Elevator guide rail making machines are used to produce the guide rails used in elevator systems. The guide rails act as tracks to precisely guide the elevator car up and down the hoistway.
Elevator Guide Rail Making Machine Key Details
- Equipment type: Roll forming machine
- Materials: Steel coils
- Forming methods: Roll forming
- Outputs: Formed metal rails
- Industrial applications: Elevator systems, material handling systems
Elevator Guide Rail Making Machine Guide
Type | Description |
---|---|
Roll forming machine | Continuously forms metal coils into customized rail profiles by progressively bending sheet through series of roller dies |
डेकोइलर | Feeds metal coil strip into roll former |
Pre-cutting shears | Trims sheets to required coil width before forming |
Roll forming stands | Successive stands with roller dies to incrementally bend metal strip |
Post-cutting shears | Cuts formed rails to required lengths |
Supporting equipment | PLC control, hydraulics, gearboxes, instruments |
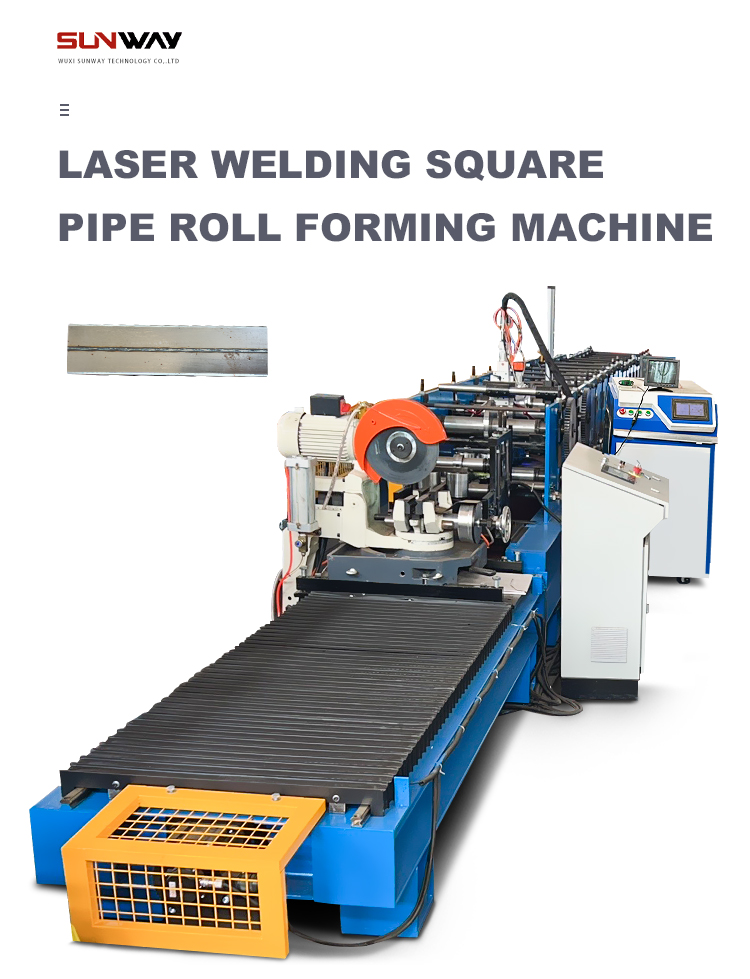
Elevator Guide Rail Making Machine Working Process
The elevator guide rail making machine works by roll forming process. The input raw material is steel coil loaded on an uncoiler. The coil passes through pre-cutting shears where it is trimmed to the specified width required for the rail profile.
The trimmed metal strip then proceeds through successive roller dies mounted on forming stands. Each set of rolls progressively bends the sheet incrementally to gradually form the desired rail configuration.
The fully formed rail profile exits the last stand of rolls and is cut to desired lengths by post-forming shears. The finished cut rails are collected on the outfeed tables.
पैरामीटर
Parameter | विवरण |
---|---|
Material | Low carbon steel, stainless steel, galvanized steel coils |
मोटाई | 1-3 mm typically |
Width | 50-100 mm typically |
Length | Up to 6000 mm |
Speed | 10-15 m/min |
Tolerances | +/- 0.02 mm |
Surface finish | <0.5 microns |
Material Feeding
- Decoiler accommodates up to 5 mt coils
- Decoiler equipped with precision feed rollers
- Width is trimmed by pre-cut shears before forming
- Coil is fed continuously at constant speed into roll forming stands
Profile Forming
- Gradually formed by set of rolls bending sheet incrementally
- 6-8 adjustable forming stands with changeable rolls
- Rolls have machined grooves to impart profile shape
- Bottom rolls powered by geared motors and drives
- Top rolls free running and adjustable by hydraulic cylinder
Profile Design
- Roll pass design software calculates correct roll groove geometry
- Roll pass simulation validates shape through forming stands
- Design optimized for material type and desired rail configuration
- Rolls CNC machined from D2 steel for hardness and durability
Length Slicing
- Carried out by robust post-forming cutting machine
- Heavy duty cutter with hardened blades shears the formed rails
- Length measurement by precision rotary encoder
- Length tolerance +/- 0.5 mm
- Length range 500 mm to 6000 mm
अनुकूलन
- Forming rolls designed and produced for custom rail dimensions
- Roll changeover in 24 hours enables rapid prototyping
- Profile simulation validates rail shape before machining rolls
- Product development support for unique applications
Suppliers and Price Range
Manufacturer | Location | Price Range |
---|---|---|
Machine Mfg Ltd | China | $100,000 – $150,000 |
Formmasters Inc | Europe | $200,000 – $250,000 |
Rolling Equipments | भारत | $125,000 – $175,000 |
Installation Requirements
Parameter | विवरण |
---|---|
Location | Indoor shop floor |
शक्ति | 25-30 kW connection |
Voltage | 380-440 V AC 3 phase |
Compressed Air | Pressure – 6 bar |
Volume – 10 CFM | |
Base Frame | Load bearing concrete floor |
Lighting | 500 lux intensity |
Climate Control | Ambient temp 15-35°C |
Humidity: 20%-60% RH |
-
Highway Guardrail End Terminal Forming Machine
-
Highway U/C Post Roll Forming Machine
-
2 Waves Highway Guardrail Roll Forming Machine
-
3 Waves Highway Guardrail Roll Forming Machine
-
ऑटो आकार बदलने योग्य सिग्मा शहतीर रोल बनाने की मशीन
-
ऑटो आकार बदलने योग्य CZ शहतीर रोल बनाने की मशीन
-
ऑटो आकार बदलने योग्य Z शहतीर रोल बनाने की मशीन
-
ऑटो आकार बदलने योग्य घन शहतीर रोल बनाने की मशीन
-
विद्युत कैबिनेट फ्रेम रोल बनाने की मशीन
Operation
- Minimum 3 operators per shift
- One operator at decoiler & feeding
- One operator to manage roll tooling
- One operator at post-forming cutting station
- Centralized PLC panel for controlling parameters
- HMI touchscreen for monitoring and datalogging
Maintenance
Task | Frequency | Method |
---|---|---|
Roll inspection | Daily | Visual inspection for damage or wear |
Roll lubrication | Weekly | Grease all bearings |
Hydraulic oil | Monthly | Check level and top up |
Yearly | Replace oil | |
Replacement parts | As needed | Spare backup rolls, blades, sensors, motors recommended |
Roll recalibration | Every 2 years | Re-grind roll grooves if wear exceeds 0.15mm |
Choosing Supplier
Parameter | Importance |
---|---|
अनुभव | High |
Roll Design expertise | High |
Build quality | High |
Roll quality | High |
Forming accuracy | High |
Production rate | Medium |
Automation level | Medium |
Service support | High |
Lead time | Low |
Price | Low |
Pros and Cons
Pros | Cons |
---|---|
Continuous and efficient forming process | High initial tooling investment |
Fast set up between batches | Requires heavy baseframe |
Compact layout compared to press brakes | Limited thickness and width capacity |
Consistent tolerance control | Regular maintenance required |
Adaptable to custom profiles | Roll damage can interrupt production |
Advantages Over Press Brakes
- No sheet marking or scratches from dies
- Higher production rate for mass production
- Lower tooling cost per piece
- Continuous forming action vs cyclic bending
- Uniform material properties along length
Limitations vs Press Brakes
- Higher initial tooling cost
- Limited thickness capacity
- Cannot form complex 3D shapes
- Certain asymmetric shapes difficult to form
- Longer tooling lead time
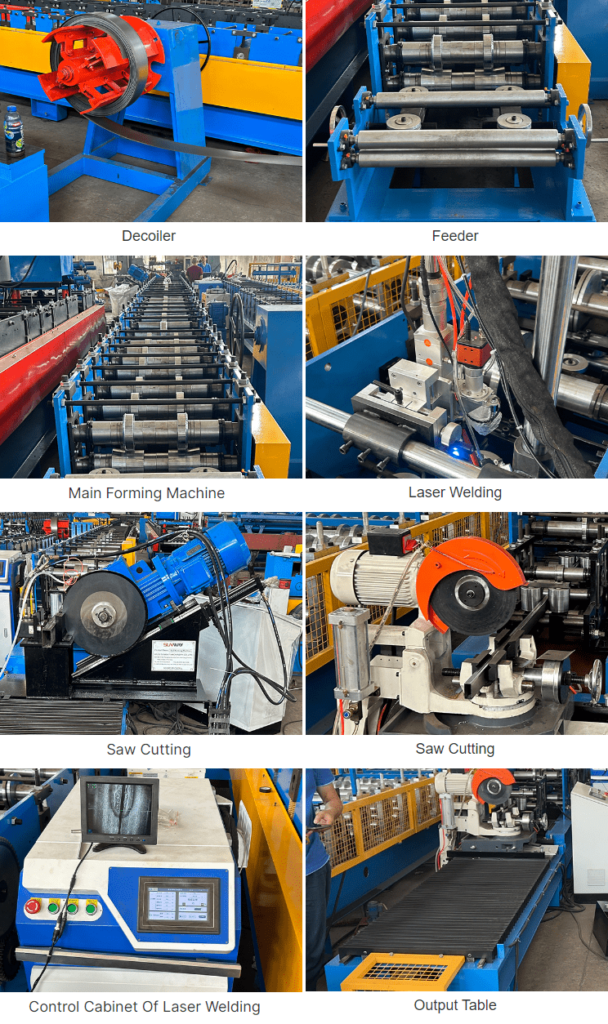
Typical Applications
- Elevator guide rails
- Drawer rails, slide ways
- Conveyor side rails
- Crane wheel tracks
- Automatic parking pallets
- Material handling tracks
- Industrial storage racks
सामान्य प्रश्न
Q: What thickness of steel can these machines handle?
A: Typically 1 mm to 3 mm thickness is possible. Maximum capacity reaches up to 4 mm steel grades.
Q: How fast is the production rate?
A: 10 – 15 meters per minute linear speed is standard. Some high speed machines achieve up to 30 m/min production rate.
Q: What length of rails can be produced?
A: Standard length capacity is 6 meters. Custom built machines can produce up to 12 meter rails.
Q: What accuracy and surface quality is possible?
A: Roll formed parts can achieve tolerances of +/- 0.02 mm and surface finish around 0.5 microns.
Q: What aftersales support is provided?
A: Installation and commissioning help, operator training, warranty on parts, field service for repairs, and phone/email tech support.