ए HAT profile making machine is used to form sheet metal into hat-shaped channel profiles with a wide flange on one side. This versatile roll forming equipment is ideal for manufacturing structural channels, studs, furring channels and other custom profiles up to 8 inches wide.
HAT profile making machines cold roll metal coils through a series of progressive dies to gradually bend the material into the desired hat shape profile with a flat center web and flanges on both sides. One flange is typically wider to facilitate connections. These hat channel profiles are lighter and more rigid than U-channels, allowing longer spans for roofs, walls and support framing.
HAT Profile Making Machine Working Process
The HAT profile production line forms sheet metal coils through a series of roll stands containing shaped rolls. The pre-cut metal strip enters a straightener/ feeder to remove coil set then feeds into the initial forming rolls which start the bending process. After passing through multiple stands, the sheet achieves the final hat channel shape. Finishing operations like cutting follow to create specified lengths.
Key stages:
- Coil Payoff: Sheet coils loaded onto a de-coiler which feeds metal into line
- Feeder & Straightener: Removes coil set and guides sheet into first rolls
- Forming Stands: Bend sheet in progressive stages into hat profile
- Cutting: Cut into lengths by saw, shear or punch
- Counting: Measure lengths for standardization
- Marking: Inkjet prints identification info like order no., length, date
- Packing: Stack and bundle or crate profiles for transport

Material Handling
HAT profile making lines process light to mid gauge sheets up to 3/16 inch thick, though thinner and thicker gauges can also be formed on customized equipment. Common materials include:
- Cold rolled steel
- Hot rolled steel
- Stainless steel
- Aluminum
- Galvanized steel
Coils are the most efficient way to feed sheet into the HAT profile making machines. De-coilers with powered unwind assists are used for consistent, smooth flow of sheet into the process.
Forming Capability
HAT profile roll forming machinery can produce flat flange widths over 8 inches wide. Common profiles include:
- 3-1/2 inch HAT channels
- 4 inch HATs
- 6 inch HAT structural studs
- Custom architectural HAT sections
Within machine limits, many different channel depths and flange widths are possible by changing roll dies. Advanced 3D CAD engineering precisely calculates the progressive roll stands required to gradually form the sheets.
Secondary Operations
In addition to the primary profile forming section, versatility is added with secondary operations integrated inline:
Punching: Pneumatic punch heads can pierce holes into the web/flange Embossing: Rolls can imprint logos, text or patterns into flanges Cutting: Shears, saws & rotary punches sever into lengths Marking: Inkjets print custom text and barcodes for identification Counting:Ensures each stack meets order specifications Packing: Channels automatically stacked, strapped, wrapped
Key Feature Summary
Feature | विवरण |
---|---|
Feed System | Powered de-coiler unwind for coil payoff with 24 inch max coil I.D.; Programmable feed control for widths up to 49 inches; Sheet thickness up to 3/16 inch |
Roll Stands | 20+ stands in forming section with quick changeover; Heavy duty bearing housings; Urethane roll coatings |
Profile Width | Up to 8 inch nominal flat flange width |
Profile Depth | Channels up to 8 inches deep |
Secondary Ops | Inline punching, embossing, shearing, inkjet marking |
Safety Equipment | Light curtains, E-stops, lockouts; Fully enclosed guards |
Computer Controls | PLC logic controls production; HMI touchscreen programming; Data monitoring and storage |
Structure | Robust welded steel frame with precision ground rails |
Applications of Hat Profiles
The high strength per weight ratio of cold formed hat channel profiles suits them for construction and engineering uses:
Structural Framing: Wall studs, floor joists, roof rafters, furring channels Transportation: Truck/trailer roof bows, chassis components, hitches Solar Mounting: Attaching solar panels and racks Building Materials: Studs, purlins, girts, stiffeners Shelving: Uprights, braces and beams Agriculture: Greenhouse framing, livestock equipment General Manufacturing: Conveyor support, mezzanines, racking
Common material choices:
- Cold rolled steel: Cost effective, readily available, recyclable
- Hot rolled steel: Higher load capacity
- Galvanized steel: Corrosion resistance for outdoor use
- Stainless steel: Extreme conditions, sanitary environments
- Aluminum: Lightweight, moderate load capacity
-
वाइनयार्ड पोस्ट रोल बनाने की मशीन
-
ऑटो आकार बदलने योग्य सिग्मा शहतीर रोल बनाने की मशीन
-
सी सेक्शन ब्रेसिंग ओमेगा स्टोरेज रैक अपराइट पोस्ट रोल बनाने की मशीन
-
स्टील बॉक्स प्लेट रोल बनाने की मशीन बनाना
-
शेल्फ कॉलम के लिए बॉक्स बीम स्टील रोल बनाने की मशीन
-
पैलेट रैकिंग स्टेप बीम पी बीम रोल बनाने की मशीन
-
गोदाम शेल्फ ईमानदार रोल बनाने की मशीन
-
विद्युत कैबिनेट फ्रेम रोल बनाने की मशीन
-
दीन रेल रोल बनाने की मशीन
Working Principle
The working principle involves gradually forming flat sheet metal strip into a hat channel profile through multiple bending stages. This cold rolling process with progressive dies avoids over-stressing the material, enabling tight tolerances.
Key steps:
- Sheet coil loaded onto a powered de-coiler
- Feeder straightens strip and guides into initial rolls
- First stage roll bends flanges downward 30-90° *
- Sequential stands gradually form arch shape
- Final two stands close arch and finish flanges
- Shear/punch cuts profiles to length
- Roll angles adjusted to control material elongation
Computerized controls closely monitor sheet feed, roll RPMs and downstream cut lengths to ensure precision parts.
Forming Method Advantages
Hat channel profile making machines provide important benefits beyond their sheet metal shaping capability:
Labor Savings: Automated operation minimizes workers Rapid Outputs: Up to 10,000 feet/hour production लचीला: Quick roll changes to alter dimensions Strong Joints: Hemmed flanges allow connections Material Savings: Optimizes material usage, less waste from shearing Safer: Reduces worker injuries handling sheet goods Energy Efficient: Lower power versus other processes
Cost Effectiveness: Saves on production versus other methods
Limitations of Roll Forming
Despite advantages, a hat profile making machine has limitations including:
- High machine cost
- Large production runs needed for economy
- Limited complexity in profile shapes
- Sheet metal expertise needed
- Periodic roll maintenance
- Floor space required
- Specialized packaging or baling downstream
Each application should be evaluated on total cost, volume needs, available labor, quality demands, and installation considerations.
Price Range
HAT profile making equipment starts around $100,000 for basics models, ranging up to $500,000 or more for large custom machines with integrated secondary operations.
Cost Considerations:
- Line speed
- Width capacity
- Profile size
- Material thickness
- Secondary operations
- Computer programming
- अनुकूलन
- Special coatings
- Support equipment
- Factory freight & installation
Get price quotes from several reputable machinery manufacturers to compare your options. Consider local suppliers as well as international imports weighing factors like support, training, documentation, maintenance accessibility, replacement parts availability, and proximity.
Supplier Evaluation Criteria
Choosing the right HAT profile making equipment supplier is critical for success:
Parameter | Importance |
---|---|
Build Quality | High |
Technical Support | High |
Previous Installations | High |
Roll Design Engineering | Medium |
Local Representation | Medium |
Staff Training | Medium |
Spare Parts Availability | High |
Software Capabilities | Medium |
अनुकूलन | Low |
Pricing | High |
Additional considerations:
- Years in business, financial stability
- Reference checks from existing customers
- Turnaround time for support issues
- Clarity of documentation & manuals
- Warranty duration and scope
Thoroughly qualify machinery suppliers using metrics like these before purchasing. Prioritize technical expertise over lowest capital cost for long term results.
Pros and Cons of Production Methods
Compare roll forming with alternate sheet metal processing choices:
Parameter | रोल बनाना | Press Brake Bending | Extrusion |
---|---|---|---|
Set Up Time | Medium | Long | Medium |
Precision | High | Medium | Medium |
Throughput Speed | Fast | Slow | Medium |
Labor Requirements | Low | High |
Installation & Setup
Proper installation and setup of a HAT profile making line is essential for efficient operation and production quality.
Key steps include:
- Offloading components from truck transport using crane or forklift
- Assembling machine sections together and anchoring to floor
- Leveling stands and verifying tolerances on straightness/squareness
- Mounting coil payoff system and securing to ground
- Stringing cable trays and hooking up electrical wiring
- Attaching hydraulic/pneumatic lines & fittings
- Installing lubrication lines to bearings
- Adjusting roll sets for initial profile parameters
- Jogging machine slowly to confirm component clearances
- Programming automation software for sizes and operations
- Tuning sensors, controls and safety circuits
- Running commission parts to validate quality
- Correcting any issues prior to production sign off
HAT machinery suppliers should provide experienced technicians for installation guidance and final quality inspection before releasing a line for independent operation. Allow several days for proper set up.
Operation Guidance
Trained operators are essential for running HAT profile making equipment to prevent poor quality or damage.
Key operating guidelines:
- Select profile parameters in control software
- Route sheet into feeder and adjust for tracking
- Align edge guides and feed tension settings
- Jog slowly to thread sheet through rolls
- Increase speeds progressively to target production rate
- Monitor strip alignment, quality and cut lengths
- Bundle profiles and remove finished stacks
- Document production counts for tracking
- Perform periodic maintenance checks/lubrication
- Report any abnormal noise, temperature or issues
Maintenance Best Practices
Consistent maintenance preserves uptime and performance for hat channel roll formers.
Daily:
- Visual inspections of guards/hardware/hydraulics/pneumatics
- Lube application on bearings/gears per schedule
- Validation of safety circuits and stops
- Monitoring of roll wear and part quality
Monthly:
- Belt tension checks on drives
- Fastener integrity checks
- Thorough cleaning of dirt/debris
- Wireless communication testing
- Electrical terminations checked for tightness
Quarterly:
- Hydraulics filtration change
- Gearbox oil changes after initial 250 hours
- Calibration of sensors and instrumentation
- Cord and cable inspections
- Test automation backup/restore
Documenting equipment health through logs and trend analysis of issues aids reliability.
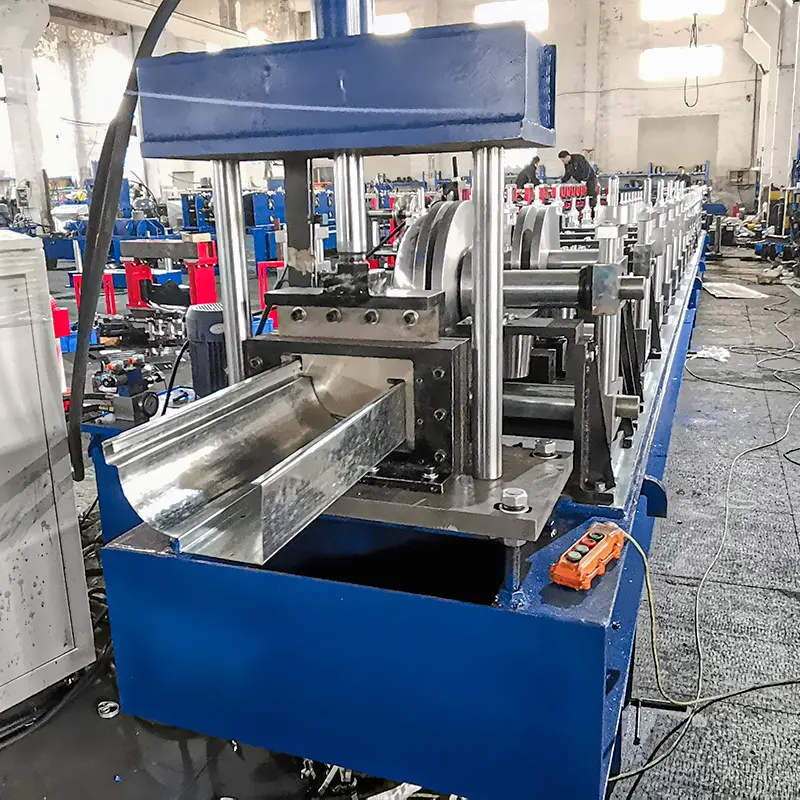
FAQs
What sheet metal thickness can be formed?
- Up to 3/16 inch thickness is possible for common carbon steel but varies based on machine. Thinner/thicker gauges can be produced with customization.
What channel widths are possible?
- Hat profile making lines can typically achieve around 8 inches maximum flat flange width. Wider may be possible through special engineering.
How fast is the production rate?
- HAT roll formers average around 10,000 linear feet per hour depending on finished profile size. Production speed also varies based on material thickness and desired quality.
What secondary operations can be integrated?
- Common integrated operations include punching holes, embossing logos, shearing cut lengths, printing identification markings via inkjets, and automatic counting/packaging of finished product.
What is the lead time for a HAT profile making machine?
Lead times range from 12-20 weeks on average from order placement to shipment. Lead times depend on customization, production workload, and destination considerations.