In the fast-paced world of metal construction, efficiency reigns supreme. Imagine a machine that could churn out not one, but two distinct metal panels simultaneously. That’s the magic of the double layer panel forming machine, a game-changer in the realm of metal sheet production.
This article dives deep into the world of double layer panel forming machines, exploring their intricacies, applications, and the advantages they bring to the table. So, buckle up and get ready to learn all about these versatile metalworking marvels.
Components of Double Layer Panel Forming Machine
A double layer panel forming machine is essentially two single layer roll forming machines stacked on top of each other and working in tandem. Here’s a breakdown of its key components:
- Uncoilers: These reels hold the metal coil that serves as the raw material.
- Levelers: As the name suggests, levelers ensure the metal sheet feeds smoothly into the forming process by removing any bends or irregularities.
- Roll Forming Stations (Upper & Lower): The heart of the machine, these stations consist of numerous forming rollers arranged sequentially. Each roller progressively shapes the metal sheet into the desired profile. The double layer machine features two independent sets of rolls, one for each layer.
- Cutting System: Once formed, the metal sheet is cut to the required length using a shearing mechanism.
- Hydraulic System: This system provides the necessary power to drive the rollers and operate the cutting mechanism.
- PLC Control System: The brain of the operation, the PLC (Programmable Logic Controller) regulates the entire process, ensuring precise control over speed, feed rate, and profile formation.
Material Compatibility: Double layer panel forming machines can handle a variety of sheet metals, including:
- Galvanized steel
- Galvalume steel
- Pre-painted steel
- Aluminum
Production Capacity: The production capacity of a double layer panel forming machine varies depending on the model and the complexity of the profiles being formed. However, they generally offer significant speed and output advantages compared to single layer machines.
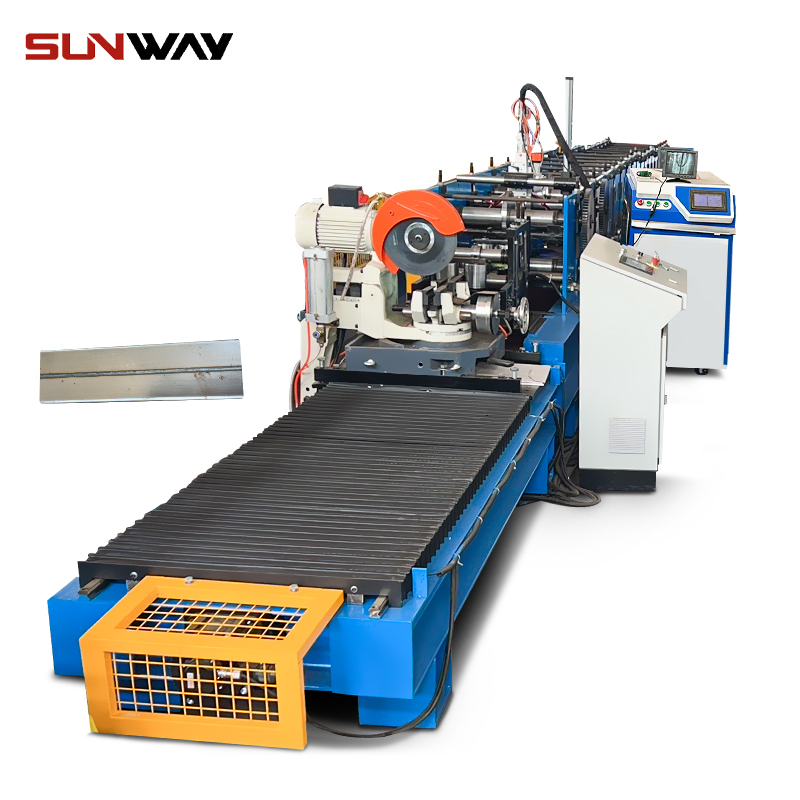
Industrial Applications of Double Layer Panel Forming Machines
Double layer panel forming machines cater to a wide range of industrial applications, particularly in the construction sector. Here are some prominent examples:
- Roofing and Cladding: Double layer machines can simultaneously produce complementary roofing and cladding profiles, such as a trapezoidal inner layer and a corrugated outer layer. This eliminates the need for separate machines and streamlines production.
- Wall Panels: These machines can create composite wall panels with an insulated core sandwiched between two metal layers. This is ideal for applications requiring superior thermal and acoustic insulation.
- Building Envelope Systems: Double layer forming facilitates the creation of integrated building envelope systems, where the inner and outer layers work together to provide structural support, weatherproofing, and insulation.
Beyond Construction: Double layer panel forming machines also find applications in:
- HVAC Systems: For manufacturing insulated duct panels.
- Appliance Manufacturing: For creating refrigerator panels with integrated insulation layers.
- Automotive Industry: For producing lightweight composite panels for vehicle bodies.
Advantages of Double Layer Panel Forming Machines
There are several compelling reasons to consider a double layer panel forming machine for your metalworking operations:
- Increased Efficiency: By producing two panels simultaneously, these machines significantly boost production output compared to single layer machines. This translates to faster project completion times and potentially higher profits.
- Reduced Floor Space: The double layer design eliminates the need for separate machines for each profile, resulting in a smaller footprint. This is especially beneficial in facilities with limited space.
- Cost-Effectiveness: While the initial investment might be slightly higher than a single layer machine, the long-term savings in terms of labor costs, machine operation time, and floor space utilization make double layer machines a cost-effective option in the long run.
- Versatility: These machines offer the ability to produce a wider range of profiles by combining different configurations in the upper and lower layers. This allows for greater flexibility in meeting diverse project requirements.
Considerations When Choosing a Double Layer Panel Forming Machine
While double layer panel forming machines offer numerous advantages, here are some factors to consider before making a purchase:
- Production Needs: Evaluate your production volume and the types of profiles you require. Ensure the machine’s capacity aligns with your specific needs.
- Material Compatibility: Choose a machine that can handle the thickness and type of metal sheet you plan to use.
- Machine Features: Consider the level of automation, control system capabilities, and ease of operation offered by different models.
- Customer Service and Support: Reliable after-sales service and readily available spare parts are crucial for maintaining smooth operations.
- Cost: Double layer machines typically come with a higher price tag compared to single layer machines. Factor in the initial investment cost, maintenance requirements, and potential return on investment before making a decision.
Here’s a table summarizing the key points to consider when choosing a double layer panel forming machine:
Feature | Description |
---|---|
Production Needs | Evaluate your production volume and profile requirements. |
Material Compatibility | Ensure the machine handles your desired metal sheet thickness and type. |
मशीन सुविधाएँ | Consider the level of automation, control system capabilities, and user-friendliness. |
Manufacturer Reputation | Opt for a well-established brand known for quality and reliability. |
Customer Service and Support | Reliable after-sales service and parts availability are essential. |
Cost | Consider the initial investment, maintenance costs, and potential return on investment. |
-
Highway Guardrail End Terminal Forming Machine
-
Highway U/C Post Roll Forming Machine
-
2 Waves Highway Guardrail Roll Forming Machine
-
3 Waves Highway Guardrail Roll Forming Machine
-
ऑटो आकार बदलने योग्य सिग्मा शहतीर रोल बनाने की मशीन
-
ऑटो आकार बदलने योग्य CZ शहतीर रोल बनाने की मशीन
-
ऑटो आकार बदलने योग्य Z शहतीर रोल बनाने की मशीन
-
ऑटो आकार बदलने योग्य घन शहतीर रोल बनाने की मशीन
-
विद्युत कैबिनेट फ्रेम रोल बनाने की मशीन
Double Layer Panel Forming Machine vs Single Layer Panel Forming Machine
Trying to decide between a double layer and a single layer panel forming machine? Here’s a breakdown of their key differences to help you make an informed choice:
Feature | Double Layer Panel Forming Machine | Single Layer Panel Forming Machine |
---|---|---|
Production Capacity | Higher output due to simultaneous production of two panels. | Lower output; produces one panel at a time. |
Floor Space | Smaller footprint; eliminates the need for separate machines. | Larger footprint; requires dedicated space for each profile. |
Cost | Higher initial investment cost. | Lower initial investment cost. |
Versatility | Can produce a wider range of profiles by combining configurations. | Limited to producing single profiles. |
Complexity | Slightly more complex to operate due to two forming sections. | Simpler to operate; suitable for basic profiles. |
Choosing the right machine boils down to your specific needs. If you require high production volume, diverse profiles, and have limited floor space, a double layer machine might be the ideal choice. Conversely, if your production needs are modest, you prioritize a lower initial investment, and work with simple profiles, a single layer machine might suffice.
Operation and Maintenance of Double Layer Panel Forming Machines
Double layer panel forming machines are sophisticated pieces of equipment, but their operation can be streamlined with proper training and maintenance practices. Here’s a glimpse into what you can expect:
- Operation: Most modern double layer machines come equipped with user-friendly PLC control systems. Operators can program the desired profiles, adjust production parameters, and monitor the process through an intuitive interface.
- Maintenance: Regular preventative maintenance is crucial to ensure optimal performance and longevity of the machine. This includes tasks like lubricating moving parts, inspecting rollers for wear and tear, and keeping the hydraulic system topped up with clean oil. Manufacturers typically provide detailed maintenance manuals and recommend periodic service intervals.
The Future of Double Layer Panel Forming Machines
The future of double layer panel forming machines looks bright. As the construction industry continues to emphasize efficiency and sustainable building practices, the demand for these versatile machines is expected to rise. Here are some trends shaping the future of double layer panel forming technology:
- Increased Automation: Advancements in automation will likely lead to machines with even more sophisticated control systems, allowing for minimal operator intervention and further streamlining production processes.
- Material Innovation: The development of new lightweight and high-strength metal alloys could open doors for the creation of novel double-layer panel configurations with superior performance characteristics.
- Integration with Industry 4.0: Double layer panel forming machines have the potential to be seamlessly integrated into Industry 4.0 workflows, enabling real-time data monitoring, optimized production planning, and predictive maintenance.
By embracing these advancements, double layer panel forming machines will continue to revolutionize the metal sheet production landscape, propelling efficiency and innovation in the construction and manufacturing sectors.
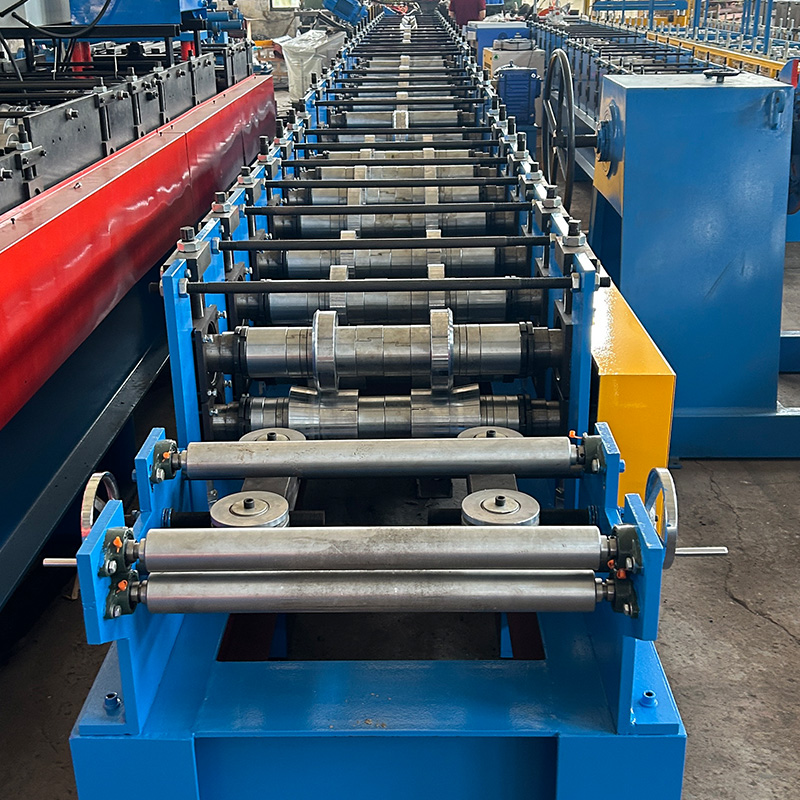
सामान्य प्रश्न
Q: What are the typical production speeds of double layer panel forming machines?
A: Production speeds depend on the machine model, the complexity of the profiles being formed, and the thickness of the metal sheet. However, they generally offer faster production rates compared to single layer machines.
Q: Can double layer panel forming machines handle different metal sheet thicknesses?
A: Yes, most machines can handle a range of metal sheet thicknesses within their specified capacity. The exact thickness range will vary depending on the machine model.
Q: Do I need any special certifications to operate a double layer panel forming machine?
A: In general, there is no requirement for specific certifications to operate a double layer panel forming machine. However, manufacturers typically provide training programs to familiarize operators with the safe and efficient operation of their machines. These programs equip operators with the knowledge to set up the machine for different profiles, adjust production parameters, troubleshoot minor issues, and perform basic maintenance tasks.
Q: Where can I find reputable manufacturers of double layer panel forming machines?
A: Several reputable manufacturers produce double layer panel forming machines. Here are some suggestions for finding them:
- Metal industry trade shows: Attending industry trade shows is a great way to connect with various manufacturers and compare their offerings firsthand.
- Online directories: Several online directories list manufacturers of metal forming equipment, including double layer panel forming machines. These directories allow you to filter your search based on location, machine specifications, and other criteria.
- Industry publications: Trade publications often feature articles or advertisements from metal forming machine manufacturers.
Q: What is the average lifespan of a double layer panel forming machine?
A: The lifespan of a double layer panel forming machine depends on several factors, including the quality of manufacturing, maintenance practices, and the frequency of use. With proper care and maintenance, a well-built double layer panel forming machine can last for decades. Manufacturers typically provide estimates of the expected lifespan for their machines.
Q: Are there any financing options available for purchasing a double layer panel forming machine?
A: Yes, several financing options might be available for purchasing a double layer panel forming machine. These may include loans from banks or equipment financing companies, lease-to-own agreements, or manufacturer-backed financing programs. It’s advisable to research different financing options and compare terms before making a decision.