ए box beam roll forming machine is equipment used to form sheet metal or coils into box beam structures with a hollow rectangular cross-section. This versatile roll former produces lightweight box beams for uses ranging from structural frames to furniture designs.
Overview of Box Beam Roll Forming Machine
Box beams provide higher load capacity and greater structural rigidity compared to other beam types like I-beams. Key features:
- Equipment type: Continuous production roll forming machine
- Forming method: Incremental bending of sheet or coil through a series of roller dies
- Key components: Uncoiler, feed mechanism, forming rollers, cutoff device
- Main parameters: Material type/thickness, beam height and width, production speed
- Output: Hollow box beam lengths cut to specified size
- Applications: Structural sections,trailers, conveyors, scaffolds, mechanical parts
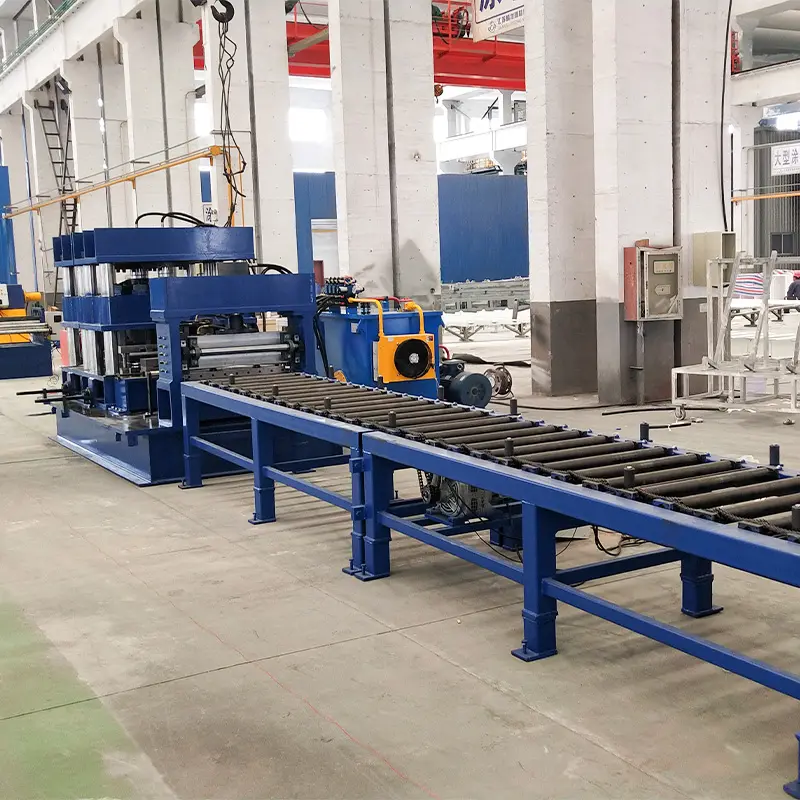
Types of Box Beam Roll Forming Machines
Type | Description |
---|---|
Standard | Fixed dimension box profiles |
Adjustable | Variable box sizes within range |
C/Z purlin lines | U-shaped beams for roofs |
Custom | Profile as per design |
Box Beam Roll Forming Machine Working Process
The roll forming process gradually forms a flat strip into a box-shaped hollow beam by progressive bending as it passes through a series of roller stations.
- Sheet or coil material loaded onto powered uncoiler
- Feed mechanism pulls strip through machine
- Forming rollers incrementally bend strip at each station
- Cutoff device shears finished beams to required length
- Formed box beams exit machine for downstream processes
Precisely aligned rollers, optimized roller contours and programmed synchronization result in beams with consistent quality and dimensional accuracy.
Key Components
Material Feeding
- Decoiler or uncoiler – rotates coil for smooth, kink-free strip release
- Sheet stacker – for box beams from individual sheets
- Feed mechanism – pinch rollers or caterpillar drives feeding into process
- Entry guides – support and straighten strip before forming
- Feed table – roller table for supporting long strip lengths
Profile Forming
- Forming stations – 5-16 stations for gradual bending
- Upper and lower rollers – progressively form flat strip into box
- Horizontal, vertical & inclined rollers
- Quick change forming heads – for profile adjustments
- Roller contour programming – for precision bending
Beam Cutoff and Exit
- Cut to length device – Flying cutoff shear/saw for accurate cuts
- Length measuring system – encoder or photocell based
- Exit tables – roller supports for finished beams
- Stacker – collects cut beams for bundling
Machine Frame and Drives
- Robust welded frame – maintains component alignment
- Geared AC motor drives – adjust production speed
- Touchscreen HMI and PLC controls – for programmed automation
Safety Equipment
- Emergency stop buttons – for instant shutdown
- Limit switches, sensors – detect errors
- Safety fences, barriers – prevent access during operation
- Status indicator lights – show operational states
-
Auto Changeable C Z Purline Machine
-
वाइनयार्ड पोस्ट रोल बनाने की मशीन
-
मचान तख़्त रोल बनाने की मशीन
-
लाइट गेज स्टील रोल बनाने की मशीन
-
ऑटो आकार बदलने योग्य सिग्मा शहतीर रोल बनाने की मशीन
-
ऑटो आकार बदलने योग्य CZ शहतीर रोल बनाने की मशीन
-
ऑटो आकार बदलने योग्य Z शहतीर रोल बनाने की मशीन
-
ऑटो आकार बदलने योग्य घन शहतीर रोल बनाने की मशीन
-
तल डेक रोल बनाने की मशीन
Forming Features
Precision Roll Forming
Programmable roll contours and sequencing enables production of box beams with reliable dimensional accuracy and repetitive precision. Quick change cassette-style tooling allows fast profile adjustments.
Flexible Manufacturing
By adjusting only a few components, the same machine can produce box beams of various sizes, thicknesses and materials. Further customization for specialized beams is also possible.
Single Operator
Fully automated operation after initial setup only needs one person for loading material and monitoring. Touchscreen controls enable easy parameter entry.
Secondary Operations
Additional punching, slotting, embossing, hole drilling, notching and marking units can be integrated for beams with modifications. Powder coating equipment can also be attached.
Suppliers and Costs
Manufacturer | Location | Price Range |
---|---|---|
ECOTECK | इटली | $100,000 to $250,000 |
FONLE | China | $50,000 to $150,000 |
Gasparini | इटली | $150,000 to $300,000 |
Metform | Turkey | $75,000 to $200,000 |
Shandong ShuangLong | China | $30,000 to $100,000 |
- Prices vary by speed, size and features
- Average cost: $125,000
- Local vendors offer operational/maintenance services
Installation and Operation
Activity | Description |
---|---|
Site preparation | Level concrete flooring Electrical connections |
Positioning | Unload sections with forklift Reassemble as per drawings |
Calibration | Adjust rollers and verify alignments |
Trial runs | Set speeds, test stops and confirms functioning |
Parameter entry | Input material specs and beam sizes |
Routine operation | Automatic running with minimal supervision |
Safety | Ensure proper guarding and no accessibility during operation |
- Install per manufacturer documentation
- 3-4 days installation duration typical
- Operator training recommended
Maintenance
Frequency | Activity |
---|---|
Daily | Clean equipment debris Check lubrication levels |
Weekly | Inspect electrical cabinets Verify hydraulic seals |
Monthly | Check alignment of components Confirm conveyor belt tension |
Quarterly | Complete oil changes Calibrate instrumentation |
Yearly | Replace wear components Schedule preventative maintenance |
Choosing a Reliable Supplier
Parameter | विवरण |
---|---|
Product range | Various sizes and options |
अनुकूलन | Profile programming services |
Certifications | ISO accreditations |
अनुभव | Years in business Installed base |
सहायता | Installation assistance Local distributors Spare parts inventory |
Production | In-house manufacturing |
Pricing | Competitive quotes Financing assistance |
Warranties | Coverage period |
Pros and Cons
Advantages
- Higher load capacities than open beams
- Increased strength-to-weight ratio
- Resists twisting and buckling forces
- Versatile sizing for wide ranging uses
- Hollow inside permits passing cables/fluids
- Lightweight compared to solid beams
- Smooth surfaces allow easy finishing
Limitations
- Beam height restrictions due to forming roller diameter limits
- Not recommended for tension components
- Expansion/contraction considerations for long exposed beams
- Limited suppliers compared to standard sections
- Higher cost than hot-rolled steel beams
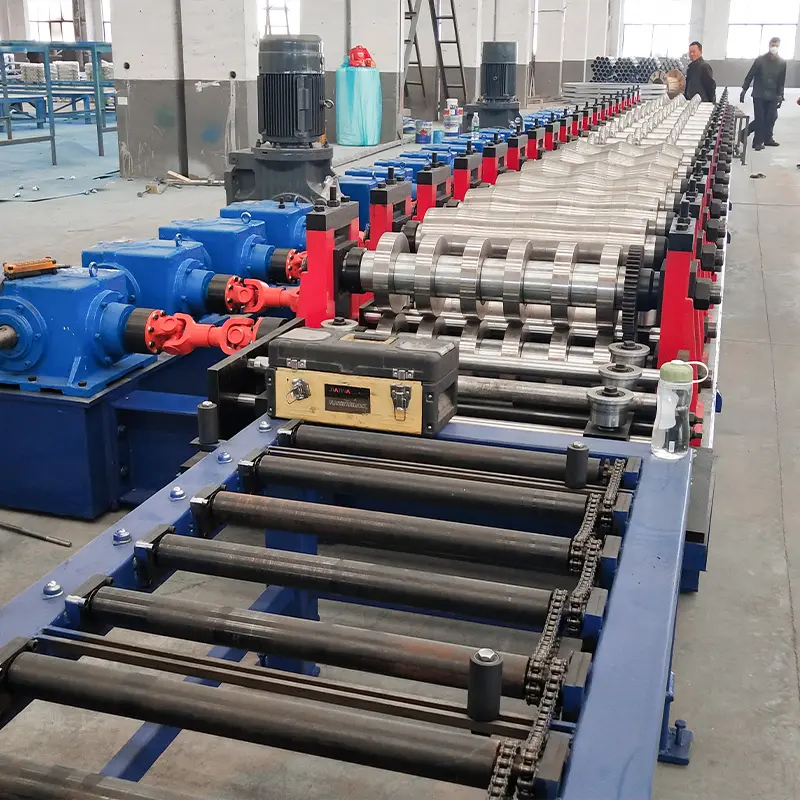
सामान्य प्रश्न
What materials can be used to manufacture box beams?
Common materials include mild steel, stainless steel, and aluminum. Galvanized steel and pre-painted coils are also suitable for corrosion resistance.
What industries utilize box beam roll formed sections?
Major applications are in construction, infrastructure, warehouses, conveyors, cranes, and customized machine structures. Box beams are also popular in truck and trailer frames.
What determines the load capacity of a box beam?
Key factors are material grade, metal thickness, height and width dimensions, beam span lengths, and end connections. Capacity values can be calculated or tested as per applicable codes.
What is the typical accuracy of the roll formed box profile?
Precision roll forming can reliably achieve tolerances of +/- 0.5 mm on critical dimensions with correctly aligned and programmed equipment.
How to select the optimal height and thickness for an application?
An engineering assessment of loading conditions and span distances should be done to finalize appropriate beam section properties. Rule of thumb is higher and thicker beams carry more load over longer spans.
What are the advantages of CNC adjustable roll formers?
Adjustable forming heads allow fast production of varied beam sizes from 50 mm up to 600 mm tall without tooling changes. Common interface bus simplifies programming.
How does automated beam cutoff length control work?
A programmable logic controller determines where to shear beams based on an incremental length measuring encoder signal. Lengths are typically accurate to +/- 2.0 mm.