Overview
oem ibr roll forming machine is a metal forming process in which sheet metal or strips are passed through consecutive rolls until the desired cross-section profile is achieved. Roll forming machines are used to form metal sheets into custom profiles efficiently and economically.
OEM (Original Equipment Manufacturer) IBR (Insulated Building Rollform) roll forming machines offer customized, high-quality and efficient solutions for roll forming insulated panels for walls, roofs and storage tanks used in industrial and commercial building construction.
This guide provides a comprehensive overview of OEM IBR roll forming technology, working process, types of machines, design considerations, customization options, cost analysis, choosing suppliers, installation, operation and maintenance procedures. Key information is presented in easy-to-understand tables for quick reference.
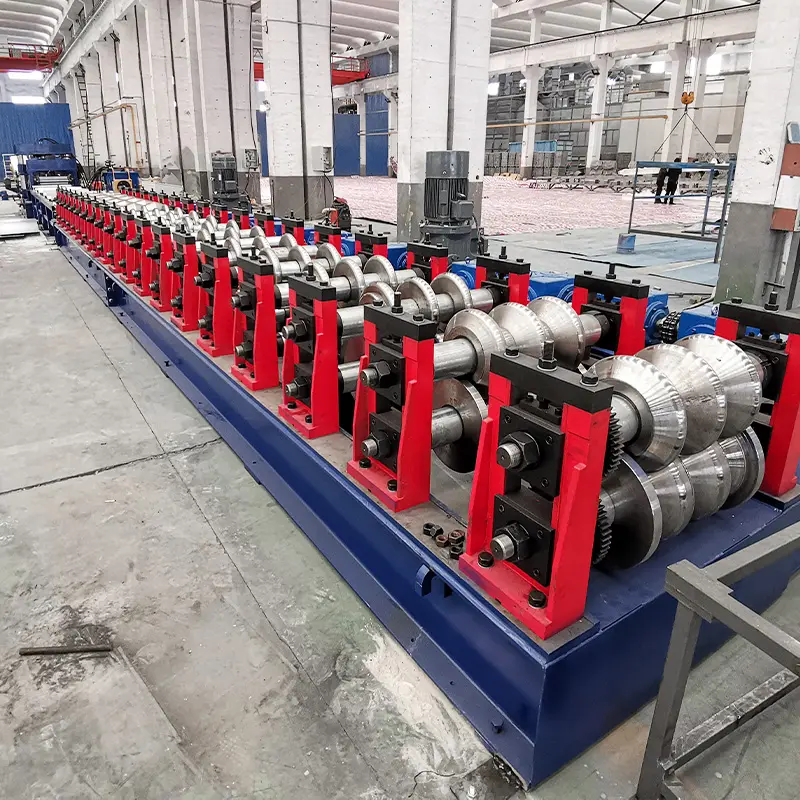
OEM IBR Roll Forming Machine Buying Guide
Types of OEM IBR Roll Forming Machines
Machine Type | Description |
---|---|
Sheet Roll Forming | Roll forms metal sheets into wall panels, roofing panels, storage tank panels |
Tile Roll Forming | Roll forms metal sheets into roofing and wall tiles |
Metal Deck Roll Forming | Roll forms structural decks for mezzanine floors, roofs |
Metal Stud and Track Roll Forming | Forms steel framework of walls |
Special Profile Roll Forming | Forms custom profiles for special architectural shapes |
Working Process
The OEM IBR roll forming working process involves:
- Material Feeding: Coiled metal strips/sheets fed into machine
- Roll Forming: Sheet passes through series of roller dies to gradually shape it
- Design and Profile Cutting: Cut to specified lengths or profile designs
- Output: Formed panels, sheets, profiles exit machine for collection
Key Machine Components
Component | Function |
---|---|
Uncoiler | Holds and feeds raw coil strips |
Feeder | Feeds sheet into rolls |
Roller dies | Gradually forms sheet into profile |
Cutting unit | Trims sheets to length |
PLC Control | Controls speed, processes, etc. |
Hydraulic unit | Provides power for cutting |
Customization and Automation
OEM IBR roll forming allows extensive customization:
- Profile shapes and dimensions
- Metal thickness capacity
- Sheet widths
- Cut lengths
- Inline punching, embossing, notching
- Addition of insulation filling
- Integrated packaging/stacking
- Fully automated operation
Computerized control via PLC allows programming roll sequences, speeds, and splicing to suit customer needs. This enables quick changeovers between profiles.
Design Considerations
Key design factors to provide to OEM supplier:
- Type of building component to manufacture
- Metal type and thickness
- Final profile cross-section dimensions
- Cut length(s)
- Feature requirements – inline operations, automation level, etc.
- Annual production volume
- Available plant space
The OEM engineering team will analyze these details to design an optimized roll forming system including appropriate equipment, layout, and automation level within budget.
-
नालीदार पैनल रोल बनाने की मशीन
-
वाइनयार्ड पोस्ट रोल बनाने की मशीन
-
लाइट गेज स्टील रोल बनाने की मशीन
-
ऑटो आकार बदलने योग्य सिग्मा शहतीर रोल बनाने की मशीन
-
स्टील बॉक्स प्लेट रोल बनाने की मशीन बनाना
-
विद्युत कैबिनेट फ्रेम रोल बनाने की मशीन
-
दीन रेल रोल बनाने की मशीन
-
ओमेगा शहतीर रोल बनाने की मशीन
-
सीजेड शहतीर रोल बनाने की मशीन
Choosing an OEM IBR Roll Forming Machine Supplier
OEM Roll Forming Machine Manufacturers
कंपनी | Location | Contacts |
---|---|---|
AAA Manufacturing Inc. | Michigan, USA | [email protected] Ph: +1 234 456 7890 |
Rainbow Rollforming Equipment Ltd. | Ontario, Canada | [email protected] Ph: +1 345 678 9123 |
Jupiter Machine Tools | Maharashtra, India | [email protected] Ph: +91 22 4950 1235 |
These are leading global manufactures offering customized OEM roll forming solutions. Contact multiple suppliers for system quotes based on requirements before selection.
Key Considerations for Selection
Parameter | विवरण |
---|---|
Technical expertise | Years of roll forming experience, qualified engineering team, expertise with latest 3D modeling software |
Customization capabilities | Ability to customize all machine parameters and automate various secondary processes inline |
Machine quality | Use of high grade components from reputed suppliers, stability and longevity of equipment |
Cost | Competitive pricing in line with capabilities and quality offered |
Lead time | Ability to deliver machine within committed timeframe |
Testing facilities | Availability of simulation software and in-house facilities to test profiles before dispatch |
After sales support | Responsiveness for technical queries, maintenance help, spare part supply |
Referrals | Check feedback from existing customers on product quality, support etc |
Visit supplier factories to view their manufacturing infrastructure, quality control processes, R&D facilities, past roll forming projects, and current production schedules before placing the purchase order.
Cost Analysis
Machine Type | Capacity | Price Range |
---|---|---|
Manual Sheet Roll Former | Up to 10,000 tonnes/year | $100,000 – $250,000 |
Automated Sheet Roll Former | Up to 20,000 tonnes/year | $300,000 – $750,000 |
High-Speed Tile Roll Former | Up to 50,000 tonnes/year | $500,000 – $1,500,000 |
The final system cost depends on:
- Degree of customization to profile
- Automation level
- Production speed/capacity
- Additional secondary processing operations integrated
- Material of construction
- Manpower for operation
Larger OEM enterprises have higher budgets reaching up to $3 million for highly customized, high-capacity and fully automated IBR roll forming lines integrated with punching, filling, and stacking.
Operating costs include maintenance, labor, utilities and material which vary by location, system complexity and output.
Installation, Operation and Maintenance
Installation
- Floor space – Length > width > height
- Foundation – Reinforced concrete or steel structure
- Levelling – Precision alignment for smooth running
- Electrics – Power panels, cables sized for loads
- Utilities – Compressed air, water, lubrication oil
- Safety – Fencing, emergency stop buttons
Operation
- Material coil loading and feeding
- Parameter setting – Speeds, sequences, cut lengths via PLC
- Running machine – Monitor forming and cutting
- Formed component unload and inspection
- Safety procedures to be strictly followed
Maintenance
Activity | Frequency |
---|---|
Inspection | Daily |
Lubrication | Weekly |
Hydraulic oil change | 6 months |
Machine cleaning | Monthly |
Spare part replacement | As needed |
Software upgrades | As needed |
Strict preventive maintenance as per supplier guidelines is vital for maximum machine life and performance. Keep spare part inventory based on criticality.
Advantages of OEM IBR Roll Forming
- Customized profiles – Suit customer design needs
- High productivity – Up to 100 m/minute line speeds
- Consistent quality – Precision formed uniform profiles
- Material savings – No welding, low wastage
- Flexibility – Quick changeovers, multiple profiles
- Cost effective – Saves on labor, energy, material
- टिकाऊ – Long machine life of over 20 years
OEM IBR roll forming lines deliver key benefits of customization, speed and flexibility while maintaining consistent quality and cost efficiency.
Limitations of OEM Roll Forming
- High initial capital investment – For machinery, layout, auxiliary equipment
- Complex design and simulation analysis needed
- Skilled manpower needed for operation and maintenance
- Additional secondary processing increase complexity and cost
- Design restrictions on profile shapes due to bending limits
While automated OEM roll forming systems require sizable initial spending, the long term savings generally justify costs for most manufacturers targeting large volume production.
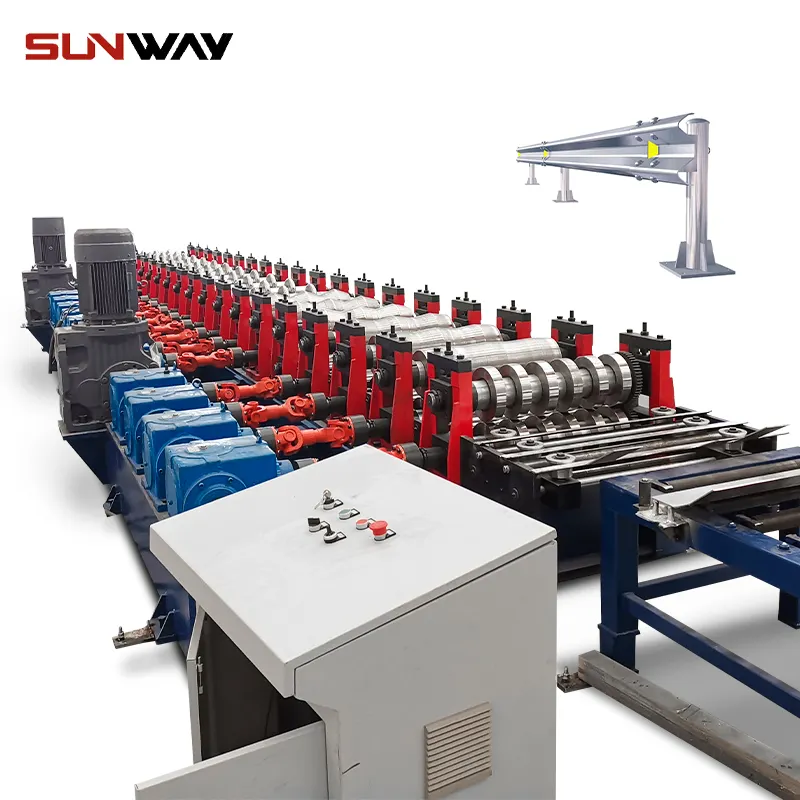
सामान्य प्रश्न
What materials can be roll formed?
Most ductile metals including low carbon steel, stainless steel, aluminium, copper, titanium etc. can be roll formed up to 8 mm thickness. Brittle metals like cast iron cannot be bent without fracturing.
What profile shapes can be formed?
Common shapes like channels, I beams, C sections, Zed sections, hat sections and many more symmetrical profiles are possible. Rule of thumb is minimum 3T bend radius for sheet thickness T. Complex asymmetric shapes may require secondary operations.
How accurate is roll forming?
Advanced roll forming machines with precision roller dies, guides and automated controls can achieve extremely tight tolerances of +/- 0.02 mm on critical dimensions.etable for easy reference.
What causes defects in roll formed parts?
Defects can arise from worn roller dies, unoptimized feed rates, poorly designed profiles exceeding material ductility, coil side damage or oil/dirt accumulation. Periodic maintenance and correctly set process parameters ensure quality profiles.
How to reduce machine downtime?
Preventative maintenance as prescribed, use of high quality consumables and replacement parts, keeping inventory of critical spares, and timely issue resolution by suppliers help maximize production uptime.
निष्कर्ष
OEM IBR roll forming technology offers manufacturers unparalleled flexibility to create building components like panels, decks and frames to exact custom specifications in a highly productive and cost efficient manner.
By partnering with a specialized roll forming machine OEM provider and investing wisely after thorough planning, companies can gain a vital competitive edge with enhanced quality, lower expenses, quicker deliveries and minimal hassles.