Imagine a world without elevators. No soaring skyscrapers, no accessible high-rise apartments, no efficient transportation within multi-story buildings. While the elevator car itself takes center stage, a crucial component behind its smooth, safe operation often goes unnoticed: the elevator guide rail. And the machine that shapes these vital rails? The remarkable Elevator Guide Rail Roll Forming Machine.
Function of Elevator Guide Rail Roll Forming Machines
Elevator guide rails are the backbone of the elevator system, providing a precise track for the car to travel along. They ensure smooth vertical movement, stability, and passenger safety. But how are these rails, often long and intricately shaped, actually produced? Enter the लिफ्ट गाइड रेल रोल बनाने की मशीन.
This industrial marvel utilizes a technique called roll forming. Imagine feeding a long sheet of metal, like a long, thin ribbon, into a series of precisely designed rollers. Each roller progressively bends and shapes the metal into the desired profile of the elevator guide rail. It’s like a metal origami machine, meticulously folding the sheet into a strong, three-dimensional structure.
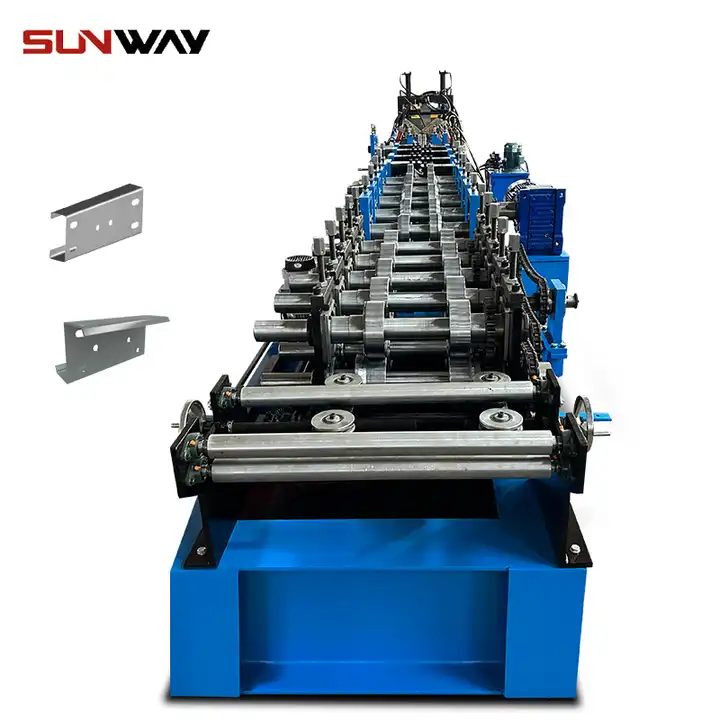
Types of Elevator Guide Rail Roll Forming Machines
The world of elevator guide rail roll forming machines isn’t a one-size-fits-all scenario. There are two main types to consider:
- Cold Roll Forming Machines: This type utilizes pressure and specially designed rollers to shape the metal at room temperature. Cold roll forming is ideal for creating high-precision rails with consistent dimensions. It’s a popular choice for manufacturing a wide variety of elevator guide rail profiles.
- High-Frequency Roll Forming Machines: For thicker metals or more complex rail shapes, high-frequency roll forming might be the answer. This method utilizes high-frequency electrical currents to heat the metal locally as it passes through the rollers. The combination of heat and pressure allows for shaping sturdier rails or those with intricate details.
Applications of Elevator Guide Rail Roll Forming Machines
The applications of Elevator Guide Rail Roll Forming Machines are as diverse as the buildings they serve. Here are just a few examples:
- High-Rise Buildings: Modern skyscrapers rely on efficient and safe elevator systems. Elevator guide rails, formed by these machines, ensure the smooth and stable movement of elevator cars in these towering structures.
- Commercial Buildings: From shopping malls to office complexes, elevators are a crucial element for efficient movement of people and goods. Elevator guide rail roll forming machines play a vital role in supplying the necessary rails for these elevators.
- Residential Buildings: Multi-story apartments and condominiums require elevators for accessibility and convenience. Elevator guide rail roll forming machines contribute to the safe and reliable operation of elevators in these residential spaces.
Advantages of Elevator Guide Rail Roll Forming Machines
Compared to traditional methods of rail creation, elevator guide rail roll forming machines offer several advantages:
- Precision and Consistency: The use of precisely designed rollers ensures consistent dimensions and profiles for each rail produced. This precision translates to smoother elevator operation and enhanced safety.
- High Production Rates: Roll forming machines can churn out elevator guide rails at impressive speeds, significantly reducing production time compared to manual forming methods. This translates to cost savings and faster completion of construction projects.
- Versatility: Modern roll forming machines can be customized to create a wide variety of elevator guide rail profiles, catering to diverse construction needs.
- Reduced Waste: The roll forming process minimizes material waste compared to traditional methods. This not only benefits the environment but also reduces production costs.
-
रोलिंग शटर स्लेट रोल बनाने की मशीन
-
Highway Guardrail End Terminal Forming Machine
-
Highway U/C Post Roll Forming Machine
-
2 Waves Highway Guardrail Roll Forming Machine
-
3 Waves Highway Guardrail Roll Forming Machine
-
विद्युत कैबिनेट फ्रेम रोल बनाने की मशीन
-
दीन रेल रोल बनाने की मशीन
-
दो लहरें राजमार्ग रेलिंग मशीन
-
तीन लहरें राजमार्ग रेलिंग मशीन
Choosing an लिफ्ट गाइड रेल रोल बनाने की मशीन
While the advantages of roll forming machines are clear, choosing the right one for your needs requires careful consideration. Here are some key factors to ponder:
- Type of Elevator Rail Needed: Consider the specific profile and thickness of the elevator guide rail you require. This will determine whether a cold roll forming machine or a high-frequency machine is better suited for the job.
- Production Capacity: Evaluate your production volume needs. How many elevator guide rails will you be producing? Choosing a machine with the appropriate production capacity ensures efficiency and avoids bottlenecks.
- Machine Features: Look for features that enhance the functionality and ease of operation. Servo motors for precise control, user-friendly interfaces, and automatic cut-off systems are some valuable features to consider.
- Reputation and Service: Invest in a machine from a reputable manufacturer with a proven track record of quality and reliable after-sales service.
Suppliers and Pricing of Elevator Guide Rail Roll Forming Machines
The landscape of Elevator Guide Rail Roll Forming Machine suppliers is global. Here’s a glimpse into some prominent players and a general idea of pricing structures
Supplier | Location | Machine Type | Capacity (meters per minute) | Price Range (USD) |
---|---|---|---|---|
Co-effort Machinery | China | Cold Roll Forming | 6 – 15 | $50,000 – $100,000 |
Lotos Forming | China | Cold Roll Forming, High-Frequency | Up to 20 | $80,000 – $150,000 |
Shini | China | Cold Roll Forming, High-Frequency | Up to 30 | $80,000 – $150,000 |
Durma Machinery | Turkey | Cold Roll Forming, High-Frequency | Up to 25 | $80,000 – $150,000 |
Davi | इटली | Cold Roll Forming, High-Frequency | Up to 40 | $80,000 – $150,000 |
Beyond the Numbers: Reputation, Service, and Customization
While price is certainly a factor, it shouldn’t be the sole deciding element. Here’s why:
- Reputation and Service: A reputable manufacturer with a history of quality machines and reliable after-sales service is invaluable. Prompt technical support, readily available spare parts, and a warranty that offers peace of mind are crucial for smooth operation and minimizing downtime.
- Customization: Your ideal machine might not be a one-size-fits-all solution. Look for suppliers who offer customization options to cater to your specific production needs. This could involve adjustments to the roll forming station design to accommodate unique rail profiles or the incorporation of additional features like automatic stacking systems.
Advantages and Disadvantages of Different Machine Types
Cold Roll Forming Machines:
- Advantages: Generally lower cost, suitable for a wide range of profiles, ideal for high-precision applications.
- Disadvantages: Limited capacity for thicker materials or complex shapes, may require post-processing for some profiles.
High-Frequency Roll Forming Machines:
- Advantages: Can handle thicker materials and intricate shapes, offers faster production speeds for some applications.
- Disadvantages: Higher initial cost compared to cold roll forming machines, might require additional expertise for operation and maintenance.
Finding the Perfect Fit
Choosing the right Elevator Guide Rail Roll Forming Machine is akin to finding the perfect puzzle piece. Consider your production needs, budget, desired level of automation, and the specific elevator guide rail profiles you’ll be producing. Researching reputable suppliers, comparing features, and inquiring about customization options are key steps in making a well-informed decision.
The Future of Elevator Guide Rail Roll Forming
The future of elevator guide rail roll forming is poised for continued innovation. Here are some exciting trends to watch:
- Increased Automation: Expect advancements in automation to further streamline the production process. Automatic loading and unloading systems, integrated quality control checks, and real-time production monitoring are on the horizon.
- Advanced Materials: As elevator technology evolves, so too will the materials used for guide rails. High-strength, lightweight composite materials might play a bigger role in the future, demanding adaptable roll forming machines.
- Sustainability: Manufacturers are constantly seeking ways to reduce environmental impact. This could involve the development of energy-efficient machines, the use of recycled materials in the roll forming process, and minimizing production waste.
The लिफ्ट गाइड रेल रोल बनाने की मशीन, once an unsung hero, is now recognized as a vital component in the construction industry. As elevator technology continues to advance, these remarkable machines will undoubtedly play a crucial role in shaping the future of vertical transportation.
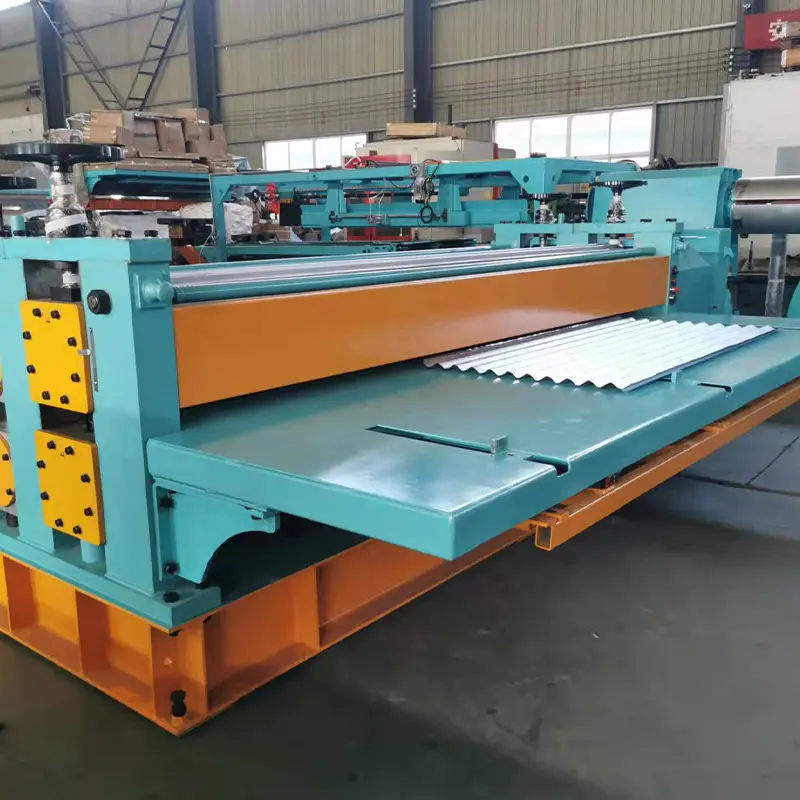
सामान्य प्रश्न
Q: What are the safety considerations when operating an Elevator Guide Rail Roll Forming Machine?
A: Safety is paramount. Always follow the manufacturer’s instructions and adhere to recommended safety protocols. Wearing appropriate personal protective equipment (PPE) such as gloves, safety glasses, and ear protection is essential. Additionally, ensure proper machine guarding is in place and that only authorized personnel operate the equipment.
Q: How long do Elevator Guide Rail Roll Forming Machines typically last?
A: The lifespan of a roll forming machine depends on various factors such as maintenance practices, usage frequency, and the type of materials being formed. Well-maintained machines from reputable manufacturers can last for decades with proper care.
Q: Can I use a second-hand Elevator Guide Rail Roll Forming Machine?
A: Absolutely! Second-hand machines can be a cost-effective option, especially for startups or lower production volume needs. Here are some things to consider when evaluating a used machine:
- Machine Age and Condition: A newer machine will likely offer greater reliability and efficiency compared to a very old model. Thoroughly inspect the machine for signs of wear and tear, particularly on the rollers and other critical components.
- Maintenance History: Request maintenance records from the seller to gauge how well the machine has been cared for. Regular maintenance is essential for ensuring longevity and performance.
- Availability of Parts: Ensure spare parts are readily available for the specific machine model you’re considering. Downtime due to unavailable parts can be costly.
- Seller Reputation: Purchase a used machine from a reputable dealer who specializes in elevator industry equipment. Look for a seller who offers a warranty or guarantee on the machine’s condition.