ए cable ladder roll forming machine is equipment used to produce cable ladders through roll forming technology. Cable ladders provide support and protection for electrical cables and wires in various industrial, commercial and infrastructure applications. This article provides a comprehensive guide on cable ladder roll forming machines.
Overview of Cable Ladder Roll Forming Machine
- Roll forming technology forms metal coils into customized cable ladder profiles through consecutive bending and shaping using roller dies
- Highly efficient, automated production of cable ladders in long lengths as per client specifications
- Capable of handling multiple materials like Mild Steel, Stainless Steel, Aluminum
- Forming speed up to 10 m/min depending on thickness and material
- Support ladder widths from 100 to 1000 mm
- Superior finish and dimensional accuracy of finished ladders
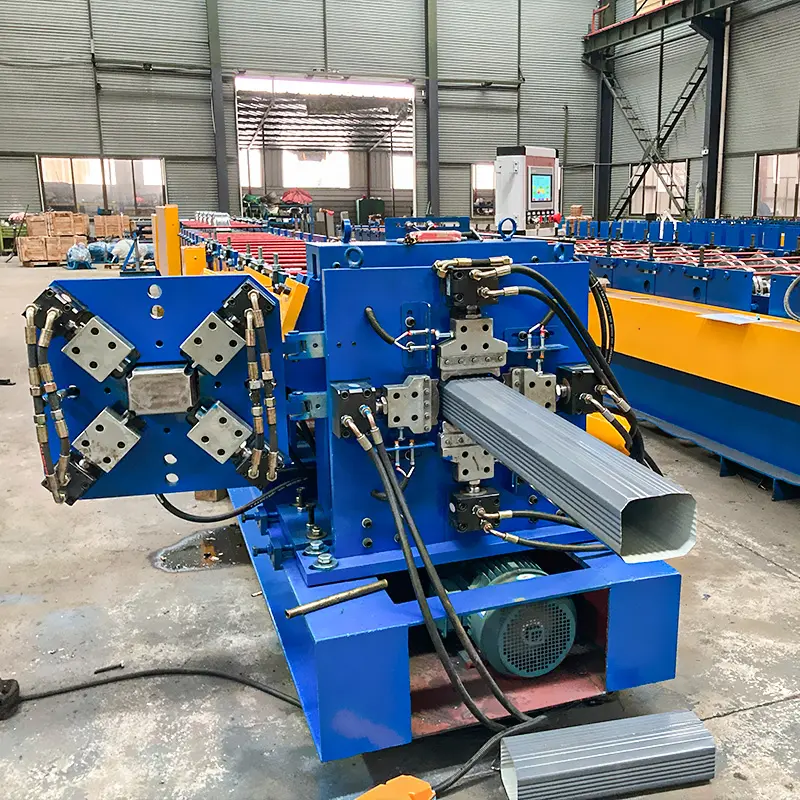
Components of केबल सीढ़ी रोल बनाने की मशीन
Component | Function |
---|---|
Uncoiler | Feeds metal coil strip into line |
Feeder rack | Guides strip through machine |
Punching Unit | Punches holes for cable ties & other fixtures |
Forming stations | Progressively forms strip into ladder profile |
Hydraulic system | Applies pressure to roller dies for forming |
Control panel | Houses PLC system to automate production |
Cutting device | Cuts ladders to desired length |
Stacker | Stacks finished cable ladders |
The key components of a cable ladder roll forming machine work in tandem to transform raw metal coils into finished cable ladder products. The forming stations apply high pressure using hydraulically controlled roller dies to gradually shape the strip into ladder side rails and rungs. Automated controls precisely regulate the feeding, punching, forming and cutting processes resulting in high dimensional accuracy and superior quality finished ladders.
Working Process
The working process of a cable ladder roll forming machine consists of:
- Material Feeding – The strip coil is loaded onto an uncoiler which smoothy feeds the strip into the machine through an initial feeder rack. Guiding devices align the strip centrally as it enters the production line.
- Punching – A computerized punching unit with programmable punches then creates holes in the strip for inserting cable ties/fasteners to the finished ladders later on.
- Pre-forming – Initial roller dies lightly pre-bend the strip to prepare it for the forming stations. Pre-forming reduces stress on the metal during shaping.
- Forming – The strip enters a series of progressive roller die forming stations – each station further bending and shaping the strip incrementally to gradually form the final cable ladder profile. Side rails and rungs are formed through careful caliberation of different steel thickness zones across the strip.
- Hydraulic Pressure – Hydraulically activated cylinders provide pressure against the roller dies required for the forming and calibration. The pressure intensifies through each station ranging from 7 tons to 25 tons.
- Cutting – Based on the input ladder length, a computerized cutting device accurately cuts each piece. Pneumatic or hydraulic shear machines are typically integrated for this purpose.
- Stacking – The finished cable ladders are stacked systematically by an exit conveyor or stacker for easy loading and transport. Each ladder can range from 3 meters to 15 meters long.
Automated programmable controls coordinate the above processes in a seamless synchronized production sequence. Modern machines also include safety measures like strip break detectors, emergency stop buttons, sensor-monitored access doors and other features. The end result is mass production of cable ladders in the exact customized specifications provided by clients.
Material, Feeding, Forming and Slicing
Parameter | विवरण |
---|---|
Materials | Mild Steel, Stainless Steel, Aluminum, Galvanized Steel |
मोटाई | 1.2 – 3 mm |
Width | 100 – 1000 mm |
Feeding | Motorized uncoiler, roller feeder rack |
Pre-forming | Initial roller dies for guiding strip |
Main Forming | 6-8 progressively calibrated stations |
Hydraulic Pressure | 7 Tons to 25 Tons across stations |
Dimensional Accuracy | ± 1 mm |
Punching | Programmable hole punching unit |
Cutting | Hydraulic shear / Pneumatic shear |
Slicing | Length from 3 meters to 15 meters |
A range of materials with thickness up to 3 mm can be formed into cable ladders of widths between 100 mm to 1000 mm by appropriately configuring the roll forming line. Smooth feeding, precise punching and cutting, and intensive hydraulic pressure applied through automated roller die forming enables production of superior quality ladders in high volumes.
-
वाइनयार्ड पोस्ट रोल बनाने की मशीन
-
ऑटो आकार बदलने योग्य सिग्मा शहतीर रोल बनाने की मशीन
-
विद्युत कैबिनेट फ्रेम रोल बनाने की मशीन
-
दीन रेल रोल बनाने की मशीन
-
केबल सीढ़ी रोल बनाने की मशीन
-
पीवी माउंटिंग ब्रैकेट सी शेप प्रोफाइल रोल बनाने की मशीन
-
केबल ट्रे रोल बनाने की मशीन
-
सीजेड शहतीर चैनल कोल्ड रोल बनाने की मशीन पूर्ण ऑटो जस्ती स्टील प्रोफाइल
-
पीवी माउंटिंग ब्रैकेट रोल बनाने की मशीन (एचएटी / ओमेगा प्रोफाइल)
Design and Customization
- Completely customized design – client provides ladder specifications
- CAD software generates roller die design to match ladder profile
- Forming stations caliberate roller dies to shape side rails and rungs
- Ladder height, width, rung spacing/size customized
- Hole punch patterns personalized for each client
- Bends, embossing, brackets optionally incorporated
- Support longitudinal and traverse cable rung direction
- Standard and heavy-duty cable ladder designs
Clients have complete flexibility in design of the cable ladder end product. They can provide custom specifications like height, width, rung spacing, hole punch patterns etc. as per their desired cable routing requirements. Advanced CAD software translates the ladder design into specialized roller dies for each forming calibration station. This facilitates mass production of fully personalized and functional cable ladders catered exactly as per the client’s needs.
Suppliers and Price Range
Manufacturer | Location | Price Range |
---|---|---|
Furukawa Rock Drill | Japan | $$ |
रोल बनाने की मशीन | China | $ |
Gasparini SpA | इटली | $$$ |
Metform | Turkey | $$ |
EWMenn | Germany | $$$ |
Automecc | भारत | $$ |
Anhui Yuanlong | China | $ |
There are a number of global manufacturing companies supplying cable ladder roll forming equipment. China provides cost effective machines starting under $50,000. European companies like Gasparini and EWMenn offer technologically advanced reliable solutions between $100,000 to $200,000. Metform, Automecc provide good mid-range options. Evaluation criteria for choosing supplier detailed in next section.
Choosing Roll Forming Machine Supplier
Parameter | विवरण |
---|---|
Industry experience | Prefer 10+ years sector experience |
Production scale | Assess factories & past equipment supplied |
Design expertise | Evaluate R&D dept. & customization skills |
Component quality | European hydraulic units recommended |
Testing process | Review machine acceptance protocols |
Commissioning support | Check installation & post-sales service process |
Certifications | ISO, CE marked electrical components |
Pricing | Compare to industry benchmarks |
Warranties | 1 year minimum comprehensive warranty |
Selecting the ideal cable ladder roll forming machine supplier requires assessing manufacturers across the above technology, quality and service parameters vital for such capital equipment. Strike a balance between price and long term production quality & performance. Be wary of lowest cost options as machine structure and components may be substandard.
Installation Requirements
- Level concrete or metal foundation
- 3-phase electrical connections
- Compressed air line setup
- Cooling water supply (for cutter)
- Exhaust fans & ducting
- Safety partitions & guarding
- Cable tray routes to control panel
The supplier will provide complete guidelines for preparing the facility prior to machine installation. This includes foundation specifications, power requirements, compressed air and water supply details, safety considerations and approval drawings. Many components like the cutters and hydraulic power packs require proper amenities to deliver rated performance – verify these are met before delivery.
Operation and Control
- Fully automatic PLC with HMI touchscreen
- Input material, size and punch pattern
- Automated forming, slicing, stacking
- Servo motor feeder with speed control
- Monitoring & feedback of all zone pressures
- Emergency stop sensors on doors
- Mode selection for jog, single or auto cycle
- Detailed alarm diagnostics & safety log
- Remote connectivity options
Modern cable ladder roll forming machines offer extensive automation and controls for simplified, safe operation. The industrial touchscreen allows intuitive inputs for material grade, ladder dimensions and production volume. Equipment safety is monitored through sensors on access doors and emergency stop circuits. Remote connectivity even facilitates diagnosing faults with the supplier’s technicians without requiring engineer visit. Such smart features minimize downtime while enabling 24×7 unmanned production.
Maintenance
Activity | Frequency |
---|---|
Inspect & tighten guard bolts | Monthly |
Lubricate bearing housings | 500 operation hours |
Monitor belt tension/wear | Weekly |
Inspect electrical wiring | 6 months |
Change hydraulic oil | Yearly |
Inspect Roller dies | 3 months |
Touch up paint | Yearly |
Pros and Cons
Pros | Cons |
---|---|
Automated mass production | High initial capital cost |
Superior finish & strength | Complex design customization |
Dimensional accuracy | Specialized maintenance requirement |
Material thickness flexibility | Occupies large facility space |
Custom hole punch patterns | Limited height adjustment |
Lightweight formed construction | Thicker coils more difficult to process |
While cable ladder roll forming machines require significant initial investment and maintenance efforts, they enable efficient large scale manufacturing of lightweight, high strength products customized to client cable support requirements. The automated production ensures consistency in dimensional and structural quality.
Limitations
- Maximum 3 mm thickness coils
- Maximum 1 meter strip width capacity
- Maximum cable ladder heights up to 600 mm
- Restricted forming capability for extreme bends
- Rungs prone to damage if very thin
- Short step obstructions difficult to incorporate
The prime limitations of cable ladder roll forming pertain to restrictions in material thickness and product dimensions they can effectively shape. While offering extensive customization, abrupt contours and thin sections prone to breaking during forming remain key challenges. Robust ladder designs adequately overcoming such limitations yield the best production results.
Benefits
- Highly efficient continuous production
- Consistent quality end products
- Completely customized design profiles
- Superior finish and dimensional accuracy
- Cost effective versus manual fabrication
- Lightweight and high load capacity
- Easy installation and maintenance
Automating the ladder manufacturing process through roll forming technology provides tangible improvements in production rates, costs, quality and customization ability over manual methods – translating into multiple benefits for clients. The light yet strong finished ladders simplify installation while meeting unique cable routing requirements.
Applications of Cable Ladders
Industry | Application Scenarios |
---|---|
Building & Construction | Electrical rooms, building infrastructure, ceilings, mechanical rooms |
Energy Infrastructure | Power plants, renewable energy farms, substations |
IT Infrastructure | Data centers, network rooms, server racks |
Industrial | Production facilities, factories, warehouses |
Commercial | Malls, airports, sports arenas |
Transportation | Shipping ports, railway infrastructure |
Utilities | Water treatment, sewage plants, gas networks |
Defense Equipment | Naval ships, armored vehicles |
Structured cable containment systems in industries transporting power or signals gain tremendous functional and safety benefits from custom designed cable ladders rather than exposed cabling. Roll formed aluminum or stainless steel ladders resist corrosion and protect critical network wiring. Ladder height and rung spacing vary greatly matching client requirements. All equipment from a remotely located wind turbine station to the racks in hyperscale cloud data center apply purpose-built cable ladders for organizing cable infrastructure.
Cost Analysis
Investment | Cost (USD) |
---|---|
रोल बनाने की मशीन | $100,000 to $250,000 |
Labor | 2 operators per shift |
Facility | 2000 sq. ft. |
शक्ति | 20 kW peak consumption |
Dies | $2000 per design |
Raw Materials | Mild Steel Coil : $0.5/kg |
Production Cost | $2 – $5 per meter |
Selling Price | $8 – $12 per meter |
Raw material makes up around 60% of the operating cost for making cable ladders through roll forming. The automated lines enable extreme cost benefits and flexibility versus manual methods. Low equipment amortization and labor overheads coupled with high production rates of over 1000 meters per shift result in very economical finished products. Ladder fabrication shops enjoy healthy profit margins given that market rates for cable ladder supply alone range between $8 to $12 per meter depending on dimensions.
Market Outlook
Global demand for structured cable support equipment will continue growing at over 6% CAGR driven by rising commercial building infrastructure and energy projects. Construction, IT infrastructure and industrial sectors in developing regions offer lucrative opportunities supported by government electrification and modernization initiatives. Leading analysts predict the cable management accessories market sustaining mid to high single digit growth over the next 5 years – synonymous trends foreseeable in subsets like custom cable ladder demand. Roll formed variants outpacing traditional welded or bracket-assembled products considering automation advantages lowering market prices. As data consumption and cloud infrastructure booms in coming times, cable ladder volumes anticipate even higher growth rates.
Latest Innovations
- Roller dies to form complex bend cable ladders
- Multi-rail and channel housing ladder designs
- Curved and height varying ladders
- Cable tray – ladder hybrid solutions
- Side rail incorporated quick fastening clamps
- Laser cutting replacing shear method
- Robotic automated bundling & palletizing
- IoT enabled production monitoring
- Vision systems for surface defect detection
- Powder coating & galvanizing integration
While fundamental roll forming process for cable ladders remains consistent for decades now, upgrading auxiliary technologies enrich product variation and quality. Patented die tooling now facilitates curved profiles, multi-rail housings and variable height along the ladder length fulfilling evolving aesthetic and structural needs. Secondary enhancements also continue through automated laser trimming, robotic bundling, shiftless powder coating, IoT-enabled analytics and computer vision capabilities taking quality and efficiency to the next level.
Future Prospects
Upcoming machine upgrades for faster and thicker material forming abilities will expand application scenarios. Expect heavier duty stainless steel cable ladders penetrating corrosive chemical and marine sectors. Similarly lighter and narrower ladders using aluminum suit 5G antenna farms. Vision-based AI promises adaptive production changes responding to defects in real-time. Growing adoption of carbon steel, titanium or composite materials foreseeable with custom roll forming techniques maturing. Key prospects summarize as:
- Wider and thicker forming capacities
- Advanced vision system integration
- High-strength exotic material ladders
- Multi-axis & curved profile designs
- Laser cutting, drilling & marking additions
- Integrated surface treatment
- Smart predictive maintenance apps
- AR assisted remote machine troubleshooting
- Eco-friendly powder coatings & galvanizing
With exponential growth in industrial Ethernet and cloud infrastructure, cable ladder innovation will continue matching application demands. Leveraging IIoT, AI/ML and material science the next generation of roll forming promises great sustainability and customization advances. Carbon-negative production, fully autonomous asset management and agile design tooling characterize the cable ladder equipment roadmap this decade.

सामान्य प्रश्न
Q: What is the fastest cable ladder production rate possible?
A: Using 3 mm thick stainless steel coils, ladder widths around 600 mm and an 8 station roll former – production rates up to 10 meters per minute are achievable.
Q: Can holes be punched anywhere along the ladder profile?
A: Yes, state of the art programmable punching units allow designing fully customized hole patterns matching client cable fastening needs.
Q: What accessories are available for cable ladders?
A: Commonly used accessories include side rails, couplers, reducers, elbows, tees, covers, dropouts, grommets, support brackets and fixation hardware.
Q: Can normal cold rolled steel be used instead of hot rolled coils?
A: We recommended low carbon hot rolled steel for optimum combination of formability and load capacity. Annealed cold rolled requires higher tonnage.
Q: What minimum order quantity is acceptable for custom cable ladders?
A: Given the design and production setup costs, minimum order volumes around 500 meters make most economic sense for buyers.
Q: What testing certification is provided with cable ladders?
A: Routine test reports include dimensional accuracy charts, structural load testing, coating thickness measurement and packaging quality audits.
Q: Can plastic cable ladders be produced using roll forming technique?
A: Plastic variants like HDPE cable ladders are typically made through extrusion process instead owing to material properties.
Q: Are cable ladder roll forming machines user friendly?
A: The automated lines just require simple initial inputs through industrial touchscreen. Quick troubleshooting also enabled through IoT-based remote connectivity.