Corrugated galvanized sheet metal—have you ever driven past a building and noticed the rugged, wave-like pattern on its roof or walls? That’s it! This iconic material has been a staple in construction for over a century, prized for its strength, durability, and aesthetic appeal. But beyond its familiar appearance lies a world of technical specifications, uses, and considerations that make it an essential topic for anyone involved in building, manufacturing, or material selection.
In this comprehensive guide, we’ll take a deep dive into corrugated galvanized sheet metal, exploring everything from its history and types to how it’s made, its applications, and how to choose the best supplier. Whether you’re a seasoned professional or a curious DIY enthusiast, this guide will equip you with everything you need to know about this versatile material.
Overview of Corrugated Galvanized Sheet Metal
Corrugated galvanized sheet metal is made by rolling sheets of steel or iron through a corrugation process and then coating them with zinc to protect against rust and corrosion. The result is a lightweight, durable, and versatile material commonly used in roofing, siding, fencing, and various other applications.
The corrugation gives the sheet its distinctive ridges and valleys, which not only add strength but also help in channeling water away, making it particularly useful in construction where weather resistance is a priority. Galvanization, the process of coating the metal with zinc, adds another layer of protection, ensuring the sheet can withstand the elements for decades.
Why is Corrugated Galvanized Sheet Metal So Popular?
The combination of durability, weather resistance, ease of installation, and cost-effectiveness makes corrugated galvanized sheet metal a favorite in various industries. It’s lightweight yet strong, easy to work with yet incredibly resilient, and it offers a unique aesthetic appeal that blends industrial toughness with a modern look.
But what truly sets it apart is its versatility. From rural barns to urban skyscrapers, corrugated galvanized sheet metal can be found just about everywhere, serving as both a functional material and a design element. And with advancements in technology, today’s corrugated sheets come in a wide range of types and finishes, allowing for even more applications.
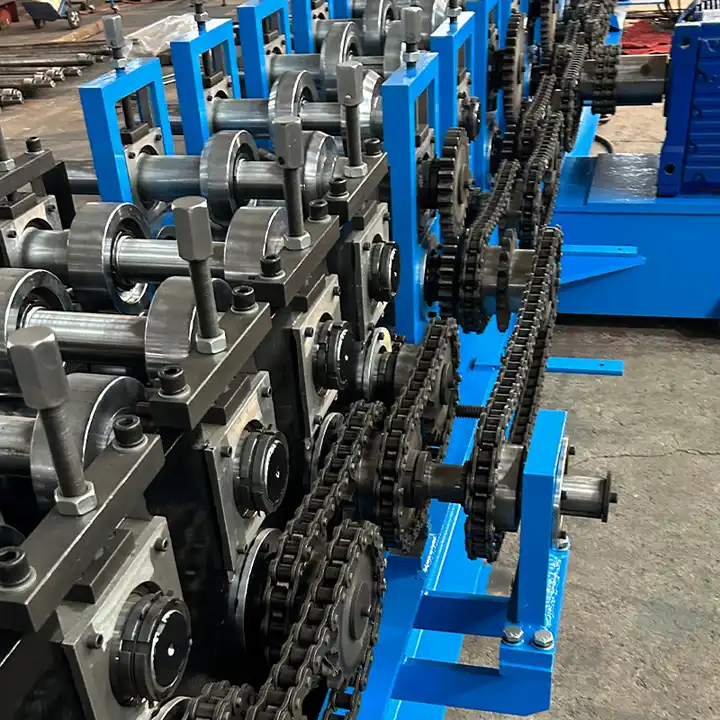
A Complete Guide to Corrugated Iron Sheets
Corrugated iron sheets are a subtype of corrugated galvanized sheet metal, and they’ve been a construction staple for over a century. Originally made from wrought iron, modern corrugated iron sheets are typically made from steel and coated with zinc for protection against rust.
These sheets are characterized by their corrugated pattern, which provides additional strength and helps with water drainage. The corrugation process, combined with galvanization, makes these sheets particularly well-suited for roofing, cladding, and fencing.
Types of Corrugated Galvanized Sheet Metal
Corrugated galvanized sheet metal comes in various types, each suited to specific applications. The differences lie in the materials used, the thickness of the sheets, the size and shape of the corrugations, and the type of galvanization. Here’s a detailed look at the most common types:
Type | Description | Best Uses |
---|---|---|
G90 Galvanized Steel Sheet | High zinc coating (90 oz/ft²) for superior corrosion resistance. | Ideal for coastal areas, high moisture environments. |
G60 Galvanized Steel Sheet | Medium zinc coating (60 oz/ft²), balancing cost and corrosion protection. | Suitable for most general construction applications. |
G40 Galvanized Steel Sheet | Lower zinc coating (40 oz/ft²), more cost-effective but less durable in harsh environments. | Best for interior applications or dry climates. |
Hot-Dipped Galvanized Sheet | Steel sheets dipped in molten zinc, providing a thick, uniform coating. | Heavy-duty applications, roofing, and outdoor use. |
Electro-Galvanized Sheet | Steel sheets coated with zinc through an electrochemical process, resulting in a thinner coating. | Used where a smoother surface is desired. |
Corrugated Aluminum Sheet | Lightweight, non-corrosive, often used where rust is a significant concern. | Perfect for roofing, siding in coastal regions. |
Color Coated Galvanized Sheet | Galvanized sheets with a color finish, offering both aesthetic appeal and additional protection. | Decorative cladding, modern building designs. |
Zincalume Steel Sheet | Coated with a mixture of zinc and aluminum, offering better resistance to corrosion compared to traditional galvanized steel. | Suitable for extreme weather conditions. |
Galvalume Steel Sheet | Coated with aluminum-zinc alloy, providing a highly durable and corrosion-resistant surface. | Ideal for industrial and commercial roofing. |
Polyester Coated Steel Sheet | A galvanized sheet with a polyester finish, enhancing corrosion resistance and providing a range of colors. | Great for residential roofing and siding. |
Each of these types has its unique strengths and is suited to specific environments and applications. The choice depends on factors such as the climate, the type of building, aesthetic preferences, and budget.
The Working Process of Corrugated Galvanized Sheet Metal
The manufacturing process of corrugated galvanized sheet metal involves several critical steps, each contributing to the final product’s strength, durability, and appearance. Here’s an overview of how it’s done:
- Material Selection: The process begins with selecting high-quality steel or iron sheets, depending on the desired characteristics of the final product. Steel is the most common material used due to its strength and flexibility.
- Sheet Rolling: The selected metal sheets are then passed through rollers that create the characteristic corrugations. This step is crucial as it not only shapes the metal but also enhances its structural integrity. The corrugations help distribute stress and make the sheet more resistant to bending and breaking.
- Galvanization: After rolling, the sheets are cleaned and dipped in a bath of molten zinc. This hot-dipping process coats the metal with a layer of zinc, which bonds with the steel or iron to form a protective barrier against rust and corrosion.
- Cooling and Quality Control: Once coated, the sheets are cooled and inspected for quality. The thickness of the zinc coating is measured to ensure it meets the required standards, and the sheets are checked for any defects or inconsistencies.
- Cutting and Finishing: The galvanized sheets are then cut to the desired size and shape. Some sheets may also undergo additional finishing processes, such as painting or coating with other materials, depending on the intended use.
- Packaging and Distribution: Finally, the finished sheets are packaged and shipped to distributors or directly to customers, ready for installation in various applications.
This process ensures that each sheet of corrugated galvanized metal is strong, durable, and ready to withstand the rigors of its intended use.
-
Highway Guardrail End Terminal Forming Machine
-
Highway U/C Post Roll Forming Machine
-
2 Waves Highway Guardrail Roll Forming Machine
-
3 Waves Highway Guardrail Roll Forming Machine
-
विद्युत कैबिनेट फ्रेम रोल बनाने की मशीन
-
दीन रेल रोल बनाने की मशीन
-
दो लहरें राजमार्ग रेलिंग मशीन
-
तीन लहरें राजमार्ग रेलिंग मशीन
-
केबल सीढ़ी रोल बनाने की मशीन
Key Components and Their Functions in Corrugated Galvanized Sheet Metal
Understanding the key components of corrugated galvanized sheet metal is crucial for anyone looking to work with this material. Each component plays a specific role in ensuring the sheet’s performance and longevity. Here’s a breakdown:
Component | Function |
---|---|
Base Metal (Steel/Iron) | Provides the core strength and rigidity of the sheet, forming the structural backbone that supports the material’s overall performance. |
Zinc Coating | Protects the base metal from corrosion and rust, extending the lifespan of the sheet, especially in harsh environments. |
Corrugations | Enhance the sheet’s structural integrity, allowing it to withstand greater loads and resist bending and deformation. |
Paint/Finish Coating | Adds an additional layer of protection and can provide aesthetic benefits, such as color matching with other building materials. |
Edge Treatments | Seals the edges of the sheet to prevent moisture ingress and improve the overall durability and safety of the installation. |
Fasteners | Secures the sheet to the structure, ensuring it remains in place and can withstand environmental forces like wind and rain. |
Sealants | Used in conjunction with fasteners to provide a watertight seal, preventing leaks and further protecting the underlying structure from water damage. |
Each of these components works together to create a product that is not only strong and durable but also versatile and easy to work with. Whether you’re installing a roof, building a fence, or cladding a wall, understanding these components will help you make informed decisions about the materials and methods you use.
Machine Speed and Efficiency in Manufacturing Corrugated Galvanized Sheet Metal
Efficiency in manufacturing is critical, especially when producing materials like corrugated galvanized sheet metal, where precision and consistency are key. Here’s a look at how machine speed and efficiency impact the production process:
Parameter | Description |
---|---|
Rolling Speed | The speed at which the metal sheet passes through the corrugating rollers. Higher speeds increase production but require more precise control to maintain quality. |
Galvanization Speed | The rate at which sheets are coated with zinc. Faster speeds can increase output but may require adjustments to ensure the coating is uniform and meets thickness standards. |
Cooling Efficiency | Refers to how quickly the sheets can be cooled after galvanization without compromising the integrity of the zinc coating. |
Quality Control Rate | The percentage of sheets that pass quality checks without requiring rework. Higher rates indicate a more efficient production process. |
Overall Production Speed | Combines rolling, galvanization, and finishing processes |
. Optimizing each step can significantly increase overall production efficiency. |
Balancing speed and efficiency in production is crucial to maintaining the quality of corrugated galvanized sheet metal. Manufacturers must continuously monitor and adjust their processes to ensure they are producing high-quality sheets while meeting demand.
Customized Mechanical Parameters of Corrugated Galvanized Sheet Metal
Customization is often necessary to meet specific project requirements. Here’s a look at the mechanical parameters that can be adjusted in corrugated galvanized sheet metal:
Parameter | Description |
---|---|
Sheet Thickness | Can range from 0.2mm to 1.2mm, depending on the application. Thicker sheets offer more strength but are heavier and more difficult to work with. |
Corrugation Depth | The height of the ridges, which can be adjusted to provide different levels of strength and flexibility. |
Corrugation Pitch | The distance between the peaks of the corrugations, affecting the sheet’s load-bearing capacity and aesthetic appearance. |
Zinc Coating Thickness | Can be customized based on the environment the sheet will be exposed to. Thicker coatings offer better corrosion resistance but add cost and weight. |
Width and Length | Sheets can be cut to specific sizes to fit the exact requirements of a project, minimizing waste and simplifying installation. |
Surface Finish | Options include plain, polished, or color-coated finishes, each offering different levels of protection and aesthetic appeal. |
These customizable parameters allow manufacturers to produce corrugated galvanized sheet metal that meets the exact needs of their customers, whether for a large industrial project or a small residential renovation.
Applications and Uses of Corrugated Galvanized Sheet Metal
Corrugated galvanized sheet metal is used in a wide variety of applications, thanks to its versatility, durability, and aesthetic appeal. Here’s a look at some of the most common uses:
आवेदन | Description |
---|---|
Roofing | One of the most common uses, providing durable, weather-resistant protection for homes, barns, and industrial buildings. |
Wall Cladding | Used to add a rugged, industrial look to buildings while providing protection against the elements. |
Fencing | Provides a strong, durable barrier for properties, often used in agricultural and industrial settings. |
Siding | Adds an extra layer of protection and insulation to buildings, with the corrugated pattern offering additional strength. |
Flooring | Used in industrial settings where a strong, durable, and non-slip surface is required. |
Sheds and Outbuildings | Ideal for constructing weather-resistant structures that are quick and easy to assemble. |
Greenhouses | Used to build frames and roofs, offering a durable and cost-effective solution for agricultural use. |
Temporary Structures | Often used in construction sites or disaster relief areas where quick, durable shelters are needed. |
Transportation | Used in the construction of containers, trailers, and truck bodies, where strength and durability are crucial. |
Architectural Features | Used in modern architectural designs for both functional and decorative purposes, adding an industrial aesthetic to buildings. |
The versatility of corrugated galvanized sheet metal makes it a popular choice across a wide range of industries. Whether you’re building a barn in the countryside or designing a modern urban structure, this material offers the strength, durability, and aesthetic appeal you need.
Installation, Operation, and Maintenance of Corrugated Galvanized Sheet Metal
Proper installation, operation, and maintenance are key to ensuring the longevity and performance of corrugated galvanized sheet metal. Here’s what you need to know:
Aspect | विवरण |
---|---|
Installation | Install sheets with the corrugations running vertically or horizontally, depending on the application. Use appropriate fasteners and sealants to ensure a watertight fit. |
Operation | Corrugated galvanized sheet metal is generally low-maintenance. However, it’s important to ensure that the sheets are securely fastened and that any damage is promptly repaired. |
Maintenance | Regularly inspect for signs of rust, especially at the edges and around fasteners. Clean the sheets periodically to remove dirt and debris, which can cause corrosion over time. |
By following these guidelines, you can ensure that your corrugated galvanized sheet metal installations last for decades, providing reliable protection and performance.
Suppliers and Price Range for Corrugated Galvanized Sheet Metal
Finding the right supplier is crucial for obtaining high-quality corrugated galvanized sheet metal at a competitive price. Here’s a look at some considerations when choosing a supplier and the typical price ranges:
Supplier | Price Range (per square foot) | Key Considerations |
---|---|---|
National Manufacturers | $1.50 – $2.50 | Offer a wide range of products and customizations, but may have longer lead times. |
Local Suppliers | $1.20 – $2.00 | Quicker delivery and more personalized service, but may have a more limited selection. |
Online Retailers | $1.00 – $2.00 | Convenient and often cheaper, but you may not be able to inspect the product before purchase. |
Wholesale Distributors | $0.90 – $1.80 | Best for bulk purchases, offering significant discounts but often requiring larger minimum orders. |
When choosing a supplier, consider factors such as the range of products offered, customization options, delivery times, and customer service. It’s also important to compare prices from multiple suppliers to ensure you’re getting the best deal.
How to Choose the Best Supplier for Corrugated Galvanized Sheet Metal
Selecting the right supplier can make all the difference in the success of your project. Here’s a guide on how to choose the best supplier for corrugated galvanized sheet metal:
- Evaluate Product Quality: Look for suppliers with a reputation for high-quality products. Check reviews, ask for samples, and inquire about the materials and processes used in manufacturing.
- Assess Customization Options: If your project requires specific sizes, thicknesses, or finishes, make sure the supplier can accommodate these needs.
- Consider Lead Times: Time is often a critical factor in construction projects. Choose a supplier that can meet your deadlines without compromising on quality.
- Compare Prices: Get quotes from multiple suppliers and compare not just the prices, but also the value offered. Consider factors like shipping costs, minimum order quantities, and bulk discounts.
- Check Customer Support: Good communication and support can make a big difference, especially if issues arise. Choose a supplier with responsive and helpful customer service.
By taking the time to choose the right supplier, you can ensure that you get the best possible product for your needs, at a price that fits your budget.
Advantages and Limitations of Corrugated Galvanized Sheet Metal
Like any material, corrugated galvanized sheet metal has its pros and cons. Here’s a comparison to help you decide if it’s the right choice for your project:
Advantages | Limitations |
---|---|
Durability | Highly resistant to rust and corrosion, especially in harsh environments. |
Lightweight | Easier to handle and install compared to other materials like concrete or wood. |
प्रभावी लागत | Generally more affordable than alternative materials, especially for large-scale projects. |
बहुमुखी प्रतिभा संपन्न | Can be used in a wide range of applications, from roofing to fencing to decorative features. |
Low Maintenance | Requires minimal upkeep, with occasional cleaning and inspections. |
Aesthetic Appeal | Offers a unique industrial look that’s popular in modern and rustic designs. |
Susceptibility to Denting | Can be prone to dents or damage if struck by heavy objects, especially in thin gauges. |
Noise Levels | Can be noisier during heavy rain or hail compared to other roofing materials, though this can be mitigated with insulation. |
Limited Insulation | Metal is a poor insulator, so additional insulation may be needed in applications like roofing or siding. |
Potential for Rusting | While galvanized, the metal can still rust over time if the zinc coating is damaged or in extremely harsh environments. |
Initial Cost | While generally affordable, the cost can increase significantly with thicker gauges, custom finishes, or higher zinc coatings. |
Understanding these advantages and limitations will help you make an informed decision about whether corrugated galvanized sheet metal is the right choice for your project.
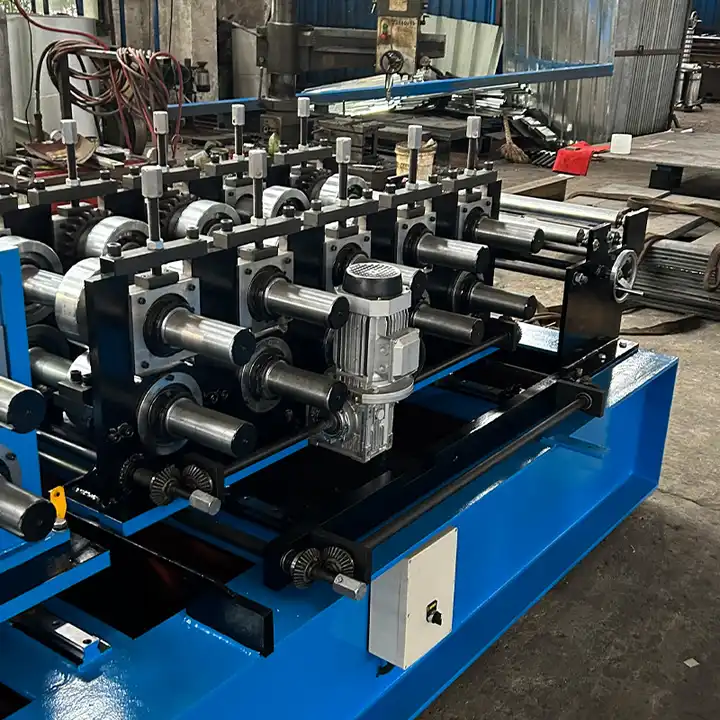
सामान्य प्रश्न
Question | Answer |
---|---|
What is corrugated galvanized sheet metal used for? | It’s commonly used for roofing, siding, fencing, and other construction applications where durability and weather resistance are required. |
How long does corrugated galvanized sheet metal last? | With proper installation and maintenance, it can last 30-50 years or more, depending on the environment and the quality of the zinc coating. |
Can corrugated galvanized sheet metal rust? | While the zinc coating protects against rust, the metal can still rust if the coating is damaged or worn away over time, especially in harsh environments. |
Is corrugated galvanized sheet metal easy to install? | Yes, it’s lightweight and relatively easy to handle, making it a popular choice for DIY projects as well as professional installations. |
What are the different types of corrugated galvanized sheet metal? | There are various types, including G90, G60, hot-dipped, electro-galvanized, and more, each with different levels of zinc coating and intended applications. |
Can I paint corrugated galvanized sheet metal? | Yes, it can be painted, especially if it has a factory-applied primer. Painting can also add an extra layer of protection against the elements. |
How do I maintain corrugated galvanized sheet metal? | Regular inspections, cleaning, and prompt repairs of any damage will help ensure the longevity of your corrugated galvanized sheet metal. |
Where can I buy corrugated galvanized sheet metal? | It’s available from national manufacturers, local suppliers, online retailers, and wholesale distributors. Choose a supplier based on your specific needs. |
What is the cost of corrugated galvanized sheet metal? | Prices can range from $0.90 to $2.50 per square foot, depending on the type, thickness, and supplier. |
Is corrugated galvanized sheet metal environmentally friendly? | It’s recyclable and has a relatively low environmental impact compared to other building materials, especially when considering its long lifespan. |
निष्कर्ष
Corrugated galvanized sheet metal is a versatile and durable material that has stood the test of time. Its combination of strength, weather resistance, and aesthetic appeal makes it a popular choice across a wide range of industries and applications. Whether you’re looking to build a new roof, clad a wall, or create an architectural feature, understanding the different types, applications, and considerations of corrugated galvanized sheet metal will help you make the best choice for your project.
From selecting the right type and thickness to choosing a reliable supplier, this guide has covered everything you need to know to make informed decisions. So, whether you’re a seasoned professional or a DIY enthusiast, you’re now equipped with the knowledge to use corrugated galvanized sheet metal to its fullest potential.