snap lock standing seam roll forming machine produces metal panels with raised vertical seams featuring an integrated self-locking sidelap able to interlock adjoining sheets through folded joint geometry without requiring through fasteners or clips.
This overview guide covers working principles, common materials, machine configurations, sizing charts, leading manufacturer selection factors, installation insights, maintenance checkpoints and pricing ranges for snap lock standing seam roll formers.
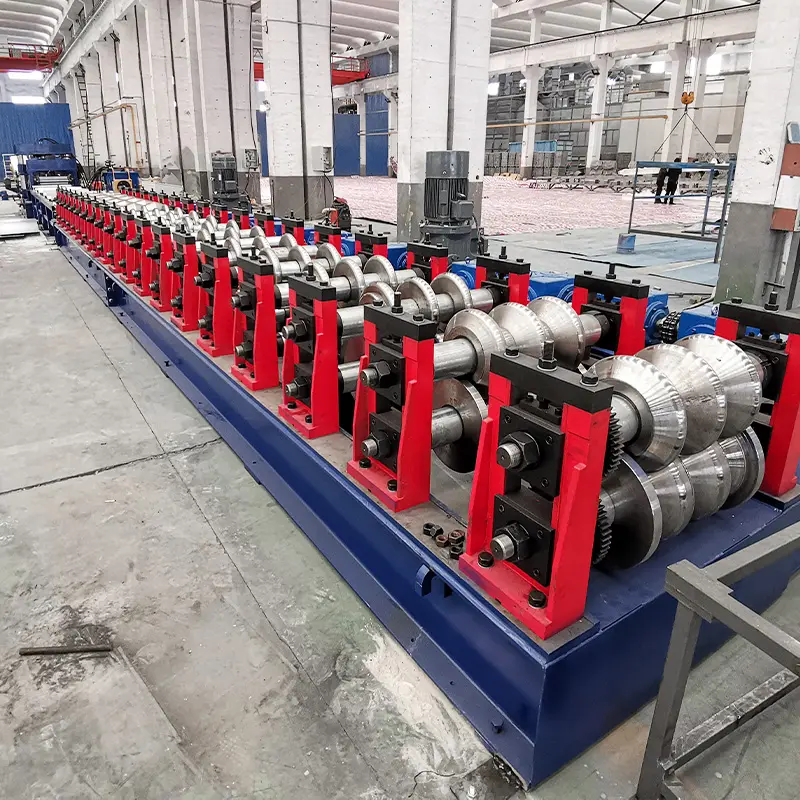
Overview of Snap Lock Standing Seam Roll Forming Machine
In their most basic configuration, snap lock standing seam roll formers take coiled aluminum or galvanized steel stock loaded onto a powered decoiler automatically feeding into sequential rolling mill stands with contouring dies that gradually bend the strip until achieving the desired ribbed sidelap geometry able to self-align and tightly crimp together.
An integrated double seaming section also folds over the leading panel edge protecting from leaks. Finally, a flying shear or rotary shear slices finished panels to specified lengths conveyed out the exit end ready for installation.
Popular Snap Lock Standing Seam Profile Types
Common architectural panel profiles featuring self-locking ribs produced include:
Trapezoidal
Sloped symmetrical angled sidewalls with flat pan drainage channel between upturned parallel ribs. Most popular and versatile machine.
BattenLok®
Folded ribs with multiple contact locking points and drainage flange improving weather sealing. Patented protected profile.
Double-Lock
Special rib geometry with side channel and reversely bent hook providing exceptional uplift resistance once interlocked.
Optional hem forming and corrugating stations offer additional panel profile aesthetics choices.
Key Components of Snap Lock Standing Seam Roll Forming Machine
In their simplest configuration, snap lock standing seam roll formers comprise:
डेकोइलर
Supplies strip coil stock into process flow
Forming Heads
Progressively shape flat sheet into ribbed profile with self-locking geometry
Seaming Section
Folds over leading edge of sheet
Support Frame
Provides housing and supports heads
Shear Station
Trims formed panels square
Conveying Tables
Rolls panels forward for easy offloading
Suitable Materials for Quality Production
Proper coil metal selection ensures final panel consistency across long production runs.
Preferred Snap Lock Roll Forming Metal Properties
Metal | मोटाई | Hardness | Grade |
---|---|---|---|
Aluminum | 0.8mm, 1.0mm | H24, H26 | AA3105, 5005 |
Galvanized Steel | 0.47mm, 0.55mm | DX51D | SGCC |
Zincalume® | 0.47mm, 0.55mm | G2 | Zincal® |
Softer fully annealed temper metals support tight hem seaming without cracking under high roller pressures. Standard coil widths between 1000mm to 1250mm accommodate common sheet cutting methods.
Popular Production Machine Sizes
Common snap lock roll former production widths balance linear speed, output volumes and acceptable coil payloads. Regional standards vary slightly.
Typical Snap Lock Standing Seam Roll Former Models
Machine Width | Output, sheets/hr | Common Uses |
---|---|---|
1000mm – 1250mm | 300 | Residential roofing |
1500mm | 400 | Commercial roofing |
2000mm | 600 | Architectural facades |
Narrower machines facilitate eave detail work while wider lines serve large surface area panel requirements.
-
वाइनयार्ड पोस्ट रोल बनाने की मशीन
-
ऑटो आकार बदलने योग्य सिग्मा शहतीर रोल बनाने की मशीन
-
पीवी माउंटिंग ब्रैकेट सी शेप प्रोफाइल रोल बनाने की मशीन
-
सीजेड शहतीर चैनल कोल्ड रोल बनाने की मशीन पूर्ण ऑटो जस्ती स्टील प्रोफाइल
-
पीवी माउंटिंग ब्रैकेट रोल बनाने की मशीन (एचएटी / ओमेगा प्रोफाइल)
-
पीवी माउंटिंग ब्रैकेट जेड शेप प्रोफाइल रोल बनाने की मशीन
Control System Platforms
While basic machines feature manual control pods, upgraded systems automate operation:
Snap Lock Line Automation Level Matrix
Level | Typical Features |
---|---|
Basic | Fixed Speeds Manual Cutoff Press |
Standard | HMI Touchscreen Powered Punch or Shear |
Advanced | Servo Feed Control Material Tracking |
Smart | Distributed I/O Inline Gauging Diagnostic Analytics |
Consider overall equipment effectiveness (OEE) benefits measuring runtime ratios, production volumes and yield rates helping schedule preventative maintenance.
Best Practices for Care & Operation
Proper machine care techniques sustain production efficiency and prolong service lifetime.
Recommended Operating Procedures
- Inspect panels continuously offloading end for defects
- Ensure appropriate material specifications
- Monitor shear blade condition and punch tonnage decay
- Schedule routine preventative maintenance
- Log hours used and output rates
- Lubricate components like wire feeders
- Keep equipment sheltered from direct weathering/sunlight
- Validate panel correct interlock engagement
Documented procedures, parts lifetime monitoring and established upkeep routines protect reliability.
Manufacturers of Snap Lock Roll Lines
Specialist firms offer customized snap lock standing seam roll former solutions featuring:
Notable Vendor Comparison
कंपनी | Max Line Width | Services |
---|---|---|
Shanghai Rollwell | 2000mm | Technical Support Resources |
Epic Machinery | 1500mm | Custom Guarding |
Formtek | 1500mm | Installation Assistance |
SuperMachines | 2500mm | ProfileEngineering |
Anson Machinery | 2000mm | Operator Training |
Review production line case studies before purchasing. Consider safety innovations, ease of maintenance, and Overall Equipment Effectiveness (OEE) analytics capabilities.
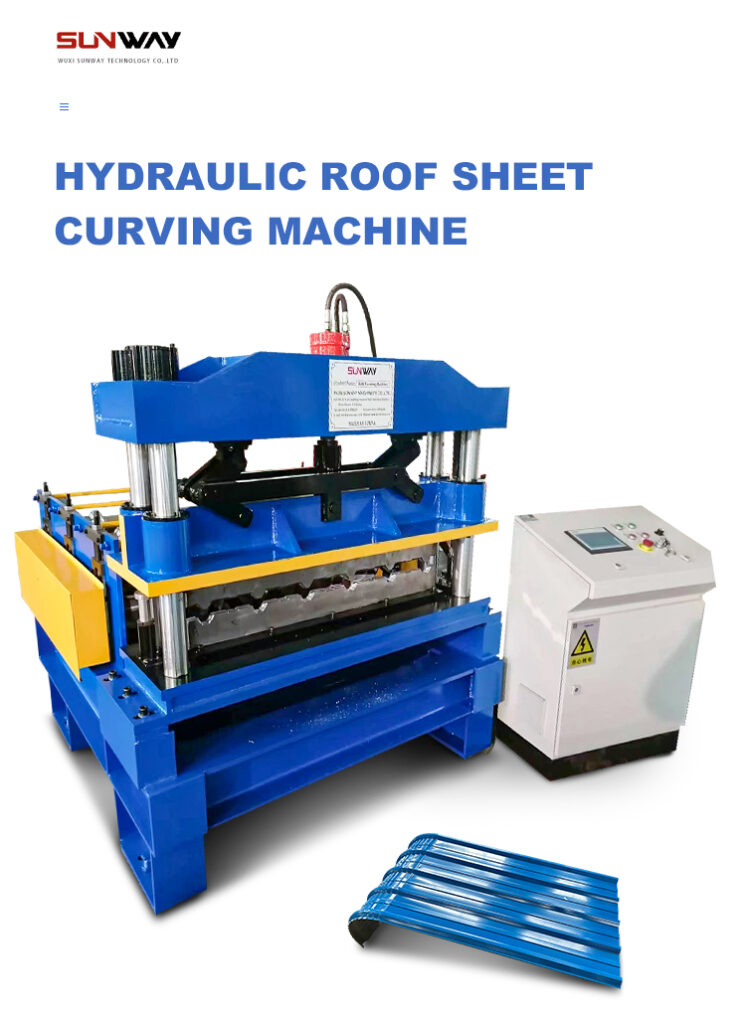
सामान्य प्रश्न
How does self-locking panel rib geometry remain sealed over decades installed?
Proven fold and return techniques coupled with properly specified temper alloy materials avoid issues like relaxation while maintaining consistent interlocking pressures between panels across thousands of joint interfaces.
What level of annual maintenance cost should be expected?
Typical preventative maintenance budgets run 1-2% of the initial equipment capital cost given regular lubrication, adjustments, component replacements and general factory upkeep expenditures. Much less than similar extrusion line investments targeting the same panel niche production output volumes.
When is upgrading antiquated lines justified?
Drivers rationalizing modern snap lock standing seam roll former upgrades encompass meeting substantially higher volume demands from business growth, expanding product width offerings, electrical controls obsolescence issues, mechanical components reliability decay degrading runtime ratios plus worker safety risks from outdated safeguard designs.
What expertise should fabricators offer during equipment selection?
Knowledgeable manufacturers appropriately guide customers on technical considerations covering optimal metal specifications matching anticipated panel sizes, forecasted productivity volumes, equipment layout recommendations and ongoing support availability. This improves selection ecosystem satisfaction converting inquiries into sustainable value added resources.
Are any custom line tweaks possible?
While standardized models fit most regions universally, application requirements do vary needing personalized solutions – especially matching unique architectural appearance preferences or leakage ratings specified by designers on higher tier commercial/industrial snap lock standing seam panel projects warranting customized tooling adjustments.