Introduction to Capping Roll Forming Machines
Capping roll forming machines play a crucial role in the production of metal capping plates used extensively across various industries. A capping roll forming machine is a type of roll former that produces metal cover plates or caps from coil stock of sheet metal.
The process involves passing sheet metal through a series of progressively arranged rollers that bend the sheet into the desired cap profile. As the sheet metal moves through the machine, it goes through a straightening process before being formed and cut to the required length. Modern capping roll forming machines are CNC-controlled for precision and efficiency.
Capping plates produced using these machines find wide application as aesthetic and protective covers and closures for exposed pipe ends, electrical apparatus housings, machinery guards, tanks, ducts, chassis openings, and several other uses where sturdy capping is required.
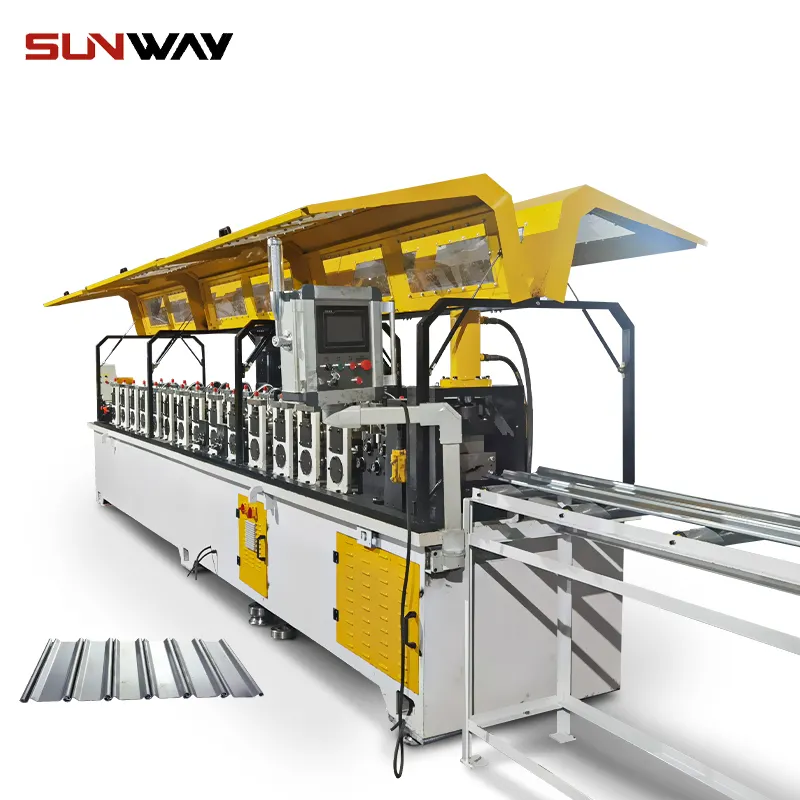
How Capping Roll Formers Work
A capping roll forming machine consists of three main sections – the decoiler or uncoiler, the forming section, and the cutoff press.
- The decoiler holds a coil of the sheet metal to be formed. It unrolls and feeds the coil into the forming section at a consistent speed and tension.
- In the forming section, the sheet passes through a series of rollers that bend it progressively into the desired cap profile. The rollers are positioned very precisely to guide the metal into shape gradually.
- The cutoff press cuts the continuously formed metal into pieces of the required length as per the application. It may use mechanical or hydraulic shearing.
Modern capping roll formers include servo motor-driven decoilers for precision feeding of the coil stock. The forming rolls and cutoff press are controlled via CNC which allows for quick roll set changes to form different profiles. These machines can be automated for inline finishing operations like hole punching.
Benefits of Capping Roll Forming Machines
Capping roll formers provide several benefits that make them ideal for high volume production of metal caps and closures:
- High Production Volumes – These machines operate at fast line speeds, allowing over 50 feet to 100 feet of cap profile to be produced per minute. This results in very high volumes ideal for mass production applications.
- Consistency – The CNC-controlled forming process ensures every cap is produced precisely to the programmed specifications without deviations.
- Lower Costs – Automated roll forming is a continuous process that is far more cost-effective compared to stamping or fabricating individual caps manually. Material waste is minimal.
- Flexibility – Quick roll changeovers allow producing various profiles on the same machine. Different metals, thickness, widths, and lengths can be run.
- Labor Savings – The automated forming process needs minimal supervision. No secondary bending or finishing operations are required.
- Compact Footprint – Capping roll formers have a relatively small footprint, reducing facility requirements.
Materials Used for Capping Plates
Capping roll forming allows processing of different metals into caps depending on the end-use requirements:
Mild Steel
Mild steel is the most common material for capping plates in industrial applications where high strength is not critical. It provides good formability and weldability at a low cost. Common mild steel grades used are:
- ASTM A1008 CS Type B
- ASTM A569
- ASTM A1011 SS Grade 36
Galvanized Steel
Galvanized steel has a zinc coating that provides excellent corrosion resistance and long service life when exposed to water or moisture. Typical grades include:
- ASTM A653
- ASTM A879 CS Types A and B
Aluminum
Aluminum is used where light weight and corrosion resistance are required. Alloy grades like 5052, 3003 are commonly roll formed into caps.
Stainless Steel
For applications needing very high strength and corrosion resistance, stainless steel grades like 304 and 316 are used. The choice depends on the exposure conditions.
Key Considerations for Capping Plate Design
Several factors have to be considered when designing metal caps to be produced by capping roll formers:
- Profile – The cap profile including dimensions like overall width, rib spacing/pattern, corner radii, etc. needs to be defined. profiles with tight radii may require special tooling.
- Material Thickness – Thicker metals may require more forming power. Thinner sheets are easier to form but compromise durability.
- Length – Longer caps may require support within the machine to prevent sagging.
- Holes – Any holes for fasteners need to be accounted for in the machine setup.
- Quantity – Estimated production volumes determine the line speed and automation level required.
- Coating – Any post-forming coating or finishing needs to be considered.
Proper design ensures efficient and problem-free production. Consulting the roll forming machine manufacturer is advisable.
Typical Uses of Capping Plates
Some common applications where capping roll formed plates provide durable and cost-effective solutions:
Pipe End Caps
Cylindrical or conical caps that cover open ended pipes for aesthetics and to prevent debris entry. Common for exposed drainage pipes.
Ducting Caps
Rectangular caps used to close the open ends of HVAC and other metal ductwork during installation.
Tank Covers
Round or rectangular cover plates that seal large openings on tanks and reservoirs. Provide access for inspection & cleaning.
Machinery Guards
Caps to cover exposed rotating shafts and mechanical parts on equipment for safety.
Electrical Enclosure Covers
Formed covers and access plates for junction boxes, electrical cabinets etc. Provide protection from outside elements.
Chassis Covers
Custom chassis caps for covering engine bays, wheel arches on vehicles and heavy equipment.
Automotive Applications of Capping Plates
Due to their sleek appearance and light weight, roll formed aluminum and steel caps are popular for automotive uses like:
- Chrome plated wheel covers
- Gas tank caps
- Gear shifter caps
- Steering column covers
- Hubcaps
- Engine bay covers
- Trunk lids
- Roof pillars
Custom car builders make extensive use of sectional cover plates that can be quickly bolted on to the vehicle frame. The capping provides a smooth exterior surface to make the modifications undetectable.
Performance cars use removable capping over wheel wells to hide inner modifications and allow quick access when required. These are secured with quick release fasteners.
Equipment Housings and Covers
Roll formed caps are ubiquitous for covering electrical and electronic equipment like motors, transformers, junction boxes, control panels, signal lights etc. Benefits include:
- Protection from dust, debris and splashing water
- Safer handling with rounded edges
- Noise reduction from covered fans and moving parts
- Improved aesthetics with no visible fasteners
- Vents for airflow where needed
- Allow quick interior access for maintenance
- Custom cutouts for protruding wires, conduits etc.
Small machine enclosures, guards around robotic arms, and covers over conveyors are other examples where metal caps enhance safety, appearance and performance.
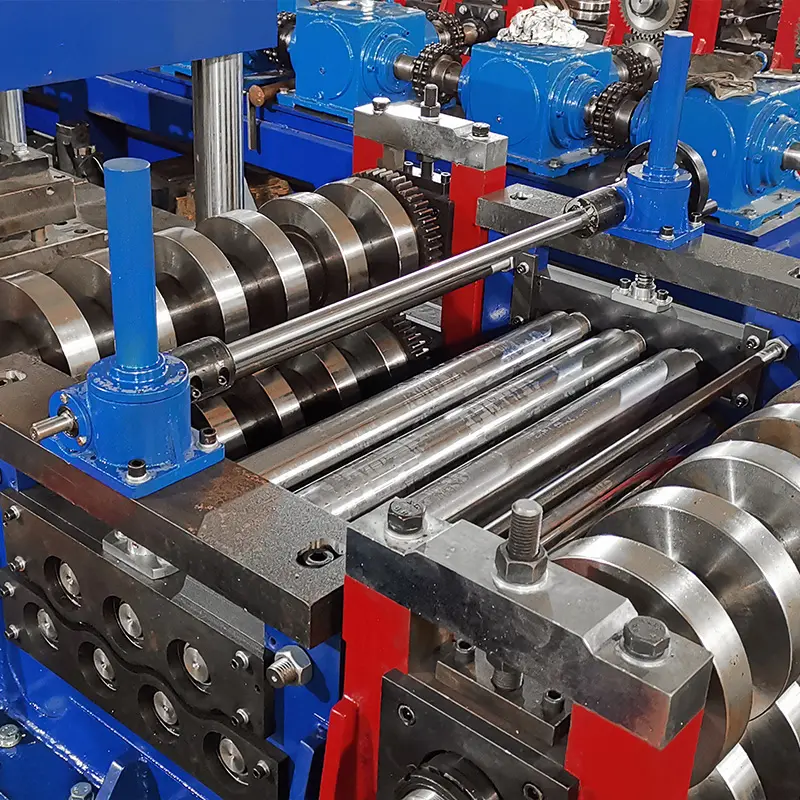
Architectural Uses of Capping Plates
In building construction and architectural applications, common uses of machine rolled capping plates include:
Wall and Ceiling Panels
- Decorative covers over junction boxes on walls
- Covers concealing structural elements like beams
- Accent wall panels
- Ceiling medallions
Exterior Facade
- Window sills
- Covering over wall seams
- Parapet covers
- Column wraps
- Corner trim
- Coping for walls & planters
Roofing
- Ridge caps
- Gravel stops
- Covering fascia boards
- Gutters
- Downspout boxes
- Cupolas
- Rooftop screening and louvers
Interiors
- Wainscoting
- Ceiling domes
- Column cladding
- Display cases
- Signage backing
Architects find metal caps ideal for both form and function. The crisp profiles and easy installation helps them achieve the desired aesthetic vision.
Comparison to Other Manufacturing Processes
Roll forming offers some clear advantages over other methods for producing metal caps and covers:
Vs. Metal Stamping: No tooling changes needed for different profiles. Lower initial capital investment.
Vs. CNC Fabrication: Much faster production with continuous forming. No programming needed.
Vs. Machining: No material waste. Higher consistency part-to-part.
Vs. Laser or Waterjet Cutting: Limitations on material thickness. Secondary bending required.
Vs. Metal Spinning: Size limitations based on spinning capacity. Slower process.
Vs. Casting: Longer tooling lead time. Secondary machining often needed.
For production volumes above 5000 pieces, roll forming is usually the optimal manufacturing process for metal caps and plates.
Latest Technological Advancements
Capping roll forming machines have undergone considerable modernization in recent years with the adoption of technologies like:
- Servo-motor driven decoilers – For precise coil feeding
- CNC controls – For quick profile changes and precision
- Automatic lubrication – Reduces maintenance needs
- Inline punching – Allows holes & cutouts during forming
- Quick change tooling – Reduces downtime for roll changeovers
- CAD programming – Creates optimal roll layouts
- Servo-electric and hydraulic cutoffs – Clean and rapid severing
- Automatic stackers – Hands-free operation
These improvements have enhanced the capacity, flexibility, and ease-of-use of modern capping roll formers.
Innovative Product Applications
Beyond conventional uses, imaginative manufacturers are using capping roll formed parts in innovative ways like:
- Decorative wall art made from formed metal sheets
- Custom furnishing like cafeteria trays and luggage carts
- Formed aluminum panels for building exteriors
- Lighting fixtures crafted from formed metal plates
- Automotive add-ons like running boards and side steps
- Protective cases for electronic gadgets and appliances
- Solar cell coverings that allow light to pass through
- Heat sinks for electronic devices
- Custom enclosures for digital signage and displays
Product designers now recognize metal caps produced on roll formers as an affordable medium for bringing creative ideas to life.
Choosing the Right Capping Roll Forming Machine
Here are key considerations when selecting a capping roll former:
- Production Volume – Optimal speed and automation levels
- Material Type and Thickness – Effects forming power needed
- Part Dimensions – Width capacity and cutoff length ability
- Profile Complexity – Number of forming heads and passes
- Tooling Requirements – Quick change preferred for flexibility
- Secondary Operations – Punching, counting, stacking etc.
- नियंत्रण प्रणाली – Ease of operation and roll changeover
- Space Constraints – Machine footprint dimensions
- Budget – Pricing and total cost of ownership
- Service Support – Installation, maintenance and training
The ideal roll former maximizes output while minimizing both operator work and production costs.
Leading Capping Roll Forming Machine Manufacturers
Some of the prominent global companies producing state-of-the-art capping roll forming machines include:
Metform International
Headquartered in New Zealand, Metform produces a wide range of world-class roll forming machines including the Evolution Capping Series with max line speed of 130 feet/min.
Formtek
Based in the USA, Formtek specializes in roll forming technology. Their product range includes the Smart Capping Roll Former for caps up to 20″ wide.
Furick International
Furick from Taiwan provides technologically advanced roll formers like the SA Series Servo Automatic Capping Roll Former.
FormProcess Engineering
India based FormProcess offers the fully automated PRF-Capping Roll Former for high speed production.
Samcoon
Korea’s Samcoon has over 50 years of roll forming expertise. They offer optimized solutions like the High Speed Capping Roll Former.
When selecting a machine, factors like production scalability, ease of operation, and service support need consideration along with technology specifications.
Future Outlook for Roll Formed Caps
With exponential growth forecasted in end-user industries, the demand for roll formed capping plates and covers will continue rising globally.
Construction, infrastructure, automotive, HVAC, and electrical industries are expected to drive volume demand. Emerging economies with rapid urbanization will also bolster consumption of machine rolled caps.
Product designers are leveraging new materials like aluminum and advanced coatings to expand applications of roll formed caps and covers.
Manufacturers will continue incorporating Industry 4.0 technologies like IoT monitoring, predictive maintenance, and big data analytics to further optimize their roll forming operations.
Overall, the future looks bright for capping roll forming with innovations on both the production and product fronts.
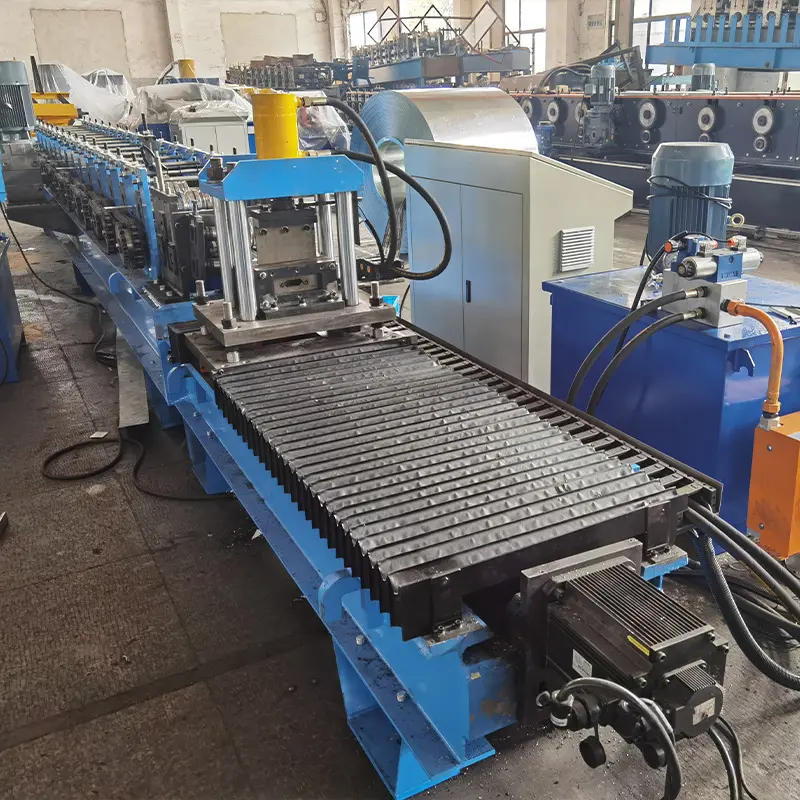
निष्कर्ष
Capping roll forming machines enable fast, and economical production of metal caps in a broad range of profiles, materials, and sizes. The automated forming process allows mass output with great precision and minimal waste.
Machine rolled caps provide durable and aesthetic closure solutions across industrial, architectural, automotive and specialty applications. With recent technological enhancements, capping roll formers now offer greater efficiency, flexibility, and ease-of-use.
Continued innovations in roll forming equipment combined with creative product designs will expand the possibilities for machine rolled caps and covers. As demand grows globally, capping roll formers will remain indispensable for high quality and cost-effective metal cap production.
सामान्य प्रश्न
Q: What are the key benefits of using capping roll forming machines?
A: The main benefits are:
- High production volumes and speed
- Consistency and precision in every piece
- Cost savings compared to other methods
- Flexibility to produce different profiles
- Minimal material waste
- Automated process needs less labor
- Smaller footprint than other equipment
Q: What types of metals can be roll formed into caps?
A: Common metals include:
- Mild steel
- Galvanized steel
- Aluminum
- Stainless steel
- Copper
- Brass
The choice depends on strength, weight, corrosion resistance, and cost considerations.
Q: What are some key design factors for roll formed caps?
A: Important design factors are:
- Profile shape and dimensions
- Metal thickness and grade
- Overall length of the cap
- Any holes or cutouts required
- Quantity to be produced
- Any post-forming finishes or coatings
Q: What are some innovative applications for roll formed caps?
A: Innovative applications include:
- Metal wall art and decor
- Furniture and luggage carts
- Architectural wall and roofing panels
- Custom automotive add-ons
- Protective cases for electronics
- Heatsinks for devices
- Solar cell covers
- Unique lighting fixtures
Q: How do you choose the right capping roll forming machine?
A: Considerations for selecting the machine are:
- Required production volumes
- Material type and thickness
- Part sizes to be produced
- Profile complexity
- Tooling flexibility needed
- Secondary operations
- Control system sophistication
- Available space
- Budget constraints
- Service and support capability
Q: What are the latest technological improvements in capping roll formers?
A: Recent advancements include:
- Servo-motor driven decoilers
- CNC forming controls
- Automatic lubrication systems
- Inline punching abilities
- Quick change tooling
- CAD-based programming
- Servo-electric and hydraulic cutoffs
- Automatic stacking systems
These improve speed, precision, flexibility, and ease-of-use.