Overview of Double Stage Roof Sheet Roll Forming
Double Stage Roof Sheet Roll Forming are designed to produce long lengths of metal roofing sheets and panels with ribbed or corrugated profiles in a high speed, continuous process.
Unlike single stage roll forming where all stands are in one line, double stage machines have forming stations split between an upper and lower level to create the male and female features on sheet metal roofing profiles. The two forming stages allow more complex shapes to be produced versus single stage roll formers.
This guide will cover:
- Roofing sheet profiles produced
- Double stage roll forming advantages
- Process overview
- Machine configurations
- Forming steps
- Specifications and rates
- Tooling
- Profile design considerations
- Raw material requirements
- Roller adjustment factors
- Cost analysis
- Top manufacturers
- Pros vs cons of double stage machines
- Latest technological developments
Overview of Roll Formed Roofing Sheet Profiles
Typical roofing profiles produced on double stage roll forming lines include:
- Corrugated sheets – Sinusoidal wave pattern, versatile and strong
- 5V crimp panels – Hemmed “V” shaped ribs at regular intervals
- Standing seam sheets – Vertical ribs with raised seams
- Trapezoidal sheets – Angled webs with flat flanges
- Double lock panels – Interlocking male and female ribs
These profiles provide structural strength, spanning ability, weather resistance, and visual appeal for roofing. Popular materials are galvanized, galvalume, and pre-painted steel coils.
Advantages of Double Stage Roll Forming
Double stage roll forming allows:
- Complex profiles – Interlocking and articulated shapes
- High strength panels – Deeper male/female ribs
- Thicker material – Up to 1.2 mm steel formed
- Down-stage access – Simplifies roll maintenance
- Independent control – Separate top and bottom parameters
- Higher rigidity – Increased spanning capacity
- Roll space efficiency – Compact layout in two levels
The split two stage configuration provides more control versus single stage machines for quality and flexibility.
Overview of the Roll Forming Process
Roll forming uses a series of rolling dies to gradually shape flat sheet metal strip into desired profiles:
- Coil sheet feeds through an uncoiler into the roll former
- Bottom stage rollers pre-bend the material
- Sheet transfers to the upper stage for final shaping
- Rotating dies bend the strip incrementally at each stand
- Formed roofing sheet exits for cutoff and collection
- Process is continuous at high production speeds
Rollers controllably bend the metal across its width without any material thickness change or scrap loss. Continuous forming enables high volumes efficiently.
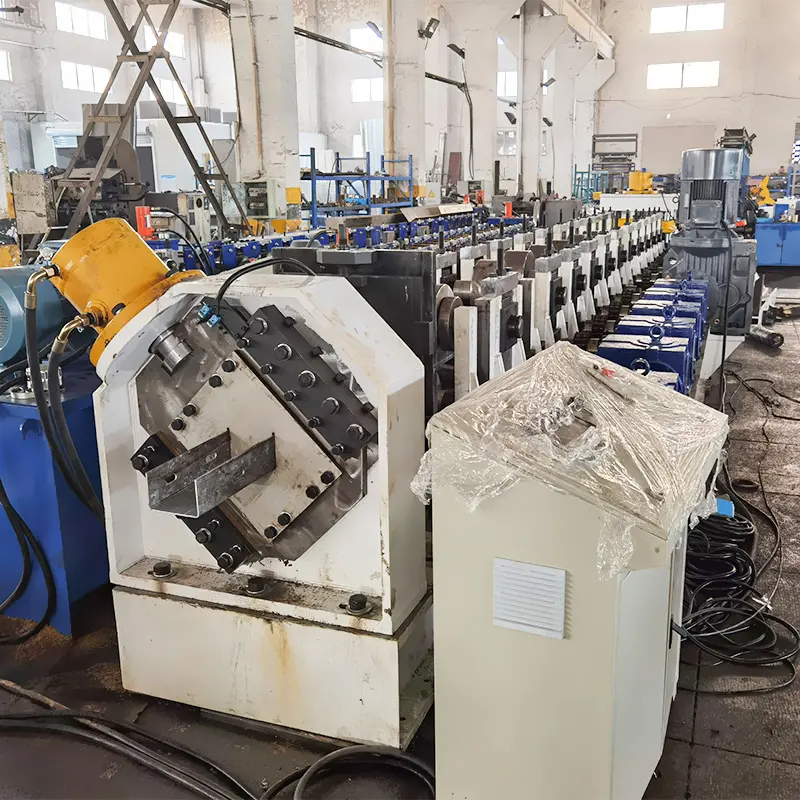
Double Stage Roll Former Configurations
Double stage roll forming lines have two main layouts:
Type | Description |
---|---|
Vertical inline | Bottom and top rolls in straight vertical line |
Side by side | Upper and lower stages side-by-side |
Machine Components
- Coil payoff reel and uncoiler
- Feed table with precision guides
- Bottom and top forming roll stations
- Hydraulic shearing cutoff press
- PLC control console for parameter settings
- Conveyors or support tables
Larger lines often incorporate automatic stackers, counters, and bundling systems.
Overview of the Double Stage Forming Process
A typical double stage roll former shapes sheet metal through these steps:
- Decoiling – Sheet coil is unwound and entered into the roll line
- Leveling – Sheets are leveled and straightened before forming
- Bottom stage – Pre-bending done on bottom roll stations
- Top stage – Final bending and profiling on top stations
- Cutting – Hydraulic end shears cut sheets to length
- Counting – Pieces are automatically counted when cut
- Stacking – Formed sheets placed on exit conveyor or tables
Servo-powered rollers allow real-time speed and position adjustments for precision forming.
Machine Specifications
Parameter | Range |
---|---|
Forming speed | 10 – 40 m/min |
Drive power | 7.5 – 15 kW |
Sheet width | 900 – 1300 mm |
Metal thickness | 0.35 – 1.2 mm |
Profile height | 20 – 150 mm |
Coil weight | Up to 6 metric tons |
Roller diameter | 120 – 220 mm |
More powerful 15 kW+ drives enable faster production speeds. Wider coil widths up to 1300 mm can be run.
Tooling Used in Double Stage Roll Forming
- Forming rollers – Machined forged steel, induction hardened
- Backing rolls – Provide counterforce support
- Guide rolls – Align strip through line
- Cutoff press – Hardened steel shear blades
- Quick change – Modular tooling for fast changeovers
Roll materials with 700-900 HV hardness prevent wear and deformation. Textured surfaces grip metal sheets.
Roofing Profile Design Considerations
Key design factors include:
- Performance needs – Span rating, weather tightness, wind/snow loads
- Applicable standards – Roofing grade, dimensions, testing specs
- Mechanical properties – Strength, bending stiffness, buckling resistance
- Metal sheet parameters – Thickness, yield strength, coatings
- Manufacturability – Ability to incrementally bend into shape
- Visual appearance – Aesthetics, pattern sizing and continuity
3D modeling and FEA helps validate roofing profile designs prior to roll tooling.
Raw Material Used in Roof Sheet Production
Typical metal coil inputs:
- Steels – Hot dip galvanized, galvalume, pre-painted
- मोटाई – 0.35 to 1.2 mm
- Width – Up to 1300 mm
- Coatings – Zinc, aluminum-zinc, painted finishes
- Mechanical properties – Tensile and yield strength
- Surface – Smooth matte with minimal imperfections
- Flatness – Maximum 5 mm over 1.5 m strip length
High quality input coil is vital for uniform roll formed roofing production and corrosion resistance.
Quality Factors in Roof Panel Forming
Key process parameters controlling quality:
- Roll adjustment – Incorrect gaps lead to wrinkles and defects
- Feed rate – Excessive speeds increase risk of tearing
- Strip support – Insufficient support causes sheet sagging
- Roll parallelism – Minimizes thickness variations in profiles
- Lubrication – Prevents abrasion between contact points
- Roll wear – Causes dimensional and quality deviations
- Strip alignment – Prevents skewing and distortion issues
Real-time monitoring and automated feedback minimizes defects and downtime.
Production Rate Analysis
Parameter | Typical Rates |
---|---|
Line speed | 10 – 40 m/min |
Output | 400 – 1600 m/hr |
Pieces per shift | 160 – 640 sheets |
- Narrower widths under 1 meter enable max speeds
- Deeper profile heights slow down forming rate
- Larger ribbed panels have lower linear output
Automated stackers can bundle 1000+ sheets per hour.
Cost Analysis vs Other Methods
Process | Equipment Cost | Material Efficiency | Labor | Cost per Piece |
---|---|---|---|---|
रोल बनाना | $$$ | 90-95% | Low | $ |
Press brake forming | $$ | 50-70% | High | $$ |
Assembly | $ | 80-90% | High | $$ |
Despite higher initial investment, roll forming enables faster production with less material waste compared to alternate processes.
Leading Manufacturers of Double Stage Machines
कंपनी | Location |
---|---|
AIMIL | भारत |
BMW | China |
Gasparini | इटली |
Metform | USA |
Pedersen | Denmark |
Rotoform | Hungary |
Shreeji | भारत |
These firms offer integrated lines from the coil payoff through to profile cutoff and stacking stages.
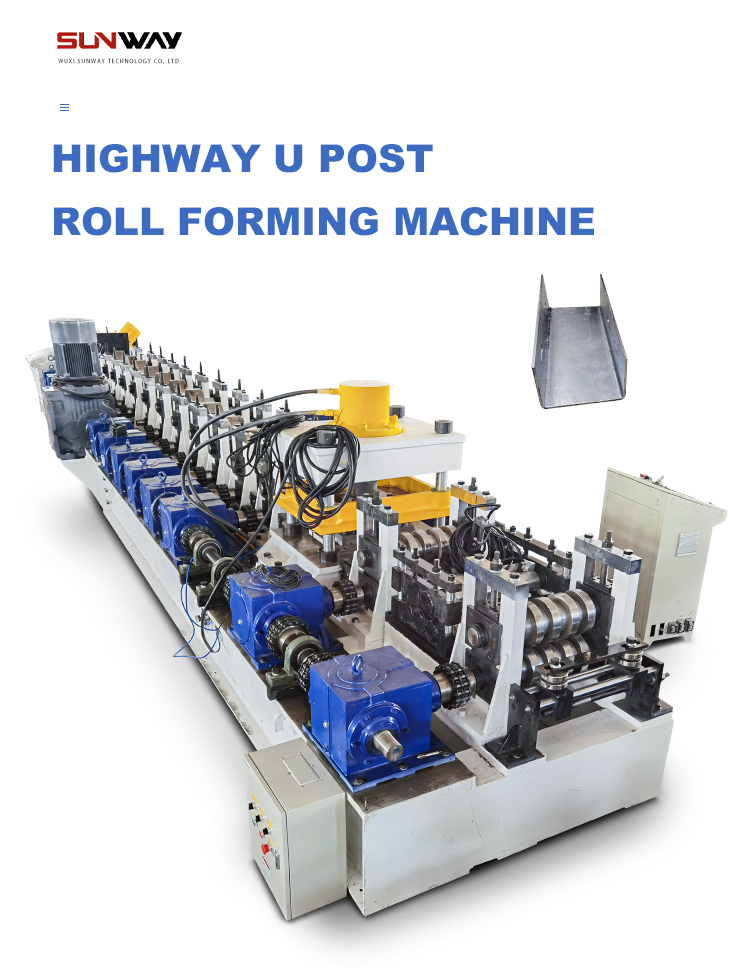
Benefits of Double Stage Roll Forming
- Continuous high speed production up to 40 m/min
- Allows complex interlocking roofing profiles
- Up to 95% material yield compared to stamping
- Consistent quality and repeatable tolerance
- Ideal for long high volume production runs
- Automated process reduces labor
- Safer enclosed equipment versus open machines
- Range of sizes from compact to heavy duty
- Minimal tooling maintenance required
The split two stage arrangement provides advantages over single stage roll forming machines.
Limitations of Double Stage Roll Formers
- Higher initial capital investment
- Not practical for short or low volume production
- Limited flexibility once tools are set for a profile
- Size constraints within machine dimensions
- Additional finishing steps required after forming
- Specialized skill needed to tune roll alignments
- Lead times required for tooling design and machining
- Can experience oil canning panel distortion
- Difficulty holding very tight tolerances
For sheet metal roofing needs under 1000 meters, alternate methods may be better suited.
Latest Advancements in Double Stage Technology
- Quick change tooling – Reduces downtime for profile changeovers
- In-line punching – Pierces registration holes during forming
- Vision systems – In-process optical inspection for defects
- Roll scanning – Detects roller alignment/gap issues
- Safety upgrades – Additional guarding, e-stop circuits
- Handling automation – Reduces manual sheet stacking
- Servo drive upgrades – Improves speed and position control
- Roll design software – Simulates forming process digitally
These innovations aim to further boost quality, flexibility, and productivity for roll formed roofing production.
निष्कर्ष
Double stage roll forming provides an efficient continuous process for high speed production of metal roofing profiles, enabling complex interlocking seam designs. When engineered properly and supplied with quality coil input, the machines can produce ribbed and corrugated panels with excellent consistency and durability to meet architectural specifications.
While requiring greater initial capital expenditure than alternate methods, the fast run rates, minimal material waste, and automated nature of double stage roll forming make it an optimal technology for long production runs where thousands of roofing sheets are required.
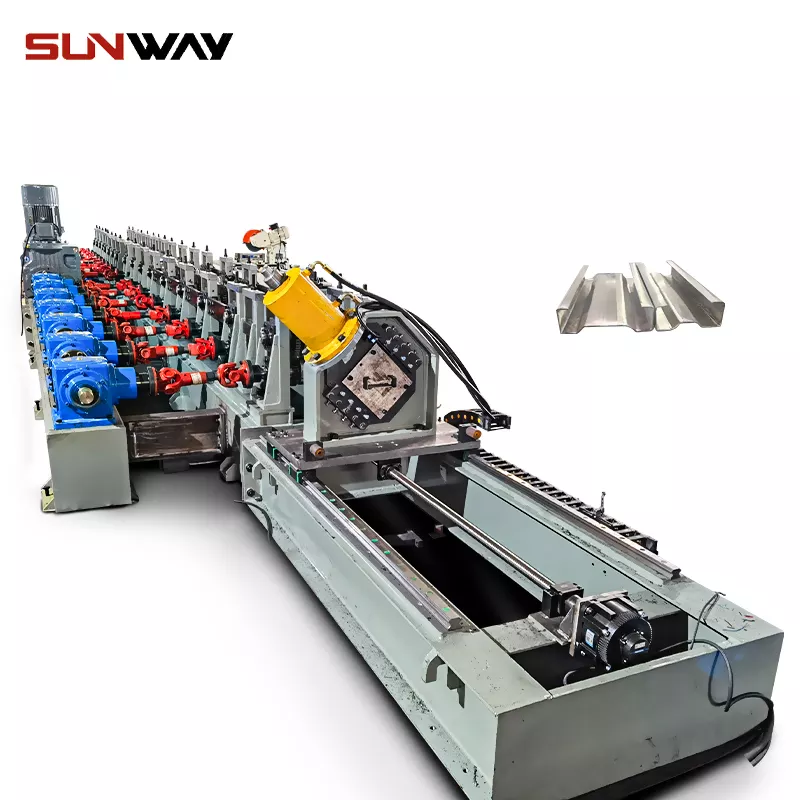
FAQs
Here are answers to some frequently asked questions:
What are the main advantages of double stage roll forming?
The ability to produce interlocking and complex profiles, thicker material capability, independent control, and down-stage accessibility are its major advantages.
What sheet metal thickness can be double stage roll formed?
Standard machines accommodate metal thicknesses from 0.35 up to 1.2 mm. Beyond 1.2 mm becomes more challenging.
What roofing profiles can be produced on double stage lines?
Common profiles include corrugated, 5V crimp, standing seam, trapezoidal, and double lock panels.
How short can the sheets be that are double stage roll formed?
While not optimal, sheet lengths as short as 3 meters can be produced but may be prone to edge tearing.
What tolerances are possible on double stage roll formed roof panels?
+/- 1.0 mm is standard tolerance but advanced machines with precision rolls and guides can achieve +/- 0.5 mm accuracy.
How long does it take to change over profile tooling on double stage lines?
With quick change modular tooling, typical changeover times range from 2-5 hours between different roof sheet profiles.
What quantities make double stage roll forming economical?
Due to higher initial costs, production volumes over 500,000 meters/year are generally required to justify investing in double stage lines.
What skills are required to safely operate double stage roll forming equipment?
Mechanical aptitude, electrical and controls knowledge, troubleshooting ability, and specific machine training are required.