Containerized bemo sheet roll forming machines are prefabricated modular systems used to form metal sheets and coils into customized profiles. These machines offer advantages like easy transport, quick installation, and flexibility to meet varying production needs.
Introduction to Containerized Bemo Roll Formers
Bemo roll forming machines shaped into containerized units provide mobility and convenience over traditional permanent factories. Key features include:
Benefits
- Transportable to work sites for on-demand production
- Faster set up time and relocation
- Flexible capacity scaling
- Lower building costs
- Customizable configurations
- Ease of maintenance and operation
Components
- Forming sections, uncoilers, guides, punches, welding
- Electrical controls, hydraulic power units
- Feeding/collection tables, cooling zones
- Packed into weatherproof ISO containers
Working Principle
Sheet coils are passed through a series of powered rollers that continuously form the material into desired cross-sectional profiles step-by-step along the length.
Capabilities
- Sheet width up to 2.5m
- Material thickness 0.5-2mm
- Forming speed up to 30 m/min
- Section heights 10-300mm
- Length only limited by coil size
- Variety of structural, architectural, storage profiles
Containerized lines offer rapid deployments matching output volumes to current needs versus fixed onsite mills. Next we will cover typical configurations and components.
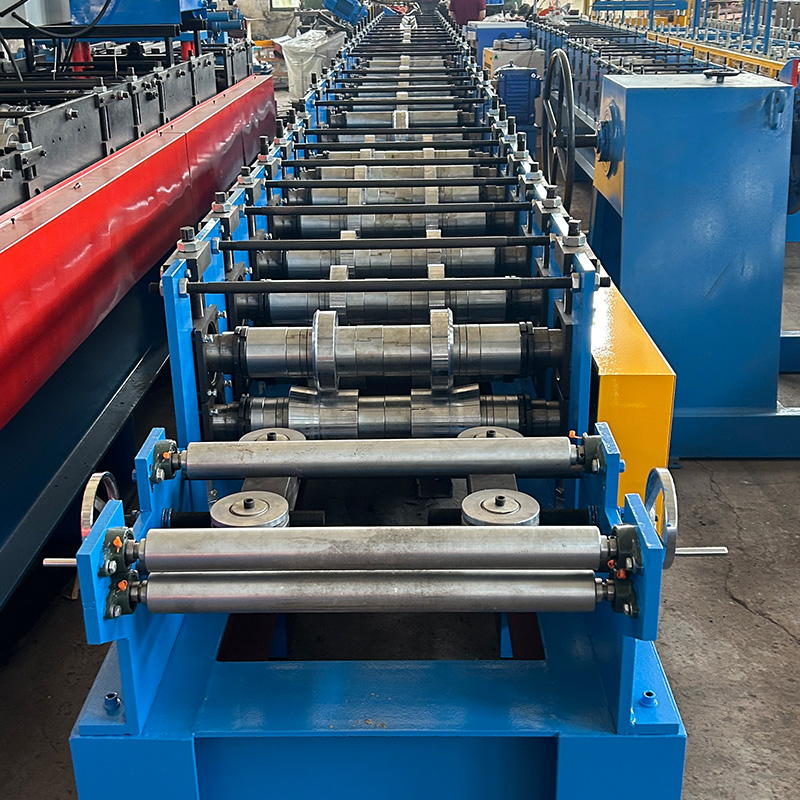
Standard Configurations of containerized bemo sheet roll forming machine
Containerized bemo roll former layouts utilize modular principles to customize capacities, profiles, and production workflows.
Typical Configurations
Line Type | Description |
---|---|
Entry-level | 1-3 forming sections in a single 40 ft container Lower output volumes Narrower sheet widths |
Intermediate | Additional forming sections Two 40 ft containers Higher volumes and part sizes |
Advanced | Three or more containers Fast production speeds Wide sheet capabilities |
Machine Sections
Component | Role |
---|---|
डेकोइलर | Feed sheet coil stock into line |
Roll forming stages | Incrementally shape sheet through sets of dies |
Punches, notches | Cut outs, holes, special features |
Welding | Join frame pieces and special fabrications |
Support tables | Straighten, guide, support sheet |
Cutoff saw | Cut formed profiles to length |
Hydraulic unit | Power forming machinery |
Control panel | Adjust and monitor line parameters |
By mixing and matching elements likedecoilers, roll stations, support tables, and saws into customized container cells, bemo lines can take on specialized capabilities. We will now examine the roll forming process in more detail.
Working Principle of Bemo Containerized Roll Forming
The rolling method forms metal sheets along their length by bending them gradually with series of roller dies. This Cold forming avoids heat treatments.
प्रक्रिया प्रवाह
- Sheet coil loaded onto powered unwind decoiler
- Feed tables with guides straighten sheet
- Forming sections with roller dies bend sheet incrementally
- Steel progresses through consecutive forming stages
- Last stage completes final shape profile
- Cutoff saw slices formed sections to length
- Formed parts exit line on outfeed tables
Forming Mechanism
- Roller dies mounted to consecutive stands
- Eccentric shafts or servos motorize stands
- Rolls continuously bend metal through calibrated gaps
- Sheet rotates 90° between each bending stage
- Gradually formed into desired profile
Profile Series
- Z purlins, C and U channels for structures
- Cladding sheets, panels, storage shelves
- Special architectural shapes
- Custom profiles designed to order
The modular design allows flexibility to add or removeforming sections to size production rates. We will now examine key components in more detail.
Main Components of Containerized Bemo Roll Lines
Containerized bemo roll formers comprise various sub-systems working together for high performance:
डेकोइलर
- Powered unwinding system
- Supports sheet coils up to 5 tons
- Braked mandrel control speed
- Guides sheet into line
Forming Sections
- Set of roll forming stands
- Mounted inside each container
- Each stand has profiled rolls
- Number of stands sets section height
Roll Tooling
- Hardened steel roller dies
- machined to profile shapes
- Mounted on eccentric shafts
- Rotate to bend sheet
Punching Unit
- Optional perforating module
- Punches holes, louvers, cuts
- Programmable patterns
- For ventilation, fasteners
Shearing
- Squaring shear or saw Slices formed sheets
- Length based on applications
- Conveyor transfer tables
Electrical Cabinet
- Central PLC logic controls
- HMI interface for adjustments
- Monitors line parameters
The modular containerized design allows for flexible combinations of decoilers, forming sections, punches, saws, and conveyors. Customized layouts enable optimized processes.
Working Capabilities of Bemo Containerized Roll Lines
Containerized Bemo roll formers produce finished cold-formed parts from coiled sheet metal:
Sheet Materials
- Mild steel
- Stainless steel
- Aluminum
- Special alloys
Sheet Capacity
- Width up to 2500mm
- Thickness 0.5-2mm
- Coil weight max 20 tons
Formed Profiles
- C, Z, U channels
- Lattice profiles
- Panel sheets
- Special shapes
Section Height
- Range from 10mm to 300mm
- Set by number of forming stands
Production Speed
- Up to 30 meters per minute
- Output ties to sheet width
Line Length
- Only limited by coil size
- Up to thousands of meters
Container length configurations adapt to desired volumes and adequate spacing between components to avoid sheet defects. We will examine the key parameters when designing these lines next.
-
रोलिंग शटर स्लेट रोल बनाने की मशीन
-
विद्युत कैबिनेट फ्रेम रोल बनाने की मशीन
-
दीन रेल रोल बनाने की मशीन
-
केबल सीढ़ी रोल बनाने की मशीन
-
पीवी माउंटिंग ब्रैकेट सी शेप प्रोफाइल रोल बनाने की मशीन
-
केबल ट्रे रोल बनाने की मशीन
-
स्टील का तार लंबाई लाइन मशीन में कटौती
-
स्टील का तार लंबाई लाइन मशीन में कटौती
-
स्टील का तार लंबाई लाइन मशीन में कटौती
Containerized Bemo Roll Former Design
Properly designing containerized bemo roll formers involves configuring for sheet widths, production rates, and profiles:
Sheet Width
- Maximum width ties to capacity
- More containers for wider sheets
- 2500mm max standard
बनाने की गति
- Increases with more stations
- Limit defects with proper tables
- Up to 30m/min based on width
Profile Height
- Set by container forming sections
- More stands increase height
- Range from 10mm to 300mm
Line Length
- Limited by coil size
- Space for loop control
- Tables guide sheet
Power Level
- Electric or hydraulic drives
- Size capacity needs
- Backup options
नियंत्रण प्रणाली
- Central PLC logic
- HMI for operation
- Monitoring sensors
The modular containerized design allows flexibility to achieve required production parameters by mixing and matching functional modules. We will examine the workflow and key processes next.
Working Process on Containerized Bemo Roll Lines
There are five key phases which make up the sheet rolling process:
1. Decoiling
- Powered unwind system
- Braked tension control
- Guide rollers straighten sheet
2. Entry
- Support tables with side guides
- Alignment rollers
- Sheet notch detection
3. Roll Forming
- Series of roller die stands
- Sheet pre-bent and final shaped
- Eccentric shafts drive rotation
- Post-forming
- Cooling zones
- Correction rollers
- Punching stations
- Exit
- Square shearing blade
- Conveyor tables
- Formed parts unloading
Continuous monitors and feedback loops control line speed, monitoring sheet position accuracy through all stages. Operators can fine tune parameters via central HMI touchscreen controls to dial in profiles. The production flexibility and mobility of containerized lines enable optimal workflows.
Advantages of Containerized Bemo Roll Lines
There are many benefits to utilizing containerized bemo roll formers versus fixed location machines:
Transportability
- Relocate equipment to work sites
- Set up quickly on demand
- Scale capacity where needed
Low Installation
- No need for building erection
- Connect utilities & run
- Weatherproof enclosures
Flexibility
- Custom layouts & capabilities
- Modify by adding containers
- Rent extra capacity if needed
Low Cost
- No property or building
- Lease financing options
- Used market availability
सहायता
- Technical experts available
- Staff training
- Maintenance help included
Containerized lines provide optimal deployment flexibility plus the backing of experienced manufacturers. We will compare permanent versus containerized next.
Comparison – Permanent vs Container Roll Lines
There are tradeoffs when considering permanent buildings versus containerized roll formers:
Parameter | Permanent | Containerized |
---|---|---|
Set up time | Months | Days to weeks |
Relocation ability | None | Easy transport |
Layout flexibility | Fixed | Customizable modules |
Initial investment | Higher building costs | Lower startup cost |
Structural support | Existing building | Self-contained units |
Weather protection | Required cladding | Integral enclosures |
Expandability | Limited space | Add more containers |
Ownership model | Purchase equipment | Leased financing |
Secondary market | Some resale value | Wider demand when finishing projects |
Permanent factories require purpose-built structures while containerized systems offer faster deployments. We examine application areas and industry uses next.
Application Areas and Uses
Containerized Bemo roll lines serve industries needing mobility and modular capacity:
Rapid Deployment
- Disaster rebuilding
- Relief housing projects
- Military site installations
Remote Operation
- Mining complexes
- Oil/gas temporary infrastructure
- Hydro & wind power projects
Supplemental Capacity
- Seasonal manufacturing peaks
- Overflow batch demands
- Expand production incrementally
Custom Fabrication
- HVAC ductwork
- Silo parts
- Special structural shapes
Field Workshops
- Precision onsite metalforming
- Bridge rehab projects
- Stadiums and venues
Built-in transportability enables containerized lines to serve markets needing adjustable forming capacity.
Buying Considerations for Containerized Bemo Roll Lines
When selecting containerized roll formers, key buying considerations include:
Reputation
- Experienced manufacturers
- Proven machine designs
- Background installing lines
Offerings
- Standard models vs customized
- Current & next gen versions
- Uptime guarantees & support
Flexibility
- Ability to reconfigure/expand
- Accommodate future needs
- Line redundancy
Component Quality
- European or Japanese preferred
- Durability for transport
- Uptime track record
Monitoring
- Sensors for sheet control
- Diagnostic feedback
- Alert messaging
Cost
- Purchase prices and leasing
- Operational costs
- Secondary value retention
Evaluating manufacturers on capability breadth, configurability, and overall value over machine lifetimes leads to optimal roll former selection. We will cover suppliers and pricing last.
Suppliers and Price Ranges
There are a handful of reputable global suppliers of containerized roll forming equipment with machines starting around $250,000:
Manufacturer | Origin | Container Configurations | Price Range |
---|---|---|---|
Bemo Systems | Netherlands | Up to 4 container lines | $250,000-$650,000 |
Famor | Poland | Multi-profile 3 container models | $325,000-$750,000 |
ROSENC | Denmark | Electric & hydraulic options | $350,000-$700,000 |
Bradbury | UK | 2 and 3 container lines | $400,000-$800,000 |
Rollvis | Slovenia | Custom solutions available | $300,000+ |
Metform | Turkey | Focus on sheet metal profiles | $200,000+ |
*Pricing varies based on line length, power levels, functional modules, and customization. Get quotes based on production parameters.
Leasing and financing options can reduce initial outlay. Support contracts are recommended for guaranteed uptime, maintenance, and buyback values after project completion. Containerized lines provide fast deploying production with flexible capacity.
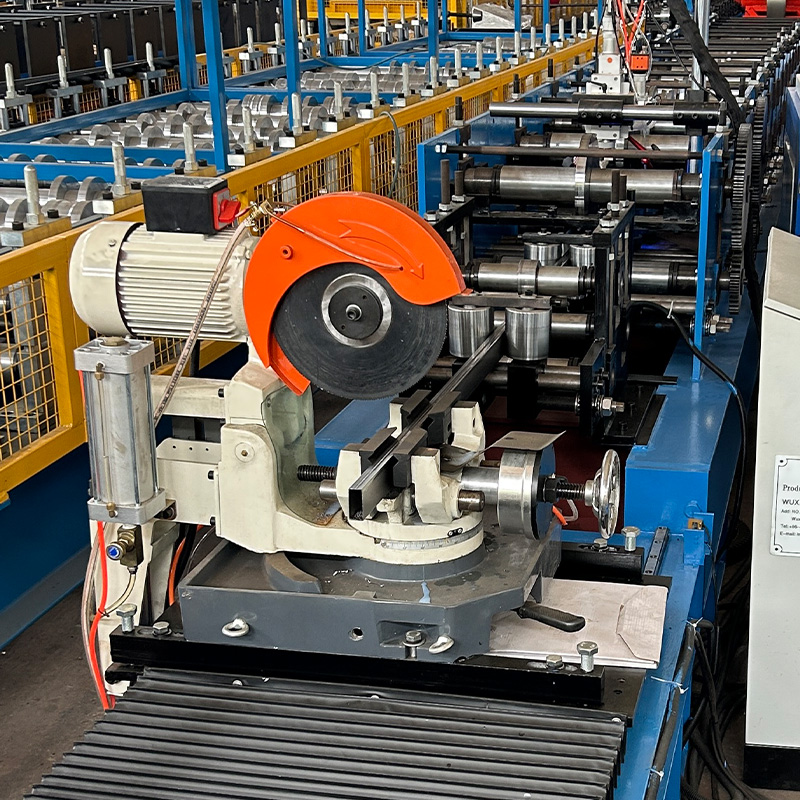
सामान्य प्रश्न
What are the shipping dimensions of containerized roll formers?
Standard containers are 12 meters (40 feet) long or 6 meters (20 feet) long. Heights up to 2.9 meters fit within ISO regulations.
How many tons per day can these lines produce?
Output ties to sheet width and line speed. Typical capacity ranges from 50 tons per month on compact lines up to 500+ tons monthly on 3+ container configs.
What structural support do containerized roll lines need?
Self-contained turnkey units only need flat concrete or packed earth foundations. No buildings required. Can mount directly on trailer frames.
What kind of warranty and technical support is included?
Reputable manufacturers provide 12 month warranties on machinery, +24 month extended care packages. Support includes remote diagnostics, preventative maintenance, and operator troubleshooting guides.
Can used containerized roll formers be purchased?
Some vendors sell refurbished units with warranties at 40-60% discounts after completing temporary factory projects. These provide affordable flexible capacity.
How long does it take to install & start running production?
Containerized lines can start trials in 1-3 weeks after delivery. Permanent roll former buildings take months for construction before equipment installation.