ए sigma purlin making machine is a type of roll forming equipment used to manufacture sigma-shaped metal purlins. Purlins are Z or C shaped structural beams widely used in metal buildings and roofing systems. They provide support for roof panels attatched perpendicular to the purlin direction.
Sigma purlins have a unique shape that offers higher strength and rigidity compared to other purlin types. The sigma shape allows optimizing material usage while bearing roof loads. Sigma purlins are an excellent choice for pre-engineered steel buildings and low-rise constructions.
This guide covers everything related to sigma purlin roll forming – working principle, main components, process flow, design considerations, capabilities, industrial applications, how to select the right machine, cost analysis, manufacturers, and more.
Sigma Purlin Making Machine Types
Sigma purlin making machines are available in various configurations designed for different production requirements:
Machine Type | Description |
---|---|
Portable Sigma Machine | Compact and movable design for on-site roll forming small batches. Suited for small contractors and builders. |
Manual Sigma Machine | Basic manually operated roll former for low volume production. Economic option for small manufacturers. |
Automatic Sigma Machine | High production rates with automated controls. Preferred for large scale manufacturing plants. |
Customized Sigma Machine | Tailor made sigma purlin lines as per required size range and output. Option for special profiles. |
Choosing the right type depends on production scale, size range, budget, and whether portability to construction sites is required.
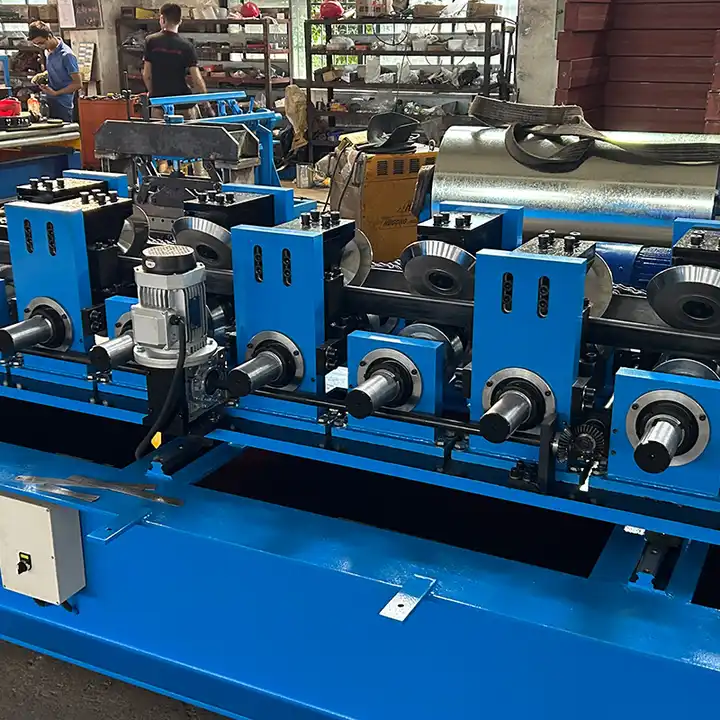
Working Principle
The working principle of sigma purlin rolling line is similar to standard metal roll forming. Continuous deformation of the metal strip passing through consecutive sets of roller dies forms the desired beam profile.
It involves uncoiling a thin metal coil, passing it through a straightener to flatten it, followed by an entry guide. The pretreated strip then passes through the modular roll forming stands.
Each rolling station makes a small bend until the final sigma shape is achieved. Other sections like a punching unit, shear and saw cut the purlins to specified lengths. The last section is the exit guide with a cooling table to set the profile.
Automated machines have powered forming stations, speed synchronization, and controls for production monitoring. While manual machines have hand operated stands for economic small scale use.
Main Components
Section | Components | Function |
---|---|---|
Decoiling | Decoiler machine | Smooth unwinding of metal coil |
Feeding | Feeding tables Rollers, guides | Transports strip, measures length |
Pre-forming | Coil car Cutter, edge trimmer Straightener | Cut to width Controls thickness and shape |
Forming | Forming stands Assembly of roll dies Gearboxes Motors | Progressively form sigma profile |
Post-forming | Punching unit Shear/cutter machine Exit tables | Making holes, cut to length Cooling and straightening |
Automation | PLC controls Servo motors Sensors Conveyors | Monitoring and handling material flow |
The modular forming section is at the heart of the machine. The number of rolling stations here determines output rate and profile quality.
Production Process Flow
A step-by-step overview of the purlin making process:
- Decoiling – The metal coil is loaded on the decoiler. As it unwinds, the strip enters the feeding section.
- Feeding – The strip is threaded through sets of rollers and guides up to the pre-forming area.
- Pre-treatment – Activities like shearing, edge trimming and flattening happen here to prepare the raw stock.
- रोल बनाना – The strip passes through a series of rolling stands. Each set of rolls makes a incremental bend, gradually forming the sigma shape.
- Post-forming – Punching, cutting processes take place here to make holes or cut into lengths.
- Cooling – Formed sigma beams cool and stabilize on the exit tables.
- Bundling – Transverse conveyors group and stack the finished purlins for storage.
Design Considerations
Key aspects that determine sigma machine design:
- Purlin size – Dimensions like depth, thickness, length, bolt holes
- Metal properties – Grade, thickness, yield strength, coatings
- Output requirements – Production speed, hourly rate, operation hours
- Feature needs – Custom profiles, mobile capability
- Budget constraints – Available investment amount
Machines can be configured to customer requirements by choosing:
- Suitable decoiler and feeding dimensions
- Adequate number of pre-treatment processes
- Dimensioning the forming sections for required profile sizes
- Adding post-forming units like punch and shear
- Incorporating automated or manual controls
-
रोलिंग शटर स्लेट रोल बनाने की मशीन
-
Highway Guardrail End Terminal Forming Machine
-
Highway U/C Post Roll Forming Machine
-
2 Waves Highway Guardrail Roll Forming Machine
-
3 Waves Highway Guardrail Roll Forming Machine
-
विद्युत कैबिनेट फ्रेम रोल बनाने की मशीन
-
दीन रेल रोल बनाने की मशीन
-
दो लहरें राजमार्ग रेलिंग मशीन
-
तीन लहरें राजमार्ग रेलिंग मशीन
Capabilities
Parameter | Range |
---|---|
Sigma depth range | 50 – 300 mm |
Max strip width | Up to 1250 mm |
Thickness capacity | 0.5 – 2 mm |
Forming speed | 10 – 25 m/min |
Production rate | 1000 – 10000 pieces/shift |
Length tolerance | +/- 1.5 mm |
- Speed and output depend on automated vs manual design
- Custom machines can exceed standard capability limits
- Advanced machines match international quality standards
Industrial Applications
Major application areas of sigma purlin making machines:
- Pre-engineered Steel Buildings – Roof and wall purlin requirements for metal building structures
- Infrastructure – Bridge beams, transmission towers, conveyor frames
- Commercial buildings – Roof supports in warehouses, factories, agricultural sheds
- Residential – Light load trusses for low height complexes and houses
- Solar energy – Mounting frames for solar PV panel arrays
Sigma purlin production lines enable factories to meet metal building component demand efficiently. These find use across industrial, commercial and residential construction.
How to Choose Sigma Purlin Making Machine
Here is a step-by-step purchasing guide for sigma machines:
1. Calculate Required Output
- Batch size vs mass production decision
- Purlin dimensions and order quantity estimates
- Daily or monthly production rate goals
- Keep output capacity 15-20% more for safety
2. Choose Essential Features
- Basic manual or fully automated
- Fixed or portable frame as per mobility needs
- Standard shapes or custom profiles
- Additional punching and cutting tools
3. Develop Design Specifications
- Structural steel grade and thickness
- Sigma profile dimensions like depth, flange width
- Length range based on construction standards
- Hole size and pattern if punching required
4. Prepare Budget
- Get price quotes from various manufactures
- Compare capabilities against needs
- Factor in auxiliary equipment
- transportation, installation and training costs
5. Select Potential Suppliers
Shortlist manufacturers with proven experience of:
- Earlier similar projects
- Meeting delivery timelines
- Providing after sales service
- Reasonable price and payment modes
- Willingness to customize
6. Review Proposals in Detail
- Evaluate proposed designs and output rates
- Cross check certifications and clientele
- Discuss customization scope if any
- Confirm budget adequacy
- Inspect sample profiles for quality assurance
Careful planning considering above aspects helps choose optimum sigma purlin machine within budget constraints.
Sigma Purlin Machine Manufacturers
Some leading global suppliers with sigma purlin making equipment:
कंपनी | Location |
---|---|
Ability Engineering | China |
Fuwente | Taiwan |
Eramak | Turkey |
Gasparini | इटली |
Metform | भारत |
Choose manufacturers with regional presence for easy service access. Imported machines also have higher cost.
Price Range
Sigma machine price varies based on:
- Automation level and output rates
- Standard vs customized design
- Additional punching and cutting features
- Costs of auxiliary equipment
- Level of after sales service
Indicative price range:
Machine Type | Price Range |
---|---|
Manual | 50,000 – 150,000 USD |
Automatic | 150,000 – 250,000 USD |
Customized | 200,000+ USD |
Higher capacity automated lines with special features may cost over 300,000 USD. Local suppliers can offer relatively economical options.
Get price quotes from shortlisted vendors for exact investment required as per project demands.
Installation & Operation
Smooth functioning of sigma roll forming machines requires:
- Civil foundation preparations
- Workers training
- Electrical, hydraulic connections
- Calibration and test runs
- Periodic maintenance
Civil requirements
- Level concrete or RCC floor
- Sufficient operational area
- Proper shed waterproofing
- Electrical origination
- Lighting and ventilation
Auxiliary equipment
- Decoiler, straightener, shear
- Conveyors for movement
- Tooling like punches, dies
- Measuring systems
Operation
- 2-4 semiskilled workers
- following SOPs for safety
- Achieving rated speed
- Monitoring product quality
- coordinating post-forming operations
Maintenance
- Regular lubrication
- Inspection of wearing parts
- Replacement of roll dies
- Software upgrades
Proper installation and operation procedures ensure high machine uptime and life.
Choosing Between Manual Vs Automatic
Manual | Automatic | |
---|---|---|
Investment cost | Low | High |
Production rate | Up to 1000 pieces/shift | Above 10000 pieces/shift |
Labor requirement | High | Low |
Size range | Limited | Wide |
Operation mode | Batch | Continuous |
Precision | Moderate | High |
Guidelines for selection:
- Manual – Small job shops with lower throughput
- Automatic – Mass production plants aiming for high quality
- Budget constraints may necessitate manual design
- Automated machines preferred for consistency
Choose machine type depending on business scale, cost budgets and target applications.
Limitations of Sigma Purlin Machines
- Manual making holes or custom cut-outs require additional processes causing production bottlenecks
- Initial investment is high for automated lines with special capabilities
- Regular roll die maintenance and skilled supervision essential for quality consistency
- Heavier or thicker coils require stronger decoiling and feeding equipment
- Not suitable for very large section lengths due to difficulty in handling
- Custom profiles complicated by cross section variations
Focus on core competency of high speed mass production of standard sigma shapes. Additional features may compromise robustness. Work with suppliers to balance customization scope against cost.
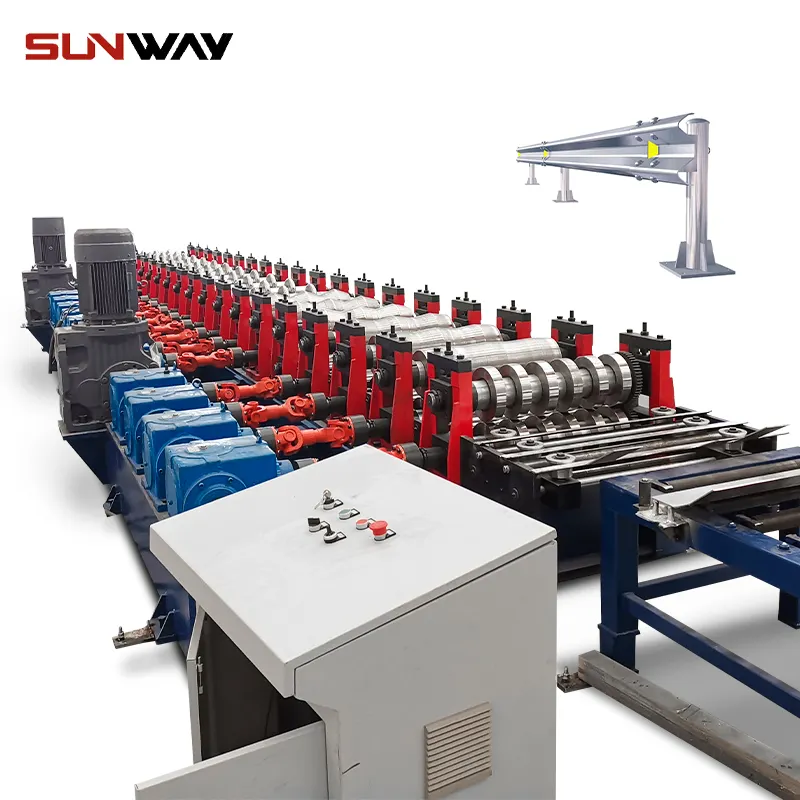
Advantages of Sigma Purlin Machines
- Robust sigma profile ensures structural rigidity for long roof spans
- Higher load bearing capacity compared to other shapes using less steel
- Resists twist or column buckling under wind uplift loads
- Easy to install on site and interface with roofing sheets
- Reduces construction timelines and labor requirements
- Mass production using coil raw material is highly economical
- Lower maintenance costs compared to wood beam roof structures
- Automated lines provide finished cut-to-length pieces consistently
Sigma purlins enable realizing economical and durable building systems due to structural and installation advantages.
सामान्य प्रश्न
What is the thickness range possible for sigma machines? | Standard input strip thickness capacity is 0.5 mm to 2 mm for cold roll forming. Thicker plates require hot or warm rolling process. Choose input stock accordingly. |
What pre-treatment processes are required before sigma forming? | Common pre-treatment includes decoiling, shearing to width, edge trimming, cleaning and flattening. The raw coil may also undergo degreasing or anti-rust oil coating as specified. |
What post-forming operations happen after roll forming sigma shape? | Common post-forming includes punching holes, cutting or shearing to lengths, stamping as per standards, protective coating like color painting and packing for transport. |
What is the lifetime of roll dies used in sigma machines? | With proper operation and maintenance, quality roll dies should handle over 500,000 meters of sheet processing. Periodic lubrication and preventing dents extends service life. Reconditioning may be an option before replacement. |