The transportation industry thrives on efficiency and durability. Trucks, the workhorses of the world, need to be built to withstand the demands of the road, and their side panels play a crucial role in their integrity. Carriage board forming machines are the unsung heroes behind these panels, shaping metal sheets into precise forms that contribute to a truck’s strength and functionality.
But what exactly are carriage board forming machines, and how do they work? Buckle up, and let’s delve into the fascinating world of these metal marvels!
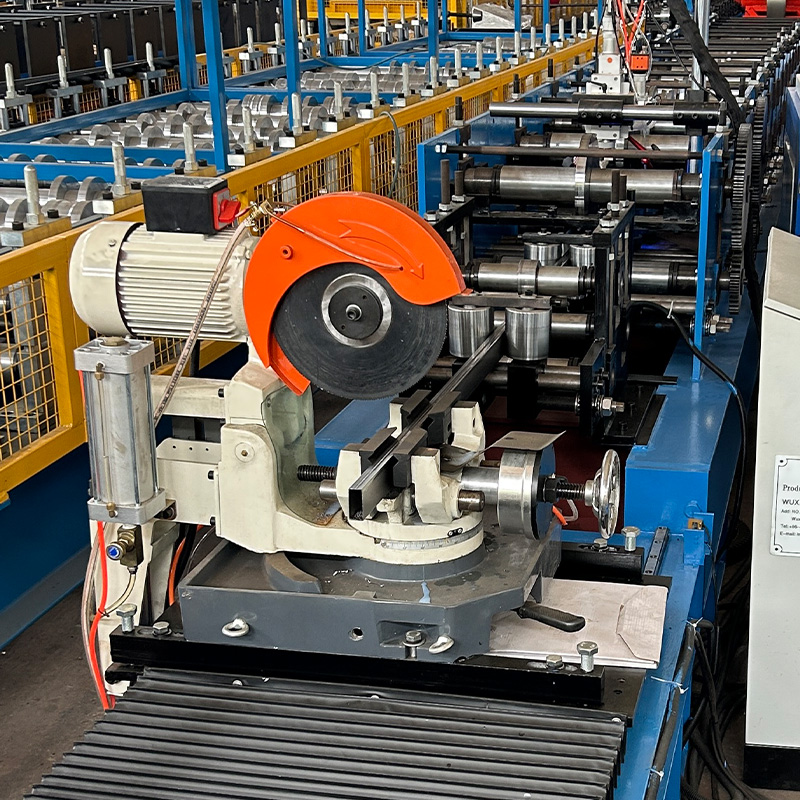
The Production Process of Carriage Board Forming Machines
Imagine a long, thin sheet of metal, like an unfurled ribbon. Now, picture a series of precisely machined rollers, each with a unique profile. As the metal sheet is fed through these rollers, they progressively bend and shape it, transforming it into a complex, three-dimensional form. That, in essence, is the magic of a carriage board forming machine.
Here’s a closer look at the production process:
- Uncoiling: The metal sheet, typically made from hot-rolled steel or galvanized steel, is loaded onto a large coil. The machine unwinds the coil, feeding the sheet into the forming process.
- Leveling: Before forming, the sheet needs to be perfectly flat. Leveling rollers ensure the sheet has a uniform thickness and eliminate any unwanted bends or ripples.
- Guiding and Looping: To maintain a continuous feed and prevent the sheet from getting taut, guiding systems and loopers are employed. These keep the metal sheet under controlled tension throughout the forming process.
- Feeding and Pre-Punching: Depending on the desired panel design, the machine might incorporate a feeding system that precisely measures and cuts the sheet to the required length. Additionally, pre-punching stations can create holes or slots in the sheet for fastening purposes.
- Roll Forming: This is the heart of the operation. The sheet is fed through a series of forming rollers, each progressively shaping the metal into the desired profile. The intricate design of these rollers determines the final shape and features of the carriage board.
- Welding (Optional): For certain applications, the formed panels might require welding along the seams to create a stronger, more rigid structure.
- Cutting and Stacking: Once the forming process is complete, the machine cuts the formed panel to the desired length and stacks them for easy handling and transport.
The entire process is usually automated, controlled by a computer numerical control (CNC) system that ensures precision and consistency in the production of carriage boards.
The Applications of Carriage Board Forming Machines
Carriage board forming machines are not just limited to producing side panels for trucks. Their versatility extends to a wider range of applications, including:
- Manufacturing of trailers: From enclosed trailers to open-bed trailers, carriage board forming machines can create the side panels that provide structural support and cargo containment.
- Construction applications: Prefabricated buildings, temporary structures, and even some roofing components can benefit from the lightweight yet sturdy panels formed by these machines.
- Automotive applications: While primarily used for trucks, some manufacturers also use carriage board forming machines to create panels for certain car models, particularly for light commercial vehicles.
- HVAC systems: In some instances, carriage board forming machines can be used to create components for heating, ventilation, and air conditioning systems, such as ductwork and panels.
The specific applications depend on the design capabilities of the machine and the desired properties of the formed panels.
A Look at Different Metal Powders for Carriage Board Forming
While hot-rolled steel and galvanized steel are the most common materials used in carriage board forming, some machines can work with other metal powders, each offering unique advantages and considerations:
Metal Powder | Description and Properties | Benefits | Considerations |
---|---|---|---|
High-strength steel | Offers superior strength and durability compared to standard steel, making it suitable for heavy-duty applications. | Increased load-bearing capacity, improved resistance to wear and tear. | Higher cost compared to standard steel, might require adjustments in forming process due to different material properties. |
Aluminum | Lightweight and corrosion-resistant, making it ideal for applications where weight reduction is crucial. | Lighter weight, better corrosion resistance than steel. | Lower strength compared to steel, might not be suitable for all applications requiring high load-bearing capacity. |
Stainless steel | Offers excellent corrosion resistance and aesthetic appeal. | Highly corrosion-resistant, visually appealing finish. | Higher cost compared to standard steel, requires specific forming techniques due to its work-hardening properties. |
Pre-painted steel | Comes pre-coated with a |
-
Highway Guardrail End Terminal Forming Machine
-
Highway U/C Post Roll Forming Machine
-
2 Waves Highway Guardrail Roll Forming Machine
-
3 Waves Highway Guardrail Roll Forming Machine
-
ऑटो आकार बदलने योग्य सिग्मा शहतीर रोल बनाने की मशीन
-
ऑटो आकार बदलने योग्य CZ शहतीर रोल बनाने की मशीन
-
ऑटो आकार बदलने योग्य Z शहतीर रोल बनाने की मशीन
-
ऑटो आकार बदलने योग्य घन शहतीर रोल बनाने की मशीन
-
विद्युत कैबिनेट फ्रेम रोल बनाने की मशीन
Where Rolling Shutter Forming Machines Shine
Rolling shutter forming machines cater to a diverse range of applications, weaving their security and convenience into the fabric of our daily lives. Here are some prominent examples:
- Securing Businesses: Rolling shutters are omnipresent guardians of storefronts, malls, and commercial establishments. They offer a robust barrier against potential break-ins, vandalism, and adverse weather conditions, ensuring the safety of inventory and property.
- Protecting Homes: Rolling shutters are increasingly finding favor in residential settings, providing an extra layer of security for garages, workshops, and even entryways. They offer peace of mind to homeowners, especially in areas with high crime rates or prone to extreme weather events.
- Ensuring Industrial Security: Industrial facilities, warehouses, and factories rely heavily on rolling shutters to secure sensitive equipment, materials, and finished goods. Their ability to withstand harsh environments and deter unauthorized access makes them an invaluable asset for industrial security.
- Controlling Light and Temperature: Rolling shutters can be strategically employed to manage light and temperature, contributing to energy efficiency. Perforated rolling shutters, for instance, allow for natural ventilation while maintaining security, potentially reducing reliance on air conditioning in specific situations. Insulated rolling shutters can improve thermal insulation, potentially lowering heating and cooling costs.
- Enhancing Privacy and Noise Control: Rolling shutters offer the flexibility to control privacy and noise levels. They can be lowered to create a private space or shield against unwanted noise, making them suitable for applications like recording studios or workshops requiring soundproofing.
- Maintaining Fire Safety: Fire-resistant rolling shutters play a crucial role in fire safety protocols. They can help delay the spread of fire, providing valuable time for occupants to evacuate and firefighters to respond. This is especially critical in buildings with high fire risk, such as factories or warehouses storing flammable materials.
- Adapting to Diverse Needs: Rolling shutter forming machines can be customized to cater to a wide range of requirements. From varying sizes and thicknesses to specific profiles and finishes, these machines offer the versatility to create rolling shutters tailored to specific applications and aesthetic preferences.
Beyond the Machine: The Symphony of Benefits
Rolling shutter forming machines offer a multitude of benefits that extend beyond their core functionality. Here’s a glimpse into the advantages they bring to the table:
- Enhanced Security: By creating robust rolling shutters, these machines contribute significantly to improved security for businesses, homes, and industrial facilities. This translates to peace of mind, reduced risk of theft or damage, and potentially lower insurance premiums.
- Increased Efficiency: The ability to produce rolling shutters in-house or source them from local manufacturers using these machines can streamline the process and potentially reduce lead times compared to relying solely on pre-fabricated options.
- Cost-Effectiveness: While the initial investment in a rolling shutter forming machine might seem substantial, the long-term cost savings can be significant, especially for businesses with a frequent need for rolling shutters. Producing rolling shutters in-house eliminates the need to rely solely on external suppliers, potentially leading to lower overall costs over time.
- Versatility and Customization: As mentioned earlier, these machines offer the flexibility to create rolling shutters in various sizes, thicknesses, profiles, and finishes. This allows for customization to suit specific needs and preferences, ensuring a perfect fit for diverse applications.
- Durability and Longevity: Rolling shutters formed using these machines are known for their durability and ability to withstand harsh environmental conditions. This translates to a longer lifespan and potentially lower maintenance costs in the long run.
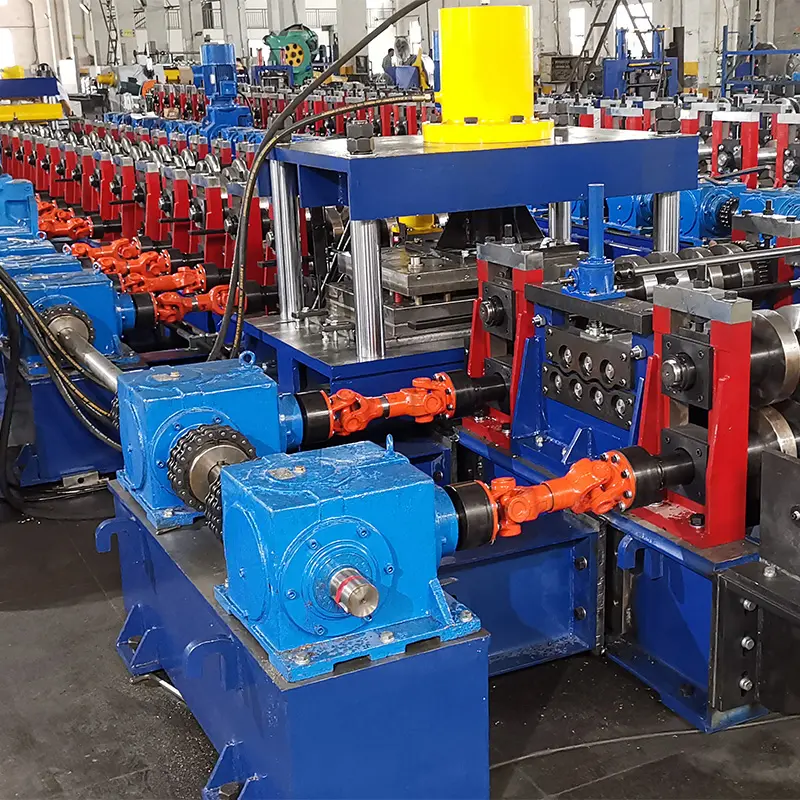
FAQs
Here are some frequently asked questions (FAQs) about rolling shutter forming machines to shed light on any lingering doubts:
Q: What factors should I consider when choosing a metal powder model for my rolling shutters?
A: Several factors come into play when selecting the ideal metal powder model. Consider the application, desired level of security, corrosion resistance requirements, weight limitations, budget, and aesthetic preferences. For instance, if security is paramount, high-strength steel might be the best choice. Conversely, if weight reduction is crucial, aluminum could be a suitable option.
Q: How complex is the operation of a rolling shutter forming machine?
A: The level of complexity can vary depending on the specific machine and its features. However, most modern machines are designed to be user-friendly and often come with comprehensive manuals and training programs. Additionally, experienced manufacturers or suppliers can provide guidance and support to ensure smooth operation.
Q: Where can I find reliable suppliers of rolling shutter forming machines?
A: Reputable manufacturers and distributors of rolling shutter forming machines can be found online, through industry directories, or by attending trade shows related to the construction or metalworking industries. Conducting thorough research, comparing different options, and seeking recommendations from trusted sources are crucial steps in finding a reliable supplier.
Q: Are there any environmental considerations when using rolling shutter forming machines?
A: Yes, environmental considerations are essential. Choosing sustainable and recyclable metal powder models, such as aluminum or steel, can contribute to minimizing environmental impact. Additionally, responsible waste management practices during the production process are crucial. reputable manufacturers often prioritize sustainability and employ eco-friendly practices whenever possible.
In Conclusion
Rolling shutter forming machines play a vital role in shaping the landscape of security and convenience. From safeguarding businesses and homes to enhancing industrial operations and offering unique functional benefits, these remarkable machines offer a symphony of potential. As technology continues to evolve, we can expect even greater advancements in rolling shutter forming machines, leading to even more robust, versatile, and sustainable solutions for the future.