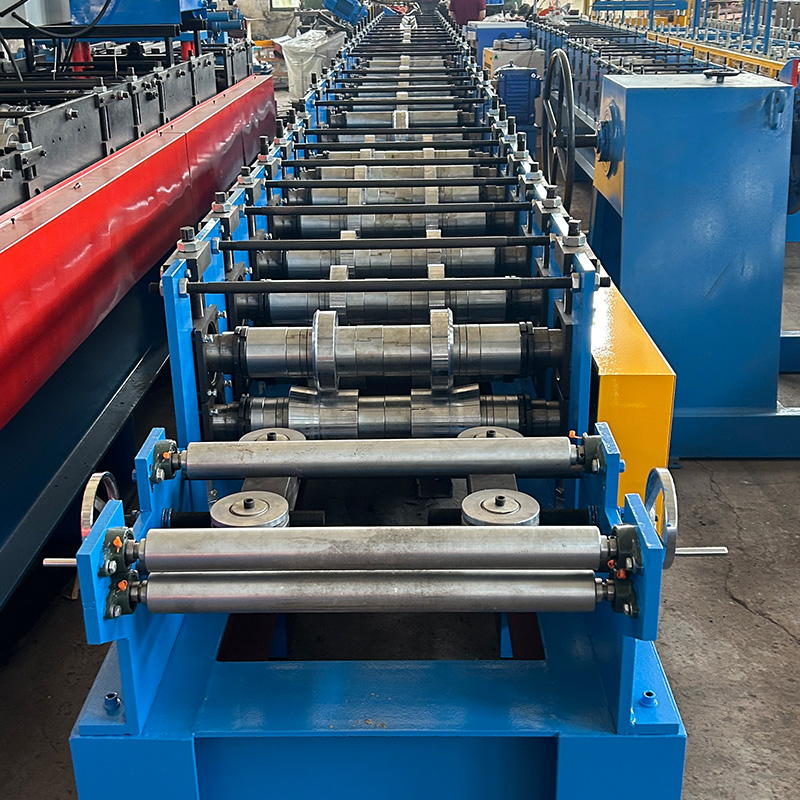
Working Principle of half round gutter roll forming machine
The working principle involves:
- Feeding: Coil/strips enter an unwinding unit
- Accumulation: Accumulator tower stores and feeds sheet at constant speed/tension
- Roll forming: Roller dies bend metal through progressive stages into half cylinder shape
- Cutting: Profiles cut to required lengths
- Output: Formed gutters exit to stock
Key stages in half round gutter roll forming process:
- Material Feeding: Coil/sheet loaded onto powered unwind reel entering through guidance rolls
- Accumulation: Accumulator tower stores and releases fed stock attuned to line speed
- Pre-forming: Initial roller dies make light bends
- Forming: Main roll forming stations make incremental bends up to 180 degrees for half round shape
- Calibration: Final rolls calibrate profile
- Cutting: Flying cut-off shears cut gutters to length
- Output: Formed gutters exit to stock conveyor/stacker
The sheet/coil material undergoes a series of bends by contoured rollers to gradually form the half round contour. Correct roller design and precise gaps between rolls are crucial for profile accuracy.
Half Round Gutter Roll Forming Machine Types
Half round gutter roll forming machines available based on:
Machine Type | विवरण |
---|---|
Light-duty | Lower output <10 m/min Manual loading/unloading Open-frame style |
Heavy-duty | Higher outputs ~18 m/min Automated material feed Closed-frame standalone units |
C-channel + Gutter | Combination machines making both C-channels and half round gutters from same frame |
Portable | Compact machines on wheels for smaller workshops |
Custom | Tailor-made roll formers for specific profile dimensions |
Choice depends on:
- Required output rates
- Gutter sizes
- Production volumes
- Budget constraints
- Factory space availability
Heavy duty half round gutter roll forming machines withautomated coil lines are ideal for large volume needs.
Custom built formers suit unique half round gutter specifications.
Main Components
Key components of half round gutter roll forming machines:
Component | Function |
---|---|
Uncoiler | Feeds raw coil/sheet |
**Feed table ** | Guides strip into machine |
Accumulator | Stores/releases material attuned to line speed |
Roll tooling | Contoured rolls make bending stages |
Forming components | Housings, gears, shafts, belts, chains |
Cutter | Flying shear cutting formed gutters to length |
Control panel | Controls machine operations |
Conveyor/stacker | Catches and stacks finished gutters |
Proper working of all constituents is imperative for quality output. Regular inspection and maintenance must be carried out.
Correct roller design, precise gaps between rolls, calibrated drive systems, rigid framing and stability during running are vital.
-
रोलिंग शटर स्लेट रोल बनाने की मशीन
-
Highway Guardrail End Terminal Forming Machine
-
विद्युत कैबिनेट फ्रेम रोल बनाने की मशीन
-
दीन रेल रोल बनाने की मशीन
-
केबल सीढ़ी रोल बनाने की मशीन
-
पीवी माउंटिंग ब्रैकेट सी शेप प्रोफाइल रोल बनाने की मशीन
-
केबल ट्रे रोल बनाने की मशीन
-
पीवी माउंटिंग ब्रैकेट रोल बनाने की मशीन (एचएटी / ओमेगा प्रोफाइल)
-
पीवी माउंटिंग ब्रैकेट जेड शेप प्रोफाइल रोल बनाने की मशीन
Working Processes
Half round gutter roll forming involves sequentially executed workings:
1. Material Loading
- Coil or sheet loaded onto powered unwind reel
- Enters through de-coiler and guidance rolls
- Fed into accumulator tower
**2. Roll Forming **
- Sheet released from accumulator attuned to line speed
- Passes through series of roller dies
- Rollers make incremental bends up to 180°
- Half round contour gradually formed
3. Cutting
- Formed gutters reach flying cut-off shear
- Shear cuts profiles to desired lengths
- Slugs fall into scrap collection bins
4. Output Conveying
- Formed gutters exit along conveyor
- Stacker collects cut pieces
- Operators offload finished product
Synchronized functioning of all constituents necessary for quality production.
Customization Capabilities
Half round gutter roll forming allows size adjustments:
Alterable parameters:
- Gutter diameters
- Material thickness
- Width of gutters
- Radius of bend
- Final length of pieces
Methods of customization:
- Roller adjustment
- Roll changing
- Program logic changes
- Mechanical part changes
Benefits:
- Caters to client specific needs
- Enhances machine utility
- Expands product range
Correct design to accommodate flexibility is key.
Customization gives half round gutter making machines the ability to produce profiles as per user requirements within machine limits.
Suppliers and Price Range
Major half round gutter roll forming machine manufacturers:
Supplier | Location | Price Range |
---|---|---|
EZ Machinery | China | $5000 – $50000 |
Mewag Tech | भारत | $3000 – $15000 |
Anhui Yuding | China | $8000 – $30000 |
Jinan Longyu | China | $10000 – $60000 |
Price factors:
- Output rate
- Gutter dimensions
- Level of automation
- Production volumes
- Additional accessories
Best value: Mewag Tech roll formers offer good quality at reasonable price points for low to mid production needs.
Reputed makers with proven product performance and service support are recommended.
Installation Requirements
Half round gutter roll forming machine installation essentials:
Parameter | विवरण |
---|---|
Space | <li> Length > 15 ft </li> <li> Width > 10 ft </li> <li> Height > 10 ft </li> |
शक्ति | <li>Main supply: 380-440V, 50-60Hz, 3 Phase</li> <li>Control voltage: 36V/42V DC</li> |
Compressed air | Pressure: 6-8 bar |
Exhaust | Fume extraction system |
Foundations | Flat leveled surface <br> Vibration dampening mounts |
Safety | Fencing, markings, gear covers |
Adequate provision of utilities and clear operating space as per machine dimensions are key for commissioning.
Operation
Half round gutter roll forming – Standard operating procedure:
- Ensure electrical, pneumatic and extraction systems ready
- Load raw material coil/sheet on unwind reel
- Thread sheet through equipment
- Set parameters on control panel – speed, length
- Initiate machine – actuate controls
- Monitor processing
- Check formed profile accuracy
- Ensure smooth sheet flow
- Watch for jams/faults
- Stop working – reset controls to neutral
- Unload finished gutters
- Clear scrap pieces from shear
- Clean equipment after use
- Regular maintenance as required
Safety measures:
- Gear covers to moving parts
- Worker PPE – gloves, shoes, glasses
- Awareness of pinch points
- No loose clothing / jewellery
- Emergency stop buttons
Maintenance
Half round gutter roll former care activities:
Task | Frequency | Method |
---|---|---|
Inspect roll tooling | Monthly | Check surface wear, refinish/replace |
Check chain/belt tension | Monthly | Tighten/adjust if needed |
Monitor shear blades | Weekly | Sharpen/change worn blades |
Test electricals | Quarterly | Check connections, buttons |
Calibrate/align parts | Yearly | Re-adjust forming rolls, settings |
Replace wear items | As needed | Bearings, clutches, seals |
Check safety provisions | Regular | All guards, markings functional |
Proactive servicing minimizes unplanned outages, improves performance and extends equipment life.
Do’s and Don’ts:
Do:
✔️ Use manufacturer approved spares
✔️ Keep maintenance logs ✔️ Inspect before every shift ✔️ Train operators periodically
Don’t:
⛔ Start without safety gear intact
⛔ Exceed process limits
⛔ Alter machine settings unknowingly
Choosing The Right Half Round Gutter Roll Forming Machine
How to select optimal half round gutter making equipment?
Key considerations:
विवरण | |
---|---|
Production needs | Output rate Gutter sizes Batch volumes |
Budget | Affordability constraints |
Raw material | Coil or sheet Metal grade मोटाई |
Flexibility | Customization needs Adjustability range |
Energy efficiency | Power consumption data Performance vs load |
Smart capabilities | Level of automation IoT enabled features |
Maker credentials | अनुभव Installations record Local support |
Overall value | Upfront cost Productivity Total operating costs |
Analyze above aspects before purchasing to get the best equipment fit.
Pros and Cons
Advantages | Disadvantages | |
---|---|---|
Benefits | Fast, automated production Uniform profile Lower labor Custom sizing | High initial cost Large space needed Limited profile range Skilled operation required |
Application range | Roof drainage gutters Gutter collectors Gutter downpipes Perimeter drainage channels | Not suitable for complex profiles Size/thickness constraints present |
Metrics | Output up to 15-18 m/min Width ~100-300mm Radius 50-125mm | Raw material type restrictions Higher maintenance & process control needs |
Balance analysis – Production efficiency merits typically override limitations for majority of users catering to standard half round gutter requirements.
Careful selection aligned to specific needs advised.
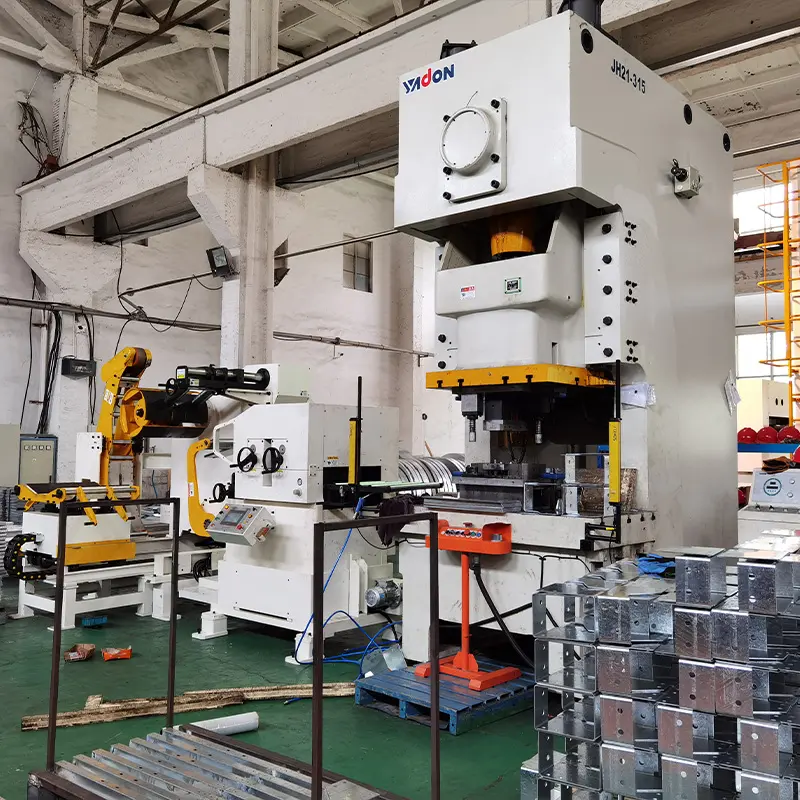
सामान्य प्रश्न
Q: What materials can be used to make half round gutters?
A: Common materials include galvanized steel, galvalume sheets, aluminum sheets up to 2 mm thickness. Special materials like stainless steel, copper are also possible in some cases.
Q: What is the typical thickness of gutters made by these machines?
A: Standard gutter thickness range is 0.4 mm to 0.8 mm though some machines can handle up to 2mm metal strips.
Q: What is the typical output rate for half round gutter roll forming?
A: Outputs starting from 8-10 m/min for manual machines and going up to 15-18 m/min for high end automated lines are commonly available. Customized units with higher throughputs are also possible.
Q: Can half round gutter making machines be used to produce box gutters?
A: No, dedicated rectangular box gutter roll forming machines are required to make square drain profiles. Half round machines can only produce curved semi-circular gutters.
Q: How to correct twisting of gutters coming out of the machine?
A: Twisting arises from internal stresses or outside factors like wind drafts. It can be controlled by adjusting alignment of rolls, bridling unit or increasing bottom support guides. Installing the machine away from open warehouse doors also helps.
Q: What are common problems needing troubleshooting in half round gutter roll formers?
A: Typical issues faced are irregular profiles, sheet jamming, cut length errors, excessive noise/vibration, loosening of parts, chain slackening etc. Following maintenance schedule and manual can prevent many problems.