Roll forming is a metal working process in which sheet metal is progressively shaped through a series of roller dies until the desired cross-sectional profile is obtained. It is an efficient and cost-effective way to manufacture parts with long profiles and uniform cross-sections.
Roll formed parts are used across industries like auto, rail, infrastructure, appliances, furniture, storage, etc. Common examples include roofing panels, door frames, racking systems, highway signage, electronic enclosures and more.
This article provides a comprehensive guide on roll forming machine parts, working, configuration options, suppliers, prices, pros/cons and tips for selection.
Overview of Roll Forming Process Parts
The main sections of a roll forming machine are:
- Material Handling
- Forming Stations
- Cutoff
- Exit Conveyor
Table 1: Key Sections of a Roll Forming Machine
Section | Components | Function |
---|---|---|
Material Handling | Uncoiler, Feed Table, Entry Guide | Hold coil stock, straighten sheet, feed into machine at constant speed/tension |
Forming Stations | Roller Stands, Rollers, Gears | Progressively cold form sheet metal through series of stands |
Cutoff | Shear, hydraulics | Slice formed profile to desired length |
Exit Conveyor | Belts, motors, supports | Transport finished parts out of the machine |
The forming section is the heart of the machine. It houses a series of roller dies progressions mounted on stands through which the material passes. Each stand incrementally forms the profile closer to the final shape.
The number of stands varies based on part complexity – from as few as 3 stands for simple geometries to over 20 stands for complex parts.
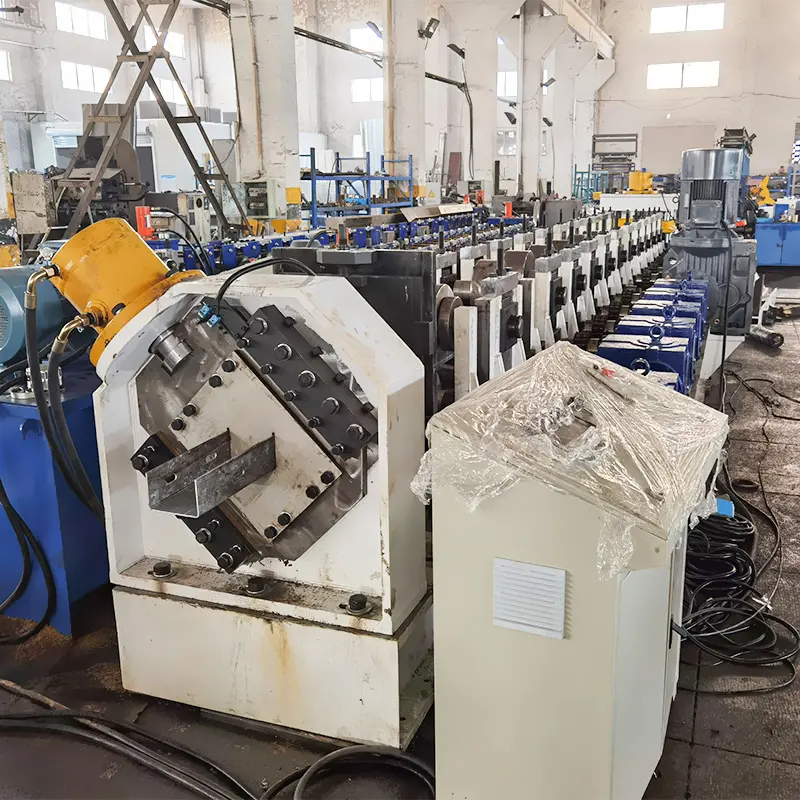
Roll Forming Machine Types
Roll forming machines are available in different configurations based on production needs:
Table 2: Roll Forming Machine Types
Type | Description | Typical Use Cases |
---|---|---|
In-line | Uncoiler is in-line with forming and cutoff sections | High volume long production runs |
Reversable | Sheet reversing mechanism allows return to forming section | Short production runs, requires part flipping |
Portable | Compact design on lockable castors | Small batches, on-site production |
Custom | Tailored to specific custom part geometry | Low volume proprietary profiles |
Working Principle
The working stages in roll forming from flat sheet to finished part are:
Straightening – The unwinding metal strip often has residual stresses and coils set from previous processes. So the first step is to straighten these imperfections using an entry guide and feed rolls.
Feeding – The straightened strip enters the forming section at a constant speed and tension regulated by servo feed rolls.
Progressive Cold Forming – As the material passes through the series of roller die stands, each stand induces more bending until the final cross-section is obtained.
Cutoff – After the profile is fully formed, the cutoff press shears it to the desired finished part length.
Exit – The finished part of transferred onto the exit conveyor for bundling and storage.
Key Aspects of Roll Forming Machine Parts
Material Feeding
The material feeding components handle and prepare the raw coil stock before roll forming:
Table 3: Material Handling System Parts
Part | Function | Types | Factors |
---|---|---|---|
Uncoiler | Hold coil stock, allow unwinding | Decoiler, Hydraulic mandrel, Reel | Coil width, I.D. & O.D |
Feed Table | Support strip end, absorb recoil | Flat/Inclined with rollers | Recoil force |
Entry Guide | Straighten incoming sheet | Pyramid, Roller straightener | Material thickness |
Feed Rolls | Regulate material speed & tension | Knurled, Smooth friction | High friction for thin sheets |
Proper sheet alignment and feeding sets the stage for quality roll formed parts.
-
रोलिंग शटर स्लेट रोल बनाने की मशीन
-
Highway Guardrail End Terminal Forming Machine
-
Highway U/C Post Roll Forming Machine
-
2 Waves Highway Guardrail Roll Forming Machine
-
3 Waves Highway Guardrail Roll Forming Machine
-
वाइनयार्ड पोस्ट रोल बनाने की मशीन
-
ऑटो आकार बदलने योग्य सिग्मा शहतीर रोल बनाने की मशीन
-
ऑटो आकार बदलने योग्य CZ शहतीर रोल बनाने की मशीन
-
ऑटो आकार बदलने योग्य Z शहतीर रोल बनाने की मशीन
Forming Stations
The forming section has the series of stands with roller dies that shape the profile:
Table 4: Forming Section Parts
Component | Role | Design Factors |
---|---|---|
Stands | House roller dies | Overall length dictates # of stands |
Roller Dies | Have machined contours to form shape | Profile complexity, material type |
Shafts | Mount dies for rotation | Length, bearing selection |
Gearing | Drive synchronized die rotation | Type, ratio, lubrication |
Casings | Protect internal parts from dust/debris | Seals, breather valves |
The roller die contour design is optimized through advancedSimulation software for the desired part shape. Precision CNC machining translates this into physical tooling. Proper roller surface finishes ensure low friction bending.
The casing provides a controlled sealed environment for smooth operation. Gear drives connects the shafts to synchronize die rotations with precision tolerances.
Cutoff System
The cutoff press slices the continuously formed profile into set lengths as per the batch requirement:
Table 5: Cutoff System Parts
Part | Description | Control Modes |
---|---|---|
Cutoff Press | Mounted downstream of final stand | Hydraulic, Servo Electric |
Upper/Lower Blades | Slice through material | Carbide inserts for wear resistance |
Scrap Chute | Collect cutoff scraps | Roller conveyor discharge |
Length Control | Regulate slice cycles | On-the-fly, Fixed increment |
Precise blade control and optimal shear angles give superior edge finish and perpendicular cuts. The scrap chute handles remnants efficiently.
Exit Conveyor
Once formed and cut, the finished parts are collected and bundled through exit handling equipment:
Table 6: Exit Conveyor Parts
Part | Function | Types |
---|---|---|
Belt Conveyor | Transport cut parts | Flat belt, Roller bed, Bucket |
Stacking Tables | Align/bundle pieces | Manual, Automated |
Baling Press | Wrap bundles with straps/film | Horizontal, Vertical |
Efficient exit handling ensures finished roll formed parts are moved without damage for storage and shipping.
Roll Forming Machine Accessories
Beyond the main modules, roll formers can be equipped with additional components as per production needs:
- Decoilers – Alternative unwinding systems for coil stock handling
- Loopers – Create slack loops in material flow before cutoff
- Embossing – Coining stations to emboss logos/text
- Punches – Hole punching units for bolt holes etc.
- Ink Markers – Inkjet systems to print date stamps etc.
- Safety Enclosures – Mesh or sheet metal enclosures for safe operation
- Conveyors – Extend part flow handling upstream and downstream
- Sensors – Measurement instrumentation for automation
- IoT Modules – Connectivity hardware for data capture
These accessories enhance capability for secondary operations or monitoring.
Roll Forming Machine Design Factors
Key aspects that drive roll former configuration:
Table 7: Roll Forming Machine Design Factors
Parameter | विवरण | Effect |
---|---|---|
Production Rate | Parts needed per hr/shift | Machine speed, indexing control |
Part Length | Distance between cutoff slices | Machine length, conveyor size |
Material Width | Coil stock strip width | Die lengths, frame width |
Material Type | Steel, aluminum etc. grain orientation | Force calculations, surface finish |
Part Shape | Profile complexity, number of bends | Number of stands, die contours |
Precision Needs | Dimensional and bend tolerance | Roller surface finish, guides |
Secondary Operations | Hole punch, emboss etc. | Additional stations, space |
Automation Level | Manual/auto material feed, stack/bundle | Labor requirement, sensors, handling |
Roll Forming Machine Suppliers
There are many established manufacturers of roll forming equipment across geographies:
Table 8: Roll Forming Machine Brands
ब्रैंड | Location | Typical Models | Price Range |
---|---|---|---|
Dimeco | USA | Helios, TFX Elite | $150,000 – $500,000 |
Formtek | Canada | Orion, Maxima | $100,000 – $800,000 |
Bradbury | USA | EasyForm, SelectRoll | $100,000 – $600,000 |
Gasparini | इटली | FlexyRoll, FastRoll | $200,000 – $1 Million+ |
Samco | भारत | Mach 2, Concept | $50,000 – $250,000 |
Both local and international vendors offer machines across output levels, automation needs and budget. Lead time is ~3-6 months.
Roll Forming Machine Pricing
Cost depends on factors like:
- Production rate
- Overall machine length
- Level of automation
- Additional secondary operation stations
- Software and IoT capabilities
Figure 1: Typical price range for various roll former configurations
- Basic machines start around $100k
- High end automated lines are $500k+
- Custom one-off profile machines can cost $1 Million+
Request detailed quotes from shortlisted suppliers based on specific needs.
Roll Forming Machine Installation
Key aspects of roll former installation:
Table 9: Roll Forming Machine Installation
Activity | विवरण |
---|---|
Site Readiness | Level flat floors for stands, provision power/air utilities |
Lifting & Positioning | Use fork trucks, cranes etc. Safety critical |
Securing | Bolt stands to foundation, true verticals |
Alignment | Precision align roller dies and knife blades |
Trial Runs | Validate feeds, performance before production |
Documentation | Supplier provides manuals for operation, maintenance & safety |
Proper groundwork and precise installation provides a robust foundation for smooth functioning.
Roll Former Operation
Day-to-day operation involves:
Table 10: Roll Forming Machine Operation
Activity | Guidelines |
---|---|
Material Loading | Position coil on mandrel securely |
Jog Mode | Initial slow speed test run |
Parameter Input | Enter batch size details |
Cycle Initiation | Start automatic forming cycle |
Monitoring | Observe process for any issues |
Safety | Follow lockout procedures during maintenance |
The operator mainly loads raw material, enters dimensions and removes finished goods. Automatic modes simplifies the workflow.
Roll Former Maintenance
Regular upkeep activities:
Table 11: Roll Forming Machine Maintenance
Task | Frequency | Tools Needed |
---|---|---|
Inspection | Daily | Flashlight, measuring tools |
Bolt/fastener check | Monthly | Wrenches, torque meter |
Roll/shaft lubrication | 3-6 months | Grease gun, lubricants |
Blade sharpening | As needed | Sharpening tools |
Gearbox oil change | Yearly | Funnel, oil container |
Sensor/wiring check | As needed | Multimeter, circuit tester |
Daily inspections coupled with periodic preventive tasks reduce breakdowns. Maintain fastener torque specs.
Choosing Your Roll Forming Machine Partner
Important considerations when selecting roll forming suppliers:
Table 12: Roll Forming Machine Selection Criteria
Parameter | Guideline |
---|---|
अनुभव | Number of years in business, client testimonials |
Domain Expertise | Understands specifics of your product needs |
Quality & Support | ISO certified, trained service engineers |
Delivery | On-time record, installed base in region |
Technology Use | Leverages simulation, sensors, data analytics |
Customization Skills | Flexibility to tailor for special needs |
Pricing and Value | Price commensurate with performance capability |
Evaluate multiple competent vendors on these aspects before choosing the right system.
Pros and Cons of Roll Forming
Table 13: Roll Forming Process Pros and Cons
Advantages | Limitations |
---|---|
Fast, continuous production | Initial tooling cost investment |
Uniform high quality cross-sections | Complex shapes need multi-pass forming |
Ideal for long straight profiles | Short etch parts not optimal |
Efficient material utilization vs machining | Specialized operators needed |
Low tooling maintenance | Horizontal floor space intensive |
Adaptable automation options | Longer lead time vs other processes |
When used for suitable applications focused on linear profiles, roll forming delivers productivity and quality at economical cost. Understand that it has limitations with short complex bends.
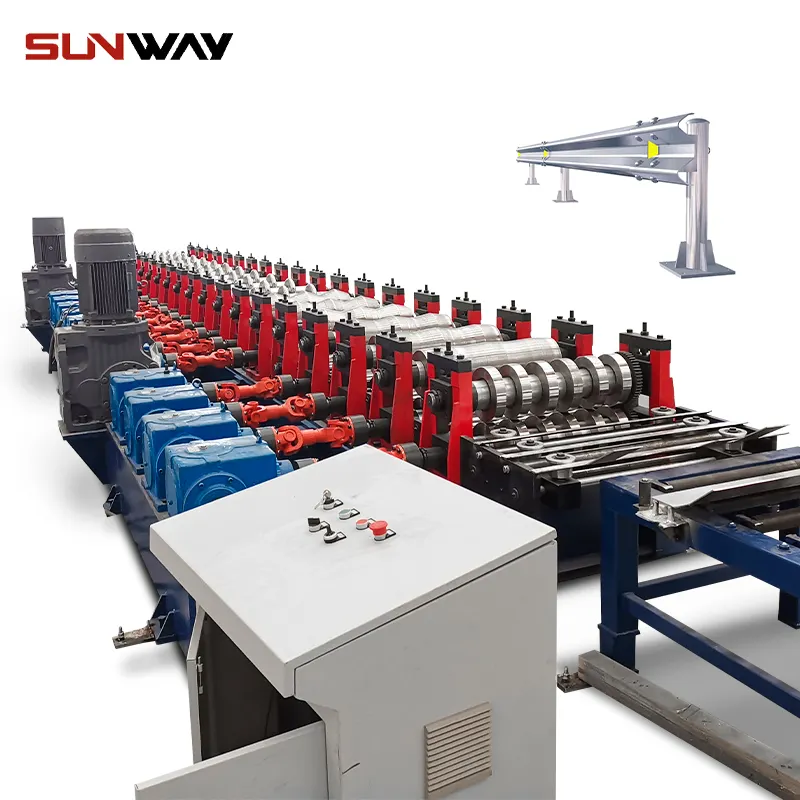
FAQs
Q: What materials can be roll formed?
A: Most ductile materials like low carbon steel, stainless steel, aluminum are commonly roll formed. With proper tooling adjustments high strength steel, copper and even plastic sheets can go through the process.
Q: What tolerances are held in roll forming?
A: Roll formed parts typically achieve profile tolerances of +/- 0.5mm in modern machining. Closer tolerances are possible but reduce productivity. Standard bend radii are around 1 to 1.5 times material thickness.
Q: How to calculate roll forming cost per piece?
A: Total cost = machine depreciation + material coil cost + labor. Calculate per piece rate based on annual production volume. As volumes scale cost goes down significantly.
Q: What safety measures are must in roll forming?
A: Require personnel to wear cut protective gear, gloves when handling coils or sharp profiles. Fully enclose nip points. Interlock guards with electrical power cutoff for entry. Install safety mats.
Q: How to reduce roll formed part rejects?
A: Monitor feeds, speeds and guide adjustments. Ensure precise 90 degree cutoffs. Improve operator training for visual inspection of cuts/bends. Perform regular machine maintenance.
Q: What are the finish options for roll formed products?
A: Common secondary finishing steps include powder coating for corrosion resistance and aesthetics, rubber lined interiors for noise insulation, perforations for air flow and adhesive foam inserts for thermal breaks.
निष्कर्ष
Roll formed sections offer excellent technical and commercial value for long straight profile requirements across a diverse range of applications in infrastructure, buildings, equipment, appliances and more.
When you partner with a dependable roll forming machine supplier and implement proper operational discipline, it results in a flexible, efficient and profitable manufacturing system with low cost of entry.