portable standing seam roll forming machine transform flat metal coil stock into finished standing seam panels featuring vertical ribs protruding upward with angled walls. As compact all-in-one coil processing solutions mounted on trailer frames, key advantages portable standing seam roll formers offer over fixed factory equipment include:
- Transportability – Tow to jobsites near metal roof installation areas
- Reduced Labor – Automates panel production onsite
- Customization – Profile panels to match specs
- Responsiveness – Quickly roll additional sheets as needed
- Convenience – Avoid inventorying preformed metal panels
- Cost Savings – No shipping expenses transferring heavy sheets
This guide covers working principles, recommended materials, common machine specifications, leading manufacturer selection criteria, operation/maintenance best practices plus pricing ranges for portable standing seam roll formers.
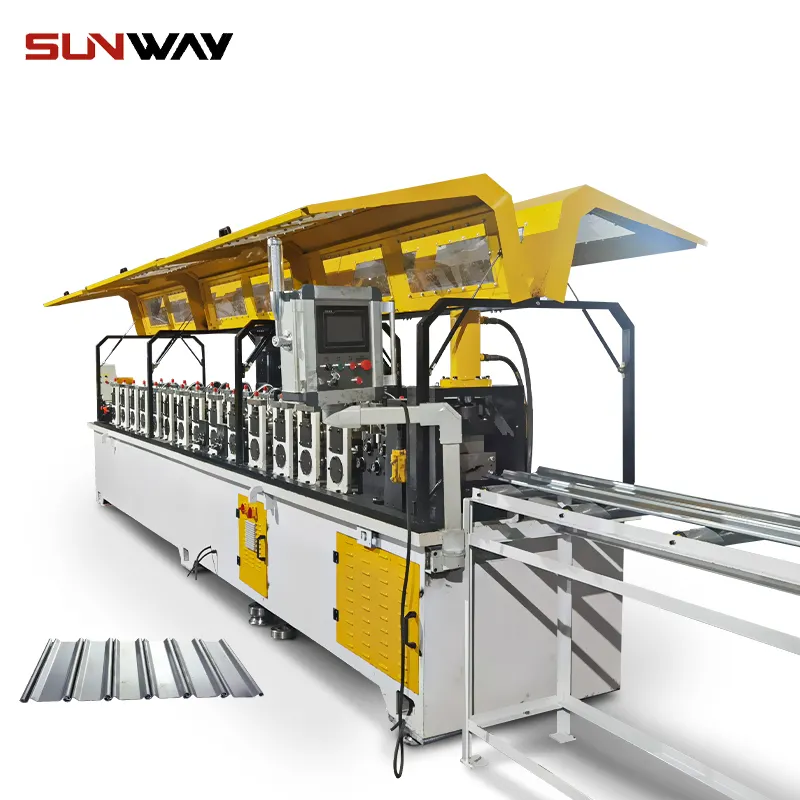
Overview of portable standing seam roll forming machine
In their most basic configuration, portable standing seam roll formers take coiled aluminum or steel stock loaded onto a powered decoiler which automatically feeds into adjacent rolling mill stands incrementally bending the strip. Box rib or trapezoidal profiles with upturned legs form as the material progresses through successive stands until reaching the desired shape. An automated flying shear or rotary shear then slices panels to specified lengths conveyed out the exit end.
Types of Standing Seam Profile Styles
Common architectural panel profiles produced include:
Trapezoidal
Sloped symmetrical angled sidewalls with flat pan between parallel ribs for simplicity. Popular and versatile.
Box Rib
Vertical sides with flat pan and ribs. Increased water drainage capability.
Pencil Rib
More frequent narrower raised ribs. Enhanced spanning reach across framing.
Tree frog
Signature style with central raised rib and descending flanking ribs resembling footprint.
Key Components of portable standing seam roll forming machine
In their simplest configuration, portable standing seam roll formers comprise:
डेकोइलर
Supplies strip coil stock into process flow
Forming Heads
Progressively shape flat sheet into ribbed profile
Forming Frame
Provides housing and supports heads
Shear Station
Trims formed panels square
Conveying Tables
Rolls panels forward for easy offloading
Tow Package
Heavy duty tires, axles, lights allowing highway transport between sites
Suitable Materials for Portable Lines
Quality panel production requires properly specified coil feedstock well matched to a machine’s rolling capabilities and trailer weight limits.
Preferred Metal Properties
Metal | मोटाई | Hardness | ASTM/EN Grade |
---|---|---|---|
Aluminum | 0.6mm – 0.8mm | H14 – H24 | AA3003, 5005 |
Galvanized Steel | 0.4mm – 0.7mm | H26/H28 | SGCC, DX51D |
55% Al-Zn | 0.7mm – 0.8mm | H26/H28 | EN AW-AZ150 |
Softer temper metals reduce cracking risk under the progressive bending forces. Standard coil widths between 700-1300mm accommodate common shears.
Popular Production Sizes
Compact all-inclusive portable machines balance transportation effort against material coil payload and optimal hourly output volumes matching typical standing seam metal roofing project demands.
Common Portable Standing Seam Roll Capability Range
Width | Sheet Thickness | Productivity | Weight |
---|---|---|---|
1000mm | 0.4mm – 0.8mm | 300 m/hr | 4500 kg |
1300mm | 0.4mm – 0.7mm | 400 m/hr | 6000 kg |
1600mm | 0.5mm – 0.7mm | 550 m/hr | 7500 kg |
Narrower widths reaching 900mm facilitate navigating tight access job sites once detached from trucks. Machines require minimal leveling before operation.
Best Practices for Care & Operation
Proper portable roll former care and usage techniques sustain production efficiency and prolong machine service lifetime into decades.
Recommended Operating Procedures
- Inspect assembled trailers before highway transport for cracks
- Torque wheel lugs to specifications
- Clear operation areas of debris interfering with conveyors
- Monitor panel dimensions continuously offloading table
- Ensure square sheet cuts by sharpening shear blades
- Watch for strip feeding issues or cracking
- Replace forming rollers upon any wearing signs
- Avoid coil stock left exposed to moisture
Established preventative maintenance schedules minimize unplanned downtime events, maximize resident expertise by retaining operators and deliver quality standing seam panels boosting overall contractor reputation.
Manufacturers of Portable Standing Seam Lines
Leading international equipment builders offer customized portable roll former solutions from manufacturing facilities across China, Europe and North America featuring:
Notable Vendors
कंपनी | Website | Max Line Width | Services |
---|---|---|---|
Rollformer | rollformer.com | 1600mm | Installation Support |
Goodtek | goodtek.com | 1600mm | Technical Training |
Epic | epicmachinery.net | 1300mm | Custom Guards |
Formtek | formequips.com | 1300mm | Panel Profile Optimization |
Anson | ansonmachinery.com | 1600mm | Relocation Assistance |
Review case studies validating reliability and collect references before purchasing. Consider vendors highlighting safety innovations and analytics integration readiness helping future operations.
सामान्य प्रश्न
What prevents cracking during the bending process?
Properly specified softer temper metal hardness along with machine tooling optimized for targeted thicknesses, widths and minimum coil inner diameter sustains quality double seaming production avoiding cracks under progressive roll forming pressure.
How do operators perform routine maintenance procedures?
Common preventative upkeep tasks production teams complete per established schedules include checking & replenishing lubrication levels on bearings, slides and actuating cylinders based on hourly runtime meter guidelines along with monitoring alignment settings between forming roller stations assuring panels remain within dimensional quality specifications as dies slowly wear rather than assuming tolerances.
What drives long term ownership costs?
Over decades of service lifespan, scheduled reconditioning or replacing wear items like forming rollers, shear blades, conveyor belts based on leading indicators prevents unplanned failures interrupting otherwise sustainable production. Keeping up staff credentials lowers risk premiums. Enabling IIoT connectivity analytics improves preventative response.
When is upgrading equipment warranted?
Justifications to invest in modern portable roll former replacements include substantially increased line width capacity requirements from business growth, tightened quality demands, electrical controls and mechanical components no longer supported for service impairing acceptable runtime ratios due to avoidable downtime or outage risks from deteriorated trailers affecting transport safety assurances and insurer premium cascades.
What buyer qualifications should vendors offer?
Knowledgeable manufacturers able guide customers through technical considerations like optimal metal specifications matching desired rib geometries and production volumes as well as project timeline engagement to steer realistic expectations supplemented by initial setup assistance followed by ongoing troubleshooting support alternatives. This lowers purchase selection regrets helping translate quoted solutions into lasting assets rather than scrap written off later.