ए box plate making machine is an essential equipment for manufacturers who need to produce large quantities of boxes, crates, pallets and other protective packaging products made of cardboard, corrugated sheets, plastic corrugated boards, aluminum plates or steel plates. This guide provides a comprehensive overview of box plate making machine technology, working process, components, suppliers, prices and more.
How Does a Box Plate Making Machine Work?
The working process of a typical box plate making machine involves roll forming methodology to convert flat sheets into shaped plates through consecutive bending and forming stations. The key processes are:
Material Feeding – Sheet materials are loaded onto an uncoiler and fed into the machine through automated rollers. Materials used include cardboard, corrugated boards, plastic boards, aluminum sheets, steel sheets etc.
पूर्व काटने – The sheets may be pre-cut to required widths by built-in slitter scorer machines or shearing machines before forming.
Forming Mechanism – The sheets pass through a series of roll forming stations which applies pressure to progressively bend them into desired plate profiles through bespoke roller dies. Common profiles produced are channels, angles and complex structural shapes.
Design & Customization – Machines utilize CAD systems and CNC precision for forming personalized profiles, logos, text, perforations, slots, holes etc. as per custom design needs.
Automated Fabrication – Formed profiles are automatically sorted, stacked, bundled by robotic arms and output systems ready for downstream packaging processes. Modern machines enable quick changeovers between plate designs.
Waste Collection – Excess materials trimmed by slitters and leftover pieces during forming are automatically collected and discharged aside by conveyors for recycling or disposal.
Therefore, through coordinated feeding, pre-treatment and multi-stage bending mechanisms box plate fabricators can mass produce protective structural packaging components just-in-time.
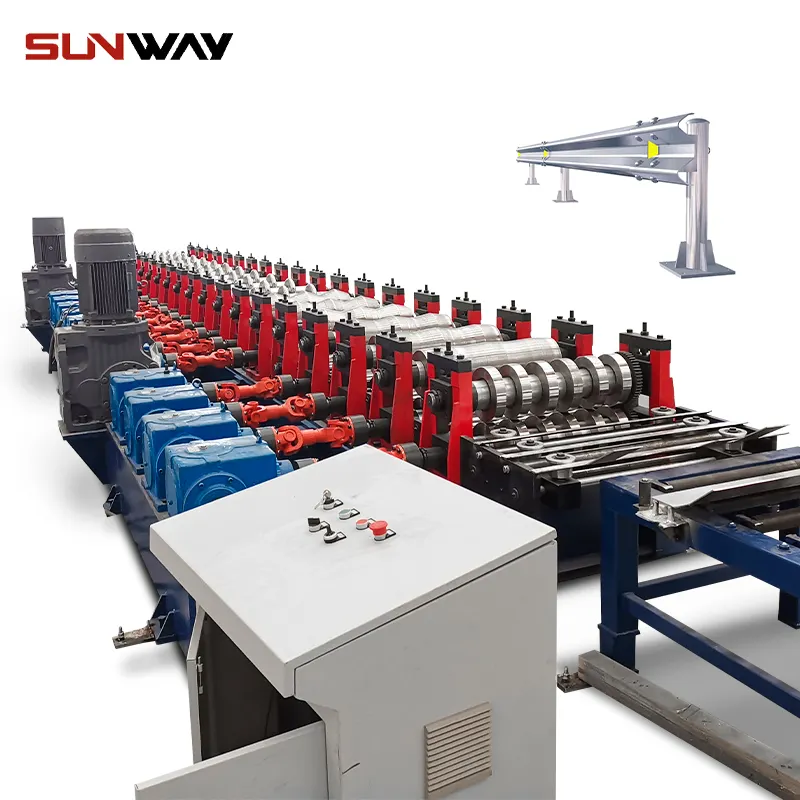
Types of Box Plate Making Machines
There are several equipment varieties used which differ in production rate, automation capabilities, theoretical flexibilities and overall technological sophistications:
Machine Type | Descriptions |
---|---|
Manual and Mechanical Machines | Basic lever operated bending equipment with manual loading/unloading of plates. Low accuracy and productivity. |
Hydraulic Type Bending Machines | Better force control and stroke movement allows precision forming. Moderate production rates. Semi automated models available. |
Pneumatic Type Bending Machines | Utilizes pneumatic cylinder and valve control for force application on sheets. Higher degree of movement flexibility possible. |
CNC Bending Machines | Most advanced computerized numeric control for multi-axis movement of forming dies. Interactive touchscreens allow easy order changes and precision execution. |
All Electric/Servo Motor Machines | Highly responsive AC servo motors coordinates all mechanical motions. Saves energy and enables most accurate positioning. |
[Insert Image of Different Types of Box Plate Making Machines]
Caption: Different varieties of plate bending machines for structural packaging component fabrication
Therefore, while basic manual and hydraulic presses may suffice for small scale applications, automated CNC integrated and all-electric box plate lines offer highest productivity and day-to-day flexibility crucial for industrial producers.
Main Components of Box Plate Machines
Though design variations exist across box plate equipment models, core constituent elements which enables the forming functionality remains similar:
Component | Function |
---|---|
Roller Feeder | Feeds sheet metal stock into machine from uncoiler/stack |
Roll Forming Stations | Applies calculated pressure for bending sheets into shape progressively |
Plate Cutoff Press | Trims formed profiles to customized lengths |
CNC Control Console | Enables flexible order programming and monitoring on touchscreen |
Servo Motor System | Provides coordinated movements between components |
Robotic Stacker | Automatically stacks finished pieces for easy collection |
Conveyor Belts | Transports waste pieces out to collector/recycler |
[Insert Illustrative Diagram Showing Key Parts of a Box Plate Making Machine]
Caption: Core components of a typical box plate fabrication equipment and their roles
While numerous auxiliary tools like loopers, straighteners and deburrers may be integrated in higher end lines, above elements enable the fundamental fabrication functions universally.
Working Process of Box Plate Machines
Understanding the step-by-step flow of sheet materials as they are converted into profiled plates allow appreciation of the forming methodology:
1. Loading – Steel, aluminum or cardboard sheets/reels loaded onto rear feeder rack enters uniformly through powered rollers
2. Feeding – Stock sheets engages with feed rollers which moves and guides it towards first forming section
3. Center Guiding – Additional guides centers the strips accurately as per width
4. Shearing – Hydraulically powered shearing blade levels leading sheet edge
5. Slitting (Optional) – Preset slitting saws slices sheets vertically into multiple strips
6. First Bending – First set of calibrated vertical rolls initiates primary bend
7. Second Bending – Sequential bending stations forms metal gradually into “U” channels through alternate roller stations
8. Final Bending – Last stands concludes profile shaping with small adjustments/flattening
9. Cutoff Press – End presses cuts finished bent shapes into set lengths by numeric control
10. Sorting – Separator gates divide custom and stock plates onto designated conveyors
11. Stacker – Robotic pickers collects and palletizes finished pieces for easy handling
12. Scrap Collection – Leftover scraps automatically ejects into collectors for recycling
Therefore, through coordinated feeding, multi-stage bending and sorting functionalities box plate making machines can transform raw sheets into finished structural packaging components rapidly.
-
सी सेक्शन ब्रेसिंग ओमेगा स्टोरेज रैक अपराइट पोस्ट रोल बनाने की मशीन
-
स्टील बॉक्स प्लेट रोल बनाने की मशीन बनाना
-
शेल्फ कॉलम के लिए बॉक्स बीम स्टील रोल बनाने की मशीन
-
पैलेट रैकिंग स्टेप बीम पी बीम रोल बनाने की मशीन
-
गोदाम शेल्फ ईमानदार रोल बनाने की मशीन
-
विद्युत कैबिनेट फ्रेम रोल बनाने की मशीन
-
दीन रेल रोल बनाने की मशीन
-
केबल सीढ़ी रोल बनाने की मशीन
-
पीवी माउंटिंग ब्रैकेट सी शेप प्रोफाइल रोल बनाने की मशीन
What Materials can be Formed by Box Plate Machines?
A wide range of sheet materials with suitable mechanical properties can be progressively roll formed into profiled box plates:
Sheet Material | Key Properties | Typical Thickness Range |
---|---|---|
Mild Steel | High strength, Durability, Reusability | 0.5 mm – 2 mm |
Stainless Steel | Corrosion Resistance, Longer Life | 0.6 mm – 1 mm |
Aluminum Metal | Lightweight, Strong, Conductivity | 0.8 mm – 1.5 mm |
Galvanized Steel | Zinc Coating, Good Weatherability | 0.3 mm – 1.2 mm |
Cardboard Sheets | Lightness, Printability, Recyclability | 2 mm – 7 mm |
Corrugated Boards | High Cushioning, Stiffness, Low Cost | 5 mm – 15 mm |
Plastic Corrugated Boards | Water/Moisture Resistance, Chemical stability | 4 mm – 10 mm |
[Insert Image Showing Different Materials Being Used in Box Plate Making]
Caption: Wide range of metallic and paper materials can be structurally profiled into box plates
Therefore steel and aluminum allows durable heavy load bearing plates while paper/cardboards suit consumer packaging purposes. Overall wide material flexibility ensures applicability across all major industries.
What are the Application Areas of Box Plate Machines?
The profiled channels, angles and custom plates produced find extremely diverse usage across sectors:
Industry | Application Areas |
---|---|
Consumer Products | Protective Packaging for White Goods, Electronics etc. |
Furniture | Knockdown Crates, Pallets |
Automobiles | Car/Bike Bodywork, Components Casing |
Aviation | Container Boxes for Aero Structures Transport |
Logistics | dexion Shelving, Warehouse Racking, Chemical Drums |
Infrastructure | Scaffolding, Construction Shuttering |
Agriculture | Grain Storage Silo, Greenhouse Framing |
[Insert Infographic Map Showing Major Application Sectors of Box Plate Fabrication Equipment]
Caption: Formed box plates caters to extremely wide ranging usage across essential industries
From delicate electronics to heavy machine structures, appropriately designed structural plates can provide secure and sometimes reusable transportation support. Custom plate capability also enables niche producers to fabricate application specific enclosures in-house through rapid reconfiguration.
How to Choose Right Box Plate Making Machine?
Selecting optimal box plate line for production needs depends on balancing key performance factors:
Machine Parameters | Considerations |
---|---|
Production Speed | Plate sizes, volumes, time targets |
Material Compatibility | Steel, aluminum, cardboard compatibility |
Plate Sizes | Max/min widths, lengths to manufacture |
Precision Rating | Tolerances as per design needs |
Automation Grade | Manual, semi or fully automated features |
Customization Flexibility | Quick design/dimension changes needed? |
Budget Range | Available investment capital for equipment |
How to Choose Right Box Plate Making Machine?
Analyzing above technology factors against business expectations allows suitable equipment matching. Additional pointers while purchasing:
- Prioritize essential functionality needed rather than unnecessary features
- Consider potential production growth over 5-10 years lifespan
- Get machine directly from manufacturer than intermediaries
- Evaluate after-sales support and maintenance ecosystem
- Cross compare multiple box plate machine suppliers on parameters
- Prefer suppliers with proven experience record over new entrants
- Visit facilities to inspect machine quality firsthand before ordering
Therefore, carefully projecting operational needs and matching with ideal box plate equipment capabilities ensures profitable manufacturing.
Who are the Leading Box Plate Making Machine Manufacturers?
With box pallet fabrication demands growing globally, companies worldwide provide technologically advanced solutions:
कंपनी | Country | Typical Price Range | Max Plate Width |
---|---|---|---|
Rollmech Machines | भारत | $100,000 – $250,000 | 1650 mm |
IMTEK Machine Builders | Turkey | $150,000 – $300,000 | 2100 mm |
Erdal Makina Ltd | Turkey | $80,000 – $220,000 | 1800 mm |
Hebei Linhui Plate Machinery | China | $60,000 – $180,000 | 1300 mm |
ASHOK IRON WORKS | भारत | $50,000 – $120,000 | 1500 mm |
[Insert Company Logos and Images]
Caption: Leading global companies providing advanced box plate making equipment solutions
In addition, many regional level manufacturers worldwide also provide cost effective models catering to local demands.
How Much Does a Box Plate Making Machine Cost?
Investment costs depends on multiple aspects like speed, scale, level of automation and customization needs:
Cost Influencing Factors | ||
---|---|---|
Automation Grade | Manual & Mechanical Machines | $50,000 – $100,000 |
Hydraulic Presses | $80,000 – $150,000 | |
CNC Touchscreen Controlled | $150,000 – $350,000 | |
Maximum Plate Width | 1000 mm – 1600 mm | $100,000 – $250,000 |
1800 mm – 2200 mm | $200,000 – $350,000 | |
Production Speed | 10-30 plates/min | $100,000 – $200,000 |
40-60 plates/min | $250,000 – $500,000 | |
Customization Flexibility | Low-Medium | Standard Base Price |
High Flexibility | 50% Price Premium |
In general, automated CNC controlled box plate machines with wider production volumes, larger part processing capabilities and high changeover flexibilities costs over $300,000. However high production scale benefits over long-term pays off the premium price.
Installation & Commissioning of Box Plate Machines
Proper machine installation ensures smooth production commencement:
- Prepare level concrete foundation as per floor plan needs with provisions for machine anchoring
- Unload machine components carefully by crane/forklift without damages
- Assemble frame, houses, stations as per manual using proper tools
- Connect hydraulic, pneumatic and electric power/control cables
- Install safety guards, sensors and accessory tools like loopers
- Check lubrication levels of all moving parts
- Initialize machine control system and set working parameters
- Feed test materials and run trial bending operations
- Fine tune roller positions till achieving target plate accuracy
- Integrate post-forming conveyors if automating transfers
[Insert Image Showing Factors to Consider During Installation]
Caption: Systematic assembly, precise positioning and meticulous testing enables smooth box plate machine commissioning
While producers can self install smaller capacity machines, complex high end lines are setup by supplier engineers ensuring operational readiness from day one.
Operation of Box Plate Making Machines
Despite wide configurational variations, core fabrication sequence remains consistent:
Pre-Operation:
- Select product bending recipe from machine library or input fresh using CAD
- Position roller dies, cutting press as per plate design
- Set feed length, conveyor sorting logic electronically
- Load sheet reels, stack onto rear feeder
Production:
- Start cycle to feed sheets automatically into process flow
- Monitor forming sequence through consecutive bending stands
- Formed pieces gets sorted, stacked by exit automation
- Continuous operation while raw material stock lasts
- Finished products unloaded to pallets/containers
Post-Operation:
- Power down, clean excess oils, material scraps
- Clear residual sheets by overriding rollers manually
- Apply rust prevention oils on exposed machine parts
- Analyze plate quality, adjust paramters if needed
- Schedule maintenance checks based on machine usage
Therefore, beneficial pre-operation preparations coupled with attentive production monitoring allows extracting optimal functioning.
Maintenance of Box Plate Making Machines
Despite sturdy designs, periodic upkeep necessary for longevity:
Maintenance Activity | Frequency | Benefits |
---|---|---|
General Cleaning | Daily | Remove sheet dusts, excess oils |
Inspection of Bearings/Gears | Weekly | Identify wearing signs early |
Hydraulic Oil Replacement | 6 Months | Clean internal contaminations |
Greasing of Moving Joints | 3 Months | Ensure smooth movements |
Machine Calibration | Yearly | Correct forming alignments overtime |
Electrical Connections Check | Yearly | Avoid loose wiring faults |
[Insert Image Showing Maintenance Activities Being Carried Out]
Caption: Systematic lubrications, inspections, recalibrations prevents unexpected downtimes
Therefore, following disciplined maintenance schedules through proper manual keeping enables realizing full machine lifespans.
Advantages of Box Plate Making Machines:
- High production speeds up to 60 plates/min enables mass fabrication
- Automated robotic stacking completely eliminates manual labor needs
- Save inventory space with just-in-time custom plate production
- Computerized metric control offers high repeatability within ±0.2mm
- Quick roller changovers facilitates easy order variety production
- Comprehensive safety mechanisms prevents workplace hazards
- Sturdy designs built for 24×7 heavy industrial loads over decades
- Key functional modules remains consistent across machine sizes
Limitations of Box Plate Making Machines:
- High initial capital investment of over $100,000
- Large factories spaces needed for machine installation
- Skilled manpower necessary for operations and maintenance
- Limited flexibility in plate width sizes due to roller constraints
- Customized plate capabilities involves additional process complexities
- Significant material wastages from sheet edge trims
- Risk of unplanned downtimes from wear/tear of components
Box Plate Machine Failure Analysis, Troubleshooting & Solutions
Failure Mode | Possible Causes | Fixes |
---|---|---|
Uneven Plate Bends | Misaligned Rollers, Improper Gaps | Recalibrate roller positions |
Worn out Roller Surfaces | Replace aging rollers | |
Excess Component Wear | Lack of Lubrication | Increase greasing frequency |
Bearing/Gear Issues | Inspect and replace damaged parts | |
Hydraulic Leaks | Broken Seals or Hoses | Identify and patch leaks |
Blockages in Valves/Pumps | Flush and overhaul hydraulics | |
Inaccurate Length Cuts | Worn out Press Blades | Resharpen or replace aging blades |
Incorrect Measurement Logic | Review and adjust machine parameters |
[Insert Images Depicting Common Defects and Solutions]
Caption: Identifying root causes of failures accurately guides appropriate fixing measures
In addition to above maintenance fixes, having annual service contracts with suppliers provides additional support for troubleshooting and spare parts supply.
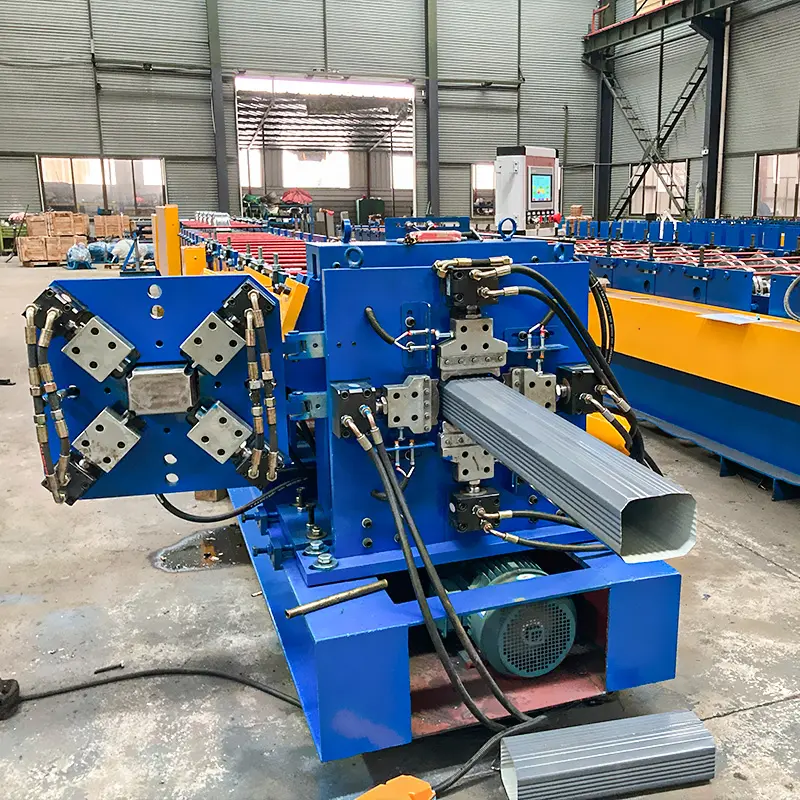
FAQs
Q: What sheet metal thickness can be formed into box plates?
A: Typically 0.5 mm to 2 mm for steel and 0.8 mm to 1.5 mm for aluminum materials can be profiled. Install appropriate roller dies to suit target thickness. Reduce speeds for thicker sheets.
Q: Does the machine require special foundation?
A: A level concrete flooring of atleast 200 mm thickness having suitable anchoring provisions for machine is recommended.
Q: Can cardboard sheets be formed into box plates?
A: Yes, corrugated boards and plastic corrugated boards within 2 mm to 15 mm thickness can be progressively bent using pressure rollers into structural plates. However ensure adhesives can withstand process heating.
Q: What auxiliary equipment helps improve production efficiency?
A: Integration of deburring stations, automatic bundling straps, plate sorting conveyors, custom printing systems helps improve automation flow.
Q: What safety mechanisms are present?
A: Standard features include emergency stop buttons, two-hand operation switches, safety mats, light curtains, door interlocks and overload protections.
Q: What is the typical production capacity?
A: Output speeds range 10-60 plates/min based on width, thickness and profile complexity. Automatic stackers with pallet dispensers helps maximize productivity.
Q: Does the machine require skilled labor?
A: Mechanical proficiencies helps but modern computerized models are simple to operate through menu driven touchscreens without special skill needs.