Wall panel roll forming is a process of progressively bending metal coils into customized panel profiles for walls and roofing. It is an efficient automated method to produce straight or curved panels in high volumes. This article will provide a complete guide on the various types of wall panel roll forming machine factory.
Wall Panel Roll Forming Machine Equipment Guide
There are several types of roll forming machine lines used in wall panel production factories:
Equipment Type | Description |
---|---|
Coil Lines | Uncoil and feed metal coil stock |
Roll Forming Lines | Form coil stock into panel profiles |
Cutting Lines | Cut panels to length |
Hole Punching Lines | Punch fitting holes |
Corner Forming | Bend panels into various angles |
Packaging Lines | Stack and band panels for transport |
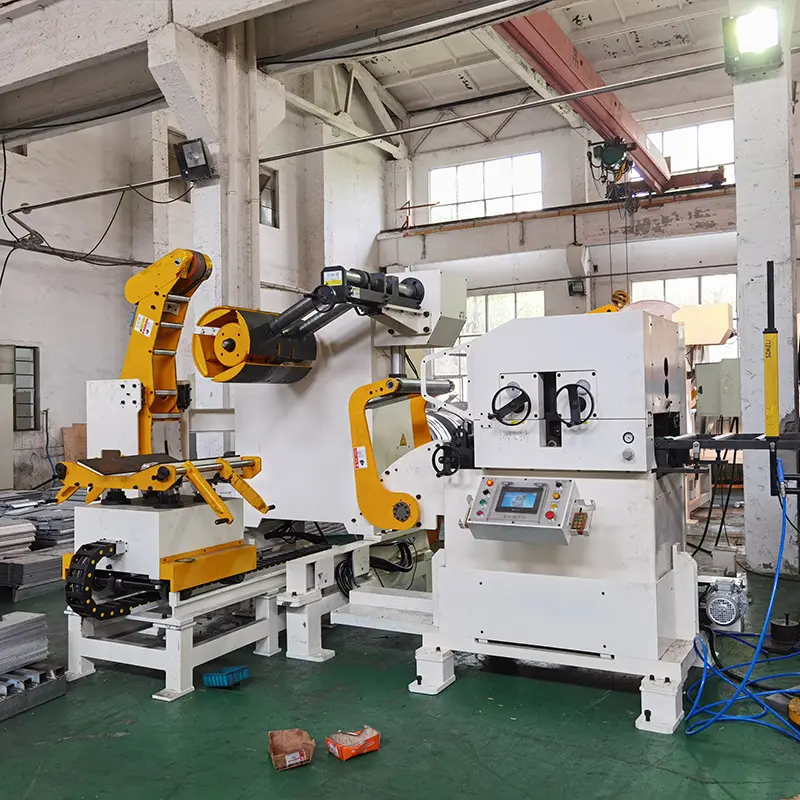
Working Process of a Wall Panel Roll Forming Machine Factory
The wall panel production process involves uncoiling metal sheets, passing them through consecutive roll forming stations to bend them into custom profiles, cutting them to specified lengths, punching fitting holes, making corner forms, and finally packing panels for shipping.
Modern roll forming machine lines are fully automated with precision controls to churn out extremely high volumes of wall panels 24×7. The feeds, speeds, tooling profiles etc. can be quickly changed to switch between different panel dimensions and designs based on specific building project requirements.
Material Feeding
Coils of galvanized steel, aluminum or other metals of widths up to 1500 mm are loaded onto powered decoilers and fed into the roll forming lines. Guiding devices straighten and feed the strips smoothly into the roll tooling stations.
Profile Forming
The pre-stripped metal sheet is progressively bent by consecutive sets of rollers until the desired panel shape is obtained. This gives the flexibility to make multiple complex panel profiles from the same equipment.
Design and Tooling
The roll tooling and dies are precision CNC machined for each custom profile. Guide channels accurately position the metal strip for the rolling heads to make uniform bends. Quick die change designs allow fast profile changes.
Slicing
After forming the panel, rotary cutting blades slice them to specified lengths between 0.3 to 13 meters as per building requirements. The cut panels are ejected onto conveyors.
अनुकूलन
Further custom enhancements like punching fitting holes, putting edge stiffeners, making corner angles can be done by adding modular stations. Special features like embossed patterns, engraved logos can also be integrated.
Packaging
Linear servo conveyors neatly stack the finished panels which are then banded together for shipping to clients. Roller conveyors and forklifts transport these bundles for storage and loading.
Major Suppliers and Models of Wall Panel Roll Forming Equipment
There are a variety of international and domestic roll forming machine manufacturers specializing in automated wall panel production lines:
ब्रैंड | Location | Sample Models |
---|---|---|
Zhongxin | China | RW75-1250 Panel Roll Forming Line |
Freudenberg | Germany | BSL 750 Roll Forming Systems |
Gasparini SpA | इटली | GP Speedroll 76/30 – 1250 TR Wall Panel Machines |
EWMenn Roll Forming | USA | Versa-Dek 7000 Series Roll Formers |
Voestalpine Roll Forming Corp | Austria | ProfilRoll Series for Wall Cladding |
The output capacity ranges from 15,000 to 30,000 square meters of wall panels per day from lines with 5-7 forming heads. The machine widths vary from 750 mm to 1250 mm and maximum strip thickness around 2 mm. Speeds range from 10 to 15 meters per minute.
Pricing Models of Roll Forming Lines for Wall Panels
The average costing scale for fully automated wall panel roll forming machines from international suppliers is:
Output Capacity | Price Range |
---|---|
10,000 m2 per day | $100,000 to $250,000 |
20,000 m2 per day | $250,000 to $500,000 |
30,000 m2 per day | $500,000 to $1 million |
Domestic manufacturers in China offer equipment from $50,000 onwards depending on production scale, level of automation and optional accessories. Buying used lines can further reduce costs.
Installation and Debugging of Roll Forming Equipment
- Civil foundation works are required for machine mounting as per supplier drawings.
- Equipment is shipped in parts for assembly onsite by engineers.
- Hydraulic, electric and pneumatic connections need to be completed before commissioning.
- Trial runs are done and tools adjusted to validate panel quality.
-
Standing Seam Roof Panel Curving Machine
-
बैरल नालीदार रोल बनाने की मशीन
-
Stand Seaming Roof Panel Roll Forming Machine
-
डाउनस्पॉट पाइप रोल बनाने की मशीन
-
गटर रोल बनाने की मशीन
-
Trapezoidal Panel Roll Forming Machine
-
रिज कैप रोल बनाने की मशीन
-
डबल परत पैनल रोल बनाने की मशीन
-
रूफ टाइल पैनल रोल बनाने की मशीन
Operation and Control of Wall Panel Roll Forming Machines
- Operators interface with the HMI touchscreen panel to set up recipes for new panel batches.
- Servo motors and PLCs automatically control feeds, speeds and staging.
- Sensors monitor strip positioning, measure lengths and detect defects.
- Data logging of production metrics helps analyze efficiency.
Maintenance for Reliable Functioning
- Daily cleaning and safety checks ensure smooth working.
- Lubricating moving parts as per manual prevents premature wear.
- Keeping hydraulic systems clear of leaks avoids downtime.
- Prompt replacement of damaged forming rolls reduces scrap rate.
- Periodic calibration tuning maintains profile accuracy.
How to Select a Wall Panel Roll Forming Machine Factory
Choosing a capable machinery factory ensures buyers get advanced production lines tailored to their requirements along with reliable after-sales service. Below are some criteria for evaluation:
Parameter | Description |
---|---|
Scale of Operations | Prefer factories with 50+ installations running reputed clienteles and high production capacities exceeding 20,000 m2 per day. |
Location and Logistics | Ensure the factory has easy access to imported components and can deliver equipment through convenient freight to your nearest seaport/dry port. Local agents should provide installation support. |
Machine Specifications | Catalogs should comprehensively cover output, speeds, power, tooling limits, automation features and certifications. One should physically inspect existing lines. |
Customization Range | Seek factories which offer a wide range of accessories for hole punching, corner forming, special profiles etc. and flexibility for future upgrades. |
Order Handling | Professional factories should provide clear quotation formats, progress timelines, inspection protocols and documentation manuals for the order process. |
R&D and Quality Control | Advanced in-house R&D for designing profiles, control software and tooling shows technical competency. Stringent quality control of outsourced parts is also mandatory. |
Cost Effectiveness | Compare pricing models to identify factories offering the most competitive value considering production scale, automation level, after-sales service etc. |
Past Clientele | Check testimonials and contact references from past clients to verify reliability, responsiveness and technical support of the manufacturing factory. |
Buyers must evaluate factories on all above aspects and not just the cheapest quote price. This ensures you invest in high grade equipment engineered to maximize productivity, product quality and ultimately profits.
Pros and Cons of Fully Automated Wall Panel Roll Forming Factories
Advantages
- 90% faster production compared to semi-automatic lines
- Around 30,000 m2 output capacity per day
- Superior precision and consistency in panel profiles
- Quick product changeover for different configurations
- Higher line availability with advanced diagnostics
- Better monitoring of overall equipment effectiveness
- Safer enclosed working stations minimize accidents
Limitations
- Much higher initial equipment investment
- Debugging complex PLC and data networks
- Dependent on outside power supply stability
- Manufacturer proprietary controllers and spares
- Requires technically skilled staff for troubleshooting
- Difficult system integration with external devices
For most buyers servicing large volume wall panel orders, the productivity and quality benefits outweigh the drawbacks of automation complexity and hardware costs of advanced roll forming factories. Custom programming and local spares sourcing can mitigate proprietary system risks. Backup generator provision guards against power fluctuations.
Applications of Wall Panel Roll Forming Machine Factories
Major building construction segments utilizing automated wall panel roll forming factories include:
Commercial Construction: Shopping malls, warehouses, exhibition centers, retail spaces, institutes, hospitals, hotels, airports, train stations etc.
Infrastructure: Airplane hangers, metro stations, road transit shelters, industrial sheds, cold storage buildings, power plants, stadiums, workshops etc.
Residential: Mass housing projects, apartments, villas, labor camps prefab homes, tiny homes.
Agricultural: Broiler poultry farms, cattle sheds, grain storage silos and other agriculture storage facilities.
Efficient wall panel forming systems are integral to prefabricated structures which are 80% quicker to assemble compared to traditional brick and concrete buildings. Automated factories help scale prefab construction projects.
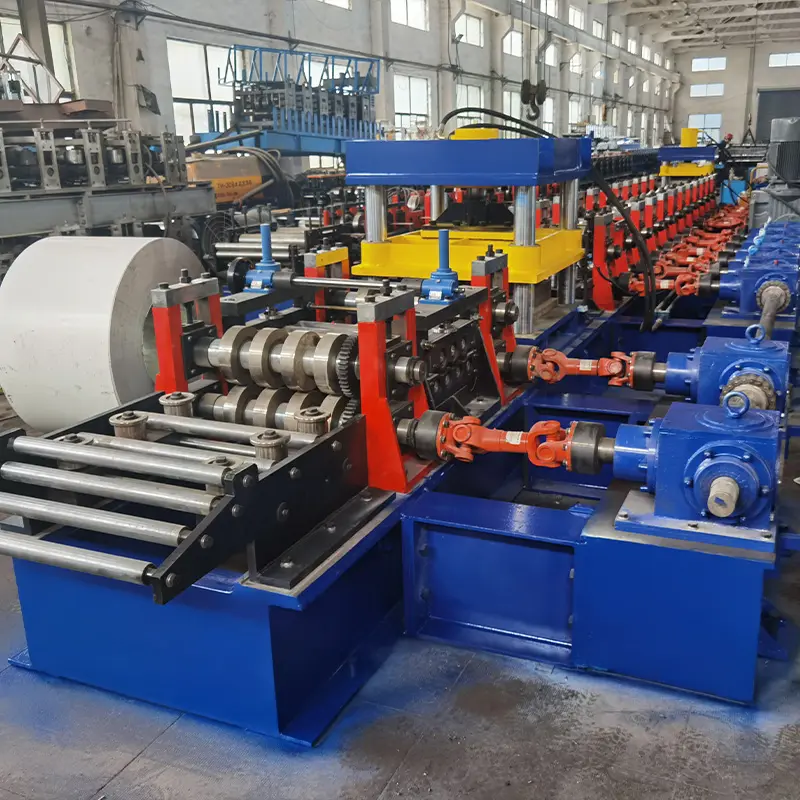
FAQs
Q: What is the cost of setting up an automated 30,000 m2 per day wall panel roll forming factory?
A: The approximate capital investment for land, building, roll forming lines, support equipment and working capital can range from USD $2 million to $5 million based on production scale, land and construction costs in the target region, level of automation etc.
Q: Does the machine factory supply design and installation services overseas?
A: Reputed automated machine factories have global technical partnerships to support overseas equipment supply. Their services include:
- Sheet metal engineering design of custom profiles
- Virtual modeling of profiles
- Roll tooling design and machining
- Equipment logistics to seaport
- Onsite assembly and commissioning
- Trial runs and operator training
Q: What are the regular maintenance requirements and spares parts replacement cycles?
A: An annual facilities maintenance contract with the machine factory helps keep equipment running at peak efficiency. Typical upkeep tasks include:
Component | Replacement Frequency |
---|---|
Forming Rollers | 12-24 months |
Bearings | 24-36 months |
Hydraulic seals | 12-18 months |
Blades | 6 months |
Conveyor chains and gears | 6-12 months |
Having an inventory of recommended spare parts allows minimizing downtime for replacements when issues arise.
Q: What factors affect wall panel quality and accuracy?
A: Key parameters impacting product consistency include:
- Incoming metal coil thickness variations
- Strip feeding precision
- Roll tool concentricity and surface finish
- Profile station alignments
- Calibration of slicing blades
- Control of line speed variations
Advanced lines continuously monitor these variables and make dynamic corrections via servo feed controls and PLCs. Statistical data analytics further optimize the forming parameters.
Q: How much space is required to set up the factory?
A: A 30,000 m2 per day output automated wall panel factory requires ~15,000 ft2 covered space:
- 6,000 ft2 for roll forming production hall
- 4,000 ft2 for inventory and dispatch
- 3,000 ft2 for offices, control room, utilities
- 2,000 ft2 for any future expansion
Ideally the facility design should have high roof clearance, consistent concrete floors, dedicated power supply and adequate circulation space for movement of coil stock and finished product.
निष्कर्ष
Investing in advanced wall panel roll forming machine factories featuring high automation allows construction companies and metal building product manufacturers to gain huge competitive advantages. The versatile equipment lines produce panels of impeccable quality at very low operational costs. Support from international technical partners and domestic installation teams further eases setup of world-class factories. By keeping informed on the latest industry 4.0 trends and implementing advanced analytics, the factories can realize their full profit-making potential through superior productivity and quality.