Roll forming is a metal working process that involves continuously bending a long strip of sheet metal into a desired cross-sectional profile. रोल बनाने की मशीनें are used to produce longitudinal profiles with a constant cross-section from sheet or strip stock.
Overview of रोल बनाने वाली मशीनें
Roll forming machines are available in a wide range of configurations to produce various geometries and sizes. The roll forming process lends itself well to high volume production and automation.
Key details about roll forming machines:
- Used to form metal sheets and coils into customized longitudinal profiles
- Produce high volumes of parts efficiently
- Well suited for automation and mass production
- Achieve accurate and repeatable profiling
- Capable of forming a variety of metals including steel, aluminum, brass, etc.
- Output products include panels, frames, enclosures, roofing, racks, solar panel frames, highway products, etc.
- Roller dies continuously shape the strip as it passes through successive stands
- Various secondary operations can be integrated in the production line
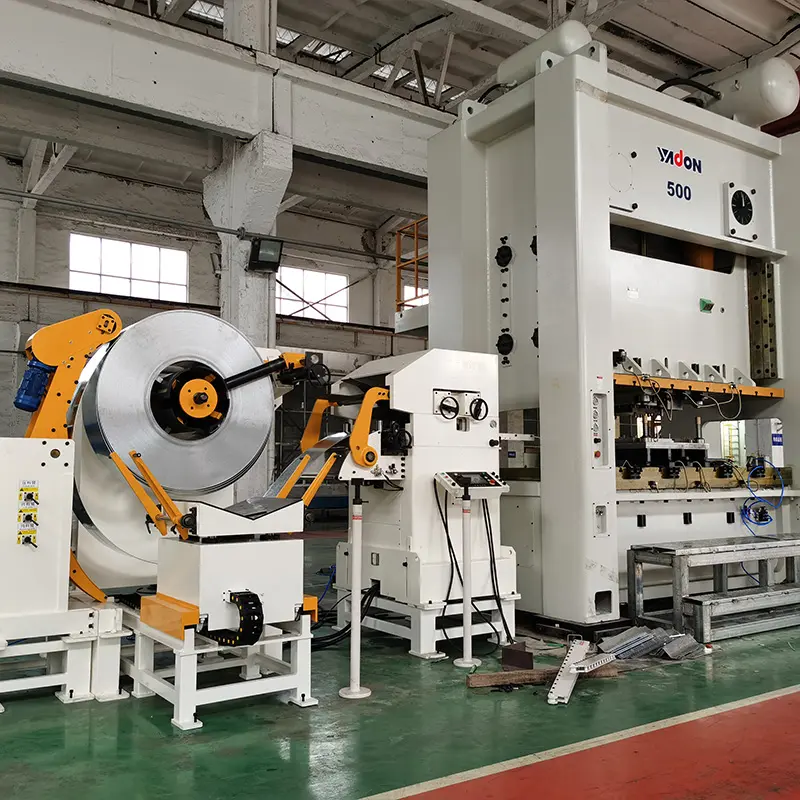
Roll Forming Equipment Guide
There are several types of roll forming equipment with varying technical specifications and capabilities:
Table 1: Roll forming equipment types
उपकरण | Description |
---|---|
Pyramid-style | Multiple roll stations arranged in a pyramid shape for compact footprint |
C-style | C-shaped frames hold roll stations on top and bottom section |
Housing line | Inline series of roll stands for long parts |
Portable | Lightweight, movable roll formers |
Custom | Configured to application requirements |
Working Process of a Roll Forming Machine
The roll forming process involves passing sheet or coil stock through consecutive stands of roller dies that continuously form the material until the desired shape is obtained.
The typical steps in roll forming are:
- Material Feeding: Sheet or coil stock entered into the roll former
- Forming: Material passes through progressive roller dies
- Cutting: Formed profile cut to length
- Secondary Operations: Additional operations like punching, welding, hardware insertion performed inline
Key Aspects of Roll Forming Machines
There are several important considerations when selecting and operating roll forming equipment:
Material Feeding
The roll forming process starts by entering sheet, coil or strip stock into the equipment.
Table 2: Roll forming material feeding
Method | विवरण |
---|---|
Coil/Reel | Continuous coils are straightened and fed into the roll former |
Sheet Stock | Individual sheets loaded manually or automatically |
Specialty Feed | Custom material handling for large/complex stock |
Forming Capabilities
The roller dies continuously transform the shape as the material passes through.
Table 3: Roll forming capabilities
Attribute | Description |
---|---|
Profiles | U-channel, C-channel, Z-profile, hat profile, tube profiles, custom shapes |
Geometries | Simple to complex forms possible |
Metals | Carbon steel, stainless steel, aluminum, copper, brass |
Sizes | Thickness from 0.15 mm to 16 mm, widths up to 3 m |
Dimensions | Lengths up to 30 m, unlimited with coil stock |
Finishes | Smooth, textured, embossed, painted, galvanized |
-
रोलिंग शटर स्लेट रोल बनाने की मशीन
-
Highway Guardrail End Terminal Forming Machine
-
Highway U/C Post Roll Forming Machine
-
2 Waves Highway Guardrail Roll Forming Machine
-
3 Waves Highway Guardrail Roll Forming Machine
-
नालीदार पैनल रोल बनाने की मशीन
-
लाइट गेज स्टील रोल बनाने की मशीन
-
स्टील बॉक्स प्लेट रोल बनाने की मशीन बनाना
-
विद्युत कैबिनेट फ्रेम रोल बनाने की मशीन
Design Considerations
Proper roll design is critical for profile accuracy and performance.
Table 4: Roll forming design factors
Aspect | विवरण |
---|---|
Roll Design | Precisely engineered rolls to produce desired profile |
CAD Models | Creating 3D models to visualize profiles |
Prototyping | Test profiling on sample materials first |
Tooling | Rolls machined from alloy steel or similar durable materials |
Accuracy | Ability to hold tight tolerances for profile consistency |
Secondary Operations
Various inline secondary operations can be integrated as needed.
Table 5: Roll forming secondary operations
Processes | Description |
---|---|
Cutting | Cutting profile to length by sawing, shearing, punching |
Hole Punching | Punching holes for fasteners, wiring, etc |
Notching | Notching sections for connections, fittings |
Embossing | Embossing decorative patterns into the profile |
Hardware Insertion | Automatically inserting clips, brackets, fasteners |
Welding | Spot welding, MIG welding pieces together |
Coiling | Recoiling product for some applications |
अनुकूलन
Roll forming lines can be customized to produce specialized products.
Table 6: Roll forming customization
Option | विवरण |
---|---|
Custom Profiles | Unique shapes for specialized applications |
Secondary Operations | Additional fabrication steps like punching, drilling, welding |
Automation | Automating material handling and secondary processes |
Quick Changeover | Minimizing tooling and setup time between jobs |
Testing | Verifying application suitability through prototyping and field testing |
Choosing a रोल बनाने की मशीन Supplier
Many factors go into choosing a roll forming machine and manufacturer.
Table 7: Roll forming equipment suppliers
कंपनी | Location |
---|---|
A.G. Roll Forming | Canada |
सैमको मशीनरी | Canada |
Metform International | USA |
Shanghai TEN-HIGH Roll Forming Machinery | China |
Botou Xianfa Roll Forming Machine Factory | China |
Uno Roll & Machine | Taiwan |
Rajlaxmi Rollform | भारत |
Roll forming machines range in price from under $10,000 to over $100,000 for fully automated production lines. Customization, secondary operations, and production capacity impact overall system cost.
Key Buying Considerations
Parameter | Importance |
---|---|
Production Volume | Match equipment size to monthly/yearly output |
Profile Requirements | Confirm equipment can produce needed shapes and sizes |
Secondary Operations | Determine requirements for punching, welding, etc |
Automation Needs | Evaluate manual versus automated operation |
Precision | Necessary accuracy and repeatability |
Changeover Time | For flexibility in small production runs |
Reputation | Choose reputable manufacturers with experience |
सहायता | Installation help, maintenance contracts |
Operating, Maintaining, and Troubleshooting Roll Forming Machines
Proper use and care of roll forming machines is essential for maximum performance and longevity.
Installation
Roll forming equipment is installed and commissioned by technicians.
Table 8: Roll forming installation
Activity | विवरण |
---|---|
Site Preparation | Verifying sufficient space, power, utilities per specifications |
Delivery | Coordinating equipment delivery and moving into place with rigging/forklift |
Assembly | Assembling machine sections, drives, controls, guards if necessary |
Connection | Connecting power, utilities, compressed air lines |
Calibration | Precision alignment of rollers and test runs |
Operation
Roll forming machines can be operated in automatic or manual mode.
Table 9: Roll forming operation
Function | Description |
---|---|
Material Loading | Feeding coils or sheet stock either manually or automatically |
Jog Controls | Using jog buttons to feed material through form roll stations |
Parameter Input | Entering production data like line speed, cut length |
Process Monitoring | Watching machine motion, lubrication levels, tooling condition |
Safety | Ensuring guards are in place, emergency stops accessible |
Maintenance
Regular maintenance enhances performance and lifespan.
Table 10: Roll forming maintenance
Activity | Frequency |
---|---|
Inspecting tooling | Daily |
Lubricating roll bearings | According to usage |
Replacing worn rollers | As needed |
Cleaning & removing debris | Daily |
Inspecting/tensioning drive chains | Monthly |
Checking hydraulic fluid | Monthly |
Tightening fasteners | Periodically |
Troubleshooting
Common roll forming issues include:
Table 11: Roll forming troubleshooting
| Issue | Solution
Links provided by Claude may not always be valid or up to date. We appreciate your patience as we work to improve link accuracy.
Choosing Between Roll Forming Machine Manufacturers
When investing in a roll forming system, it’s important to compare the pros and cons between equipment suppliers.
रोल बनाने की मशीन Brand Comparison
Table 12: Comparing roll forming equipment brands
ब्रैंड | Pros | Cons |
---|---|---|
A.G. Roll Forming | Broad product range, high precision, robust construction | On the expensive end |
सैमको मशीनरी | Reliable performance, quick delivery times | Limited customization options |
Metform | Heavy duty American-made, highly configurable | Long lead times on orders |
Ten-High | Cost effective, high production output | Questionable quality control |
Xianfa | Budget friendly prices, decent quality | Can lack sophistication of premium brands |
When evaluating brands, key aspects to consider are build quality, tolerances, production rates, lead times, cost, and service support. On-site demos and getting client references is also suggested.
Applications of Roll Formed Parts
Roll formed components have broad use across industries like:
Table 13: Roll formed parts applications
Industry | अनुप्रयोग |
---|---|
Construction | Studs, door frames, roofing, cladding, drainage, structural profiles |
Automotive | Body panels, rails, enclosures |
Aerospace | Aircraft fittings, frames, interior panels |
Infrastructure | Light posts, railings, road barrier, solar panel frames |
Transportation | Truck & trailer panels, hitches, frames |
Shelving | Uprights, beams, ties, decking |
एचवीएसी | Ducts, vents, air distribution components |
Common roll formed parts include C-studs, U-channel, Z-purlins, solar rails, roofing panels, building panels, highway products, rack uprights, and enclosures.
Advantages of Roll Forming
Compared to other fabrication techniques, roll forming offers benefits like:
Table 14: Roll forming advantages
Benefit | Description |
---|---|
Efficiency | High production rates, low cost per part |
Flexibility | Fast changeovers between jobs |
Accuracy | Excellent tolerance control |
Consistency | Repeatable quality part to part |
Automation | Easy to integrate robots, conveyors |
Strength | Cold working improves material strength |
Safety | Low risk compared to stamping or machining |
Material Savings | Low waste relative to other processes |
Design Freedom | Produce complex geometries |
With precision tooling and automation, roll forming competes favorably against other manufacturing approaches on cost, quality and lead times.
Limitations of Roll Forming
Despite benefits, limitations include:
Table 15: Roll forming limitations
Drawback | विवरण |
---|---|
Initial Cost | Significant investment for equipment, tooling |
Range of Materials | Not as wide as other methods |
Secondary Operations | Requires additional steps for holes, notches |
Profile Length | More passes needed for longer parts |
Low Volume | Higher volume required for efficiency |
Non-Standard Sizes | Limited to available tooling and machine width |
Roll forming favors high volume continuous production. Challenging limitations can be overcome with creative tooling and line design tailored to product requirements.
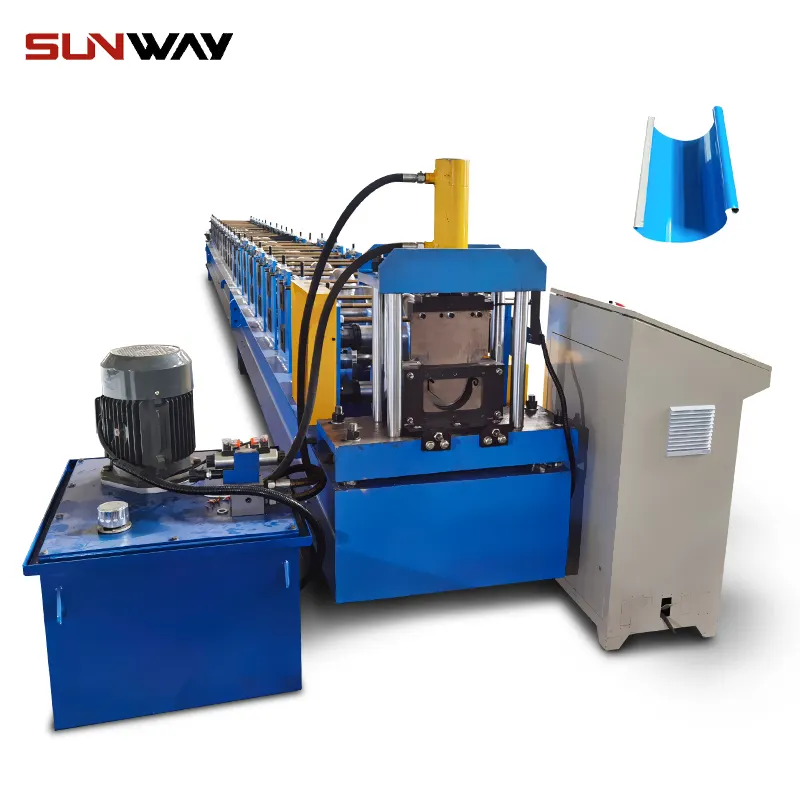
सामान्य प्रश्न
Table 16: Roll forming FAQs
Question | Answer |
---|---|
What thickness of metal can be roll formed? | From thin foils around 0.15 mm up to 16 mm plate can be roll formed |
What shapes can be made by roll forming? | Roll forming can make simple to highly complex profiles with straight sections, curves, twists and varying wall thicknesses |
How long of a part can be roll formed? | There are no length restrictions – systems can produce parts over 150 feet long from coiled stock |
Can roll forming bend metal? | Yes absolutely – roll forming involves continuously bending metal through a series of roller dies |
Is roll forming expensive? | Systems range from compact entry-level units under $10k to high production lines over $100k. With automation, very low cost per part is achievable at high volumes |