परिचय
In the realm of manufacturing, the utilization of advanced machinery has led to remarkable transformations. One such innovation is the Cold Roll Forming Machine, which has revolutionized the process of shaping metal sheets and strips. This article delves into the intricacies of cold roll forming machines, their mechanisms, applications, advantages, and much more.
Understanding Cold Roll Forming
Cold roll forming is a metal fabrication process that involves shaping metal sheets or strips into desired profiles and cross-sections. Unlike traditional hot rolling methods, cold roll forming operates at room temperature, imparting distinct advantages in terms of material properties and energy efficiency.
The Mechanics of Cold Roll Forming Machines
Cold roll forming machines are the heart of this transformative process. These machines consist of several integral components working in harmony to convert raw metal into precise profiles. The process involves feeding the metal through a series of rollers that gradually shape it into the desired form.
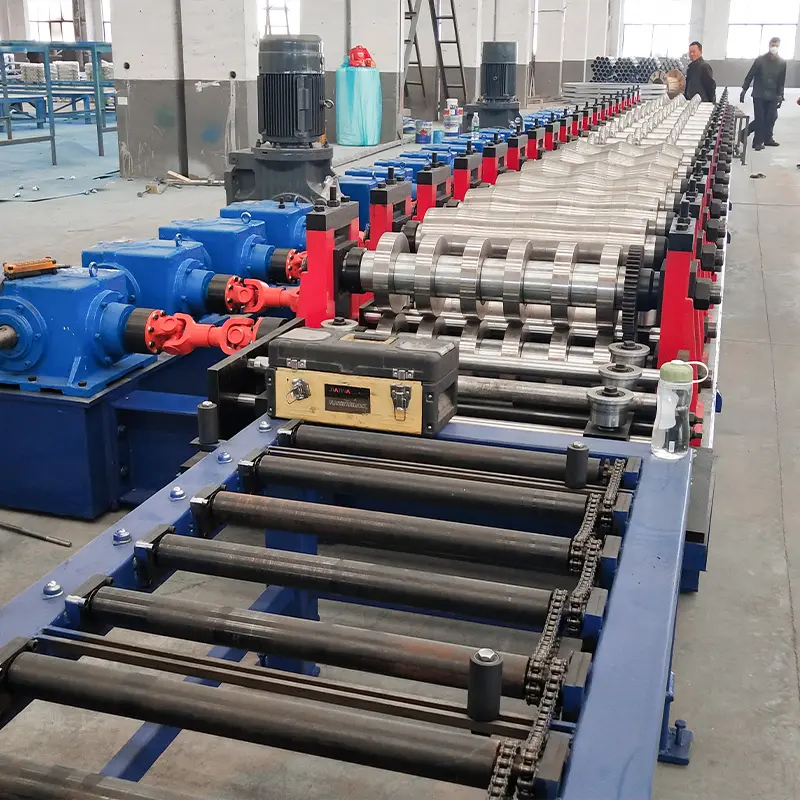
Advantages of Cold Roll Forming Machines
- Material Efficiency: Cold roll forming machines use a continuous bending process to shape metal sheets into desired profiles. This process minimizes material waste, as it uses a single, continuous piece of metal to create a finished product. This efficiency can lead to cost savings over traditional machining methods that generate more scrap material.
- High Precision and Consistency: Cold roll forming machines provide tight tolerances and consistent shapes. The process involves multiple forming stations that gradually shape the material, ensuring accurate dimensions and uniform profiles throughout the length of the product. This precision is particularly important for applications where components must fit together precisely.
- Cost-Effectiveness: While the initial investment in a cold roll forming machine can be relatively high, the long-term cost benefits are significant. The reduced material waste, efficient production process, and minimal need for secondary operations contribute to lower overall production costs.
- Versatility: Cold roll forming machines can produce a wide range of complex profiles and shapes. With proper tooling and adjustments, these machines can create products with various cross-sections, such as C-channels, Z-channels, hat sections, angles, and more. This versatility makes them suitable for diverse industries like construction, automotive, aerospace, and furniture.
- Reduced Material Distortion: Since cold roll forming is conducted at or near room temperature, there is minimal risk of thermal distortion or changes in material properties. This is particularly advantageous for metals that could be negatively affected by high temperatures, preserving their structural integrity.
- High Production Rates: Cold roll forming is a continuous process, allowing for high production rates. Once the machine is set up and the process parameters are optimized, it can produce components at a consistent rate, contributing to efficient large-scale production.
- Minimal Secondary Operations: The precise shaping and forming achieved by cold roll forming machines often eliminate the need for extensive secondary operations such as cutting, welding, and machining. This reduces the overall production time and labor costs associated with these additional processes.
- Suitable for Various Materials: While cold roll forming is commonly associated with steel and other metals, it can also be used with other materials like aluminum, copper, and certain polymers. This adaptability expands the range of applications and industries that can benefit from the process.
- Quick Setup and Changeover: Modern cold roll forming machines are designed for quick tooling changes and adjustments. This flexibility allows manufacturers to switch between different profiles relatively easily, reducing downtime and enabling efficient production of various products.
- Automation Integration: Cold roll forming machines can be integrated into automated production lines, further enhancing efficiency and reducing the need for manual labor. This is especially valuable for high-volume production environments.
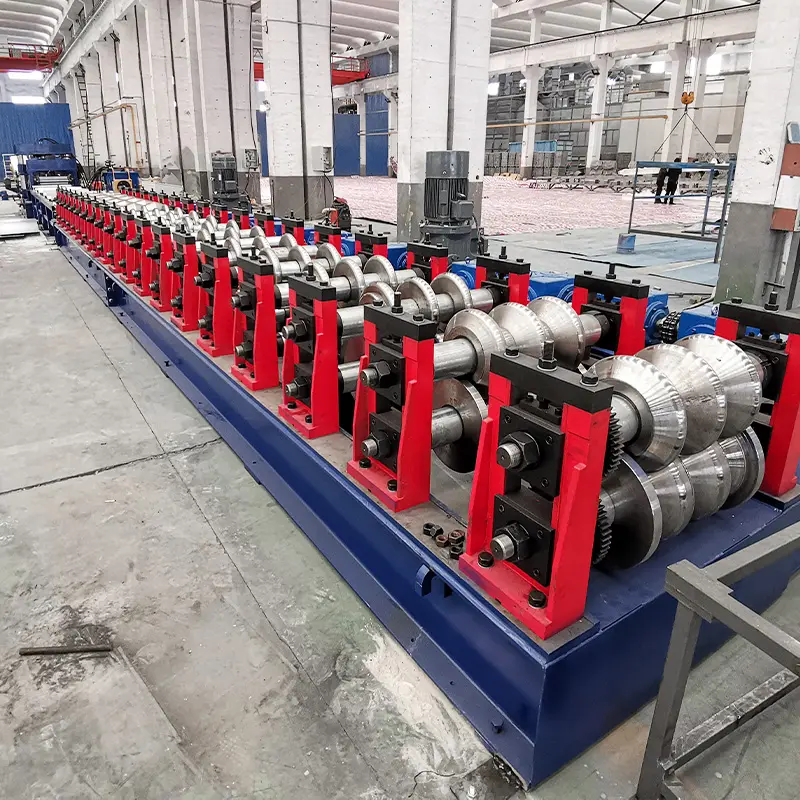
Applications and Industries
- Uncoiler: The uncoiler is the starting point of the process. It holds the coil of metal strip or sheet and feeds it into the roll forming machine. The uncoiler can be motorized to control the feed rate and tension of the material.
- Entry Guide and Leveler: These components help guide the material into the forming section and ensure it enters the machine evenly and without distortion. The leveler helps flatten the material if it has any inherent curvature or bends.
- Roll Forming Stations: The roll forming stations are the heart of the machine. These are sets of rollers, typically in pairs, arranged in a sequence along the production line. Each set of rollers gradually bends and shapes the material into the desired profile. These rollers are adjustable to achieve the precise dimensions and cross-section of the final product.
- Roller Tooling: The roller tooling consists of a series of custom-designed rollers that match the shape of the desired profile. These rollers are mounted on the roll forming stations and determine the final shape of the product. Roller tooling can be changed to produce different profiles on the same machine.
- Gears and Transmission System: The transmission system, often consisting of gears, chains, and belts, transfers power from the main motor to the roll forming stations. It ensures synchronized movement of the rollers and maintains the desired feed rate.
- Cut-off Mechanism: Some cold roll forming machines have an integrated cut-off mechanism that trims the continuous formed product into individual lengths. This can be a shear or a flying cutoff system, depending on the design.
- Guiding Systems: Guiding systems help maintain the alignment of the material as it goes through the forming process. This ensures the accuracy and consistency of the profile throughout the production run.
- Cooling and Lubrication: Cold roll forming generates friction and heat, so cooling and lubrication systems are often incorporated to prevent material damage and reduce wear on the rollers and tooling.
- नियंत्रण प्रणाली: Modern cold roll forming machines are equipped with advanced control systems that allow operators to set various parameters such as roll gap, speed, and feed rate. These systems also enable monitoring of the production process, ensuring consistent quality and making adjustments as needed.
- Exit Guide: Similar to the entry guide, the exit guide helps guide the formed material out of the machine, ensuring it maintains its shape and accuracy.
- Stacker or Conveyor: Once the material is formed and cut, it may be collected using a stacker or conveyor system, facilitating easy collection and transportation for further processing or packaging.
- Safety Features: Safety mechanisms such as emergency stops, safety guards, and interlocks are crucial to ensure the well-being of operators and prevent accidents during machine operation.
Key Components of a Cold Roll Forming Machine
A cold roll forming machine comprises key components such as uncoilers, feeding systems, roll stands, cutting units, and control systems. These components collaborate meticulously to ensure accurate and consistent profile shaping.
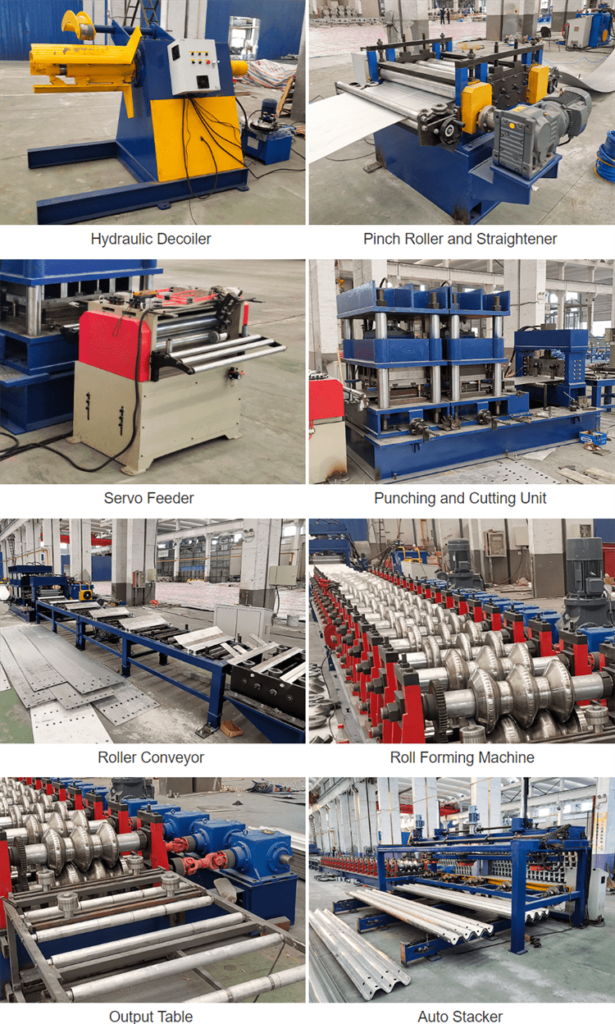
Factors to Consider When Choosing a Cold Roll Forming Machine
Selecting the right cold roll forming machine demands consideration of factors like material type, desired profile, production volume, and budget. The choice between standard and custom machines further shapes the decision-making process.
Setting Up and Operating a Cold Roll Forming Machine
The setup and operation of a cold roll forming machine require expertise and precision. Proper material handling, alignment, and adjustment of roll stands are vital for achieving the desired product outcome.
Maintenance and Troubleshooting
Sustaining the machine’s performance necessitates routine maintenance and prompt troubleshooting. Regular inspections, lubrication, and addressing wear and tear contribute to prolonged machine life and consistent output quality.
Innovations in Cold Roll Forming Technology
Advancements in technology continue to enhance cold roll forming processes. Computer simulations, automation, and improved materials have optimized product quality, reduced waste, and accelerated production cycles.
Future Trends and Outlook
The future of cold roll forming machines is promising, with an emphasis on sustainability, process efficiency, and further integration of digital technologies. These trends are set to shape the manufacturing landscape.
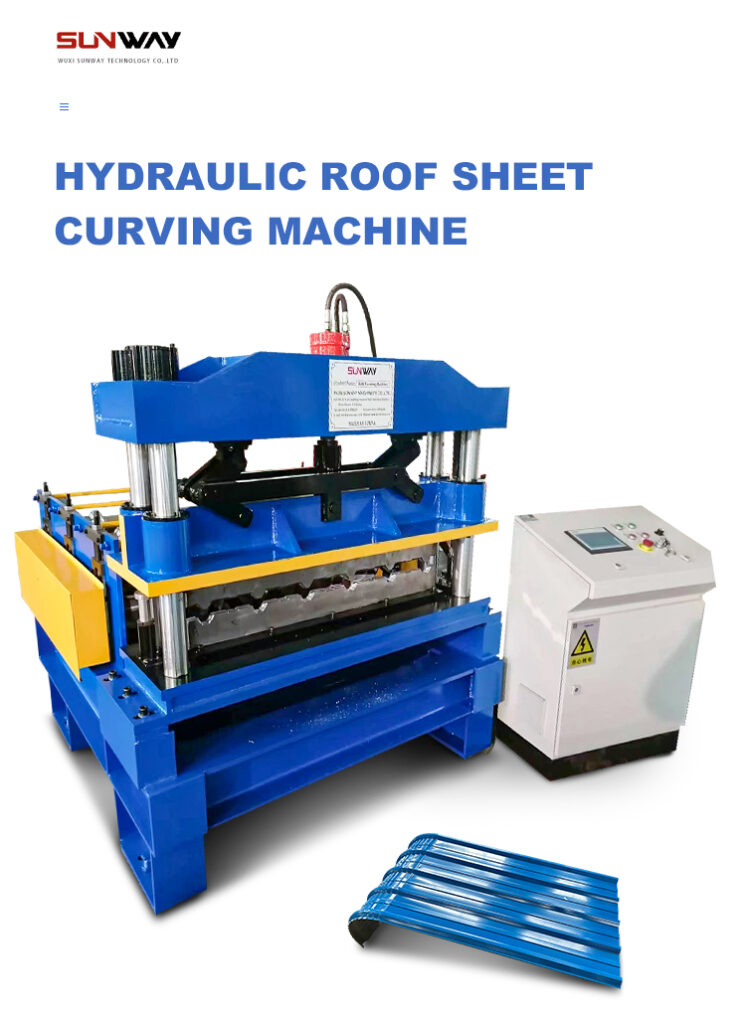
निष्कर्ष
In the dynamic world of metal manufacturing, cold roll forming machines have cemented their importance. The fusion of innovative design, precision engineering, and adaptability has made these machines indispensable across industries. As technology evolves, so does the potential of cold roll forming machines, ushering in a new era of efficient and sustainable manufacturing.
सामान्य प्रश्न
1. What materials can be processed using cold roll forming machines? Cold roll forming machines can process various metals, including steel, aluminum, copper, and more.
2. How does cold roll forming differ from hot rolling? Cold roll forming operates at room temperature, preserving material properties and eliminating the need for extensive post-processing, unlike hot rolling.
3. What industries benefit from cold roll forming machines? Industries such as construction, automotive, aerospace, and manufacturing benefit from the versatility of cold roll forming machines.
4. What is the role of automation in modern cold roll forming? Automation enhances precision and efficiency in cold roll forming, leading to higher production rates and consistent quality.
5. How are custom profiles accommodated in cold roll forming? Cold roll forming machines can be customized to create specific profiles, catering to diverse industrial needs.