OEM u channel roll forming machines are used to form u channel metal profiles for construction, racks, frames, and various structural applications. This article provides a comprehensive guide on u channel roll forming machine types, working principles, suppliers, prices, installation, operation, maintenance, and more.
Introduction to U Channel Roll Forming
Roll forming is a continuous bending operation in which sheet or strip metal is gradually formed into a specified cross-sectional shape by passing through consecutive pairs of contoured rolls. U channels are U-shaped profiles with an open section suitable for beams, columns, frames, roofing, racking, and mechanical parts.
OEM u channel roll forming lines transform flat metal coils into finished u channels efficiently on a large production scale. These machines offer high productivity, flexibility, and quality for mass manufacturing u channel frames, racks, structures and components.
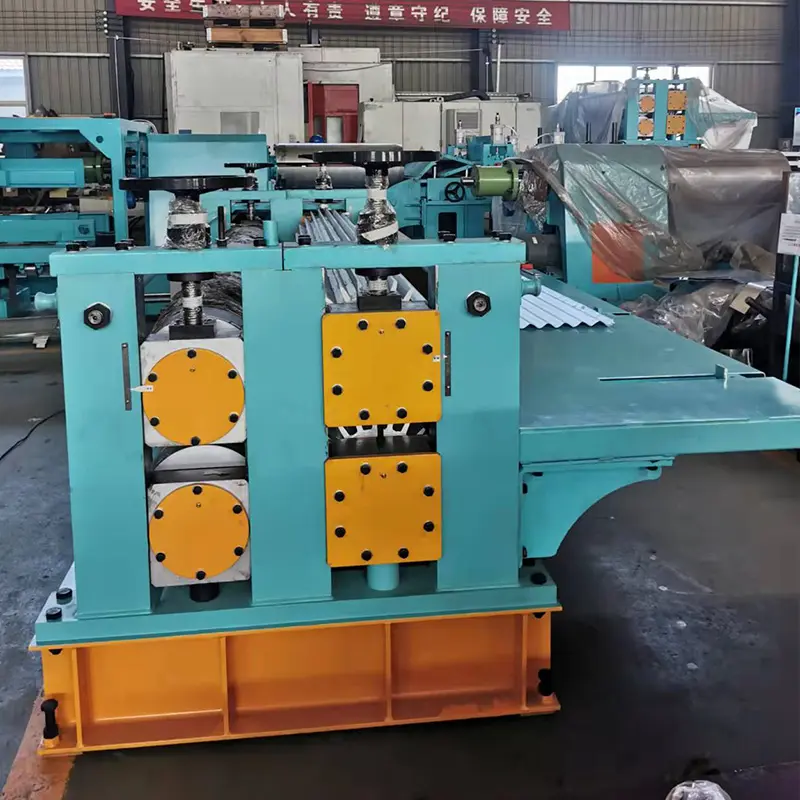
Benefits of U Channel Roll Forming Lines
- Highly productive and efficient forming large volumes
- Consistent and uniform channel dimensions and quality
- Rolls can be changed for different channel sizes
- Low operator labor compared to manual or press braking
- Minimal material waste from sheared blanks or offcuts
- Automated in-line punching, cutting, stacking possible
- Low maintenance and operation costs
OEM U Channel Roll Forming Machine Types
There are several design configurations of u channel roll forming lines:
Machine Type | Description |
---|---|
Basic | Entry-level low cost lines for small scale production |
Standard | Optimized design for most u channel applications |
Heavy-duty | Robust frames and components for large channels |
Customized | Tailored to produce special channel sizes and shapes |
Working Principle of U Channel Roll Formers
The working principle involves gradually forming the channel profile by passing sheet metal strip through several forming stands containing upper and lower rollers.
Feeding: Sheet coils are placed on an unwinding reel and fed into an automatic feeder mechanism that straightens and feeds at constant speed into the roll form mill.
Forming: The strip passes through several forming stands, each with an upper and lower set of wheels. The rollers have machined contours that apply pressure and bend the strip incrementally into the u shape.
Cutting: Finished u channel lengths are cut by rotating circular shearing blades as per specified length.
Supporting operations: Modern lines incorporate punched slots, notching, hole punching, specialized edge cutting prior to cutting lengths.
-
रोलिंग शटर स्लेट रोल बनाने की मशीन
-
Highway Guardrail End Terminal Forming Machine
-
Highway U/C Post Roll Forming Machine
-
2 Waves Highway Guardrail Roll Forming Machine
-
3 Waves Highway Guardrail Roll Forming Machine
-
विद्युत कैबिनेट फ्रेम रोल बनाने की मशीन
-
दीन रेल रोल बनाने की मशीन
-
दो लहरें राजमार्ग रेलिंग मशीन
-
तीन लहरें राजमार्ग रेलिंग मशीन
Choosing OEM U Channel Roll Forming Machine
Consider the following when selecting u channel roll forming equipment:
Parameter | विवरण |
---|---|
Channel sizes | Dimensions (height, width, thickness) should match |
Production rate | Outputs from 10 – 300 meters/minute |
Material type | Mild steel, stainless steel, aluminum etc |
Operating costs | Power consumption, maintenance etc |
Automation features | Coil handling, forming, cutting, stacking |
Durability | Depends on tonnage, frames, overall robustness |
Precision | Tolerances for finished profile dimensions |
Easy operation | Control panel, setup changeover process |
Safety | Emergency stop buttons, guards etc |
Certification | ISO, CE marked electrical components |
अनुकूलन | Abilitiy to make special channels if needed |
Budget | Overall cost considerations |
U Channel Roll Forming Machine Suppliers
There are many international manufactures and OEM suppliers of u channel roll forming equipment with varying price ranges:
Supplier | Location | Price Range |
---|---|---|
SafanDarley | Germany | $100,000 – $150,000 |
Formtek | Taiwan | $30,000 – $120,000 |
Jou Fong | Taiwan | $40,000 – $100,000 |
JinDe Machinery | China | $30,000 – $60,000 |
Jiaxing Xinchang | China | $15,000 – $40,000 |
When sourcing machinery, considerations include production output, features, price ratio, and overall vendor reputation and service.
Installing OEM U Channel Roll Former
Proper installation is vital for optimum equipment performance. Key steps include:
- Civil foundation works
- Positioning and leveling
- Electrical connections to control panel
- Trial runs to set roll gaps, test safety
- Calibration to achieve channel dimensions and tolerances
Vendors usually provide an installation guide manual covering the complete procedure.
Operating U Channel Roll Forming Machines
Operators should follow the standard operating procedures:
- Visual inspection of all parts before startup
- Turn on forward/reverse modes slowly to avoid shocks
- Input recipes on the PLC for automatic coil changing
- Jog to feed strips when changing coils
- Set forming stands gaps as per channel size
- Monitor line speed, coil joiners, blade tolerances
- Conduct test runs and inspection checks
The operator console allows easy adjustment of various settings during production.
Maintenance of OEM U Channel Roll Lines
Regular preventive maintenance is key for longevity and output volumes:
- Oil gearboxes and lubricate bearings weekly
- Check alignments, fasteners, gears monthly
- Replace wearing parts like blades and belts
- Verify hydraulic systems and pumps
- Inspect electrical wiring and controls
- Validate forming stand gaps calibration
- Ensure cleanliness by removing metal scrap and dust
Roll replacement or regrinding may be needed periodically depending on tonnage and operating hours.
Pros and Cons of U Channel Roll Forming
Advantages
- Continuous and efficient high volume production
- Labor cost savings compared to manual methods
- Consistent and uniform channel dimensions
- Ideal for long structural frames, racks, chassis
- Low tooling costs to change profiles
- Compact layout, fast delivery, and installation
Limitations
- High initial capital investment
- Fixed tooling restricts profile shapes
- Limited thickness and width capacity on lower end models
- Precision quality monitoring systems not included in basic versions
Applications of Roll Formed U Channels
U channel profiles are extensively used across industries to manufacture:
- Warehouse storage racks, shelving frames
- Scaffoldings, safety railings
- Electrical cable trays
- Automotive chassis, trailers
- Windows, doors, and facade framing
- Furniture frames and bedsteads
- Agricultural, gym and greenhouse structures
- Mezzanine platform supports
- Wall girts and purlins in metal buildings
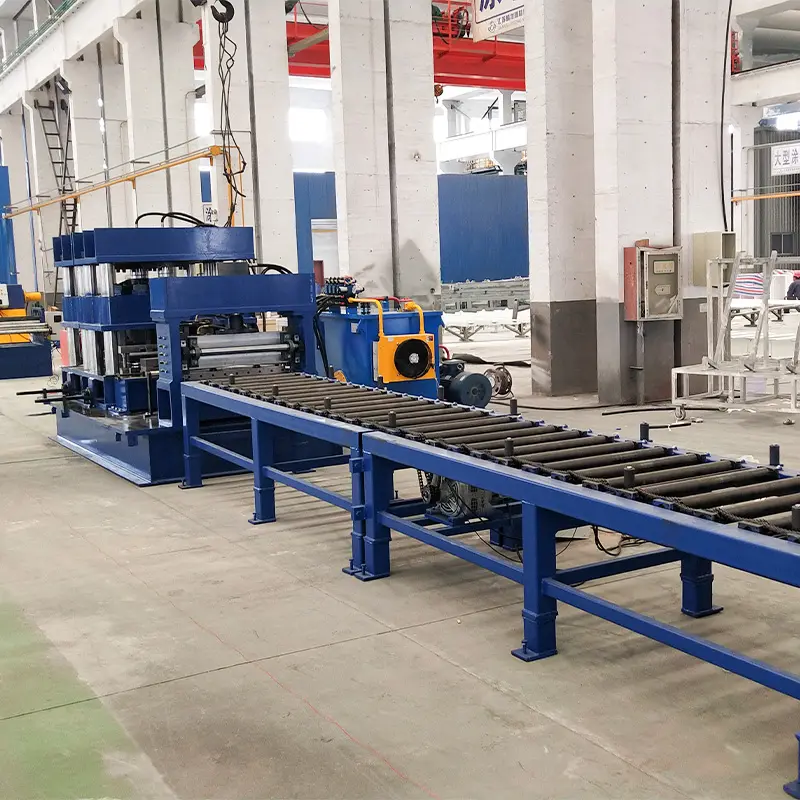
सामान्य प्रश्न
Q: What sheet metal thickness can be roll formed into u channel?
A: Typically 0.5 mm to 3 mm thickness material can be formed by u channel roll forming lines depending on the machine tonnage capacity.
Q: How to customize u channel dimensions?
A: Sections are customized by modifying the roll pass design, roll grinding, and adjusting forming stage positions.
Q: What automation options are available?
A: Automatic coil handling, strip feeding, joining, punching, cutting, stacking, and PLC recipe control for quick size changes.
Q: What factors affect u channel roll forming machine price?
A: Price varies based mainly on production speed, coil width capacity, material thickness range, automation features, and overall robustness.
निष्कर्ष
OEM suppliers offer quality u channel roll formers to produce uniform sections with good dimensional accuracy and finish at high speeds. With knowledge of working principles and design considerations, manufacturers can select optimal roll forming lines to meet their quantity, schedule and budget needs. U channel profiles continue seeing high demand growth across industries given the advantages of modular framing using cold formed structural steel shapes.