Imagine a giant metal oven that can transform flat sheets of steel into wave-like panels with impressive strength and durability. That’s the magic of a corrugated roof panel roll forming machine. This industrial marvel is the unsung hero behind the vast stretches of metal roofs gracing commercial buildings, warehouses, and even residential structures.
In this comprehensive guide, we’ll delve into the world of corrugated roof panel roll forming machines, exploring their functionalities, various types, and the advantages they bring to the table. We’ll also unveil the key players in the market and equip you with the knowledge to make informed decisions if you’re considering incorporating this machine into your metal roofing operations.
Function of Corrugated Roof Panel Roll Forming Machines
At its core, a corrugated roof panel roll forming machine is a metalworking marvel designed to continuously shape sheet metal coils into specific corrugated profiles. Here’s a breakdown of its working principle:
- Feeding the Machine: The process begins with feeding a metal coil, typically made of galvanized steel or aluminum, into the machine. Imagine a giant roll of sheet metal, much like a long ribbon ready to be transformed.
- Shaping Through Stations: The unformed metal sheet then progresses through a series of stations, each equipped with precisely designed rollers. These rollers, metaphorically speaking, act like sculpting tools, gradually bending and shaping the metal into the desired corrugated profile. The number of stations can vary depending on the complexity of the final shape.
- The Final Cut: Once the metal sheet has traversed all the forming stations, a shearing unit precisely cuts the formed panel to the predetermined length.
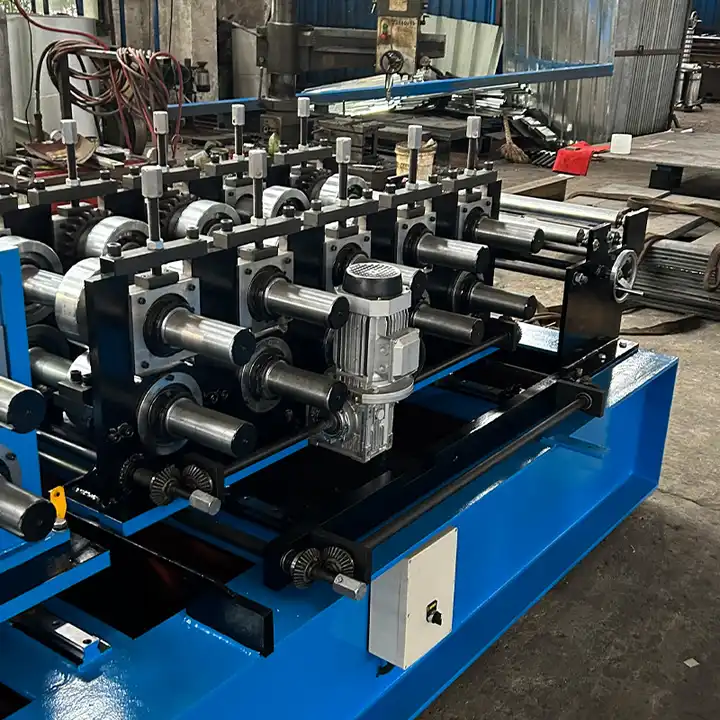
Types of Corrugated Roof Panel Roll Forming Machines
The world of corrugated roof panel roll forming machines isn’t a one-size-fits-all scenario. Here’s a glimpse into the diverse range of machines available:
- Single Profile Machines: These workhorses specialize in forming a single specific profile, such as the classic sinusoidal wave or the trapezoidal profile. They offer efficiency and affordability for high-volume production of a particular type of roofing panel.
- Multi-Profile Machines: For those who crave versatility, multi-profile machines are the answer. They can be configured to produce a wider range of corrugated profiles, offering greater flexibility for catering to diverse project needs. However, this versatility often comes at a higher price tag compared to single profile machines.
- Portable Roll Forming Machines: Not all roofing projects require a permanent production setup. Portable roll forming machines are designed for on-site production, particularly beneficial for remote locations or situations where pre-cut panels might be impractical due to transportation limitations.
Applications of Corrugated Roof Panel Roll Forming Machines
Corrugated roof panels, the brainchild of these roll forming machines, find application in a wide range of structures:
- Commercial Buildings: From industrial warehouses to shopping centers, corrugated metal roofs are a popular choice due to their affordability, durability, and low-maintenance requirements.
- Agricultural Structures: Barns, sheds, and other agricultural buildings often benefit from the weatherproof properties and cost-effectiveness of corrugated metal roofing.
- Residential Applications: While less common than in commercial settings, corrugated metal roofs can add a touch of rustic charm to certain residential styles, while offering the same benefits of longevity and weather resistance.
Advantages of Corrugated Roof Panel Roll Forming Machines
Investing in a corrugated roof panel roll forming machine can bring several advantages to your metal roofing operations:
- Increased Production Efficiency: Compared to relying on pre-manufactured panels, roll forming machines allow for on-demand production, streamlining your workflow and potentially reducing lead times.
- Reduced Costs: Eliminating dependence on pre-cut panels can lead to cost savings, especially for large-scale projects. Additionally, the ability to produce your own roofing materials reduces reliance on external suppliers.
- Material Customization: Roll forming machines offer the flexibility to work with different metal gauges and coatings, allowing you to tailor the roofing panels to specific project requirements.
- Reduced Waste: On-site production with roll forming machines minimizes the risk of damaged or mismatched pre-cut panels, leading to less material waste.
-
रोलिंग शटर स्लेट रोल बनाने की मशीन
-
Highway Guardrail End Terminal Forming Machine
-
Highway U/C Post Roll Forming Machine
-
2 Waves Highway Guardrail Roll Forming Machine
-
3 Waves Highway Guardrail Roll Forming Machine
-
विद्युत कैबिनेट फ्रेम रोल बनाने की मशीन
-
दीन रेल रोल बनाने की मशीन
-
दो लहरें राजमार्ग रेलिंग मशीन
-
तीन लहरें राजमार्ग रेलिंग मशीन
Choosing a नालीदार छत पैनल रोल बनाने की मशीन
Selecting the right corrugated roof panel roll forming machine requires careful consideration of several factors:
- Production Needs: Evaluate the volume and type of roofing projects you typically undertake. A single profile machine might suffice for high-volume production of a specific panel, while a multi-profile machine offers greater flexibility for diverse projects.
- Material Compatibility: Ensure the machine can handle the desired metal gauge and material type, such as galvanized steel or aluminum.
- Machine Features: Consider features like punching capabilities for ventilation holes or pre-cutting options for specific panel lengths.
Top Corrugated Roof Panel Roll Forming Machine Suppliers
Knowing the different types and advantages of corrugated roof panel roll forming machines is only half the battle. Now, let’s meet some of the key players who manufacture these industrial marvels:
- Englert Inc.: A renowned name in the metal roofing industry, Englert offers a range of roll forming machines, including their state-of-the-art MetalMan Multi-Panel Roofing Machine. This versatile machine boasts the ability to produce up to ten panel configurations, making it a favorite for those seeking flexibility.
- StandGroup: This global supplier presents a comprehensive portfolio of roll forming machines, including their SS4E-15 Double Standing Seam Roof Panel Roll Forming Machine. This machine caters specifically to standing seam roof panel profiles, known for their clean aesthetics and superior weather resistance.
- HZ Roll Forming Machinery: A Chinese manufacturer, HZ Roll Forming Machinery offers cost-effective solutions for corrugated roof panel production. Their machines prioritize functionality and affordability, making them a good option for budget-conscious buyers.
- New Tech Machinery: Specializing in portable roll forming machines, New Tech Machinery caters to contractors who require on-site production capabilities. Their machines are designed for portability and ease of use, making them ideal for remote locations or situations with limited space.
Pricing Considerations for Corrugated Roof Panel Roll Forming Machines
The price tag of a corrugated roof panel roll forming machine can vary significantly depending on several factors:
- Machine Capabilities: Single profile machines are generally less expensive than their multi-profile counterparts. The ability to handle thicker metal gauges or produce complex profiles can also drive up the cost.
- Brand Reputation: Established brands with a proven track record might command a premium compared to lesser-known manufacturers.
- Automation Level: Machines with advanced automation features, like automatic shearing or pre-punching capabilities, tend to be more expensive than their manual counterparts.
Here’s a glimpse into the typical pricing range for different types of corrugated roof panel roll forming machines (DISCLAIMER: Prices are based on publicly available information and may vary depending on specific configurations and supplier quotes):
- Single Profile Machine: Expect a starting range around $6,000 [5] and upwards, depending on the complexity of the profile and brand reputation.
- Multi-Profile Machine: The versatility comes at a cost, with multi-profile machines typically starting in the $8,000 and above range [8].
- Portable Roll Forming Machine: Due to their compact size and focus on essential functionalities, portable machines can be found in the $7,000 and up range [5].
Remember, these are just ballpark figures. It’s crucial to obtain quotes directly from various suppliers to get an accurate picture of pricing based on your specific needs and desired functionalities.
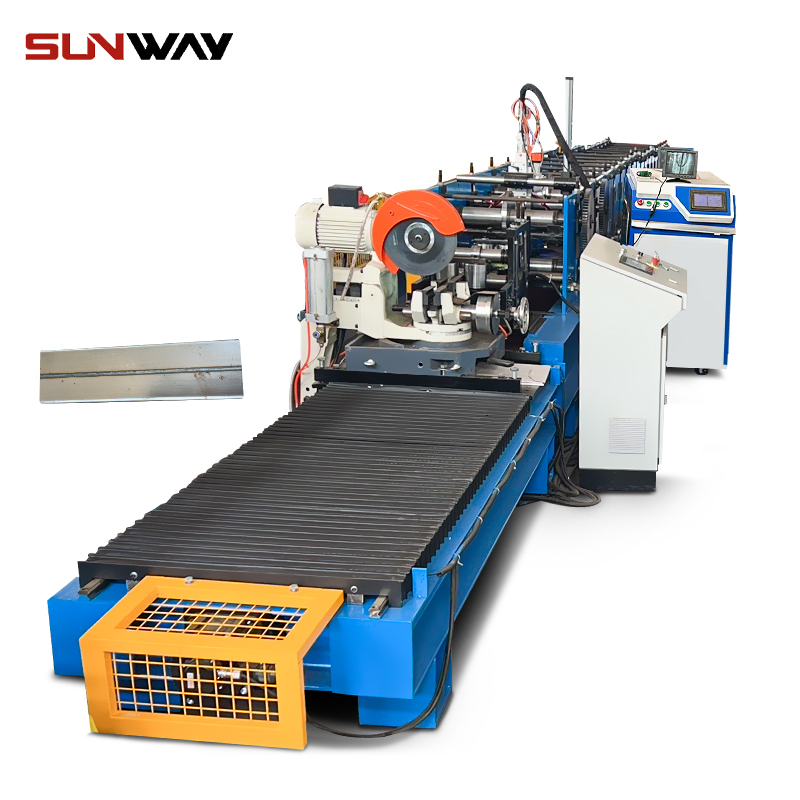
सामान्य प्रश्न
Q: What are the benefits of using a corrugated roof panel roll forming machine compared to purchasing pre-manufactured panels?
A: Several advantages come with owning a roll forming machine:
- Cost savings: On-demand production eliminates dependence on pre-cut panels, potentially reducing overall project costs.
- Reduced waste: Producing panels on-site minimizes the risk of damaged or mismatched pre-cut panels, leading to less material waste.
- Production flexibility: You can tailor the roofing panels to specific project requirements by using different metal gauges and coatings.
- Faster turnaround times: No need to wait for pre-ordered panels; on-site production allows for quicker response to project needs.
Q: I’m new to metal roofing. What’s the difference between a single profile and a multi-profile roll forming machine?
A: Single profile machines specialize in forming a specific corrugated profile, like the classic sinusoidal wave. They’re ideal for high-volume production of one particular panel type.
Multi-profile machines, on the other hand, offer more versatility. They can be configured to produce a wider range of corrugated profiles, catering to diverse project needs. However, this flexibility typically comes at a higher cost compared to single profile machines.
Q: How do I choose the right corrugated roof panel roll forming machine for my business?
A: Consider these factors when making your decision:
- Production volume and types of roofing projects you undertake.
- The desired level of profile variety (single profile vs. multi-profile).
- The types of metal and gauges you plan to work with.
- Budgetary constraints.
- Required features, such as punching capabilities or pre-cutting options.
It’s wise to consult with experienced roll forming machine suppliers and discuss your specific needs to ensure you select the most suitable machine for your operations.