परिचय
In the world of metal profile production, efficiency and precision play a critical role in meeting the demands of various industries. Among the many methods used, roll forming has emerged as a prominent and cost-effective technique. This article dives into the fascinating world of C section roll forming machines, exploring their functionality, advantages, applications, and future prospects.
What is a C Section Roll Forming Machine?
A C section roll forming machine is a specialized piece of equipment used in the roll forming process to produce C-shaped metal profiles. These profiles, also known as C channels, offer excellent strength-to-weight ratio and are widely used in various construction, manufacturing, and industrial applications.
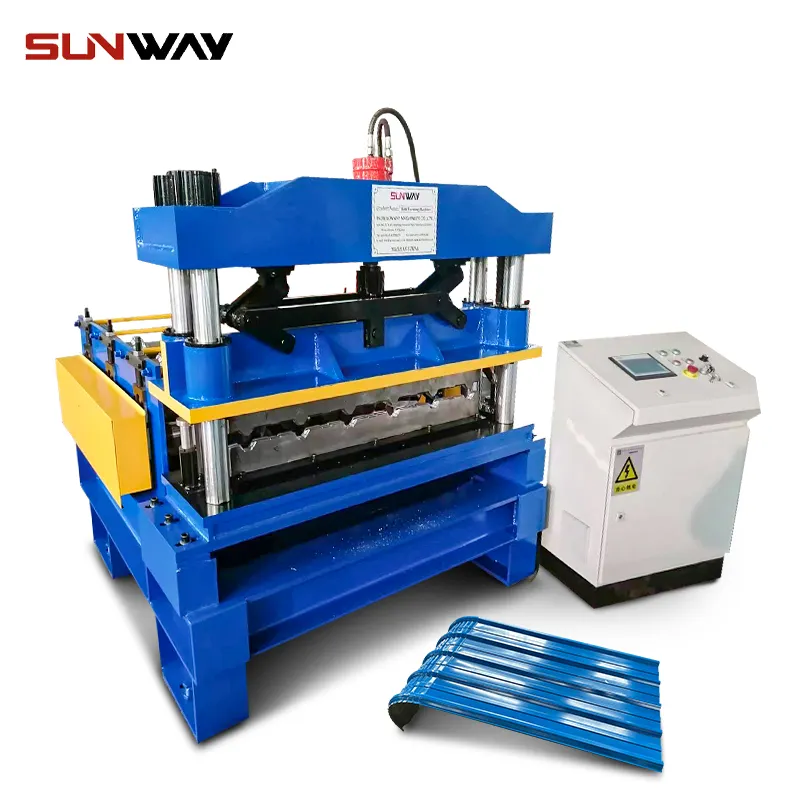
How Does a C Section Roll Forming Machine Work?
The roll forming process involves feeding a strip of metal through successive pairs of rollers, each contributing to shaping the final profile. A C section roll forming machine uses a series of precisely designed rollers to gradually transform the flat metal strip into the desired C-shaped cross-section.
Advantages of Using a C Section Roll Forming Machine
Cost-Effective Production
C section roll forming machines enable continuous and high-speed production, resulting in reduced labor costs and material wastage compared to other metal forming methods.
High Precision and Consistency
The use of rollers ensures uniform shaping, dimensional accuracy, and consistent quality throughout the production process.
Versatility in Profile Shapes
Modern C section roll forming machines can produce various sizes and shapes, making them adaptable to a wide range of applications.
Time and Labor Efficiency
Automated operation and efficient production reduce turnaround time and enhance overall productivity.
Types of C Section Roll Forming Machines
C section roll forming machines come in several configurations to meet specific production requirements:
Single C Section Roll Forming Machine
A single-station machine produces a specific C section profile with a fixed set of rollers.
Double C Section Roll Forming Machine
This type of machine can produce two different C section profiles without manual adjustments, improving production flexibility.
Multi-Station C Section Roll Forming Machine
With multiple stations, this machine can create complex profiles in a single pass, streamlining the production process.
Customizable C Section Roll Forming Machine
Some machines allow for easy roller adjustments, enabling quick changes between various C section profiles as needed.
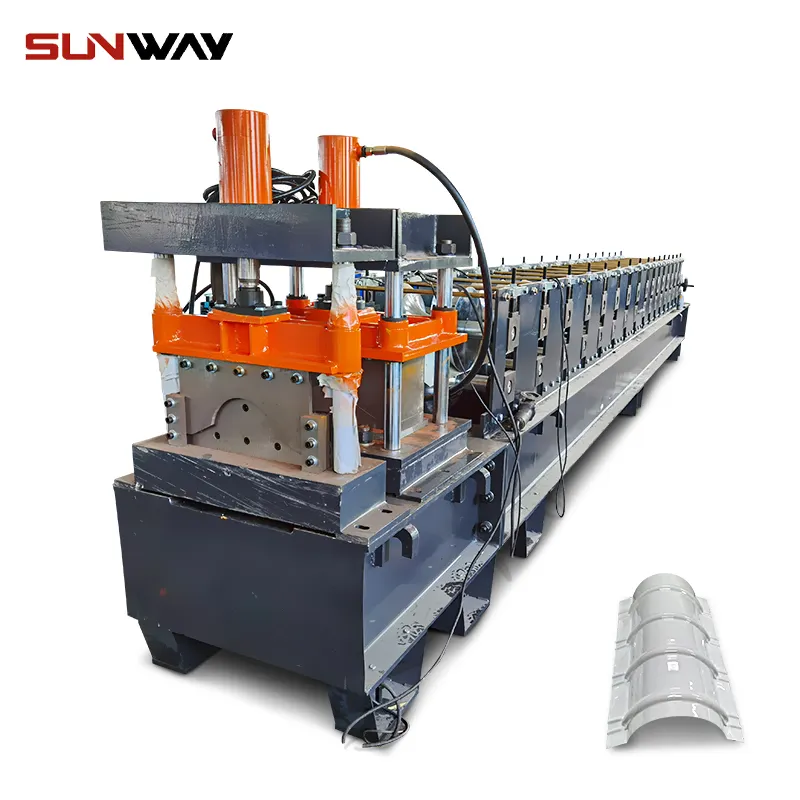
Components of a C Section Roll Forming Machine
A typical C section roll forming machine consists of several essential components:
Uncoiler
The uncoiler holds the metal coil and feeds the strip into the roll forming machine.
Roll Forming Station
This is where the magic happens. The roll forming station houses the series of rollers responsible for shaping the metal strip into a C section profile.
कटिंग सिस्टम
After roll forming, a cutting system precisely trims the profile to the desired length.
Control Panel
The control panel enables operators to set parameters, monitor the process, and make adjustments as needed.
Stacker
The stacker collects the finished profiles, making handling and packaging easier.
Factors to Consider When Choosing a C Section Roll Forming Machine
Several crucial factors influence the selection of the right C section roll forming machine for specific applications:
Production Speed
The desired production rate must align with the machine’s capabilities to meet demand efficiently.
Material Thickness and Width
Different machines accommodate varying metal strip dimensions, affecting the range of profiles that can be produced.
Profile Complexity and Customization
Consider the degree of complexity and customization required for the intended applications.
Automation and Integration Options
Automation features and integration with other systems can streamline production and improve overall efficiency.
Manufacturer Reputation and Support
Choosing a reputable manufacturer ensures a reliable and well-supported machine with quality components and service.
Maintenance and Care of a C Section Roll Forming Machine
Regular maintenance and proper care are essential to keep a C section roll forming machine in optimal condition and ensure consistent performance. Here are some crucial aspects of maintenance:
Regular Inspections and Cleaning
Periodically inspect the machine for any signs of wear, damage, or misalignment. Clean the rollers, cutting system, and other components to prevent debris buildup that could affect the quality of the profiles.
Lubrication
Proper lubrication of moving parts is vital to reduce friction and extend the lifespan of the machine. Follow the manufacturer’s guidelines for lubrication frequency and use appropriate lubricants.
Blade and Roller Replacement
Worn-out blades and rollers can negatively impact the profile’s quality and consistency. Replace them as needed to maintain precision and performance.
Electrical System Maintenance
Ensure the electrical system is well-maintained and free from any issues. Check for loose connections, damaged wires, and other electrical components regularly.
Safety Measures
Safety should be a top priority in operating a C section roll forming machine. Train operators on safety protocols, and ensure they adhere to them diligently. Implement regular safety checks and maintenance procedures to prevent accidents.
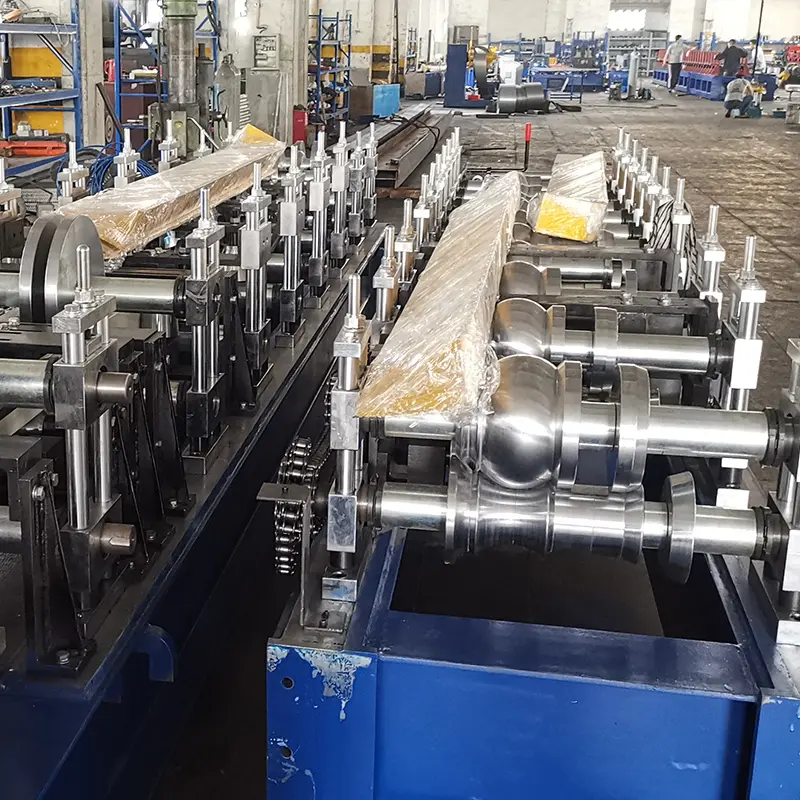
Common Quality Issues and Troubleshooting
Even with proper maintenance, issues may arise during production. Here are some common quality issues and possible troubleshooting steps:
Uneven Profile
Uneven shaping can occur due to misaligned rollers or improper material feeding. Check and adjust the roller alignment and ensure consistent material feeding.
Material Deformation or Wrinkling
Deformation or wrinkling of the metal strip may happen due to excessive forming pressure or improper tension. Adjust the forming pressure and ensure proper tension control.
Inconsistent Dimensions
If the dimensions of the profiles are not consistent, it may indicate an issue with the cutting system or roller calibration. Inspect and calibrate the cutting system and rollers as needed.
Excessive Noise or Vibrations
Unusual noise or vibrations during operation can signal misalignment or worn-out components. Conduct a thorough inspection, identify the source, and address it promptly.
Material Wastage
Minimize material wastage by optimizing the roll forming process, ensuring precise measurements, and making necessary adjustments to reduce scrap.
Safety Precautions While Operating a C Section Roll Forming Machine
Safety is paramount when working with any machinery, including C section roll forming machines. Here are some essential safety precautions:
Training and Certification
Operators should receive proper training on operating the machine safely. Certify them once they demonstrate a thorough understanding of safety procedures.
Proper Use of Personal Protective Equipment (PPE)
Operators must wear appropriate PPE, such as safety glasses, gloves, and ear protection, to protect themselves from potential hazards.
Emergency Stop Procedures
Ensure that all operators know how to activate the emergency stop feature to halt the machine immediately in case of an emergency.
Safe Material Handling
Follow safe material handling practices to prevent injuries while loading and unloading metal coils.
Machine Isolation and Lockout-Tagout (LOTO) Procedures
Before performing maintenance or repairs, isolate the machine from power sources and follow LOTO procedures to prevent accidental startup.
Applications of C Section Roll Forming Machines
C section roll forming machines have diverse applications across various industries:
Construction Industry
C sections find extensive use in constructing metal buildings, roof structures, and framing systems due to their strength and versatility.
Automotive Sector
In the automotive industry, C section profiles are utilized in vehicle frames, chassis components, and structural reinforcements.
Furniture Manufacturing
C section profiles are incorporated into furniture designs for added strength and support.
Renewable Energy Sector
The solar panel and wind turbine industries employ C section profiles for their structural frameworks.
General Metal Fabrication
C section profiles serve a wide range of general metal fabrication purposes, including shelving, racking, and enclosures.
Future Trends and Innovations in C Section Roll Forming
As technology advances, C section roll forming machines are likely to undergo exciting developments:
Advanced Material Compatibility
Machines will be capable of handling a broader range of materials, including advanced alloys and composites.
Integration of Robotics and AI
Automation through robotics and AI will enhance production efficiency and reduce human intervention.
Energy Efficiency Improvements
Future machines will focus on optimizing energy consumption for sustainable production.
Enhanced Customization Capabilities
Advancements will enable quicker and easier adjustments for producing highly customized profiles.
Industry 4.0 Integration
Smart manufacturing practices will connect C section roll forming machines to digital networks, enabling data-driven decision-making and real-time monitoring.
Environmental Impact of C Section Roll Forming
As the world embraces sustainability, the environmental impact of roll forming becomes more crucial:
Material Waste Reduction
Efforts will be made to minimize material waste during production, leading to cost savings and reduced environmental footprint.
Energy Consumption
Manufacturers will focus on energy-efficient machine designs to reduce electricity consumption.
Recycling and Sustainability Initiatives
Recycling initiatives will ensure that end-of-life C section profiles are responsibly handled and repurposed.
Life Cycle Analysis
A comprehensive life cycle analysis will help manufacturers identify areas of improvement and implement sustainable practices.
Environmental Certifications
Machines meeting stringent environmental standards will receive certifications, providing assurance to environmentally conscious customers.
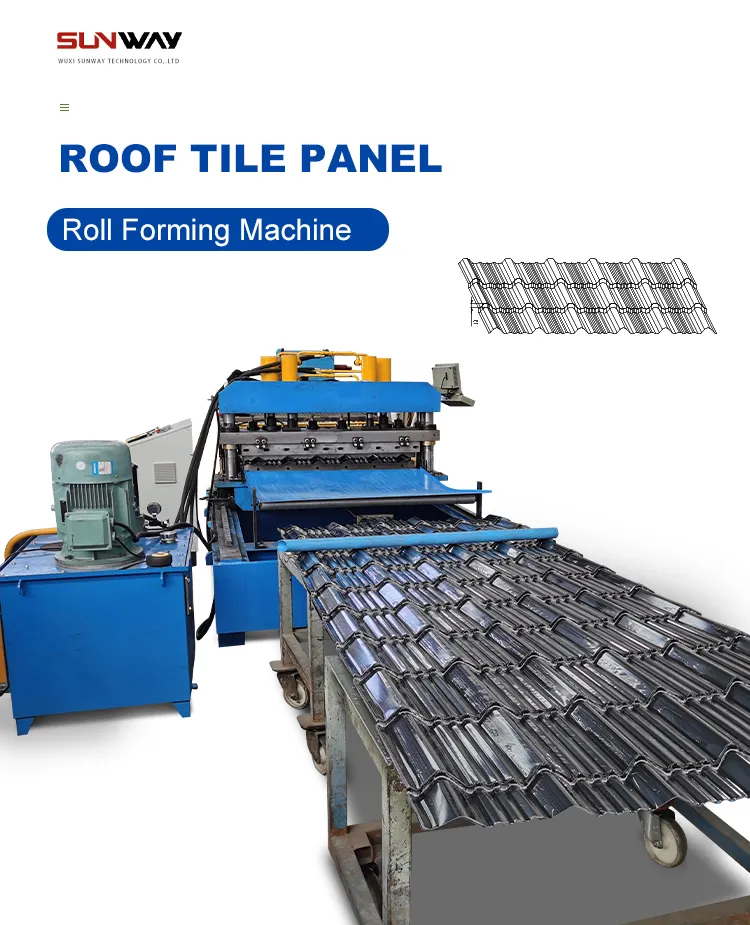
निष्कर्ष
C section roll forming machines have revolutionized metal profile production with their efficiency, precision, and versatility. As various industries continue to grow, the demand for customized and high-quality profiles will increase, driving further innovations in the roll forming technology. By embracing safety, maintenance, and sustainable practices, manufacturers can ensure the long-term success and positive environmental impact of C section roll forming machines.
FAQs
1. What is the typical production speed of a C section roll forming machine? C section roll forming machines can achieve production speeds ranging from 10 to 120 meters per minute, depending on the machine’s design and capabilities.
2. Can C section roll forming machines produce profiles with complex shapes? Yes, modern C section roll forming machines are capable of producing profiles with various shapes and complexities, thanks to advanced roller design and adjustable settings.
3. Are C section profiles stronger than traditional solid beams? Yes, C section profiles offer comparable strength with lower weight, making them a preferred choice in many structural applications.
4. What is the expected lifespan of a C section roll forming machine? With proper maintenance and care, a C section roll forming machine can last for decades, providing a high return on investment.
5. Can a single machine produce different C section profiles? Yes, some C section roll forming machines are designed to be easily adjustable, allowing operators to produce different profiles with minimal downtime.