oem gutter roll forming machines are used to manufacture rain gutters for buildings in an automated process. This comprehensive guide covers everything you need to know about OEM gutter roll forming equipment.
Overview of OEM Gutter Roll Forming Machines
- Automated forming equipment that shapes metal coil into rain gutter profiles
- High production volumes with speeds up to 35 meters per minute
- Form various gutter shapes – half round, square, rectangle, specialty profiles
- Use galvanized steel, aluminum, copper coils up to 1.5mm thickness
- Offer customization for specific gutter dimensions and configurations
- Supplied by OEMs with integrated components and software controls
- Requires proper installation, operation and maintenance procedures
Main Parameters for Specification
Parameter | Options |
---|---|
Production Speed | 10 – 35 meters per minute |
Metal Thickness | 0.3mm – 1.5mm |
Materials | Galvanized steel, aluminum, copper |
Gutter Types | Half round, square, rectangular, custom |
Gutter Sizes | 80mm to 400mm width |
Machine Size | 8ft to 32ft length |
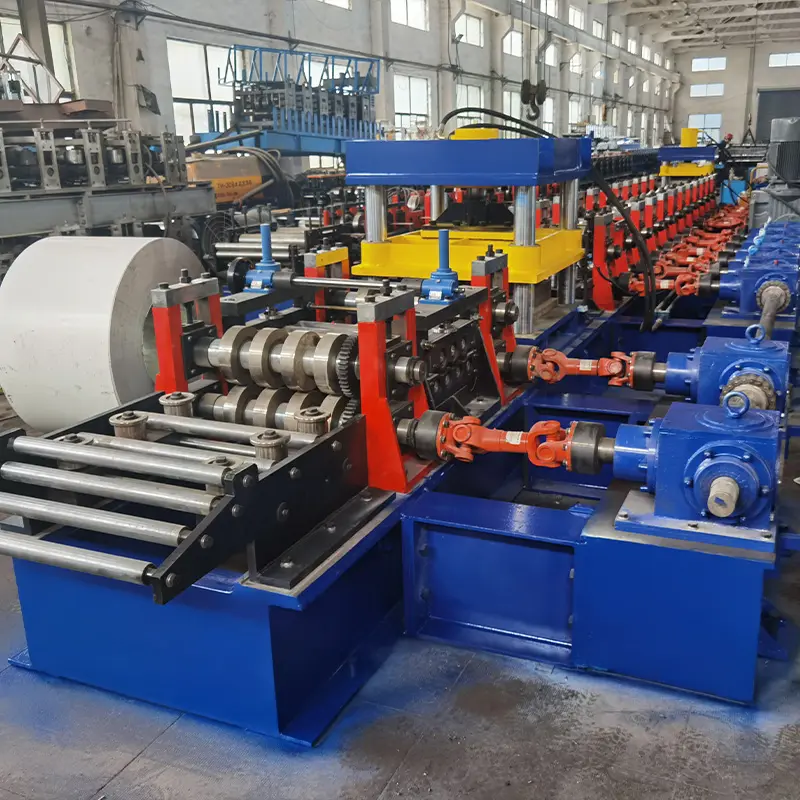
Working Principle of Gutter Roll Forming
Gutter roll forming follows a step-by-step process to convert flat metal coils into shaped rain gutter profiles:
Material Feeding
- Coil payoff reel holds main coil
- powered decoiler feeds metal strip
- guide rollers direct strip through machine
Shaping Stages
- Sheet passes through series of forming rollers
- Each set of rolls bend sheet incrementally
- Rollers arranged to gradually shape gutter profile
- Bottom rollers support forming sheet
- Top rollers apply pressure to bend metal
Calibration and Cutting
- Final forming rollers calibrate shape
- Cutting device slices gutters to length
- Cut to length device sizes gutters
- Conveyors collect finished product
Visual Representation
Below diagram shows key components of a gutter roll former:
The forming process gradually bends and forms the raw coil stock into the final gutter profile using precision machined rollers. The key advantage of roll forming is its continuous production method enabling mass manufacturing of finished metal products.
Types of Gutter Profiles Formed
Common gutter profiles produced on these machines include:
Profile Shape | Description |
---|---|
Half Round Gutters | 180 degree U-shape, popular for durability |
Square Gutters | 90 degree square U, modern appearance |
Rectangular Gutters | Flat bottomed with straight walls |
Custom Profiles | Unique decorative shapes |
Half Round Gutters are the most common due to their strength and sloped bottom that allows drainage. The rounded shape also avoids sharp bends that can accumulate debris.
Square line gutters deliver a contemporary linear look. The right-angled sides complement modern architecture. However debris tends to accumulate in square gutters.
Rectangular gutters feature a flat bottom and vertical walls. They can hold more water volume before overflowing. But debris collects easily unless flushed regularly.
Custom profiles enable specialty decorative gutter shapes and designs to match unique building fronts. These require custom tooling and roll sets.
Key Components of Roll Forming Lines
Gutter roll forming equipment is supplied as complete production lines including:
Coil Payoff: Holds main coil for automated unwinding
Decoiler: Feeds strip through machine at set speed
Guiders: Guide flat strip in straight path
Forming Stations: Contain top and bottom rollers
Punching Units: Cut outs for gutter brackets
Calibration Station: Final sizing of profile
Cutoff Device: Slices gutters to length
Collecting Conveyor: Catches formed product
Electrical Cabinet: Houses PLC controls
Proper specification, integration and tuning of components is critical for peak performance. Reputed OEMs design the entire system to work cohesively.
-
नालीदार पैनल रोल बनाने की मशीन
-
वाइनयार्ड पोस्ट रोल बनाने की मशीन
-
लाइट गेज स्टील रोल बनाने की मशीन
-
ऑटो आकार बदलने योग्य सिग्मा शहतीर रोल बनाने की मशीन
-
ऑटो आकार बदलने योग्य CZ शहतीर रोल बनाने की मशीन
-
ऑटो आकार बदलने योग्य Z शहतीर रोल बनाने की मशीन
-
ऑटो आकार बदलने योग्य घन शहतीर रोल बनाने की मशीन
-
सी सेक्शन ब्रेसिंग ओमेगा स्टोरेज रैक अपराइट पोस्ट रोल बनाने की मशीन
-
स्टील बॉक्स प्लेट रोल बनाने की मशीन बनाना
Working Process Steps Explained
The gutter forming sequence involves discrete steps to convert raw material into finished product:
1. Decoiling
The decoiler mechanism pays out the flat coil strip from the main payoff reel. The feed rate must synchronize to the speed of subsequent stations.
2. Guiding
Guide rollers/discs ensure the strip travels straight before entering the first forming section.
3. Forming
In the roller forming stations, top and bottom rollers apply pressure to gradually bend the steel into shape. Each set incrementally forms the profile.
4. Punching
Punching units cut rectangular slots for mounting gutter brackets. This takes place before the final calibration.
5. Calibrating
The last roller station fine tunes the profile shape to exact dimensions using hardened rollers.
6. Cutoff
The cutoff press shears the formed gutters to specified lengths as they rapidly index through.
7. Collecting
Formed gutters are collected on a conveyor system before bundling and stacking.
Synchronizing the components to operate continuously without stopping enables high production volumes demanded of professional gutter manufacturing.
Raw Material Selection
Choosing the appropriate metal coil material impacts performance factors like strength, weight, corrosion resistance and cost:
Material | विशेषताएँ | Suitable Applications |
---|---|---|
Galvanized Steel | Durable, affordable | Half round profile for residential buildings |
Aluminum | Lightweight, strong | Decorative / commercial gutters |
Copper | Beautiful appearance | Premium decorative gutters |
Galvanized Steel
The optimal balance of durability and low cost makes galvanized steel the top choice. It offers reliable protection against corrosion via zinc coating over the carbon steel. Hot dip galvanized steel works well for half round profiles up to 400mm diameter demanded by most residential structures. It can be powder coated for added protection and visual appeal.
Aluminum
This lightweight non-rusting metal allows for larger gutter sizes without requiring thicker gauge material. The strength resists dents and damage better than galvanized steel. Popular for decorative architectural shapes on commercial buildings and high end homes. More expensive material cost but gutters last longer. Anodizing improves appearance and corrosion resistance.
Copper
Pure copper with its beautiful appearance provides an ornate touch for premium decorative gutters. The natural patina develops a classic weathered look over time. Despite higher cost, copper is in demand for luxury estates, public buildings, churches and museums seeking an opulent distinguished look with a gutter system designed to impress.
Ideally choose a material appropriate for each project depending on performance requirements, life expectancy and budget.
Gutter Roll Forming Machine Manufacturers
Reputable global original equipment manufacturers offer advanced gutter production lines with quality components, software controls, customization services and support:
OEM Roll Former Suppliers | Location |
---|---|
Botou Xianfa Roll Forming Machine Factory | China |
Jindal Pipes Limited | भारत |
Safintra Roofing & Steel Structures | South Africa |
Ernst Metal Roll Forming | Germany |
Astro Metal Craft | Australia |
Shanghai Metal Corporation | China |
These industry leaders engineer fully integrated turnkey solutions for manufacturing metal rain gutter systems. They supply specialized tooling, software and equipment to produce optimal quality and efficiency. Custom-designed production lines available for specialized gutter profiles beyond standard shapes.
China offers cost-effective machinery paired with high quality components and engineering expertise. Advanced German and European equipment focuses on heavy duty durable metalworking equipment for round the clock production cycles. Indian and Asian suppliers offer good balance of technology and competitive budget equipment. Engage a supplier suited for production volumes, quality needs and cost levels appropriate for each gutter fabrication project.
Cost Analysis
Gutter roll forming machine price varies based on:
- Line speed/production output
- Type of material – steel, aluminum, copper
- Gutter dimensions
- Level of automation
- Optional accessories & tooling
- Manufacturer’s brand & experience
Production Volume | Price Range |
---|---|
Up to 30 meters/minute | $8,000 – $15,000 |
30 – 45 meters/minute | $16,000 – $28,000 |
45+ meters/minute | $30,000+ |
Higher automation and speeds increase efficiency at a higher initial investment offset by overall lower part cost. Additional cost for custom tooling packages to form specialty gutter profiles beyond standard shapes. Global OEM suppliers and Chinese manufacturers offer optimum balance of cost and technology.
Installing Gutter Roll Forming Equipment
Site Preparation
- Pour concrete base & anchor machine to withstand vibration
- Ensure sufficient space for safe operation & maintenance access
- Provide sturdy wall or frame for equipment mounting
- Install electrical supply per local codes to power control cabinet
Positioning
- Carefully locate machine using laser alignment tools
- Precision mounting to avoid distortion during operation
- Insert shims underneath to level roll former completely
Connections & Commissioning
- Hook up decoiler unit, exit conveyors, chute tables
- Install cable chains, hydraulics, electrics per diagrams
- Lubricate machine slides, gears, bearings
- Jog machine slowly to confirm component alignment
- Commission per OEM guidelines to launch production
Proper installation by qualified technicians ensures peak functioning, maximizes up time and prevents early wear and tear.
Operating Gutter Roll Forming Machines
Start Up
- Turn main disconnect ON; Start industrial PC
- Check area clear of obstructions
- Ensure mechanisms move freely
- Inch jog machine to confirm readiness
- Select forming program on HMI screen
Running Production
- Position metal coil on decoiler
- Thread strip through rollers and enter guides
- Set feed length/speed rates
- Start cycle to initiate automatic operation
- Monitor forming process as gutters get produced
Temporary Halts
- Press “Feed Hold” button to stop production
- Clear obstructions, correct issues
- Press “Cycle Start” to resume – line re-threads itself
Shutdown
- Press red “Stop” on industrial PC screen
- Power down – turn main disconnect OFF
- Clean equipment; inspect for issues
Follow all safety procedures during the forming process. Wear appropriate PPE while operating or maintaining the machine.
Maintenance of रोल बनाने वाली मशीनें
Regular preventative maintenance enhances performance and uptime on gutter roll forming equipment:
Daily Maintenance
- Clean debris from forming stations
- Check electrical wiring condition
- Confirm guide roller turns freely
- Inspect gears/chains/bearings
- Lubricate moving components
- Check hydraulic fluid levels
Monthly Maintenance
- Inspect machine mounting – re-tighten anchors
- Adjust roll pressure settings
- Confirm coil payoff brake tension
- Validate automation sensor signals
Yearly Maintenance
- Complete machine inspection & tuning
- Replace worn belts/bearings
- Update control software
- Calibrate tooling and mechanisms
- Touch up paint condition
Document all procedures done for quality system compliance. Thorough maintenance keeps the production line in peak shape.
Guide to Selecting Gutter Roll Former OEM
Choosing the ideal gutter roll former supplier for your application requires evaluating several criteria:
Product Quality
- Type of components used
- Frame rigidity and vibration damping
- Software control sophistication
- Finish and tolerances achieved
Customization Ability
- Range of tooling packages offered
- Feasibility of special gutter shapes
- Integration of accessories
Company Profile
- Years in business and experience
- Manufacturing vs trading company
- Installation support services
- Local parts inventory and service
Pricing
- Total investment cost
- Optional accessories included
- Cost of consumables and spare parts
- Payment terms available
Testing and Documentation
- Quality control validation
- Factory acceptance testing
- Manuals provided for operation/maintenance
Selecting an established manufacturer with strong R&D, quality control and customer support provides a strategic long term partnership as requirements evolve over future years.
Pros and Cons of Gutter Roll Forming Process
Advantages
- High production speeds up to 45 meters per minute
- Continuous operation with automated coil feeding
- Consistent quality with precision components
- Lower labor by reducing secondary operations
- Safer enclosed machinery versus manual bending
- Minimal scrap generation during startup
- Quick changeover between gutter profiles
- Compact equipment footprint to conserve factory space
Limitations
- High initial capital investment
- Qualified staff needed to program and operate
- Power consumption for industrial components
- Tooling packages unique to each shape
- Not ideal for low volume intermittent jobs
- After sales service support varies by manufacturer
When weighed for the total cost of ownership, the productivity and quality benefits of roll forming lines outweigh limitations for most professional gutter production facilities.
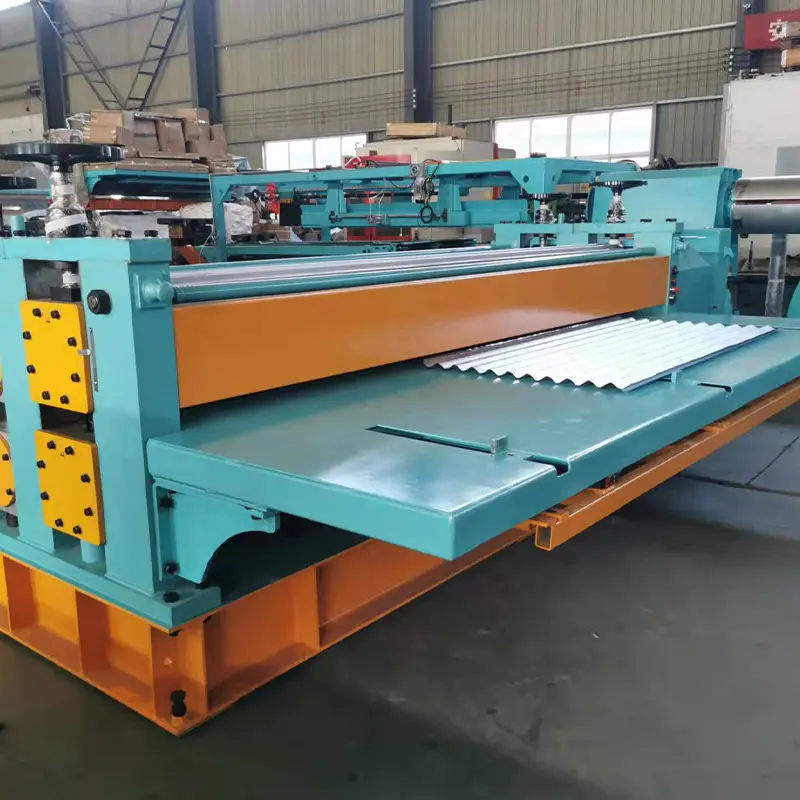
सामान्य प्रश्न
Q: What thickness of metal can be formed?
A: Up to 1.5mm thickness galvanized steel, aluminum or copper coils can be formed by these machines depending on configuration.
Q: Can a single machine make different gutter profiles?
A: Machines with quick change tooling allow alternating between select profiles. Dedicated roll former better for high volume continuous runs.
Q: How to create custom gutters shapes?
A: Custom gutter profiles require custom engineering of top and bottom roll tooling packages. Dimensional drawings needed to design matching roller sets. Additional costs involved.
Q: What defects can occur in formed gutters?
A: Waviness, twisting, flare outs at open hem, thickness variations along length indicate improper roll design, pressure settings or machine tuning issues.
Q: What is the production rate?
A: 10 – 45 meters linear speed per minute depending on machine specifications. Production volumes from 100 up to 500 meters per shift.
Q: What secondary operations may be needed?
A: Downstream punch presses, saws or shears often added for brackets, ends dressing or cutting to final rectangular lengths if the roll former only slices into linear pieces.
Q: What is the ideal plant space needed?
A: Allow 15 – 20 feet length x 10 feet width for the machine plus coil storage and gutter collection area. Height clearance of 12 feet.