Overview
Roll forming is a continuous bending process for producing long metal sections from coiled stock. Ongoing technological advances are bringing new capabilities, efficiency and flexibility to modern roll forming lines.
This guide covers the latest innovations in roll forming machine design, components, control systems, and features. It provides an overview of emerging technologies improving speed, changeovers, automation, quality assurance, and more. Helpful comparison tables summarize the benefits of new technology roll formers versus traditional equipment.
By understanding the available technological improvements, manufacturers can upgrade their roll forming capabilities and remain competitive. Investing in the newest equipment allows producers to boost productivity, reduce costs, meet tighter tolerances, and expand product offerings.
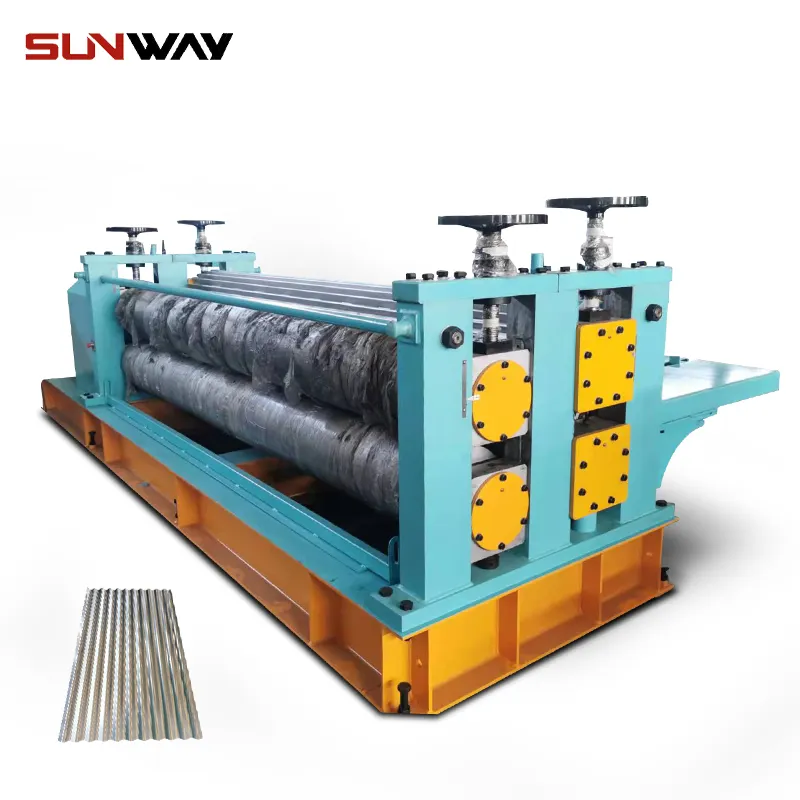
new tech roll forming machine Types
The latest roll forming innovations span inline, orbital, wheel, and other standard machine types:
New Tech Roll Former Machine Configurations
- Servo-driven inline roll formers
- High speed shuttle roll formers
- Precision planetary gear orbital roll formers
- Multi-axis roll forming centers
- Ultra-compact wheel or rotary roll formers
- Continuous embossing roll formers
- Roll forming lines with inline punching or cutting
- Roll-bending integrated machines
- Custom roll formers with quick changeovers
- Integrated roll forming manufacturing cells
New machines retain the fundamental roll forming process while incorporating modern component, control, and automation enhancements.
Enhanced Components
The latest hardware advancements for roll formers include:
new tech roll forming machine Components
- Servo electric actuation on material feed, punches, and forming stands
- Robotic part handling for loading and unloading
- Precision helical gearboxes on orbital machines
- Direct drive servo roll stations
- Linear motor driven forming heads
- Quick changeover roll cassette systems
- Multi-axis programmable bend angle roll stations
- High speed flying cutoff shears
- Laser scanning systems for on-line measurement
- Touchscreen HD operator interfaces
Upgraded components allow expanded capabilities, speed, and flexibility while improving precision and ease of operation.
Advanced Control Systems
New generation control platforms enable smarter roll formers:
Advanced Control Systems for New Tech Roll Formers
- Distributed servo architecture for performance
- PC-based machine control with industrial Ethernet
- Integrated drives, PLC, HMI, and I/O
- Programming in IEC 61131-3 languages (Ladder Logic, etc.)
- Open connectivity using OPC UA, MQTT, etc.
- Real-time closed loop monitoring of forming processes
- Simulation and 3D visualization software
- Databases and cloud connectivity for data logging
- Artificial intelligence for predictive maintenance
- Tablet-based interfaces for mobile monitoring
Sophisticated controls make new equipment highly flexible, efficient, and smart while simplifying interfacing.
Innovative Features
Latest generation roll formers boast advanced capabilities:
New Feature Highlights on Next-Gen Roll Forming Machines
- Quick roll change systems reduce profile changeover times
- Multi-profile tooling allows alternating forms on the fly
- Integrated punching or laser cutting
- Roll stations with NC programmable bend angles
- Part marking and barcode labeling
- Belt wrappers for automatic part banding
- Auto lubrication and preventative maintenance alerts
- Variable speed controls for on-demand throughput
- Touchless laser or optical sensors for measurement
- Wireless connectivity and tele-diagnostics
- Cloud-based data logging, analytics, and OEE monitoring
Optional innovative features customize machines for specialized production needs.
Functional Machine Components
New tech roll formers retain familiar physical elements:
Functional Components of new tech roll forming machine
- Decoiler or coil carousel for efficient material payoff
- Servo feed tables with precision roll stands
- Quick change roll cassette stations
- Programmable bend angle roll clusters
- Flying shears or saws for high speed cutoff
- Part stackers, conveyors, or robots
- Enhanced operator ergonomics and information displays
- Compact footprint and guarding for safety
Latest components build on proven designs for feeding, forming, and finishing formed parts.
Technical Specifications
New generation roll former technical capabilities include:
new tech roll forming machine Specifications
Parameter | Typical Capabilities |
---|---|
Speed | Up to 300 ft/min |
thickness | 20 gauge to 1/2″ plate |
Width | Up to 16 feet |
Accuracy | Profile tolerances to +/- 0.5 mm |
Changeover time | 10 minutes or less |
Controls | Servo modules, PLC, HMI |
Connectivity | OPC UA, MQTT, Ethernet IP |
HMI | 24″ touchscreens |
Data logging | Cloud storage, analytics |
Safety | Guarding, light curtains, e-stops |
Specifications vary based on machine size and configuration selected.
-
लाइट कील वॉल एंगल रोल बनाने की मशीन प्रोटेक्टर कॉर्नर वॉल एंगल बनाने की मशीन
-
लाइट कील कॉर्नर बीड मेकिंग मशीन वी कील एंगल आयरन रोल बनाने की मशीन
-
पूर्ण स्वचालित सीजेड शहतीर मशीन स्टील धातु पूर्व फ्रेम और शहतीर मशीनें
-
पूरी तरह से स्वचालित हाइड्रोलिक आसान ऑपरेशन 80-300 एडजस्टेबल सी शहतीर बनाने की मशीन रोल बनाने की मशीनरी
Leading New Technology Roll Former Manufacturers
Top international suppliers pioneering roll forming equipment innovations:
Suppliers of New Tech Roll Forming Machines
कंपनी | Location | Equipment Focus |
---|---|---|
Formtek | USA | Quick change modular frames |
सैमको मशीनरी | Canada | Custom roll formers |
Shanghai Todaytec | China | Servo orbital and rotary roll formers |
Metform | International | Integrated punching and cutting |
Rolling Specialties | USA | Kitchen cabinet door solutions |
Rinox | Thailand | Container chassis production lines |
Epicor Equipment | Canada | Next-gen portable roll formers |
Many provide turnkey project engineering plus line upgrades and retrofits.
Cost Considerations
Investment costs vary widely based on production needs:
New Technology Roll Former Price Ranges
Machine Type | Price Range |
---|---|
entry-level | $75,000 – $250,000 |
mid-range | $250,000 – $500,000 |
high production | $500,000 – $5,000,000+ |
fully custom | Application dependent |
Quoting considers production rates, line configuration, controls, and overall scope.
Roll Former Line Installation
A proper production environment enables full performance:
Installation Factors for New Technology Roll Formers
- Flat, stable reinforced concrete foundations
- 3-phase high voltage electrical supply
- Compressed air lines and pressure regulators
- Material load/unload handling ability
- Adequate ceiling height and clearance
- Climate control for consistent material properties
- Dust collection and noise abatement
- Control room or office space
- Conformance with safely codes
Work closely with your supplier to prepare the site for ideal working conditions.
Operation and Maintenance
New tech roll formers are designed for ease of use and minimal maintenance:
Operating and Maintaining Next-Generation Roll Forming Machines
- Intuitive touchscreen controls and wizards
- Automatic fault diagnostics
- PM alerts and remote monitoring
- Proactive part replacement based on runtime
- Quick alignment checking and adjustment
- Roller replacement every 4000-6000 hours
- Keep critical spare parts on-site
- Detailed manuals and training tools
- Maintain cleanliness of material path
- Ensure proper lubrication
With proper operation and preventative maintenance, latest generation equipment delivers consistent production and uptime.
Buying Considerations
Key factors when purchasing the newest roll forming technology:
- Annual production volumes by product
- Variety of profiles required
- Level of customization needed
- Available operator skills and maintenance team capabilities
- Total budget constraints
- Expected ROI timeline
- Options to incrementally upgrade capabilities
- Supplier expertise and support infrastructure
- Future extensibility and flexibility prospects
Take a consultative approach with an experienced supplier to define the optimal technical solution balancing production, quality, and costs.
Benefits of New Tech Roll Forming Machines
Advantages of Next-Generation Roll Forming Equipment
- Dramatically faster product changeovers
- Higher throughput with precision tolerance control
- Intuitive controls and information accessibility
- Lower operational costs and less waste
- Real-time production monitoring and analytics
- Knowledge capture from data logging
- Early insight into potential issues
- Easier integration with upstream and downstream operations
- Flexible and modular configurations
- Scalable incremental investment strategies
The latest advancements provide significant benefits but require careful cost-benefit analysis.
Considerations with Adopting New Roll Former Technology
Factors When Upgrading to New Roll Forming Equipment
- Higher initial capital investment required
- Potential for underutilized capabilities
- Retraining operators on new methods required
- Increased complexity of troubleshooting
- Risk of downtime during installation and commissioning
- Existing tooling may not be compatible
- Longer vendor selection and procurement process
- Updated maintenance practices and documentation
- Infrastructure upgrades may add costs
- Resistance to change from some personnel
Any major technology transition requires careful change management.
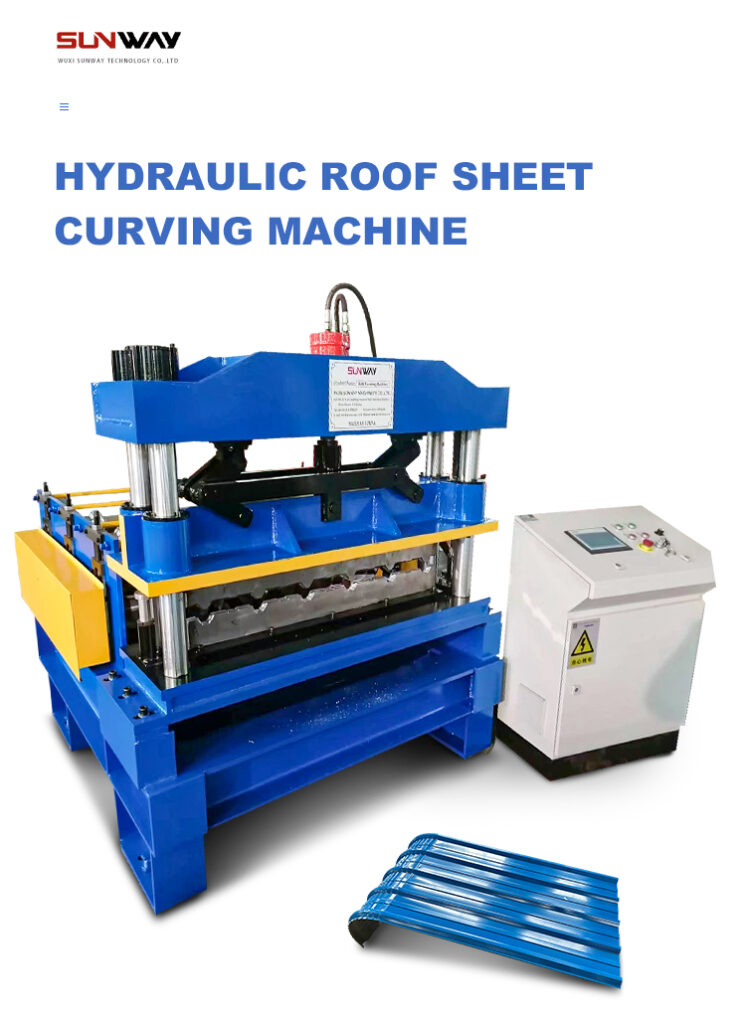
FAQs
How quick are the latest changeovers between profiles?
Quick change tooling allows profile changes in 10 minutes or less on properly engineered lines. Motorized roll cassette systems automate some change processes.
What determines the maximum forming speed?
Main limitations are material thickness, required bend radii, machine length, number of driven stands, and cutoff method. Direct servo drives enable fast and accurate forming.
Can new roll formers make curved or tapered parts?
Yes, CNC programmable bend angle rolls and articulating forming heads allow sophisticated curved, conical, and helical profile forming on the latest generation of machines.
How are next-gen roll formers interconnected?
Modern controls use industrial Ethernet, OPC UA, integrated databases, and wireless connectivity to tie together modules into coordinated lines and optimize data flows.
What types of safety measures are included?
Typical features are emergency stops, operator guarding, light curtains, segmented safety zones, redundant sensors, and mechanical locking of safeguards.
How can cloud data help my operation?
Cloud-based data aggregation provides production statistics, forecasts, OEE, predictive maintenance alerts, and process insights to continuously improve and assist decision making.
निष्कर्ष
The latest roll forming machine advancements provide manufacturers with an expanded toolkit to engineer agile, automated, precision solutions for diverse forming needs. New technology addresses key industry demands like faster changeovers, increased productivity, improved quality and operator experience. With expert guidance, manufacturers can capitalize on new innovations, avoid potential pitfalls, and craft a strategic equipment roadmap to upgrade capabilities over time.