Overview of Box Profile Sheets
Box profile sheets are an increasingly popular choice in the construction and industrial sector due to their strength, durability, and versatility. These metal sheets, often made from materials like galvanized steel, aluminum, or zinc-aluminum alloy, provide a strong and aesthetically pleasing roofing and cladding solution. But why choose box profile sheets over other roofing materials? The answer lies in their unique profile design that offers excellent water drainage, higher load resistance, and reduced noise during rain, making them ideal for a variety of climates and structures.
Box profile sheets come in a range of thicknesses, coatings, and designs, ensuring there’s a model suited for almost any application, from residential buildings to large-scale industrial warehouses. This article dives deep into the types, working processes, materials, key components, and maintenance procedures to guide you in making an informed choice.
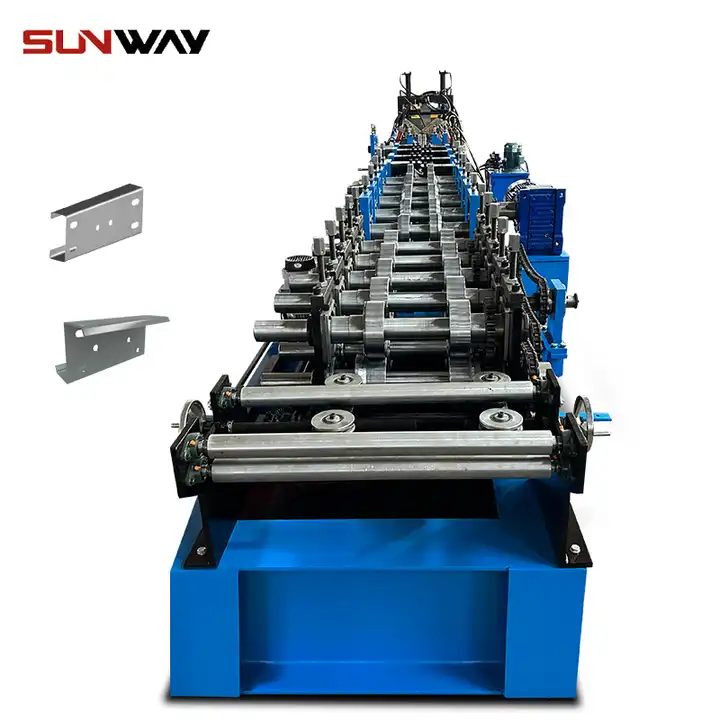
Guide to Corrugated Iron Sheets and Box Profile Sheets
Corrugated iron sheets are an early precursor to box profile sheets. Unlike the box profile design, corrugated sheets have a wavy pattern and are generally used for agricultural and rural structures due to their simple appearance and limited aesthetic options. Box profile sheets, in contrast, are manufactured with a distinct, structured design that allows for better load-bearing capabilities and greater architectural flexibility.
Box Profile Sheets Compared to Corrugated Iron Sheets
Box profile sheets stand out for their ability to cover large spans without additional support, making them suitable for modern roofing and cladding needs. Below is a comparison:
Feature | Box Profile Sheets | Corrugated Iron Sheets |
---|---|---|
Strength | High load-bearing capacity, suitable for wide spans | Moderate strength, requires closer support |
Water Drainage | Excellent due to profile design | Moderate due to wavy pattern |
Noise Reduction | Reduced noise during rain | Noisy during rain |
Application Flexibility | Widely used for industrial, commercial, residential buildings | Primarily rural or agricultural use |
Types of Box Profile Sheets
Choosing the right type of box profile sheet depends on your project’s requirements for thickness, durability, and coating. Here’s a breakdown of some popular models:
Model Name | Material Type | मोटाई | Coating Type | Key Features |
---|---|---|---|---|
Box Profile 32/1000 | Galvanized Steel | 0.5-0.7 mm | Polyester or PVC | Lightweight, durable, rust-resistant |
Box Profile 34/207 | Aluminum | 0.6-0.8 mm | PVDF or Zinc-Aluminum | High corrosion resistance, excellent for coastal areas |
Box Profile 40/960 | Galvanized Steel | 0.8-1.0 mm | Polyester, Polyurethane | High load resistance, preferred for industrial use |
Box Profile 45/150 | Aluminum Alloy | 1.0 mm | PVDF, Polyester | Long lifespan, used for heavy-duty applications |
Box Profile 50/250 | Steel-Zinc Alloy | 1.2 mm | Zinc-Aluminum | Superior durability, suitable for warehouses |
Box Profile 60/200 | Stainless Steel | 0.8-1.2 mm | Polyurethane | Ideal for extreme weather resistance |
Box Profile 75/350 | Galvanized Steel | 1.5 mm | Polyester, PVDF | Robust, ideal for high-load environments |
Box Profile 100/500 | Aluminum Composite | 0.9 mm | Polyurethane, PVDF | Lightweight, heat-resistant |
Box Profile 105/400 | Copper Alloy | 1.0 mm | Natural Finish | Aesthetic appeal, suitable for custom designs |
Box Profile 120/700 | Zinc-Aluminum Alloy | 1.2-1.5 mm | Polyurethane, Zinc Coating | Maximum durability, large span applications |
Each type is designed for specific purposes, whether it’s heavy industrial load-bearing needs or residential applications focused on aesthetics.
Working Process of Box Profile Sheets
The manufacturing process of box profile sheets involves precision and automation to ensure consistent quality. It starts with metal sheets that are coated and treated to prevent rust and increase durability. Here’s a breakdown of the main steps:
- Material Preparation
The sheet metal is cut to the desired thickness and treated with anti-corrosion coatings. This treatment extends the sheet’s life, especially in harsh weather environments. - Profiling and Forming
The sheets are passed through a profiling machine, where rollers shape the sheet into the distinct box profile. The process involves a careful combination of pressure and speed to avoid deformities. - Coating Application
Depending on the intended application, a variety of coatings like PVDF or polyurethane are applied. This coating step not only enhances appearance but adds to the sheet’s durability, ensuring it withstands elements like UV rays and moisture. - Quality Inspection
Each sheet is inspected for uniformity, coating quality, and dimensional accuracy. Quality checks ensure that only high-quality sheets make it to the market. - Packaging and Shipping
Finally, the sheets are bundled and packaged with protective wrapping to prevent damage during transport.
-
Standing Seam Roof Panel Curving Machine
-
बैरल नालीदार रोल बनाने की मशीन
-
Stand Seaming Roof Panel Roll Forming Machine
-
डाउनस्पॉट पाइप रोल बनाने की मशीन
-
गटर रोल बनाने की मशीन
-
Trapezoidal Panel Roll Forming Machine
-
रिज कैप रोल बनाने की मशीन
-
डबल परत पैनल रोल बनाने की मशीन
-
रूफ टाइल पैनल रोल बनाने की मशीन
Key Components of Box Profile Sheets and Their Functions
The construction of box profile sheets involves several essential components, each contributing to their effectiveness and durability.
Component | Function |
---|---|
Base Metal Sheet | Provides structural strength and rigidity |
Anti-Corrosion Layer | Protects from rust and extends sheet life |
Primer Layer | Enhances the bond between base metal and coating |
Top Coating | Provides color, UV protection, and additional durability |
Backing Coat | Protects the underside of the sheet from corrosion |
Machine Speed and Efficiency in Box Profile Production
Machine Type | Production Speed (m/min) | Efficiency (%) |
---|---|---|
Standard Profile Machine | 30-50 m/min | 85% |
High-Speed Profile Machine | 70-100 m/min | 95% |
Custom Profile Machine | 20-30 m/min | 80% |
Customized Mechanical Parameters for Box Profile Sheets
Parameter | Customization Options |
---|---|
Sheet Thickness | 0.5 mm – 1.5 mm |
Profile Width | 500 mm – 1200 mm |
Profile Height | 32 mm – 120 mm |
Coating Type | PVDF, Polyester, Polyurethane |
रंग | Custom colors available |
Applications of Box Profile Sheets
आवेदन | Description |
---|---|
Residential Roofing | Durable and aesthetic roofing solution |
Commercial Buildings | Ideal for warehouses, factories, and shopping malls |
Agricultural Sheds | Long-lasting and cost-effective for rural setups |
Industrial Facilities | Withstands heavy loads and adverse weather conditions |
Installation, Operation, and Maintenance
Aspect | Key Steps |
---|---|
Installation | Secure panels with screws, overlapping as specified |
Operation | Maintain load-bearing limits, avoid undue pressure |
Maintenance | Regular inspections, clean to avoid debris buildup |
Choosing a Supplier: What to Consider
When choosing a supplier for box profile sheets, it’s essential to balance cost, quality, and delivery options. Consider aspects such as material durability, customer reviews, and warranty options to ensure long-term satisfaction.
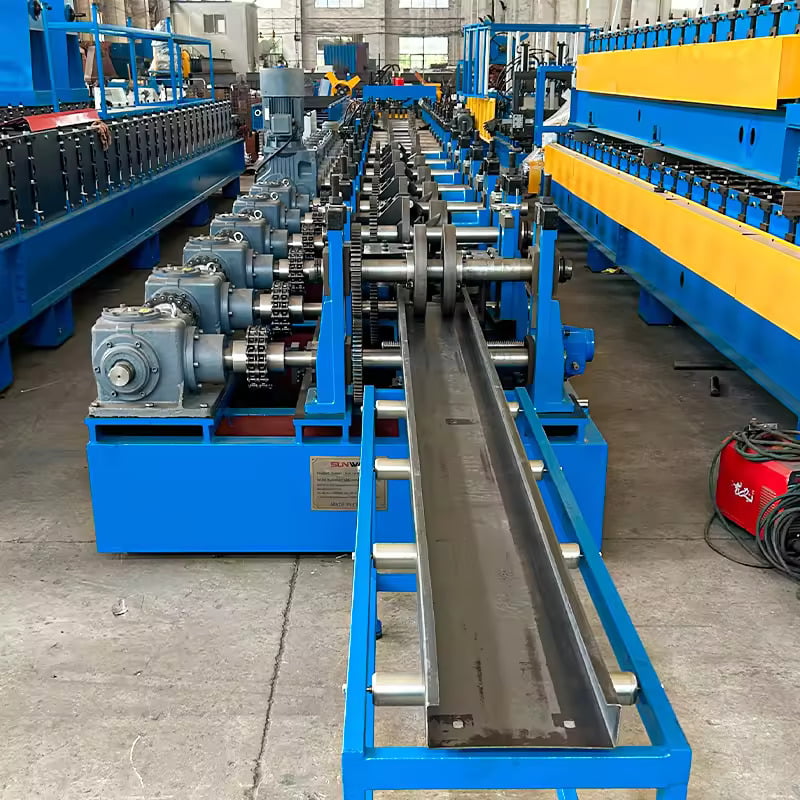
Pros and Cons of Box Profile Sheets
Advantages | Limitations |
---|---|
Durable and Long-Lasting | Initial cost may be higher than alternatives |
Weather Resistant | Requires professional installation |
Aesthetic Variety | May require regular maintenance in harsh climates |
सामान्य प्रश्न
Question | Answer |
---|---|
What are box profile sheets made of? | Typically galvanized steel, aluminum, or zinc-aluminum alloys |
Are box profile sheets good for coastal areas? | Yes, especially those with anti-corrosion coatings like PVDF. |
How often should they be maintained? | Inspect annually and clean if necessary to prolong lifespan. |