परिचय
Welcome to our comprehensive guide on guardrail roll forming machines. In this article, we will explore the various aspects of guardrail roll forming machines, including their importance, types, features, working principle, applications, factors to consider when choosing one, and more. Whether you are a manufacturer or an industry professional looking to expand your knowledge, this article will provide you with valuable insights into guardrail roll forming machines.
रेलिंग रोल बनाने की मशीन क्या है?
A guardrail roll forming machine is a specialized equipment used in the manufacturing process of guardrails. Guardrails are essential safety barriers installed along highways, roads, and other transportation infrastructure to prevent vehicles from veering off the road or colliding with obstacles. The roll forming machine plays a crucial role in shaping metal sheets into the desired profile, enabling the production of guardrails in large quantities with consistent quality.
Importance of Guardrail Roll Forming Machines
Guardrail roll forming machines are vital for the production of high-quality guardrails. They offer several benefits that make them indispensable in the industry. Firstly, these machines enable the efficient and cost-effective production of guardrails in large volumes, meeting the demands of infrastructure projects. Secondly, they ensure precise and consistent shaping of metal sheets, resulting in uniform guardrail profiles. Lastly, guardrail roll forming machines improve production efficiency by automating the process, reducing manual labor requirements and enhancing overall productivity.
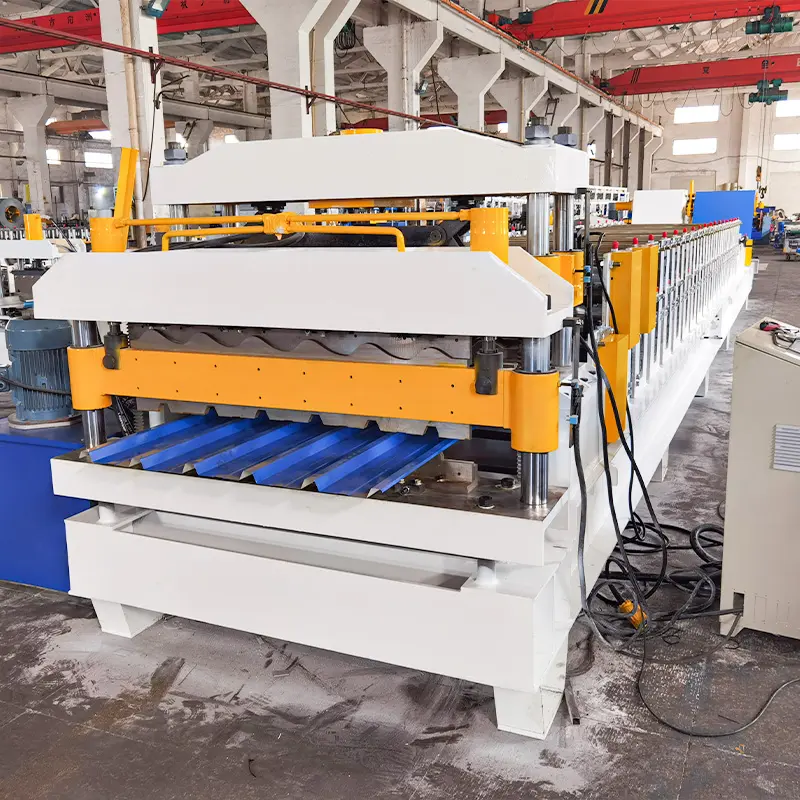
Types of Guardrail Roll Forming Machines
There are several types of guardrail roll forming machines available, each suited for specific guardrail profiles. Let’s explore some common types:
Single Wave Guardrail Roll Forming Machine
The single wave guardrail roll forming machine is designed to produce guardrails with a single wave shape. These guardrails are widely used due to their simplicity and effectiveness in redirecting vehicles and preventing accidents.
Double Wave Guardrail Roll Forming Machine
The double wave guardrail roll forming machine is capable of manufacturing guardrails with a double wave profile. This type of guardrail provides enhanced safety by offering higher impact resistance and stability.
Three Wave Guardrail Roll Forming Machine
The three wave guardrail roll forming machine produces guardrails with a triple wave pattern. This design offers maximum strength and durability, making it suitable for high-speed roads and areas prone to heavy traffic.
W Beam Guardrail Roll Forming Machine
The W beam guardrail roll forming machine is specifically designed to manufacture W-shaped guardrails. W beam guardrails are widely used due to their superior performance in absorbing impact energy and reducing the risk of vehicle rollovers.
Features and Benefits of Guardrail Roll Forming Machines
Guardrail roll forming machines come with a range of features that contribute to their efficiency and performance. Some notable features include:
- High Precision: These machines are equipped with precision tools and rollers that ensure accurate shaping of metal sheets, resulting in consistent guardrail profiles.
- Versatility: Guardrail roll forming machines can be adjusted to produce different guardrail profiles, allowing manufacturers to cater to various project requirements.
- Efficiency: These machines are designed for high-speed production, optimizing productivity and reducing manufacturing time.
- Automation: Many guardrail roll forming machines are equipped with advanced control systems and automation features, minimizing manual intervention and improving operational efficiency.
- Durability: The machines are built with sturdy materials and components, ensuring long-lasting performance even in demanding manufacturing environments.
The benefits of using guardrail roll forming machines include:
- Cost-effectiveness: By automating the production process and reducing material waste, these machines offer cost savings in the long run.
- Consistency: Guardrail roll forming machines ensure consistent product quality, eliminating variations in guardrail profiles.
- Increased Production Capacity: These machines enable manufacturers to produce guardrails in large quantities, meeting project deadlines and increasing market competitiveness.
- Enhanced Safety: Guardrail roll forming machines contribute to the production of reliable and durable guardrails that enhance road safety and protect motorists.
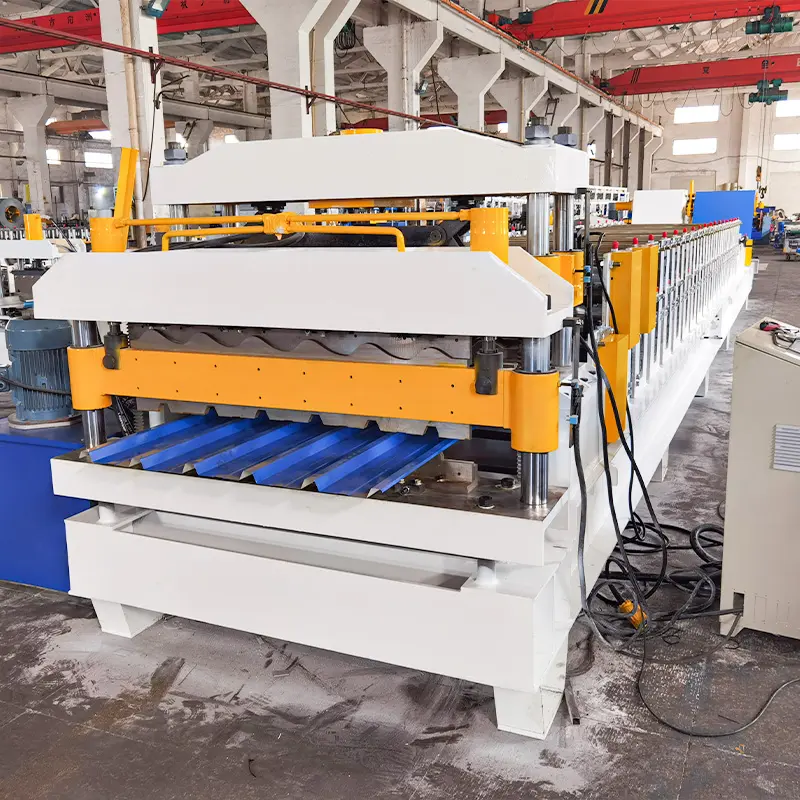
Working Principle of Guardrail Roll Forming Machines
Guardrail roll forming machines operate based on a continuous process that involves several steps. The working principle can be summarized as follows:
- Decoiling: The process begins with feeding the metal coil into the decoiler, which unwinds the coil and feeds it into the roll forming machine.
- Feeding System: The metal strip is guided through the feeding system, ensuring precise alignment and smooth material flow.
- Roll Forming System: The metal strip passes through a series of rollers that gradually shape it into the desired guardrail profile. Each roller set performs a specific forming operation, gradually transforming the flat strip into the desired shape.
- कटिंग सिस्टम: Once the guardrail profile is formed, the cutting system trims the strip to the required length, creating individual guardrail sections.
- नियंत्रण प्रणाली: The control system regulates the machine’s speed, forming parameters, and other operational settings, ensuring consistent output and quality.
- Hydraulic System: The hydraulic system provides power for various machine functions, including feeding, forming, and cutting.
By following this continuous process, guardrail roll forming machines can efficiently produce high-quality guardrails with minimal human intervention.
Key Components of a Guardrail Roll Forming Machine
A guardrail roll forming machine consists of several key components that work together to facilitate the production process. Let’s explore each component:
डेकोइलर
The decoiler is responsible for holding and unwinding the metal coil. It ensures a continuous supply of material to the roll forming machine.
Feeding System
The feeding system guides the metal strip into the roll forming machine, ensuring precise alignment and smooth material flow. It may include rollers, guides, and entry shears to prepare the strip for the forming process.
Roll Forming System
The roll forming system is the heart of the machine. It comprises a series of rollers, each performing a specific forming operation to shape the metal strip into the desired guardrail profile. The number and arrangement of rollers vary depending on the guardrail design.
कटिंग सिस्टम
The cutting system trims the formed guardrail sections to the required length. It can be equipped with mechanical or hydraulic cutting mechanisms to ensure accurate and clean cuts.
नियंत्रण प्रणाली
The control system manages and regulates the machine’s operations. It includes a control panel with user-friendly interfaces that allow operators to set parameters such as speed, length, and forming specifications. The control system ensures consistent output and monitors the machine’s performance.
Hydraulic System
The hydraulic system provides power to various machine functions, such as feeding, forming, cutting, and adjusting. It utilizes hydraulic cylinders, valves, and pumps to generate the necessary force and control movements during the manufacturing process.
These key components work in synergy to ensure the smooth and efficient operation of guardrail roll forming machines.
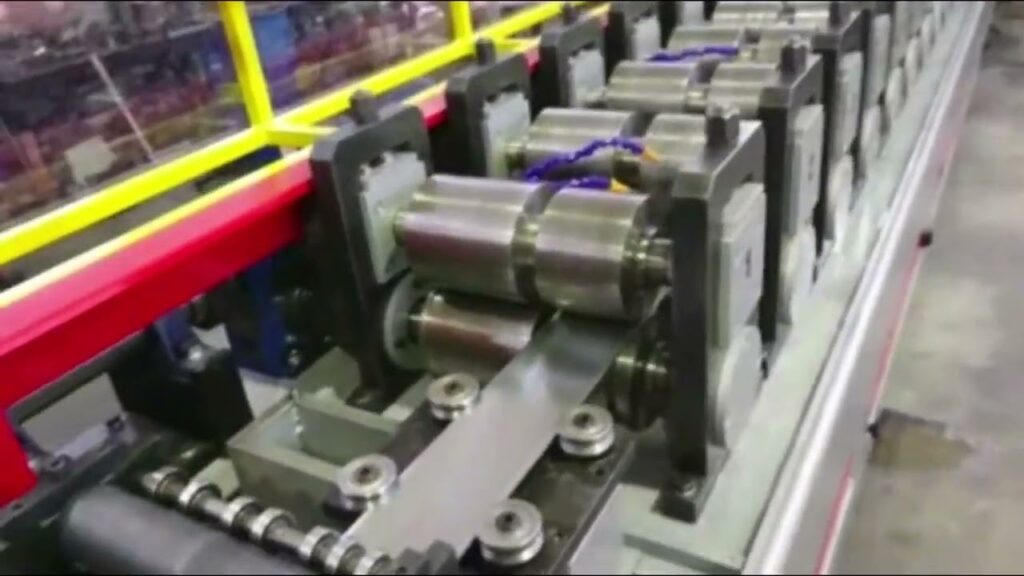
Applications of Guardrail Roll Forming Machines
Guardrail roll forming machines find extensive applications in the construction and transportation industries. Some common applications include:
- Highways and Roads: Guardrails produced by roll forming machines are installed along highways and roads to provide a protective barrier for vehicles, preventing accidents and reducing the severity of collisions.
- Bridges and Overpasses: Guardrails are crucial safety features on bridges and overpasses, ensuring the safety of motorists traveling at elevated heights.
- Parking Lots: Guardrails are used in parking lots to delineate parking spaces, guide traffic flow, and protect pedestrians and vehicles from collisions.
- Industrial Sites: Guardrails are installed in industrial areas to separate pedestrian walkways from vehicular traffic, ensuring the safety of workers and visitors.
- Residential and Commercial Areas: Guardrails are utilized in residential and commercial areas to enhance safety on staircases, balconies, and elevated platforms.
The versatility of guardrail roll forming machines allows manufacturers to produce guardrails that meet the specific requirements of these diverse applications.
Factors to Consider When Choosing a Guardrail Roll Forming Machine
When selecting a guardrail roll forming machine, several factors should be taken into account to ensure optimal performance and value for investment. Here are some essential considerations:
- Machine Specifications: Evaluate the machine’s technical specifications, including its capacity, speed, dimensions, and power requirements, to ensure it aligns with your production needs.
- Production Capacity: Consider the machine’s output capacity and its ability to meet your production volume requirements within the desired time frame.
- Material Compatibility: Verify that the machine can handle the specific types and thicknesses of materials used for guardrail production, such as galvanized steel or aluminum.
- Automation and Control Features: Assess the machine’s automation capabilities, control system features, and ease of operation. Advanced features such as touch-screen interfaces, automatic length adjustment, and error detection systems can enhance productivity and efficiency.
- After-Sales Support and Service: Choose a manufacturer or supplier that provides comprehensive after-sales support, including maintenance, training, and spare parts availability.
By carefully considering these factors, you can select a guardrail roll forming machine that meets your production requirements and ensures long-term success.
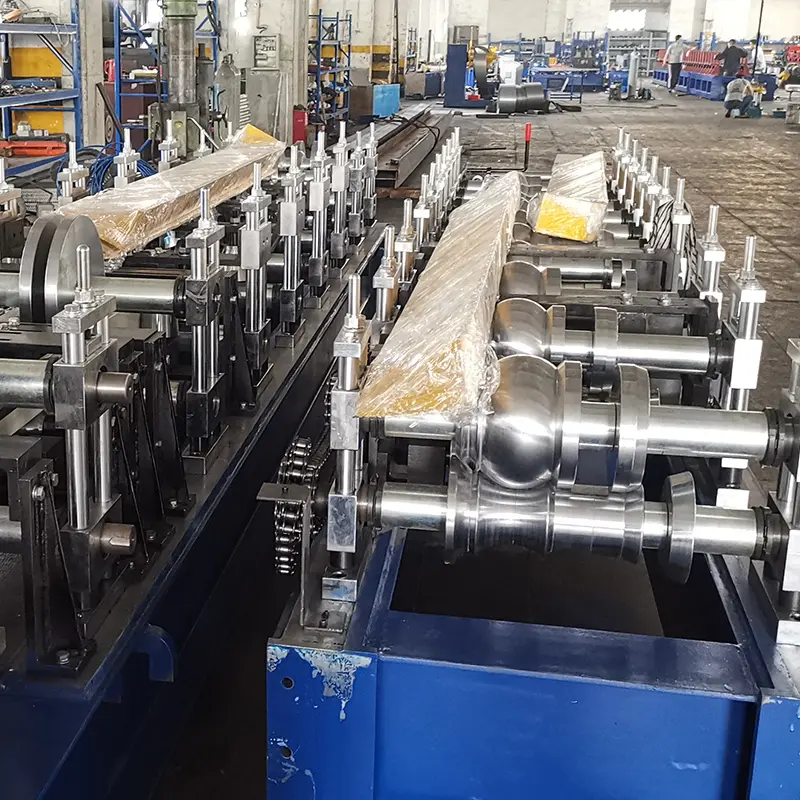
Maintenance and Safety Tips for Guardrail Roll Forming Machines
To maximize the lifespan and performance of a guardrail roll forming machine, regular maintenance is essential. Here are some maintenance tips to follow:
- Routine Inspections: Regularly inspect the machine for any signs of wear, loose bolts, or damaged components. Address any issues promptly to prevent further damage.
- Lubrication: Ensure proper lubrication of moving parts to minimize friction and extend the life of the machine. Follow the manufacturer’s recommendations for lubrication intervals and use appropriate lubricants.
- Cleaning: Keep the machine clean and free from debris or metal shavings that can affect its performance. Use appropriate cleaning methods and tools to maintain the machine’s integrity.
- Safety Measures: Implement safety protocols and provide proper training to operators. Ensure they wear appropriate personal protective equipment (PPE) such as safety glasses, gloves, and ear protection. Regularly inspect safety features such as emergency stop buttons and safety guards to ensure they are functioning correctly.
- Documentation and Records: Keep a record of maintenance activities, including inspections, lubrication, and repairs. This documentation helps track the machine’s maintenance history and aids in identifying any recurring issues.
By following these maintenance tips, you can prolong the lifespan of your guardrail roll forming machine and ensure its optimal performance.
In terms of safety, it is crucial to prioritize the well-being of operators and adhere to safety guidelines. Here are some safety tips to consider:
- Training and Education: Provide comprehensive training to machine operators on safe operating procedures, emergency protocols, and hazard identification. Ensure they understand the risks associated with operating the machine.
- Machine Guarding: Install proper safety guards and protective barriers to prevent access to moving parts and reduce the risk of accidents.
- Emergency Stop and Safety Devices: Ensure that the machine is equipped with functional emergency stop buttons and other safety devices. Train operators on how to use them effectively in case of emergencies.
- Proper Tooling and Handling: Provide operators with the appropriate tools and equipment for material handling, loading, and unloading. Encourage safe lifting techniques and the use of lifting aids to prevent strain or injuries.
- Regular Safety Inspections: Conduct routine safety inspections to identify any potential hazards or safety concerns. Address any issues promptly to maintain a safe working environment.
By implementing these safety measures, you can minimize the risk of accidents and create a safe working environment for operators and other personnel involved in the manufacturing process.
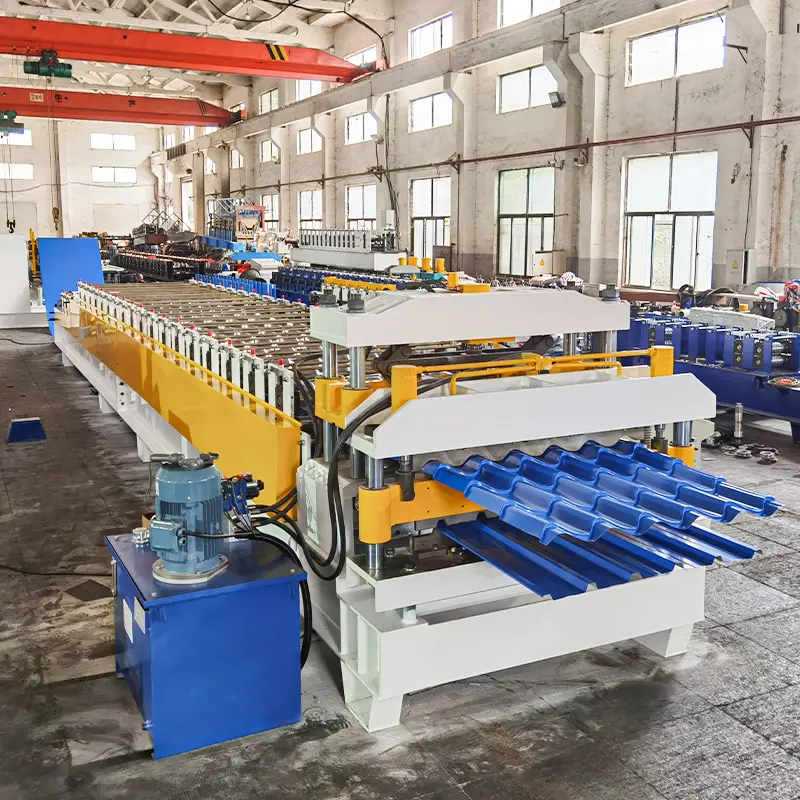
Market Trends and Outlook for Guardrail Roll Forming Machines
The market for guardrail roll forming machines is expected to witness steady growth in the coming years. Several factors contribute to this positive outlook:
- Infrastructure Development: Increasing investments in infrastructure development projects, such as road expansions, bridges, and highways, drive the demand for guardrails. This fuels the need for efficient and high-capacity roll forming machines.
- Stringent Safety Regulations: Governments and regulatory bodies are implementing stricter safety regulations to enhance road safety and minimize accidents. This mandates the installation of guardrails, further boosting the demand for roll forming machines.
- Technological Advancements: Continuous advancements in roll forming technology, such as improved automation, precision control, and material handling capabilities, enhance the efficiency and productivity of guardrail roll forming machines.
- Growing Awareness of Safety: The growing awareness of the importance of road safety among the general population and governments increases the demand for high-quality guardrails. This, in turn, drives the need for advanced roll forming machines.
- Sustainable and Environmentally Friendly Practices: The industry is witnessing a shift towards sustainable manufacturing practices. Guardrail roll forming machines that offer energy-efficient operations and minimize material waste align with these practices and attract manufacturers.
Overall, the market for guardrail roll forming machines is poised for growth, driven by infrastructure development, safety regulations, technological advancements, and the growing emphasis on sustainable manufacturing practices.
निष्कर्ष
Guardrail roll forming machines play a critical role in the efficient and cost-effective production of high-quality guardrails. They offer precise shaping capabilities, automation features, and increased production capacity. By understanding the working principle, key components, and types of guardrail roll forming machines, manufacturers can make informed decisions when selecting the most suitable equipment for their production needs. Regular maintenance, adherence to safety protocols, and staying updated with market trends contribute to the long-term success of guardrail roll forming machine operations.
By investing in reliable and advanced guardrail roll forming machines, manufacturers can contribute to road safety, infrastructure development, and the overall well-being of motorists and pedestrians.