Overview
Ridge capping roll forming machines are used to produce roofing ridge caps from metal coil stock. Ridge caps are installed along the peak of a roof to cover the intersection where two sloping roof planes meet. Ridge caps serve both aesthetic and functional purposes, providing an attractive finish for the roof apex while shielding the vulnerable joint area from weather damage.
Roll forming is an efficient, high-speed manufacturing process for continuous production of ridge caps and other longitudinally bent or formed metal components. In roll forming, the flat metal strip is progressively shaped by passing through a series of rotating forming rollers that apply localized bending forces along the strip. This incremental forming through a series of stands allows tight-radius bends to be achieved without overstressing the material.
Key attributes and capabilities of ridge capping roll forming machines:
- High production speeds up to 120 meters per minute
- Forming of high strength steels, aluminum, copper
- Available in standard widths or custom widths
- Roller cassettes for quick profile changeovers
- Single-pass and two-pass roll forming configurations
- Integrated notching, punching, or cutting
- Automatic bundle stacking of finished parts
- Touchscreen controls, recipe storage, diagnostics
Roll formed ridge caps are lightweight, durable, and economical to produce in long continuous lengths without welds. They are commonly used for metal roofs on residential, commercial, and industrial buildings. This guide provides detailed specifications, manufacturing processes, and component information on ridge capping roll forming equipment.
Ridge Cap Profiles and Materials
Ridge capping roll forming machines produce roof ridge caps in a range of industry standard profiles, materials, dimensions, and thicknesses.
Table 1. Common Ridge Cap Profiles
Profile | Description |
---|---|
Standard | Angled cap with central raised rib |
Corrugated | Trapezoidal or sinusoidal rib pattern |
Diamond | Interlocking diamond-shaped pans |
Shingle | Overlapping tabs like asphalt shingles |
V-Groove | Lengthwise V-shaped grooves |
Custom | Unique non-standard profiles |
Table 2. Typical Ridge Cap Materials
Material | विशेषताएँ |
---|---|
Galvanized Steel | Corrosion resistance, strength |
Aluminum | Lightweight, long-lasting |
Copper | Natural weathering, prestigious |
Zinc | Rustic matte gray appearance |
Painted Steel | Color options, affordability |
Stainless Steel | Ultimate corrosion resistance |
Table 3. Standard Ridge Cap Dimensions
Widths | 12″, 18″, 24″, 36″ |
---|---|
Lengths | 10+ feet sections |
Thicknesses | 26 – 28 gauge (.45 – .64 mm) |
Rib Heights | 1/2″ – 2″ (12 – 50 mm) |
Custom sizes, radii, and material gauges can be specified based on application requirements. Heavier materials and larger profiles may necessitate two-pass roll forming.
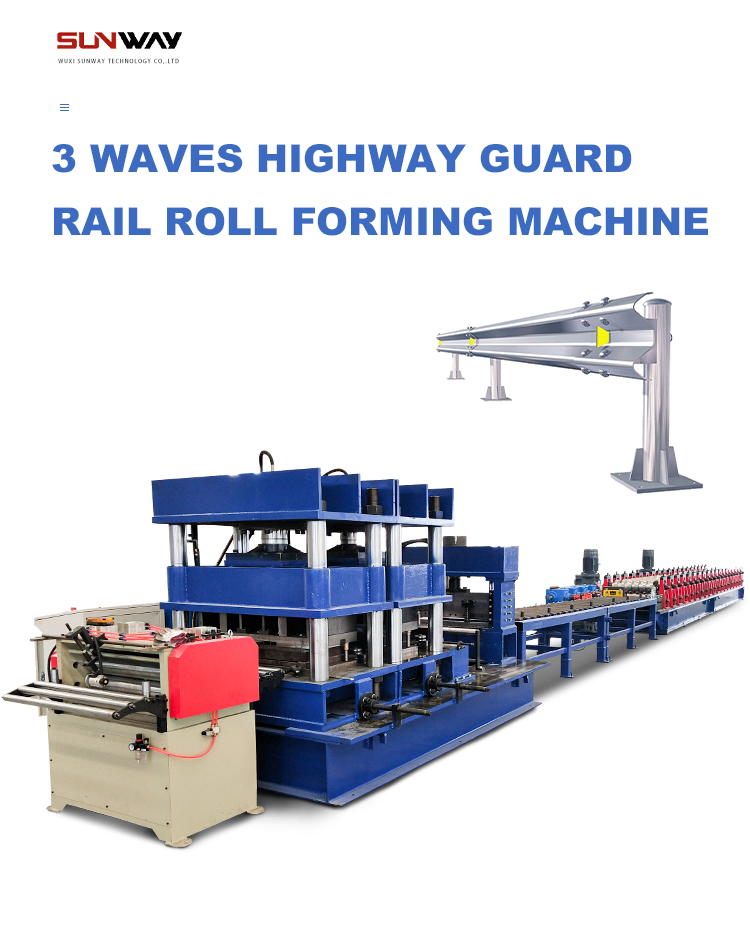
How Ridge Capping Roll Forming Machines Work
Ridge capping roll forming machines take flat sheet metal coil stock as input and produce accurately formed ridge caps as output in a continuous, automated process:
1. Sheet Decoiling
Coiled sheet is loaded onto a powered decoiler which feeds the strip into the roll former at a constant speed.
2. Roll Forming
The strip passes through a series of roller stations which progressively bend and shape the profile.
3. Profile Cutoff
Formed caps are automatically cut to length by a flying shear or rotary shear.
4. Stacked for Bundling
Finished ridge caps are collected and neatly stacked for banding into bundles.
5. Packaged for Shipment
Ridge cap bundles are protected with corner covers, sealed in plastic, strapped to pallets.
Roll Forming Process In-Depth
The core roll forming process involves continuous incremental bending of sheet metal through a series of roller dies to shape the desired profile:
- Sheet is fed into initial roller station which imparts first small bend
- As material advances, subsequent roll stations make additional bends
- Bending progresses gradually from gentle to sharp radii
- Rollers precisely control material flow and avoid thinning or tearing
- Bottom rollers provide counter-force to top bending rollers
- Final roll station completes profile shaping
Roll forming relies on localized, low strain deformations so high strength materials like galvanized steel can be formed without risk of cracking. The longitudinal continuous process enables efficient mass production of finished parts.
Roller Die Types
There are several specialized types of roller dies used in ridge capping roll forming lines:
Forming Rollers
- Precision machined rolls make series of bends
- Hardened to resist wear over millions of cycles
- Can utilize urethane coverings for scratch-free finishing
Pre-punching Rollers
- Optional punching during roll forming
- Eliminates secondary punch press operation
- Result is perforated ridge caps
Embossing Rollers
- Provide decorative surface textures
- Matte, glossy, stippled, or lined finishes
- Popular for high-end architectural metal roofs
Notching Rollers
- Cut notches at precise longitudinal intervals
- Facilitate joining of ridge cap sections
- Indexed by PLC or on fixed periodic basis
Roll Forming Line Components
In additional to roll stands, ridge capping roll forming machines include the following sub-systems:
डेकोइलर
- Capable of handling 5-10 ton coils
- Powered unwinding of sheet
- Maintains consistent line tension
- Uses leveler to flatten coiled sheet
Feed Table
- Supports strip through initial forming stands
- Keeps material tracking straight
Servo Driven Feed
- Precision servo electric drives on pull rolls
- Ensures constant material speed though line
- Prevents tearing or jamming
Automated Stacker
- Collects formed product exiting the line
- Neatly stacks parts for banding
- Eliminates manual labor for stacking
Touchscreen HMI
- Operator interface for production monitoring
- Displays machine status, diagnostics
- Stores recipes for quick changeovers
Safety Guarding
- Full perimeter fencing with interlocks
- Prevents access during operation
- Lockable disconnect switch
Roll Former Configurations
Ridge capping roll forming machines are available in different configurations to suit particular production needs:
Standard Roll Former
- Single-pass design forms in one direction
- Typically for thinner gauges
- Compact footprint, lower cost
Reversing Roll Former
- Sheet is passed back and forth
- Achieves tighter radii bends
- For heavier gauge materials
Serpentine Roll Former
- Material snakes back and forth
- Each pass at slight angle to last
- Permits very long part lengths
Two-Pass Roll Former
- First pass does initial forming
- Second pass completes sharper bends
- For strength materials and large profiles
Portable Roll Former
- Compact, movable unit
- Sets up onsite for on-demand work
- For intermittent ridge cap production
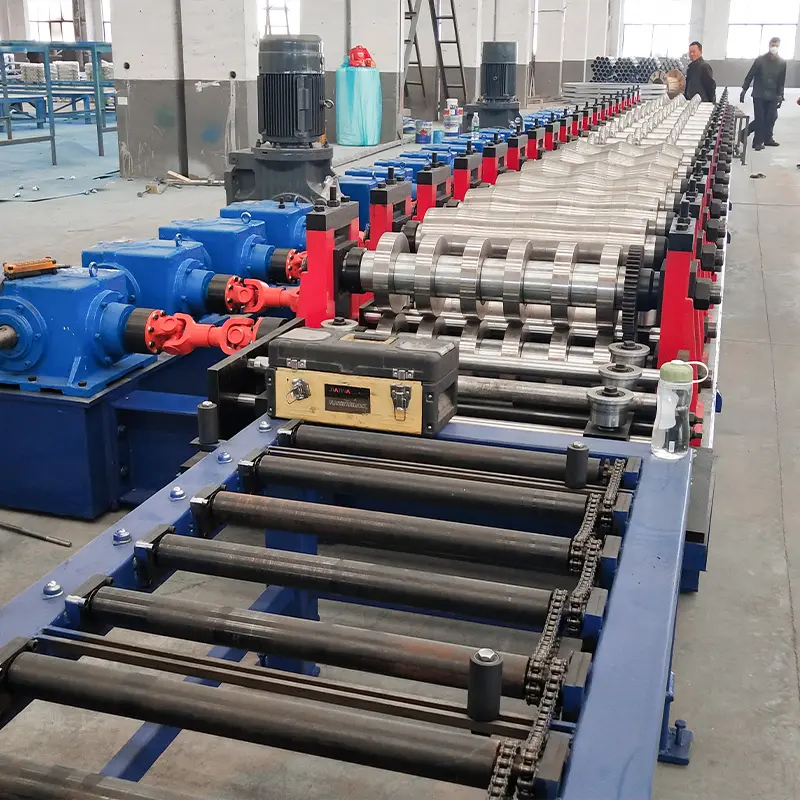
Integrated Fabricating Capabilities
In addition to roll forming, ridge capping lines can integrate inline processing and fabricating capabilities:
Punching
- Optional hydraulic punch unit
- Perforates cap with hole patterns
- For snow/rain drainage and aesthetics
Notching
- Cut notches for aligning sections
- Fixed or indexed spacing
- Use a rotating knife, punch, or laser
Seaming
- Join short caps into longer sections
- Overlapping seam is mechanically locked
- For extended ridge cap lengths
Hemming
- Rolls over edges for safety and appearance
- Improves stiffness, removes sharp edges
- Key for walkable cap applications
Cut-Off
- Flying shear or rotating shear
- Automatically cuts to length after forming
- Lengths from 2 feet to 50+ feet
Marking
- Inkjet prints identifying codes
- Indicates profile, batch, production date
- Assists with inventory and sorting
Machine Control and Monitoring
Modern ridge capping roll forming machines feature advanced controls and diagnostics:
PLC Control
- Programmable automation controller
- Coordinates all machine functions
- Stores recipes for fast changeovers
HMI Interface
- Color touchscreen operator interface
- Displays machine status and diagnostics
- Inputs for production management
Servo Drives
- Closed-loop servos coordinate speed
- Maintain consistent material feed rate
- Enable precision bending and cutoff
Sensors
- Monitor component health and tolerances
- Early warning for preventive maintenance
- Help avoid downtime or quality issues
IIoT Connectivity
- Built-in connectivity to plant data systems
- Remotely monitor production rates
- Assist with troubleshooting and upgrades
Safety Systems
- Light curtains, e-stops, gate interlocks
- Avoid accidental contact with machinery
- Enable safe operation and maintenance
Roll Tooling Setup
A key aspect of achieving quality roll formed parts is proper setup of the roller dies and tooling:
- Roll tools should be free of nicks and wear
- Rolls must be parallel along their length
- Top and bottom rolls should have even pressure
- Roll gaps precision set per tooling specs
- Tooling lubricated to reduce friction and wear
- Tooling should be ground/lapped periodically
- Worn tooling will result in poor tolerances
When changing profiles, a full set of properly gapped tooling must be installed. Stock should be run at slow jog speed to check form quality before full production.
Ridge Cap Specifications and Tolerances
Roll formed ridge caps must meet standards for critical dimensions and key tolerances:
Table 4. Ridge Cap Tolerances
Parameter | Tolerance |
---|---|
Rib Height | +/- 1/32 inch |
Width | +/- 1/16 inch |
Camber | 1/8 inch per 10 feet |
Bow | 1/8 inch per 10 feet |
Twist | 1/8 inch per 10 feet |
Table 5. Ridge Cap Standards
Standard | Key Criteria |
---|---|
ASTM A792 | Galvanized steel specs |
AS 1397 | Steel sheet properties |
AISI SG03-3 | Galvanized coating thickness |
ASTM B209 | Aluminum alloys, tempers |
Roll formed ridge caps should be 100% visually inspected for defects. Length, rib height, and seam alignment should be spot checked periodically. Destructive cross-section tests verify proper bend radii.
Roll Forming Process Optimization
There are several ways to optimize the ridge capping roll forming process:
- Material – Use high strength steel with consistent thickness and surface quality. Aluminum alloys may require two-pass forming.
- Roller Design – Roll geometry, surface finish, hardness, and lubrication all impact quality.
- Tooling Setup – Precise gapping, parallelism, and perpendicularity are essential.
- बनाने की गति – Faster production rates increase risk of material thinning and tearing.
- Roller Pressure – Adequate top/bottom force avoids flattening while preventing ripples.
- Servo Control – Tight speed regulation provides consistency and repeatability.
- Quality Inspection – Verify first piece setup and conduct sampling during runs.
Ridge Cap Roll Forming Machine Manufacturers
There are a number of manufacturers globally that design and build ridge capping roll forming machines:
Table 6. Major Ridge Cap Roll Former Manufacturers
कंपनी | Description |
---|---|
Metform | Broad range of roll forming equipment (Turkey) |
Formtek | Complete lines for roofing components (USA) |
Gasparini | Robust Italian-made roll forming machines |
Bradbury | Leading brand for over 50 years (USA) |
Samuel | Rigorous German engineering standards |
JD Norman | Custom roll formers (USA) |
Shanghai Shengzao | Affordable Chinese roll forming equipment |
Sahil Machines | India-based roll former manufacturer |
When selecting a roll forming machine, key factors to consider are reliability, precision, rigidity, experience, and local service support. Higher cost European equipment generally offers the greatest longevity and tightest tolerances.
Purchasing Considerations
Key considerations when investing in a ridge capping roll forming machine:
Production Volume
- Machine capacity more than needed = waste
- Capacity too low = bottlenecking
Material Type
- Gauge rating and yield strength
- Suitability for high strength steels
Profile Flexibility
- Quick changeover between profiles
- Library of tooling for various caps
Automation Features
- Self-feeding, stacking, bundling
- Reduce labor, increase consistency
Controls
- Touchscreen HMI for monitoring
- Data collection, diagnostics
- Programmable recipes
Quality
- Precision machined components
- Stringent dimensional tolerances
- Vibration resistance for smooth operation
सहायता
- Installation, training, documentation
- Maintenance and service
- Local parts inventory
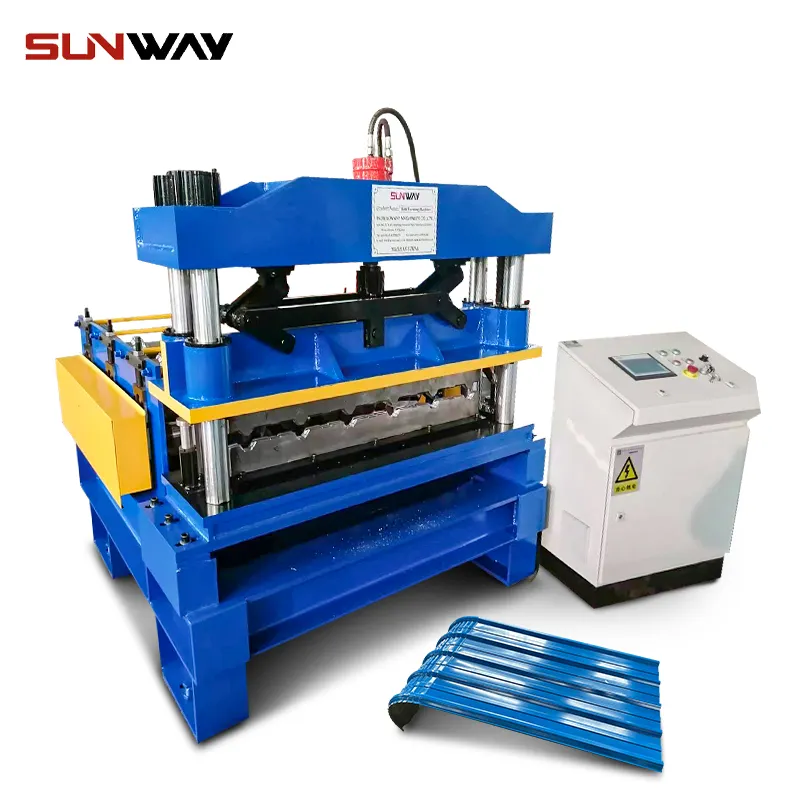
Operating Costs
Ongoing operating costs for a ridge capping roll forming machine include:
Tooling
- Roll dies wear over time
- Replacement every 2-3 years
- Costs $5000 – $10000 per profile
Maintenance
- Consumables like lubricants
- Preventive maintenance labor
- Repairs of worn components
Labor
- Machine setup and loading
- Inspection and packing
- Dependent on level of automation
Utilities
- Machine electrical consumption
- Air compressor usage
- Plant space costs
Materials
- Sheet coil feedstock
- Bundling and packaging
Total operating costs typically range from 10% – 20% annually of machine purchase price. Proper care, maintenance, and operation will provide maximum ROI on the equipment.
सामान्य प्रश्न
Q: What sheet metal thickness can be roll formed into ridge caps?
A: Standard sheet thickness used is 26 – 28 gauge. Heavier gauges up to 16 gauge can be formed in two passes. Thinner 30+ gauge requires special handling.
Q: What motors power the drive system?
A: Servo electric motors paired with precision gear reducers. Inverter duty AC induction motors also common.
Q: How long does it take to changeover between profiles?
A: With pre-gapped quick change roll cassette tooling, profile changeover takes 30 – 60 minutes.
Q: Can the machine work with other metals like copper or brass?
A: Yes – though certain materials may require lower production speeds, two-pass forming, or other adjustments.
Q: What factors determine the ridge cap forming speed?
A: Key factors are material thickness/strength, profile complexity, number of passes, and machine rigidity.
Q: How are multiple ridge cap sections joined together?
A: Adjacent sections can be overlapped in a shingle style. There are also seaming machines to interlock sections.
Q: What safety features are included?
A: Full perimeter guarding, light curtains, emergency stops, electrical disconnects, and redundant safety monitoring.
Q: What determines whether a single or two-pass machine is required?
A: Two-pass roll formers enable tighter radii bends, larger profiles, and heavier gauge materials exceeding the capacity of single-pass designs.
Q: Can the machine produce variable length parts or only fixed lengths?
A: Machines can produce fixed lengths using cam-actuated cutoff or can be configured for variable cutoff on demand.
Q: How should coiled sheet be stored to avoid quality issues?
A: Store coils indoors away from moisture and inspect/clean surfaces for dirt, debris, or scratches prior to roll forming.