Tile roll forming machines are essential equipment for tile manufacturers. This guide provides a detailed overview of tile roll forming machine types, characteristics, applications, specifications, suppliers, installation, operation, maintenance, and more.
Overview of Tile Roll Forming Machines
Tile roll forming machines take flat metal coils and form them into profiles for roofing tiles, wall tiles, and floor tiles. The roll forming process involves gradually bending the strip material through a series of rollers until the desired cross-sectional shape is achieved.
Key benefits of tile roll forming machines:
- Highly efficient continuous production of tile profiles
- Capable of high output with speeds up to 35 m/min
- Repeatability and precision in forming tile shapes
- Flexibility to switch between different tile profiles
- Lower tooling costs compared to other forming methods
- Minimal material waste
Roll formed tiles have excellent strength and durability while being lightweight and easy to install. Tile roll forming technology enables efficient mass production of quality metal tiles.
Types of Tile Roll Forming Machines
There are two main types of tile roll forming machines:
Type | Description |
---|---|
C and Z Tile Roll Forming Machines | Have C-shaped or Z-shaped forming stands with horizontal incoming and outgoing tile paths. Allow forming more complex and deeper profiles. |
U and O Tile Roll Forming Machines | Have U-shaped or O-shaped stands with vertical incoming and outgoing tile paths, taking up less floor space. Best for simpler, shallower profiles. |
In addition, there are reversible and non-reversible machines:
- Reversible machines can produce tile profiles with patterns on both sides.
- Non-reversible machines can only form patterns on one side.
Main Components of Tile Roll Forming Machine
The key components of a tile roll forming machine include:
- Decoiler: Feeds metal coil strip into the roll forming section
- Guiding system: Guides strip through machine and evens coil tension
- Roll forming stands: Progressively bend strip through series of stands
- Cutting device: Cuts formed tile profiles to length
- Counting device: Counts cut tiles
- Hydraulic system: Applies even pressure to forming rollers
- Control panel: Controls machine parameters and production
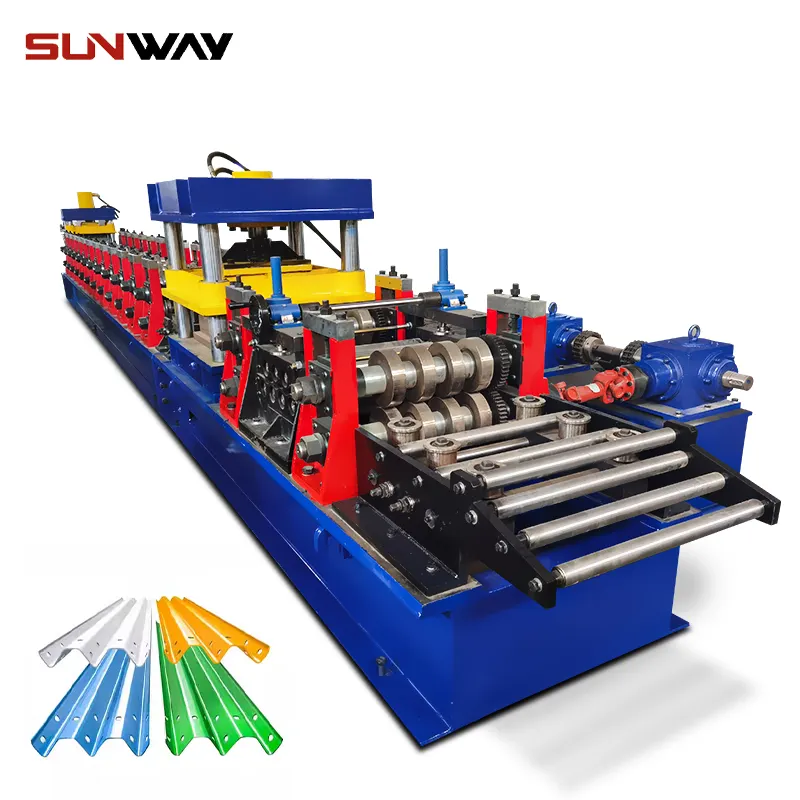
Applications and Uses of Tile Roll Forming Machines
Tile roll forming machines are widely used by tile manufacturers to produce different types of profiled tiles out of metal coils:
Roofing Tiles
- Corrugated roofing sheets
- Trapezoidal roof panels
- Standing seam roof panels
- Interlocking roof shingles
- Metal roof tiles replicating clay or concrete roof tiles
Wall Tiles
- Decorative exterior wall panels
- Metal siding profiles
- Perforated decorative tiles
- Interlocking wall shingles
Floor Tiles
- Interlocking floor tiles
- Anti-slip floor tiles
- Grating and checker plate tiles
Specifications and Design of Tile Roll Forming Machines
Key specifications and design parameters for tile roll forming machines include:
Parameter | Typical Values |
---|---|
बनाने की गति | 10 – 35 m/min |
Max Coil Width | 1015 mm |
Min Coil Thickness | 0.15 mm |
Max Coil Thickness | 1.5 mm |
Formed Tile Height | 8 – 150 mm |
Length Tolerance | ± 1 mm |
Hydraulic Power | 5.5 – 30 kW |
Machine Weight | 2000 – 6000 kg |
- Number of forming stands is based on profile depth and complexity
- Distance between stands impacts profile accuracy
- Roll diameters, shapes, and materials determine quality of formed tiles
- Larger machines used for higher volumes, smaller ones for special profiles
Tile roll forming machines are designed according to applicable standards and buyer specifications. ISO, ASTM, EN standards cover materials, dimensions, testing, safety, etc.
Suppliers of Tile Roll Forming Machines
There are many manufacturers supplying tile roll forming machines worldwide. Here are some of the major suppliers:
Supplier | Location | Machines | Price Range |
---|---|---|---|
Zhongtuo Roll Forming Machinery | China | C & Z machines up to 35 m/min | $8,000 – $60,000 |
T&H Lemont | इटली | High-speed C machines up to 75 m/min | $100,000 – $250,000 |
Formtek | USA | O and U machines for wall/floor tiles | $50,000 – $150,000 |
Kinhill Engineers | भारत | Smaller reversible machines up to 15 m/min | $15,000 – $50,000 |
SSE Enterprise | Thailand | Compact machines for 30-50 mm tiles | $5,000 – $15,000 |
Pricing varies based on speed, size, automation features, and customization. Chinese manufacturers offer cost-effective machines while European/US suppliers provide high-speed/high-precision equipment.
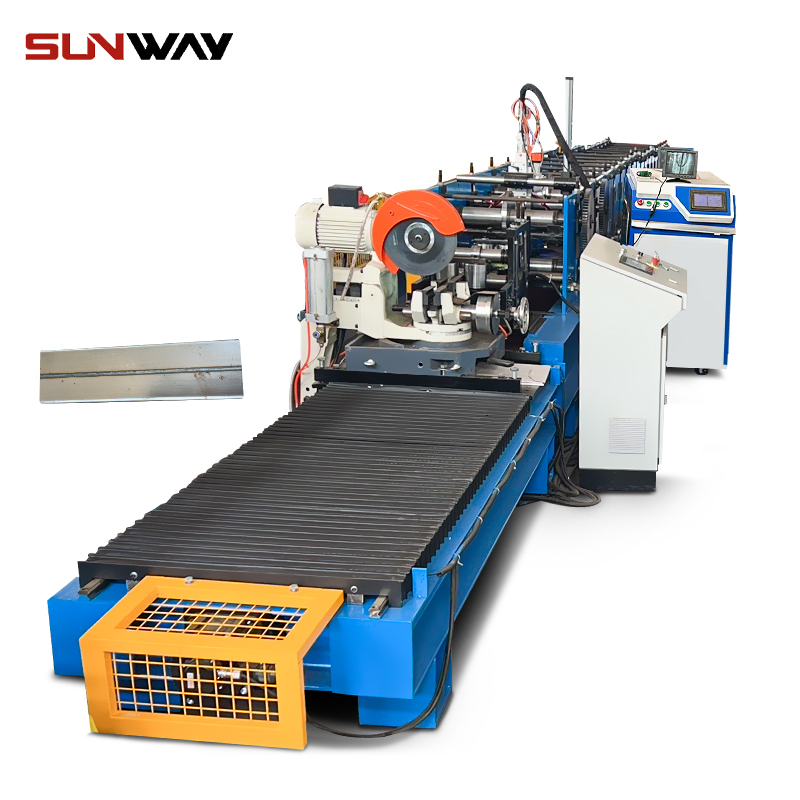
Installation and Setup of Tile Roll Forming Machines
Proper installation is key for tile roll forming machines to function accurately and efficiently:
- Strong level concrete foundations needed to prevent vibration
- Machine anchoring according to manufacturer instructions
- Enough space around for safe operation and maintenance access
- Power supply connections as per electrical load requirements
- Decoiler unit should be mounted on raised platform for proper coil alignment
- Trial runs with plastic/paper to check formed profiles before using coils
Ideally a test run or inspection by supplier representatives is done before full production. Proper machine setup and calibration prevents defects in roll formed tiles.
Operation and Maintenance of Tile Roll Forming Machines
To achieve smooth operation and long machine life, some key operation and maintenance best practices for tile roll forming machines include:
Operation
- Select tooling for desired profile and install properly according to roller layout
- Ensure machine settings are calibrated and work safely up to max rated speed
- Monitor strip feed, pre-punch if needed for difficult alloys/tempers
- Use coils of recommended alloys and thicknesses
- Control line speed based on coil quality to prevent jamming
- Apply lubricants properly on formed tiles without contaminating them
- Inspect finished tiles periodically for defects
Maintenance
- Clean machine regularly to prevent accumulated dirt/metal dust
- Lubricate bearings, gears, chains as per schedule
- Check hydraulic oil levels and top up when needed
- Monitor wear on forming rollers and change when damaged
- Check strip guides for bends/wear and replace if not straight
- Retighten any loose fasteners on stands or connections
- Repair or replace damaged/worn components like cutoff dies
How to Choose a Tile Roll Forming Machine Supplier
When selecting a tile roll forming machine, here are key considerations for choosing the right supplier:
- Type and specs of machine matching required capacity and tile profiles
- Reliable after-sales service for maintenance and troubleshooting
- Quick turnaround on spare parts and consumables
- Responsiveness to requests for machine upgrades or additions
- Flexibility for modifications and customization
- Reasonable pricing for base machine and additional tooling
- Supplier track record, reviews, and reputation
- Local representation if sourcing from foreign manufacturers
- Warranties and guarantees on machine performance
Visiting a supplier’s manufacturing facility provides helpful insights on their production quality and capabilities.
Comparison of Tile Roll Forming Machines
Machine Type | Advantages | Limitations |
---|---|---|
C & Z Tile Machines | – Deeper profile forms<br>- Higher outputs<br>- Reversible option | – Larger footprint<br>- Higher cost |
U & O Tile Machines | – Compact design <br>- Lower cost | – Limited to simpler profiles<br>- Lower speeds |
Reversible Machines | – Forms patterns on both sides | – Lower speeds<br>- Higher maintenance |
Non-reversible Machines | – Higher speeds<br>- Lower operating costs | – Single sided patterns only |
C & Z vs. U & O: C and Z roll machines are better suited for complex tile profiles while U and O work for simpler, shallow profiles.
Reversible vs. Non-reversible: Reversible machines allow patterning on both sides but have lower speeds and higher maintenance needs compared to non-reversible machines.
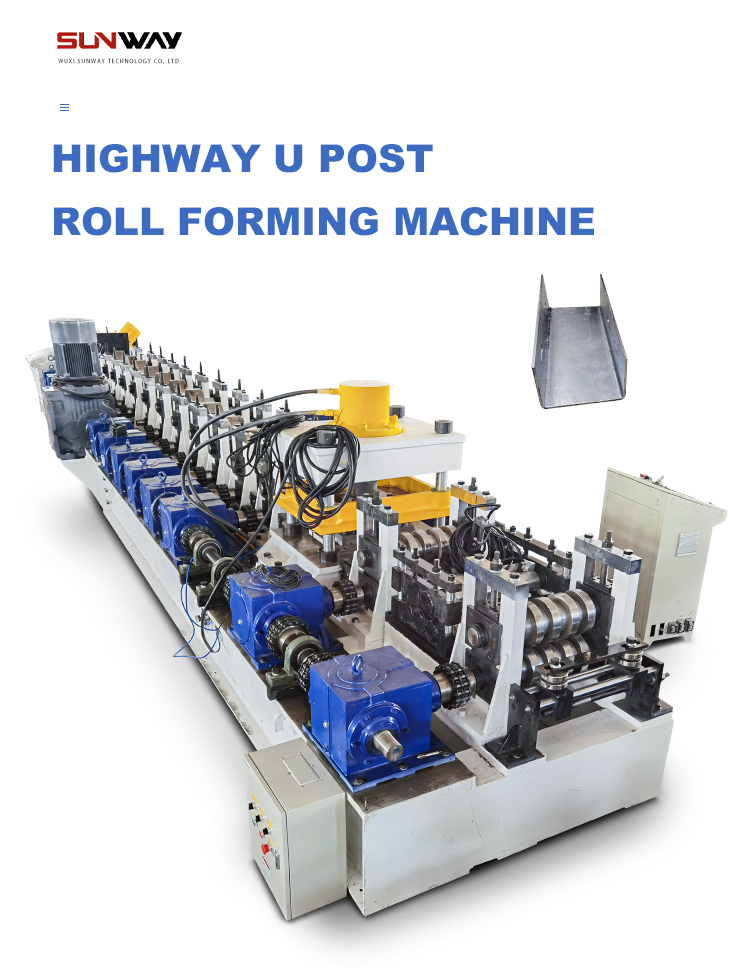
FAQs
Q: What is the cost of tile roll forming machines?
A: Tile roll forming machine prices range from $5,000 for basic machines up to $250,000 for high-speed, fully automated machines. Exact cost depends on speed, size, features, and customization.
Q: Can tile roll forming machines make different profiles?
A: Yes, by changing the roll tooling different tile profiles can be produced on the same machine. Quick change tooling allows fast profile changes.
Q: How to choose right thickness of coils for roll forming tiles?
A: Follow the machine specifications for min and max coil thickness. Typically 0.4-0.7 mm coils are used. Softer temper coils like annealed are easier to form vs harder tempers.
Q: What safety measures are required?
A: Safety features like emergency stops, guards, light curtains, and two-hand operation are necessary. Safety training and PPE for operators is also mandatory.
Q: How much maintenance is needed?
A: Daily cleaning and lubrication is needed. Periodic activities like roller changes, hydraulic oil changes follow supplier schedule. Breakdown maintenance as needed.
Q: What is the production rate for tile roll forming?
A: Production rates vary from 10-35 meters per minute normally based on machine speed and tile specifications. High-end machines exceed 75 meters per minute.
निष्कर्ष
Tile roll forming is an efficient method for high-volume production of metal roofing, wall, and flooring tiles. With the right forming machine selection, operation, and maintenance, manufacturers can produce quality tiles in different profiles cost-effectively. This guide has provided a detailed overview of all aspects of tile roll forming machines to help potential buyers and users.