ए सीजेड शहतीर रोल बनाने की मशीन is an industrial equipment used for continuously bending and forming sheet metal into C and Z shaped purlins. Purlins are structural steel members used in buildings to support roofing and sheeting. This equipment allows efficient, high-volume production of standardized purlins.
Introduction to CZ Purlin Roll Forming
Roll forming is a metal working process in which sheet metal is passed through consecutive sets of rolls to bend it into various profile shapes. C and Z purlins have a unique cross-section that provides strength and rigidity to roofing systems.
Roll formed C and Z sections have several advantages over other forms of bar steel:
- Higher strength-to-weight ratio, allowing lighter and affordable structures
- Standardized dimensions for ease of installation
- Smooth surfaces that are aesthetically pleasing
- Compatible with modern roofing materials and techniques
ए सीजेड शहतीर रोल बनाने की मशीन can rapidly produce continuous lengths of cold-formed purlins from coiled steel feed stock. The formed sections emerge with precisely defined dimensions engineered for structural integrity.
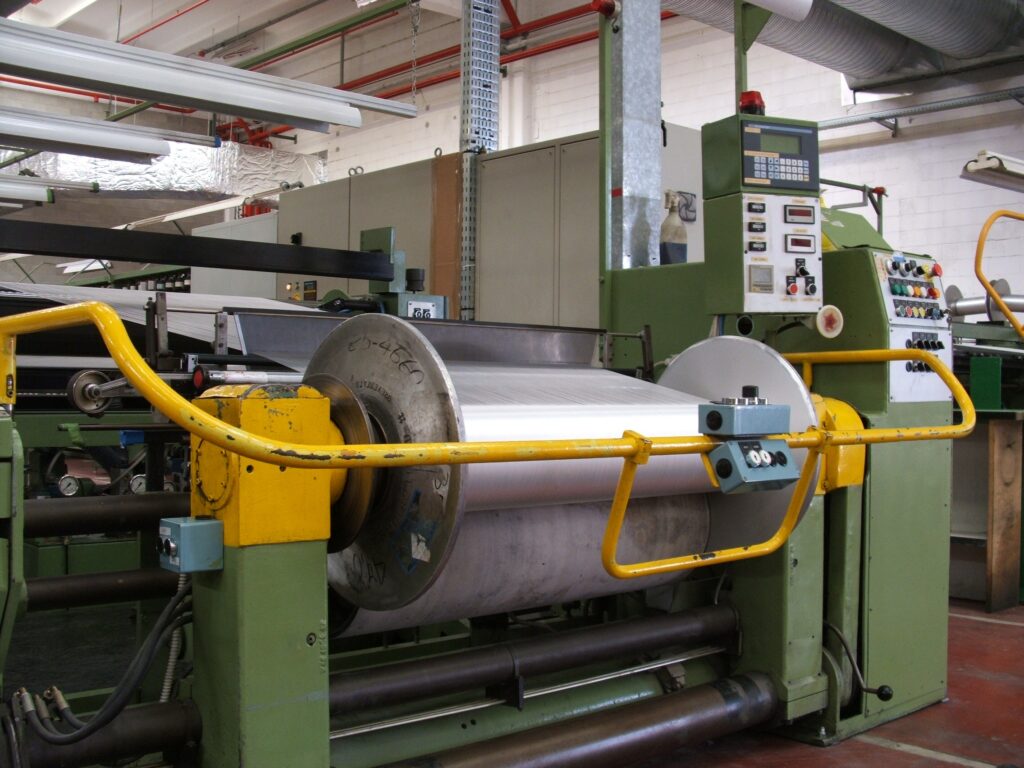
Working Principle of CZ Purlin Roll Forming Machine
A CZ purlin roll forming machine consists of different working sections:
- Uncoiling and feeding – Coiled steel sheet is loaded and passed through a straightening mechanism
- रोल बनाना – The sheet goes through several rolling stations to gradually bend it into shape
- Cutting – Formed sections of the required length are cut off
- Supporting – Special guides stabilize the thin walled sections during forming
- Control – Sensors monitor production and PLC units control the sequential forming operations
By changing the roll tooling, the same machine can produce various purlin sizes and designs. Advanced units have automatic tool changing capability.
Features of CZ Purlin Roll Forming Machine
- Heavy welded frame structure with precision machined components
- Roller boxes house bearing mounted forming rolls
- Adjustable forming assemblies for applying correct amount of bend
- Roller pressure control for thin and thick materials
- Entry guides, support arms, exit tables to handle thin walled sections
- Automatic lubrication systems for reducing wear
- Touchscreen control panel for production monitoring
- Servo electric or hydraulic cut off actuators for length control
- Safety guarding as per industrial regulations
Parameters of CZ Purlin Roll Forming Machine
Parameter | विवरण |
---|---|
Production Speed | Up to 15 m/min |
Raw material thickness | 0.7 mm to 2.0 mm |
Final section height | 50 mm to 400 mm |
Final section width | 30 mm to 250 mm |
Length capacity | Customizable as per requirement |
Power consumption | Around 25 kW + 10 kW for every additional forming station |
Industrial Applications of सीजेड शहतीर रोल बनाने की मशीन
CZ purlin roll forming machines are indispensable equipment in factories involved in:
- Manufacturing of standardized roofing and walling components
- Mass production of structural C and Z purlins
- Supplying formed steel sections to construction industry
- Roof panel and metal building manufacturers
- Large warehouses, industrial plants, and commercial complexes
The ability to rapidly produce continuous, long length purlins makes these machines ideal for high volume applications in infrastructure and building projects.
-
Highway Guardrail End Terminal Forming Machine
-
Highway U/C Post Roll Forming Machine
-
2 Waves Highway Guardrail Roll Forming Machine
-
3 Waves Highway Guardrail Roll Forming Machine
-
विद्युत कैबिनेट फ्रेम रोल बनाने की मशीन
-
दीन रेल रोल बनाने की मशीन
-
दो लहरें राजमार्ग रेलिंग मशीन
-
तीन लहरें राजमार्ग रेलिंग मशीन
-
केबल सीढ़ी रोल बनाने की मशीन
Working Process of CZ Purlin Roll Forming Machine
The CZ purlin production cycle involves coordinated operation of multiple functional units:
1. Material Loading
- Coiled steel sheet loaded onto a mandrel
- Lead end aligned to feeder mechanism
- Various widths and thicknesses accommodated
2. Feeding
- Powered rollers/straigtening machine feeds sheet
- Consistent tension maintained
- Controls stop/start of feed
3. Pre-forming
- Sheet stabilized and pre-bent by entry guides
- Prepares it for profile forming
4. Profile Forming
- Sheet passes through series of forming rollers
- Applying calculated angles of bend at each station
- Gradually forming CZ cross-section
5. Post-forming
- Formed purlins supported by arms
- Preventing distortion
- Allowing precise cut off
6. Cut Off
- Purlins cut to specified lengths
- By hydraulic or servo electric shears
- Cycle restarts automatically
7. Exit
- Sections placed on table for collection
- Operator packs finished purlins
Forming Stations in CZ Purlin Roll Forming Machine
The number of forming stations determines the complexity of the final profile and quality of formed components.
Station | Process Performed |
---|---|
1 | Feeds sheet at entry |
2 | Rolls start bending sheet |
3 | Forms fundamental shape |
4 | Further profile development |
5 | Establishes overall dimensions |
6 | Final calibration of purlin shape |
7-10 | Additional stations for shape correction and sizing |
More stations allow gradual bending for consistent quality along the formed length. They permit close tolerances as per design specifications.
Components of CZ Purlin Roll Forming Machine
The main sub-assemblies of the CZ purlin roll forming line are:
1. Uncoiler
- Mounting stand for coil mandrel
- Powered unwinding mechanism
- Multi-width slitting facility
2. Feeder
- Accumulator for tension control
- Straightening rolls
- Servo motor drive
3. Forming Assembly
- Housing frames to hold stations
- Heavy duty bearing blocks
- Tooling – top & bottom rolls
4. Post-forming
- Support arms to prevent distortion
- Guide plates to stabilize shape
5. Cutoff Shear
- Robust steel shear frame
- Moving hydraulic blade mechanism
- Length measurement system
6. Controller
- Industrial PC and PLC
- HMI touchscreen panel
- AC drive panels
7. Structural Frame
- Precision machined thick plate welded structure
- Lateral supports and braces
- Front and rear platforms
Customization of CZ Purlin Roll Forming Machine
- Customized tooling as per required purlin sizes
- Profile fine-tuned by adjusting bend angles
- Number of stations changed to alter complexity
- Compatible with upstream slitting line
- Length measurement and cutoff systems tailored to needs
- Additional forming assemblies for special profiles
- Robotic systems for part handling after forming
- Selection of fully electric or hydraulic drives
Design Calculation for CZ Purlin Tooling
The cross-sectional profile of CZ purlins has strict structural requirements. Tooling design is based on precise mathematical calculations factoring in:
- Geometry of final shape with angles
- Developed length of formed flanges
- Sheet thickness and yield strength
- Rolling angles at successive stations
- Springback compensation in bands
- Clearances between formed surfaces
Advanced software accurately simulates the progressive roll forming process. This allows optimizing the number of stands needed to avoid defects. The 3D modeled tools are CNC machined to fine tolerances for quality profiles.
Quality Inspection of Formed CZ Purlins
To validate production as per specifications, formed CZ purlins undergo the following checks:
- Dimensional inspection – Cross-section dimensions measured and verified with gauge
- Geometry check – Shape examined for twist or distortion
- Surface finish – Smoothness evaluated by visual inspection
- Length confirmation – Sample lengths checked with steel tape
- Hardness testing – Material hardness measured by portable durometer
- Coating thickness – For painted samples, dry film thickness ensured
Statistical quality control is applied with samples from each batch. Operators also constantly monitor for defects.
Defects in CZ Purlin Roll Forming
Some potential defects needing corrective action:
- Twisting – Section gets distorted during forming
- Wavy edges – Rippling along cut ends from shear
- Flange bending – Improper support leading to deformation
- Thickness variation – Due to non-uniform coiled stock
- Surface marks – Impression or scratches from tools
- Angular deviation – Inaccurate bend angles altering dimensions
- Length differences – Incorrect cutoff leading to short purlins
Defect analysis helps identify weak points needing adjustment – stock material properties, tooling design issues, machine calibration, or operational parameters.
Price Range of CZ Purlin Roll Forming Machines
The price range for standard CZ purlin roll forming lines from international suppliers is approximately:
- $8,000 to $15,000 for low capacity mini lines
- $18,000 to $38,000 for medium range models like 150 to 300 mm
- $45,000 upwards for heavier duty 450 mm or more sized lines
- Additional charges for customization, automation, and special features
Domestic manufacturers may offer 35-50% lower prices by saving on import duties and freight costs. But the quality and technology may be inferior.
Installation & Commissioning of CZ Purlin Roll Forming Machine
Proper installation by technicians ensures optimum production efficiency and machine life. The key steps are:
- Positioning & leveling – Line mounted on flat concrete floor using anti-vibration pads
- Alignment – Precise alignment of unwind and feed sections with rest of frames
- Assembly – Joining modular frames; tightening all structural connections
- Electrical – Power wiring to control panel; laying cables and earthing
- Pneumatic – Compressed air pipes connected to lubrication systems
- Trial runs – Testing sequential operation; tuning components
- Tooling setup – Installation of profile tooling; adjustment of stations
- Safety – Guarding and safety devices activated; area clearance ensured
Testing is done with multiple coil batches having different material thickness and coatings to validate performance.
Operation of CZ Purlin Roll Forming Machine
Efficient functioning involves standardized working procedures by trained operators:
- Visual inspection of machine for oil, wear, leaks
- Program selection from control panel recipe as per coil
- Mounting of purlin tooling & adjustment of roll gaps
- Loading coil on unraveler; feeding end into opener
- Jogging for threading sheet through stands
- Initiating automatic run; setting parameters
- Monitoring operation & checkpoints via control panel
- Ensuring formed pieces conveyed properly
- Regular collection of output sections
- Visual checking for defects
- Periodic measurement of dimensions
- Signalling for programmed stoppages
- Scheduled maintenance during breaks
- Analyzing any downtime or defects
- Reporting feedback for improvements
Maintenance of CZ Purlin Roll Forming Machine
Preventative maintenance is vital for maximum performance. Daily and weekly upkeep activities required:
- Cleaning dust, oil, dirt from assemblies
- Checking roller bearing health via temperature or vibration
- Inspecting gear wear and backlash
- Tightening loose foundation bolts
- Adjusting belt tension, chains, sprockets
- Lubricating moving joints with grease
- Replenishing hydraulic oil levels
- Examining electrical terminals, connections
- Testing emergency stop safety circuits
- Monitoring drive loads and signs of overload
- Reviewing unusual sounds from moving parts
- Tracking units due for overhaul
Well maintained equipment with scheduled part replacement enhances output and reduces breakdowns.
Choosing Supplier for CZ Purlin Roll Forming Machine
The important aspects to consider when selecting supplier:
Technical factors
- Experience supplying such roll formers globally
- Capability to deliver required production volumes
- Quality of material and components used
- Precision and finish of fabricated parts
- Overall structural stability for smooth operation
- Advanced integrated control systems
- Commitment to service support
Commercial factors
- Reasonable pricing appropriate to offered quality
- Payment options including LC, terms
- Responsiveness to technical queries
- Willingness for trial order
- Clarity on shipping, taxes, duties
- Previous customer reference checks
Visiting factory helps assess manufacturing processes, quality control, R&D infrastructure.
Pros and Cons of सीजेड शहतीर रोल बनाने की मशीन
Advantages
- High production rate up to 15 m/min
- Low operating cost per ton material
- Consistent quality along lengths
- Dimensional accuracy as per standards
- Interchangeable tooling for various profiles
- Low maintenance compared to press brakes
- Compact layout with small footprint
- Fully automatic for labor reduction
- Safe enclosed forming with no sharp edges
- Standard models available fast at lower prices
- Various size customizations possible
- Integrates with upstream and downstream processes
Limitations
- High initial capital investment
- Complex programming and setup
- Requirement of flat, leveled floor
- Trained staff needed for operation
- Production losses in case of defects
- Special cranes needed for tool change
- Manual feeding and unloading of coils
- Limited thickness and width capacity
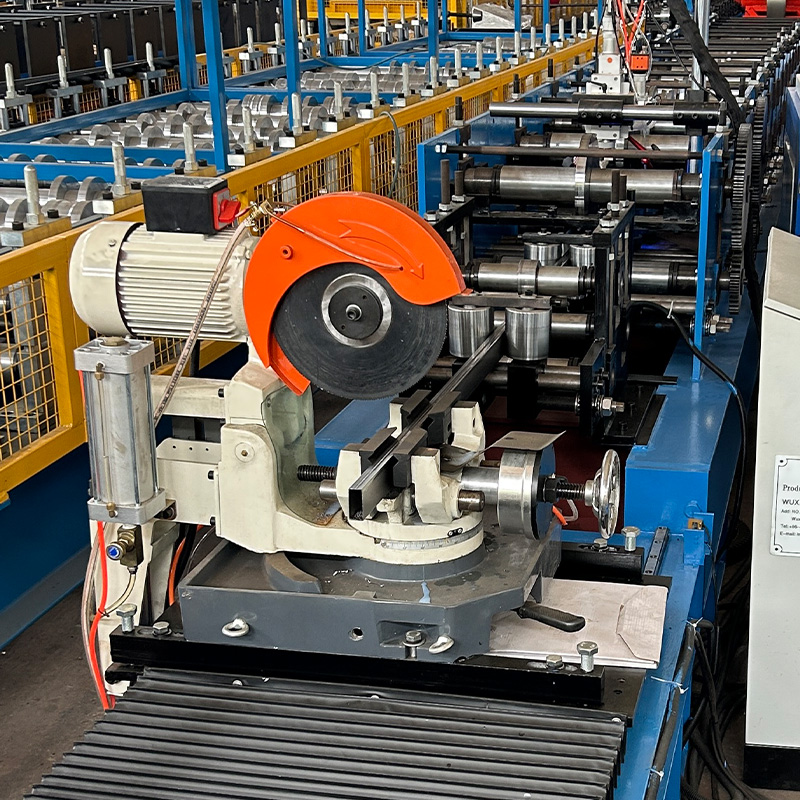
FAQs
Q: What is the difference between a C and Z purlin?
A: C sections have a C-shaped cross section with lips facing inwards while Z sections have lips facing outwards. The orientation provides differences in structural capacity.
Q: What materials can be used for roll forming purlins?
A: Hot-dipped galvanized steel and cold-rolled steel coils are commonly used. Aluminum, stainless steel and painted coils can also be formed.
Q: What determines the production speed of the machine?
A: Parameters like material thickness, yield strength, number of passes, part length, tooling design, and main drive motor power all impact the maximum speed.
Q: How to calculate the operational cost?
A: Consider fixed costs like initial machine investment, facilities, and labor. Variable costs involve material consumption rate, utilities per hour, and maintenance parts/service.
Q: What safety equipment should operators wear?
A: Essential PPE gear includes safety shoes, gloves, ear protection, eye glasses, and head protection when working around or maintaining the running machine.
Q: What are some major purlin roll forming defects?
A: Twisted profiles, dimensional variations, flange distortions, longitudinal bowing, and angular leg distortions are some typical defects requiring troubleshooting.
Q: How much area is needed for a complete line?
A: Approximately 5-10 meters width for the inline equipment and 5-8 meters length for the common profile lengths needed. Height of 6 meters for material handling.
Q: What is the difference between manual, semi-automatic and automatic models?
A: Manual models involve manual loading of coils, feeding sheets, and offloading sections. In semi-automatic, loading & unloading is manual while production is auto. Fully automatic uses robotics and conveyors for total hands-off operation.