Overview
ए HAT profile machine, also known as a roll forming machine or a profile bending machine, is a specialized equipment used to form metal sheets into various profiles or shapes. These machines are widely used in the construction, automotive, and manufacturing industries for producing components such as roof trusses, door frames, window frames, and other structural elements. The HAT profile machine is designed to bend and form metal sheets into a specific cross-sectional shape, typically resembling a hat profile, hence the name.
The process of creating HAT profiles involves feeding a coil of metal sheet through a series of rollers that progressively bend and shape the material into the desired profile. The rollers are arranged in a specific pattern to achieve the required cross-section, and the machine can be adjusted to produce profiles of varying dimensions and complexities.
Understanding HAT Profile Machines
HAT profile machines are versatile and can be used to process a wide range of materials, including steel, aluminum, and other non-ferrous metals. The choice of material depends on the intended application and the desired properties, such as strength, durability, and corrosion resistance.
These machines are designed to operate continuously, allowing for high production rates and efficient manufacturing processes. They can be integrated into larger production lines or used as stand-alone units, depending on the specific requirements of the application.
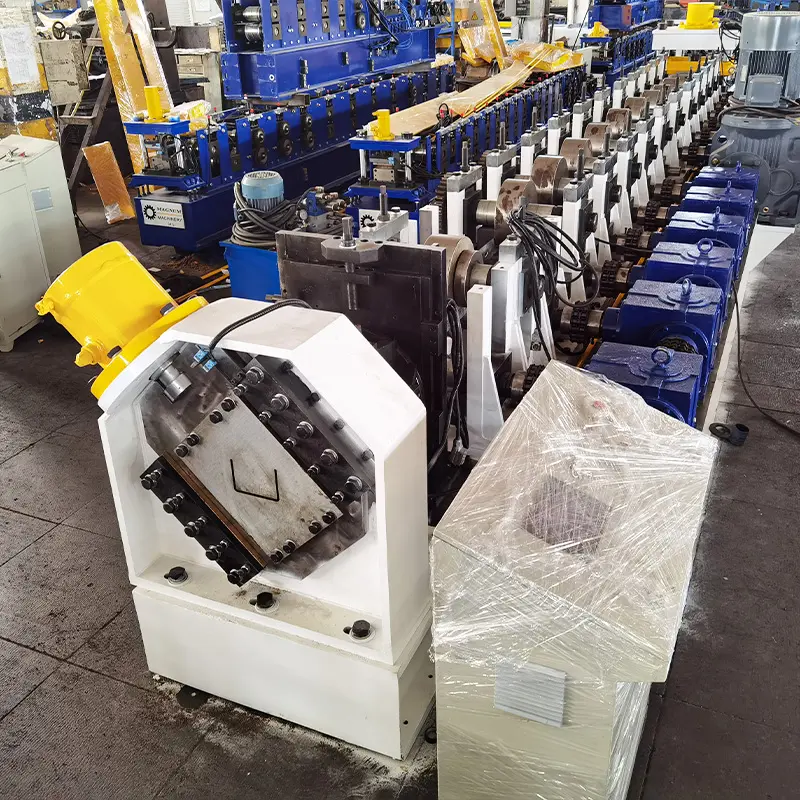
Types of HAT Profile Machines
HAT profile machines can be classified into different types based on their design, operation, and the specific profiles they can produce. Here’s a table summarizing the common types of HAT profile machines:
Machine Type | Description |
---|---|
Entry-Level HAT Profile Machines | These are compact and economical machines suitable for small-scale production or prototyping. They typically have a smaller number of roller stations and may have limited profile forming capabilities. |
Mid-Range HAT Profile Machines | These machines offer a balance between cost and performance, making them suitable for medium-sized manufacturing operations. They can produce a wider range of profiles and may have additional features such as computerized controls or automated material handling systems. |
High-End HAT Profile Machines | These are advanced and highly customizable machines designed for large-scale industrial production. They can handle complex profiles, multiple materials, and offer various automation options for improved efficiency and productivity. |
Working Process of a HAT Profile Machine
The working process of a HAT profile machine involves several stages, each contributing to the final shape and quality of the formed profile. Here’s a breakdown of the typical process:
- Material Feeding: The metal coil or sheet is loaded into the machine’s feeding system, which guides the material into the roller stations.
- Decoiling: The coil is unwound, and the metal sheet is straightened and guided towards the forming section.
- Pre-Forming: In some machines, the metal sheet may undergo initial bending or pre-forming to prepare it for the main forming process.
- Forming: The metal sheet passes through a series of roller stations, each with specifically designed rollers that progressively bend and shape the material into the desired HAT profile. The number of roller stations and their configuration determine the complexity of the profile that can be produced.
- Cutting: Once the desired length of the formed profile is achieved, the machine may incorporate a cutting or shearing mechanism to separate the finished profile from the continuous sheet.
- Post-Processing: Depending on the application, the formed profiles may undergo additional processes such as welding, painting, or surface treatment before being assembled or shipped.
Material Feeding and Forming
The material feeding and forming processes are critical in ensuring the quality and accuracy of the final HAT profiles. Here’s a table highlighting the key aspects of these processes:
Aspect | Description |
---|---|
Material Feeding | Precise and consistent material feeding is essential to maintain the desired profile dimensions and prevent defects. Machines may incorporate advanced feeding systems with tension control and automatic material positioning. |
Roller Design | The design and arrangement of the rollers are crucial for achieving the desired profile shape. Roller configurations can be customized to produce different profiles, and precision machining ensures accurate roller geometries. |
Forming Precision | High-quality machines offer precise forming capabilities, with tight tolerances and consistent profile dimensions along the entire length of the material. This is achieved through robust roller designs, accurate roller positioning, and advanced control systems. |
Material Compatibility | HAT profile machines can handle a variety of materials, including steel, aluminum, and other non-ferrous metals. The machine settings and roller configurations may need to be adjusted based on the material properties and thickness. |
-
वाइनयार्ड पोस्ट रोल बनाने की मशीन
-
ऑटो आकार बदलने योग्य सिग्मा शहतीर रोल बनाने की मशीन
-
ऑटो आकार बदलने योग्य CZ शहतीर रोल बनाने की मशीन
-
ऑटो आकार बदलने योग्य Z शहतीर रोल बनाने की मशीन
-
ऑटो आकार बदलने योग्य घन शहतीर रोल बनाने की मशीन
-
सी सेक्शन ब्रेसिंग ओमेगा स्टोरेज रैक अपराइट पोस्ट रोल बनाने की मशीन
-
स्टील बॉक्स प्लेट रोल बनाने की मशीन बनाना
-
शेल्फ कॉलम के लिए बॉक्स बीम स्टील रोल बनाने की मशीन
-
पैलेट रैकिंग स्टेप बीम पी बीम रोल बनाने की मशीन
Design and Customization
One of the key advantages of HAT profile machines is their ability to produce customized profiles tailored to specific application requirements. These machines can be configured to create a wide range of profile shapes and sizes, enabling manufacturers to meet unique design specifications.
Many machine manufacturers offer customization services, allowing customers to provide their desired profile designs or collaborate with engineers to develop new profiles. The roller configurations and machine settings can be adjusted to accommodate these custom designs, enabling the production of specialized components for various industries.
Suppliers and Price Range
The market for HAT profile machines is served by several reputable suppliers, ranging from local manufacturers to global industry leaders. The price range for these machines can vary significantly based on factors such as machine type, production capacity, level of automation, and additional features. Here’s a table with some potential suppliers and their approximate price ranges:
Supplier | Price Range (USD) |
---|---|
ABC Machinery Corp. | $50,000 – $150,000 |
Global Roll Forming Solutions | $100,000 – $500,000 |
Precision Metal Forming Systems | $200,000 – $1,000,000 |
Industrial Machinery Experts | $300,000 – $2,000,000 |
Please note that these are approximate price ranges, and the actual cost may vary based on specific machine configurations, customizations, and additional equipment or services.
Installation, Operation, and Maintenance
Proper installation, operation, and maintenance are essential for ensuring the optimal performance and longevity of a HAT profile machine. Here’s a table summarizing the key considerations for each aspect:
Aspect | Description |
---|---|
Installation | Professional installation services are often recommended to ensure proper machine setup, alignment, and integration with other equipment or systems. Proper site preparation, including adequate space, power supply, and necessary utilities, is crucial. |
Operation | Trained operators are essential for safe and efficient machine operation. Manufacturers provide comprehensive training programs and user manuals to ensure proper usage, troubleshooting, and maintenance procedures. |
Maintenance | Regular maintenance is crucial for maintaining the machine’s accuracy, reliability, and longevity. This includes tasks such as lubricating moving parts, inspecting and replacing worn components, and calibrating the machine to ensure consistent profile quality. |
Choosing the Right Supplier
Selecting the right supplier for a HAT profile machine is crucial to ensure you receive a high-quality machine that meets your specific requirements. Here are some key factors to consider when choosing a supplier:
Factor | Description |
---|---|
Reputation and Experience | Look for suppliers with a proven track record in the industry and experience in manufacturing high-quality HAT profile machines. Reviews, customer testimonials, and industry recognition can provide valuable insights. |
Product Range and Customization | Evaluate the supplier’s product range to ensure they offer machines that can meet your current and future production needs. Also, consider their ability to provide customized solutions tailored to your specific requirements. |
Technical Support and Service | Reliable technical support and after-sales service are essential for ensuring smooth operations and addressing any issues that may arise. Look for suppliers with a strong support network and responsive customer service. |
गुणवत्ता आश्वासन | Assess the supplier’s quality control measures and certifications to ensure that the machines meet industry standards and deliver consistent performance. |
Pricing and Payment Terms | While cost should not be the sole deciding factor, it is important to evaluate the supplier’s pricing and payment terms to ensure they align with your budget and procurement processes. |
Pros and Cons of HAT Profile Machines
Like any manufacturing equipment, HAT profile machines have their advantages and limitations. Here’s a table comparing the pros and cons of these machines:
Pros | Cons |
---|---|
Versatility: Can produce a wide range of profile shapes and sizes | High Initial Investment: HAT profile machines can be expensive, especially for advanced models with automation features |
High Production Rates: Capable of continuous forming, enabling efficient and high-volume manufacturing | Material Limitations: Some materials may require specialized roller configurations or machine settings to achieve desired profiles |
Precision and Consistency: Advanced machines offer tight tolerances and consistent profile dimensions | Maintenance Requirements: Regular maintenance is necessary to ensure optimal performance and prevent downtime |
Automation Capabilities: Many machines offer automation options for improved efficiency and productivity | Specialized Expertise: Skilled operators and maintenance personnel are required for proper operation and upkeep |
Customization Options: Ability to create custom profiles tailored to specific application requirements | Setup Time: Changing roller configurations or material types may require significant setup time and adjustments |
Advantages of HAT Profile Machines
HAT profile machines offer several advantages over traditional metalworking methods, making them a preferred choice in various industries. Here are some key advantages:
- Efficiency and Productivity: These machines can operate continuously, enabling high production rates and efficient manufacturing processes. This results in reduced lead times and increased output, ultimately improving overall productivity.
- Precision and Consistency: Advanced HAT profile machines are designed to produce profiles with tight tolerances and consistent dimensions along the entire length of the material. This ensures quality and repeatability, which is crucial in applications where precise specifications are required.
- Material Versatility: HAT profile machines can process a wide range of materials, including steel, aluminum, and other non-ferrous metals. This versatility allows manufacturers to produce components for various applications across different industries.
- Customization Capabilities: These machines can be configured to create custom profiles tailored to specific design requirements. This flexibility enables manufacturers to develop specialized components and cater to unique customer needs.
- Reduced Material Waste: Roll forming processes, including those used in HAT profile machines, are known for their efficient material utilization. This results in reduced material waste compared to traditional metalworking methods, contributing to cost savings and environmental sustainability.
- Automation Potential: Many HAT profile machines offer automation options, such as computer-controlled systems, material handling, and integrated cutting or welding operations. Automation can further improve efficiency, productivity, and overall process consistency.
Limitations of HAT Profile Machines
While HAT profile machines offer numerous advantages, they also have some limitations that should be considered:
- High Initial Investment: High-quality HAT profile machines can be expensive, especially advanced models with automation features and customization capabilities. This can be a barrier for smaller manufacturers or those with limited budgets.
- Material Limitations: Certain materials or material thicknesses may require specialized roller configurations or machine settings to achieve the desired profile accurately. This can limit the range of materials that can be processed on a particular machine.
- Maintenance Requirements: Like any industrial equipment, HAT profile machines require regular maintenance to ensure optimal performance and prevent downtime. This includes tasks such as lubricating moving parts, inspecting and replacing worn components, and calibrating the machine.
- Specialized Expertise: Proper operation and maintenance of HAT profile machines require skilled operators and maintenance personnel. Adequate training and experience are necessary to ensure efficient and safe machine operation.
- Setup Time: Changing roller configurations or material types may require significant setup time and adjustments. This can impact production schedules and lead times, especially for smaller batches or frequent product changeovers.
- Production Flexibility: While HAT profile machines are versatile in terms of profile shapes and sizes, they may have limitations in producing complex or irregular geometries compared to other metalworking methods like stamping or casting.
Industrial Applications of HAT Profile Machines
HAT profile machines find applications in various industries due to their ability to produce high-quality, consistent profiles from a wide range of materials. Here are some common industrial applications:
- Construction Industry: HAT profiles are widely used in the construction industry for structural components such as roof trusses, door frames, window frames, and other architectural elements.
- Automotive Industry: These machines are employed in the production of automotive components, including body panels, structural reinforcements, and interior trim pieces.
- Aerospace Industry: HAT profiles are used in the aerospace industry for manufacturing aircraft components, such as structural members, door frames, and floor support beams.
- Furniture Manufacturing: HAT profile machines are utilized in the production of furniture components, including chair frames, table legs, and other decorative elements.
- Agricultural Machinery: Components used in agricultural machinery, such as tractor frames, implement frames, and various structural elements, can be produced using HAT profile machines.
- Renewable Energy Industry: HAT profiles are used in the construction of solar panel mounting systems, wind turbine components, and other renewable energy infrastructure.
- Transportation Industry: HAT profiles are employed in the manufacturing of components for railcars, trucks, trailers, and other transportation equipment.
- General Manufacturing: HAT profile machines find applications in various manufacturing sectors, including electrical enclosures, shelving systems, display racks, and other metal fabrication projects.
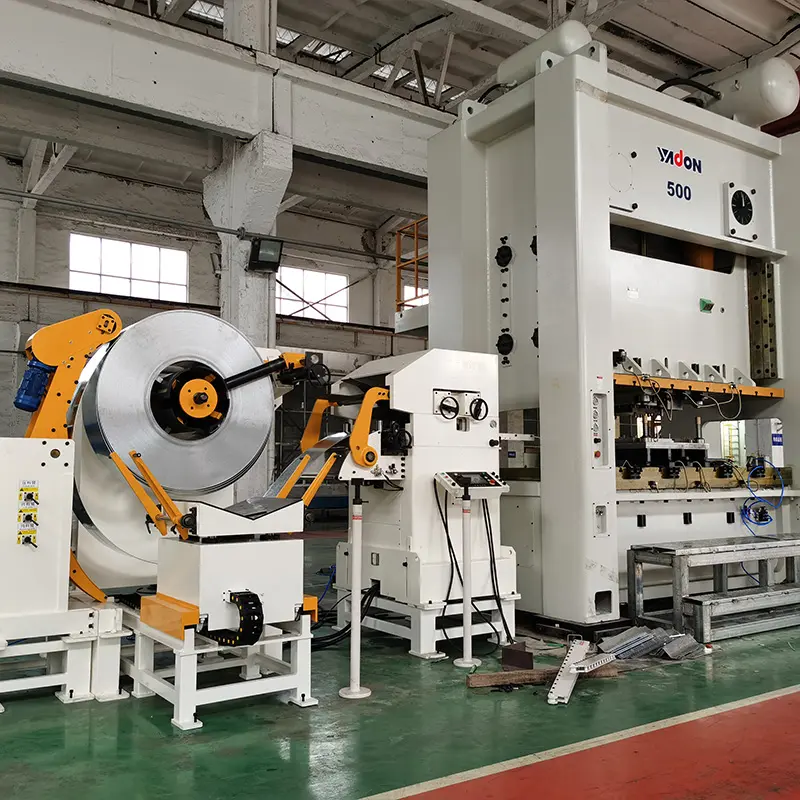
Choosing the Right HAT Profile Machine
When selecting a HAT profile machine for your manufacturing needs, it is essential to consider several factors to ensure you make an informed decision. Here are some key considerations:
- Production Requirements: Assess your production volume requirements, desired profile shapes and sizes, and material specifications. This will help you determine the appropriate machine capacity, roller configurations, and material compatibility.
- Budget and Cost Considerations: HAT profile machines can vary significantly in price, depending on their features, automation levels, and production capabilities. Evaluate your budget and consider the long-term return on investment (ROI) when making your selection.
- Automation and Integration: Determine whether you require automation features, such as computer-controlled systems, material handling, or integrated cutting or welding operations. These features can improve efficiency and productivity but may increase the overall cost.
- Supplier Reputation and Support: Choose a reputable supplier with a proven track record in manufacturing high-quality HAT profile machines. Consider their technical support, training offerings, and after-sales service to ensure proper machine operation and maintenance.
- Customization Capabilities: If you anticipate the need for custom profiles or specific design requirements, evaluate the machine’s customization capabilities and the supplier’s ability to accommodate your needs.
- Space and Infrastructure Requirements: Ensure that you have sufficient space and the necessary infrastructure (e.g., power supply, utilities) to accommodate the machine’s size and operational requirements.
- Operator Training and Expertise: Consider the level of operator training and expertise required for the machine you select. Proper training is essential for efficient operation, maintenance, and safety.
- Future Expansion Potential: If you anticipate future growth or changing production needs, consider selecting a machine that offers scalability or the ability to upgrade with additional features or capabilities.
By thoroughly evaluating these factors and consulting with experienced suppliers or industry experts, you can make an informed decision and select the most suitable HAT profile machine for your specific manufacturing requirements.
FAQs
Q1: What is the typical production speed of a HAT profile machine? The production speed of a HAT profile machine can vary depending on the specific machine model, material being processed, and the complexity of the profile being formed. Generally, these machines can operate at speeds ranging from 10 to 100 meters per minute (33 to 328 feet per minute). Higher-end machines with advanced automation features may achieve even higher production rates.
Q2: Can HAT profile machines handle different material thicknesses? Yes, most HAT profile machines are designed to accommodate a range of material thicknesses. However, the specific thickness capabilities may vary between machine models and manufacturers. It is essential to consult the machine specifications and work closely with the supplier to ensure that the machine is properly configured to handle your desired material thickness.
Q3: How much customization is possible with a HAT profile machine? HAT profile machines offer a high degree of customization in terms of the profile shapes and sizes they can produce. By adjusting the roller configurations and machine settings, manufacturers can create custom profiles tailored to specific design requirements. Additionally, some suppliers offer customization services, allowing customers to collaborate with engineers to develop new profiles or modify existing ones.
Q4: What is the typical maintenance required for a HAT profile machine? Regular maintenance is crucial for ensuring optimal performance and longevity of a HAT profile machine. Common maintenance tasks include lubricating moving parts, inspecting and replacing worn components (such as rollers or bearings), and calibrating the machine to maintain consistent profile quality. Manufacturers typically provide maintenance schedules and guidelines specific to their machines.
Q5: Can HAT profile machines be integrated into larger production lines? Yes, HAT profile machines can be integrated into larger production lines or automated systems. Many machines offer features such as computer control, material handling systems, and interfaces for connecting to other equipment. This integration allows for seamless workflow and increased efficiency in high-volume manufacturing environments.
Q6: How does the material type affect the performance of a HAT profile machine? The material type can influence the performance and settings of a HAT profile machine. Different materials have varying properties, such as strength, ductility, and work-hardening characteristics, which can impact the forming process. Manufacturers typically provide guidelines and recommended settings for processing specific materials to ensure optimal performance and quality.
Q7: What are the typical applications of HAT profiles in the construction industry? In the construction industry, HAT profiles are commonly used for structural components such as roof trusses, door frames, window frames, and various architectural elements. These profiles provide strength and durability while allowing for efficient manufacturing and installation processes.