Overview of Cold Roll Forming Machines
Cold roll forming machines are essential in the manufacturing industry, particularly for shaping metal sheets into precise profiles. These machines operate at room temperature, hence the term “cold” roll forming, and are highly valued for their efficiency and precision. In this comprehensive guide, we’ll delve into every aspect of cold roll forming machines, from their operation and components to their advantages and uses in various industries.
What is a Cold Roll Forming Machine?
A cold roll forming machine is a type of equipment used to continuously shape metal sheets into desired profiles by passing them through a series of rollers. Unlike hot forming processes, cold roll forming is conducted at room temperature, which preserves the mechanical properties of the metal. This method is particularly advantageous for creating long, uniform shapes in high volumes.
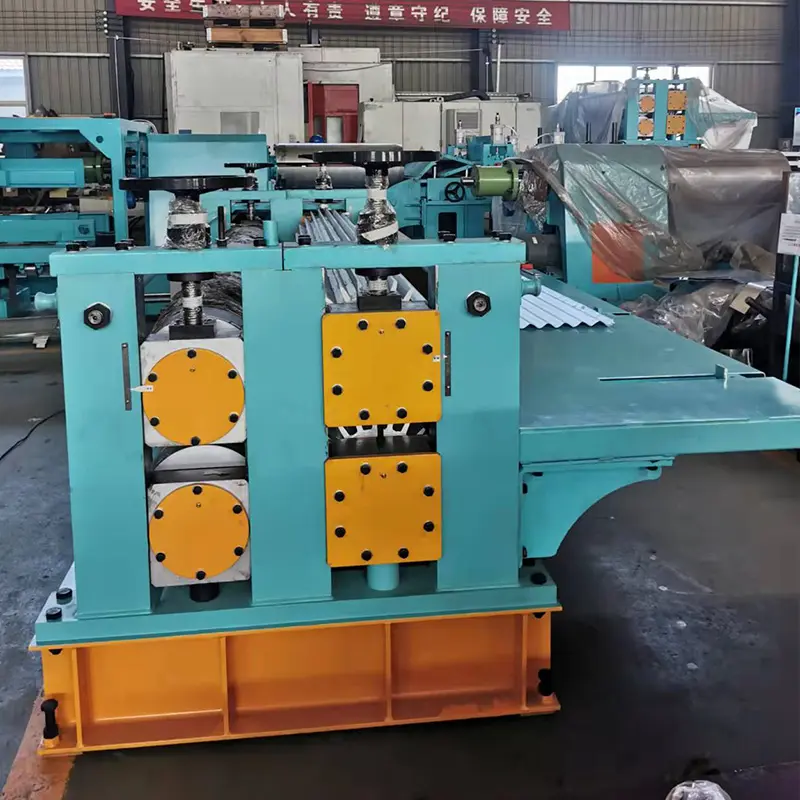
Key Components and Their Functions
Here’s a detailed look at the essential components of a cold roll forming machine and their functions:
Component | Function |
---|---|
Uncoiler | Holds and feeds the metal coil into the machine. |
Guiding Equipment | Ensures the metal strip is aligned correctly before entering the rollers. |
Rollers | Gradually shape the metal into the desired profile through successive stages. |
कटिंग सिस्टम | Cuts the formed metal into specified lengths. |
नियंत्रण प्रणाली | Manages the operation of the machine, including speed, alignment, and cutting. |
Exit Support | Supports the shaped metal as it exits the machine, preventing distortion. |
Types of Cold Roll Forming Machines
Cold roll forming machines come in various types, each suited for different applications. Here are some of the most common types:
Type | Description |
---|---|
Standard Roll Forming Machine | General-purpose machine used for a variety of profiles. |
High-Speed Roll Forming Machine | Designed for high production rates, ideal for mass production. |
Precision Roll Forming Machine | Used for creating profiles with tight tolerances and high accuracy. |
Adjustable Roll Forming Machine | Can be adjusted to produce different profiles without changing the entire roller setup. |
Multi-Profile Roll Forming Machine | Capable of forming multiple profiles simultaneously, increasing efficiency. |
Cassette Type Roll Forming Machine | Utilizes interchangeable cassettes for quick profile changeovers. |
Double Layer Roll Forming Machine | Features two sets of rollers to produce two different profiles concurrently. |
Portable Roll Forming Machine | Smaller, mobile units used for on-site roll forming, such as in construction sites. |
CNC Roll Forming Machine | Equipped with CNC controls for precise automation and complex profile production. |
Servo Roll Forming Machine | Uses servo motors for enhanced control over the forming process and higher precision. |
The Working Process of a High-Speed Roll Forming Machine
High-speed roll forming machines are engineered for rapid production, making them ideal for industries that require large quantities of formed metal profiles in short timeframes. Here’s a step-by-step look at their working process:
- Loading the Metal Coil: The process begins with loading a metal coil onto the uncoiler. The uncoiler feeds the coil into the machine at a controlled rate.
- Guiding and Aligning: The guiding equipment ensures the metal strip is correctly aligned as it enters the first set of rollers. Proper alignment is crucial to maintain the accuracy of the final profile.
- Forming: The metal strip passes through a series of rollers, each set gradually bending the strip into the desired shape. High-speed machines are equipped with precision-engineered rollers to ensure consistent shaping at high speeds.
- Cutting: Once the metal has been shaped, it reaches the cutting system. High-speed roll forming machines often use flying cutters, which move with the metal strip to cut it into specified lengths without stopping the machine.
- Exit Support: After cutting, the formed metal exits the machine onto the exit support, which maintains its shape and prevents any deformation.
-
Highway Guardrail End Terminal Forming Machine
-
Highway U/C Post Roll Forming Machine
-
2 Waves Highway Guardrail Roll Forming Machine
-
3 Waves Highway Guardrail Roll Forming Machine
-
वाइनयार्ड पोस्ट रोल बनाने की मशीन
-
ऑटो आकार बदलने योग्य सिग्मा शहतीर रोल बनाने की मशीन
-
ऑटो आकार बदलने योग्य CZ शहतीर रोल बनाने की मशीन
-
ऑटो आकार बदलने योग्य Z शहतीर रोल बनाने की मशीन
-
ऑटो आकार बदलने योग्य घन शहतीर रोल बनाने की मशीन
Precision Roll Forming Machine Types
Precision is key in many manufacturing processes. Here are various types of precision roll forming machines and their applications:
Type | आवेदन |
---|---|
Single Profile Precision Machine | Produces a single, highly precise profile, used in industries where exact dimensions are critical. |
Multi-Profile Precision Machine | Capable of switching between different precise profiles without significant downtime. |
Complex Profile Precision Machine | Designed for creating intricate profiles with multiple bends and shapes. |
Thin Gauge Precision Machine | Specializes in forming very thin metal sheets with high accuracy. |
Heavy Gauge Precision Machine | Used for thicker metal sheets, ensuring precision despite the increased material strength. |
Wide Strip Precision Machine | Handles wider metal strips, maintaining precision across the entire width. |
Narrow Strip Precision Machine | Focuses on narrow strips, often used in electronics and specialized manufacturing. |
High Strength Precision Machine | Forming high-strength materials while maintaining precise dimensions and avoiding material cracking. |
High Speed Precision Machine | Combines high-speed operation with precision, ideal for mass production of high-tolerance profiles. |
CNC Precision Machine | Utilizes computer numerical control for enhanced accuracy and complex profile creation. |
Speed and Efficiency of Cold Roll Forming Machines
Cold roll forming machines vary in speed and efficiency depending on their design and purpose. Here’s a comparison of different machine types:
Machine Type | Speed (m/min) | Efficiency |
---|---|---|
Standard Roll Forming Machine | 10-30 | High versatility but moderate speed. |
High-Speed Roll Forming Machine | 60-150 | Extremely high speed, suitable for large-scale production. |
Precision Roll Forming Machine | 5-25 | Lower speed due to focus on accuracy and tight tolerances. |
Adjustable Roll Forming Machine | 10-40 | Moderate speed with the flexibility of producing different profiles. |
Multi-Profile Roll Forming Machine | 20-60 | Good balance of speed and the ability to form multiple profiles simultaneously. |
Cassette Type Roll Forming Machine | 15-50 | Reasonable speed with quick changeover capabilities. |
Double Layer Roll Forming Machine | 20-70 | High efficiency with dual profile production. |
Portable Roll Forming Machine | 5-20 | Lower speed, designed for mobility and on-site use. |
CNC Roll Forming Machine | 10-40 | Precision-focused, moderate speed with high accuracy. |
Servo Roll Forming Machine | 15-50 | Enhanced control and efficiency, suitable for precision applications. |
Customized Mechanical Parameters
Cold roll forming machines can be customized to meet specific requirements. Here are some common mechanical parameters that can be tailored:
Parameter | Description |
---|---|
Profile Width | The width of the metal strip that can be processed, typically ranging from narrow strips to wide sheets. |
Profile Thickness | The thickness of the metal that can be handled, from thin gauges to heavy-duty sheets. |
Material Type | The type of metal used, such as steel, aluminum, copper, or titanium. |
रोलर सामग्री | The material of the rollers, often hardened steel for durability and precision. |
Roller Diameter | The diameter of the rollers, which affects the bending and shaping process. |
Cutting Length | The length to which the formed profiles are cut, which can be adjusted based on requirements. |
Machine Length | The overall length of the machine, which varies depending on the number of rollers and the complexity of the profiles. |
नियंत्रण प्रणाली | The type of control system used, from manual to advanced CNC controls. |
Production Speed | The speed at which the machine operates, customizable to balance speed and precision. |
Power Consumption | The amount of power required to operate the machine, which can be optimized for efficiency. |
Applications and Uses
Cold roll forming machines are used in various industries. Here’s a look at some common applications:
आवेदन | Description |
---|---|
Construction | Producing metal frames, roofing, and siding panels. |
Automotive | Forming structural components, chassis parts, and trim pieces. |
Aerospace | Creating lightweight yet strong profiles for aircraft structures. |
Electrical and Electronics | Manufacturing enclosures, brackets, and conductive pathways. |
Furniture | Shaping metal parts for desks, chairs, and storage systems. |
Appliances | Producing components for washing machines, refrigerators, and ovens. |
Transportation | Making parts for trains, buses, and ships. |
Agriculture | Forming machinery components and structural parts for agricultural equipment. |
Energy | Creating profiles for solar panel frames and wind turbine components. |
Storage Solutions | Producing shelving, racks, and other storage system components. |
Installation, Operation, and Maintenance
Proper installation, operation, and maintenance are crucial for the longevity and efficiency of cold roll forming machines. Here are key considerations:
Aspect | विवरण |
---|---|
Installation | Ensure a solid foundation, proper alignment, and electrical connections. Follow the manufacturer’s guidelines. |
Operation | Train operators thoroughly on the control system and safety procedures. Regularly check alignment and adjust as necessary. |
Maintenance | Schedule regular maintenance to inspect and replace worn parts, lubricate moving components, and ensure all systems are functioning correctly. |
Suppliers and Price Range Details
Choosing the right supplier is critical. Here’s an overview of some reputable suppliers and the typical price ranges for cold roll forming machines:
Supplier | Description | Price Range (USD) |
---|---|---|
सैमको मशीनरी | Offers a wide range of roll forming machines for various industries. | $50,000 – $300,000 |
फॉर्मटेक ग्रुप | Known for high-quality, durable machines with advanced features. | $60,000 – $350,000 |
Gasparini Industries | Specializes in customized solutions for complex profiles. | $70,000 – $400,000 |
Jinggong Science & Technology | Leading Chinese manufacturer with competitive pricing. | $40,000 – $250,000 |
Dallan | Focuses on innovative, high-precision roll forming machines. | $80,000 – $450,000 |
Fagor Arrasate | Provides robust machines for heavy-duty applications. | $90,000 – $500,000 |
Bradbury Group | Renowned for reliable and efficient roll forming systems. | $75,000 – $400,000 |
Zeman Bauelemente | Offers advanced, automated roll forming solutions. | $85,000 – $420,000 |
Tishken | Manufactures machines for a variety of metal forming needs. | $55,000 – $320,000 |
Yingkou Professional Roll Forming Machine Co. | Known for cost-effective, high-quality machines. | $35,000 – $200,000 |
How to Choose a Supplier
Selecting the right supplier involves several key considerations. Here are some tips to help you make an informed decision:
Consideration | विवरण |
---|---|
Reputation | Research the supplier’s history and read reviews from other customers. |
Quality of Machines | Evaluate the build quality, materials used, and technological advancements in their machines. |
Customization Options | Check if the supplier offers customization to meet your specific needs. |
After-Sales Support | Ensure they provide reliable after-sales support, including maintenance and parts supply. |
Price | Compare prices, but also consider the value and features offered. |
Delivery Time | Inquire about the lead time and ensure it aligns with your project schedule. |
Technical Expertise | Assess the supplier’s expertise and ability to handle complex technical requirements. |
Training and Installation | Confirm if they offer training for your staff and assistance with installation. |
Advantages and Disadvantages of Cold Roll Forming Machines
When considering cold roll forming machines, it’s essential to weigh their pros and cons:
Aspect | Advantages | Disadvantages |
---|---|---|
Precision | High precision in forming profiles with consistent dimensions. | Requires precise setup and maintenance to avoid defects. |
Efficiency | Suitable for high-volume production, reducing overall manufacturing time. | Initial setup can be time-consuming. |
Material Utilization | Minimal material wastage compared to other forming processes. | Limited to certain material thicknesses and types. |
Cost-Effectiveness | Lower operational costs in the long run due to reduced labor and material waste. | High initial investment in machinery and setup. |
Versatility | Capable of producing a wide range of profiles for various applications. | Less suitable for low-volume or custom production runs. |
Structural Integrity | Maintains the material’s mechanical properties and increases strength through work hardening. | Complex profiles may require multiple passes, increasing processing time. |
Automation | Easily integrated with automated systems for enhanced productivity. | High complexity in programming and maintaining automated systems. |
अनुकूलन | Customizable to produce specific profiles with unique features. | Customization can add to the cost and complexity of the machine. |
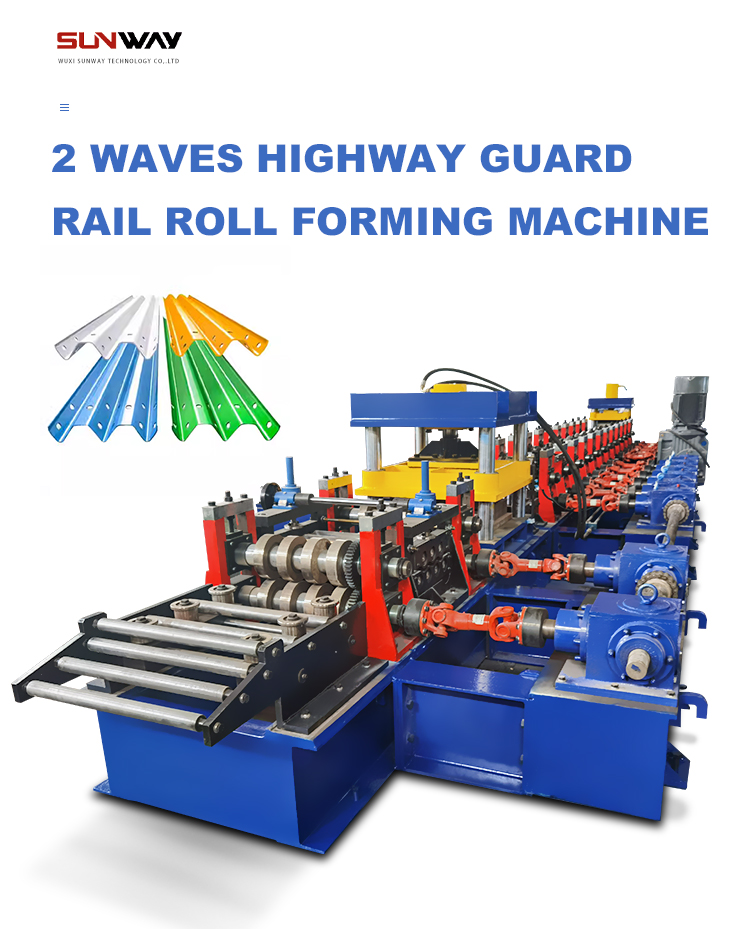
FAQs
Here are some frequently asked questions about cold roll forming machines, presented in a table format for clarity:
Question | Answer |
---|---|
What is the main advantage of cold roll forming? | It allows for high-precision, high-volume production of metal profiles with minimal waste. |
How does cold roll forming differ from hot roll forming? | Cold roll forming is done at room temperature, preserving material properties, while hot roll forming involves heating the metal. |
Can cold roll forming machines handle different materials? | Yes, they can process various metals, including steel, aluminum, copper, and more. |
What industries use cold roll forming machines? | Construction, automotive, aerospace, electronics, furniture, and many others. |
How do you maintain a cold roll forming machine? | Regular inspections, lubrication, alignment checks, and timely replacement of worn parts. |
Is it possible to customize the profiles produced? | Yes, machines can be customized to produce specific profiles based on user requirements. |
What factors affect the cost of a cold roll forming machine? | Machine size, complexity, customization, brand, and additional features. |
Are there portable cold roll forming machines? | Yes, portable models are available for on-site roll forming applications. |
What is the typical lifespan of a cold roll forming machine? | With proper maintenance, these machines can last for several decades. |
Do cold roll forming machines require skilled operators? | Yes, trained operators are necessary to ensure proper setup, operation, and maintenance. |
निष्कर्ष
Cold roll forming machines are indispensable tools in modern manufacturing, offering unmatched precision, efficiency, and versatility. Whether you’re in construction, automotive, aerospace, or another industry, understanding the capabilities and applications of these machines can help you make informed decisions and optimize your production processes. By considering factors like machine type, speed, customization options, and supplier reputation, you can select the best equipment to meet your specific needs and drive your business forward.