परिचय
Panel roll forming machines play a crucial role in the manufacturing industry, enabling efficient and precise production of various types of panels used in construction, automotive, and other sectors. In this comprehensive article, we will explore the key aspects of panel roll forming machines and address the most frequently asked questions about them.
Common Questions about Panel Roll Forming Machines
- What is a panel roll forming machine?A panel roll forming machine is an industrial equipment used to shape metal sheets into desired panel profiles. It consists of a series of rollers and tooling that gradually bend the metal sheet into the desired shape. This process is continuous and automated, allowing for high-volume production of uniform panels.
- What types of panels can be produced with these machines?Panel roll forming machines are versatile and can produce a wide range of panels, including roofing panels, wall panels, floor decking panels, and even automotive body panels. The flexibility in design and tooling allows manufacturers to create panels with various profiles, sizes, and thicknesses.
- How does panel roll forming compare to other metal forming methods?Panel roll forming offers several advantages over other metal forming methods like stamping or press braking. It is highly automated, reducing labor costs, and offers consistent quality. Additionally, it can handle large sheet lengths, making it suitable for long panels used in construction.
- What materials can be used in panel roll forming machines?Panel roll forming machines primarily work with metals such as steel, aluminum, and copper. The material’s malleability and thickness determine the ease of roll forming. These machines can handle both coated and uncoated metal sheets.
- What are the key components of a panel roll forming machine?A panel roll forming machine consists of several essential components, including decoilers to feed the metal sheet, leveling units to ensure a flat sheet, a series of rollers and tooling for shaping, and a cutting or shearing system to trim the panel to the desired length.
- How is the quality of roll-formed panels ensured?Quality control measures are integrated into the roll forming process. Automated systems monitor parameters like roller pressure, speed, and material thickness to maintain consistent panel dimensions and profiles. Regular maintenance of the machine and tooling also plays a crucial role in quality assurance.
- Can custom panel profiles be created?Yes, panel roll forming machines allow for the creation of custom profiles. Manufacturers can design and develop specific tooling to achieve unique panel shapes. This flexibility is especially advantageous for architectural projects that require distinctive panel designs.
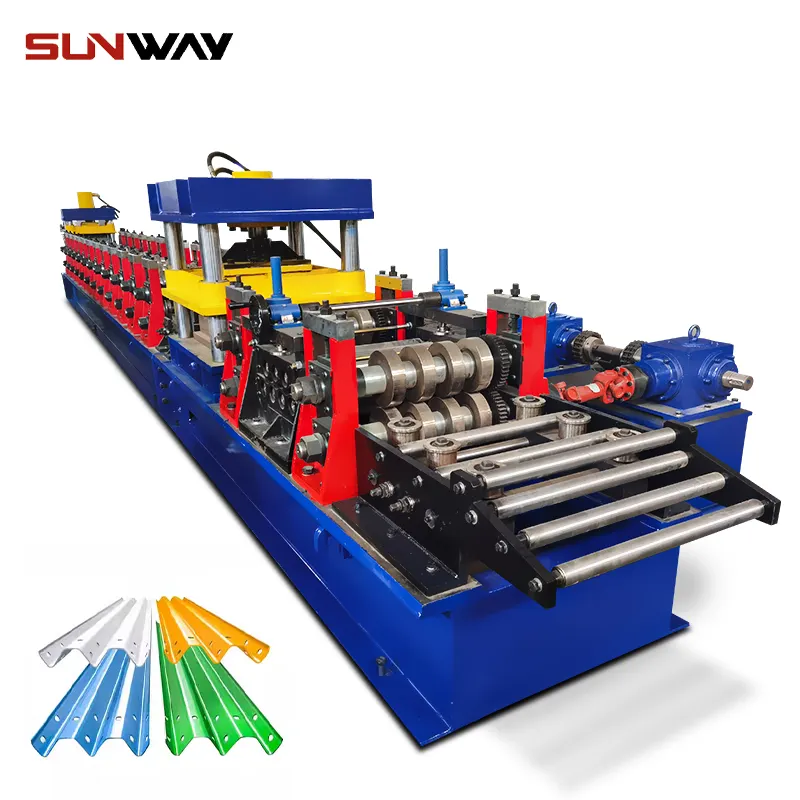
Exploring the Working Principles of Panel Roll Forming Machines
Panel roll forming machines operate on a set of well-defined principles:
- Feeding the Material:The process begins with a metal coil loaded onto a decoiler. The machine gradually feeds the metal sheet into the forming section.
- Gradual Bending:The forming section consists of a series of rollers placed in pairs. These rollers gradually bend the metal sheet as it passes through them. Each roller pair contributes to shaping the panel profile.
- Roller Design:The rollers are designed based on the desired panel profile. They can have different contours, allowing them to shape the metal in precise ways.
- Cutting or Shearing:Once the metal sheet has been fully roll-formed, a cutting or shearing system trims the panel to the required length. This step completes the manufacturing process for one panel.
- Collecting and Stacking:The finished panels are collected and stacked for further processing or packaging. This automation minimizes manual handling and reduces the risk of damage.
Maintaining and Troubleshooting Panel Roll Forming Machines
Maintaining and troubleshooting panel roll forming machines is essential to ensure their efficiency and longevity. Here are some key considerations:
- Regular Lubrication:Proper lubrication of moving parts, especially the rollers, is crucial to prevent wear and tear. Regular maintenance schedules should include lubrication routines.
- Checking Alignment:Misalignment of rollers can lead to irregular panel shapes. Regularly inspect and adjust the alignment of rollers to maintain accurate forming.
- Replacing Worn Tooling:The tooling used in roll forming can experience wear over time. Replace worn or damaged tooling promptly to avoid defects in the panels.
- Monitoring Electrical Systems:Panel roll forming machines often have complex electrical systems controlling various aspects of the process. Regularly inspect and test these systems to ensure they are functioning correctly.
- Addressing Vibrations:Excessive vibrations can indicate mechanical issues or misalignment. Investigate and resolve the source of vibrations to prevent further damage.
Safety Measures for Operating Panel Roll Forming Machines
Operating panel roll forming machines safely is of paramount importance. Follow these safety measures:
- Training:Operators should receive thorough training on the machine’s operation, including emergency shutdown procedures.
- Protective Gear:Operators must wear appropriate personal protective equipment, such as gloves, safety glasses, and ear protection, to prevent injuries.
- Emergency Stop Buttons:Machines should be equipped with easily accessible emergency stop buttons that immediately halt the operation in case of any safety concerns.
- Lockout/Tagout:Before performing maintenance or adjustments, the machine should be properly locked out or tagged out to prevent accidental startup.
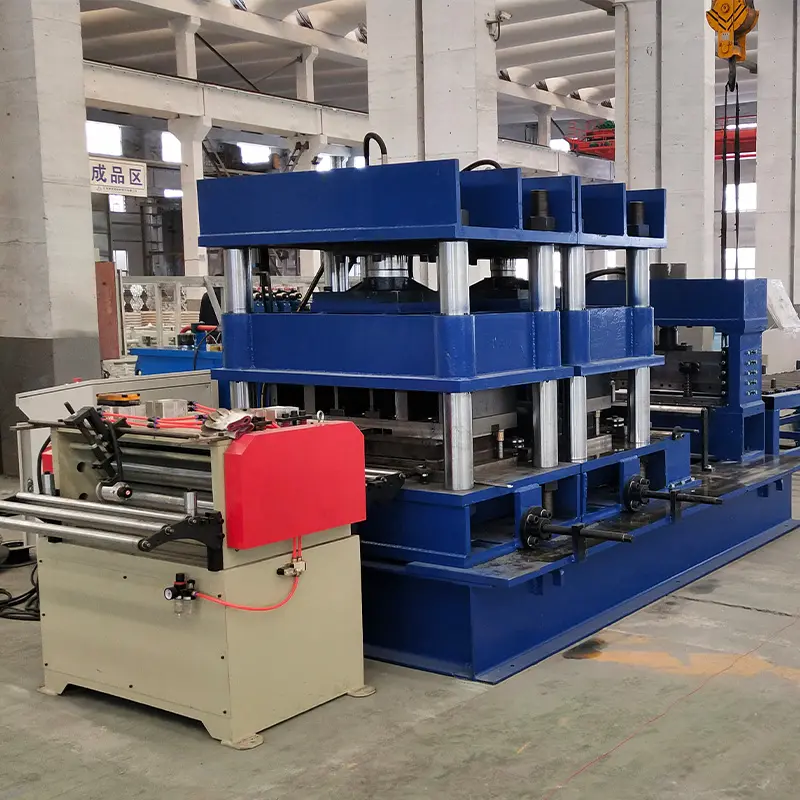
Advantages and Applications of Panel Roll Forming Machines
Panel roll forming machines offer numerous advantages and find applications in various industries:
- Advantages:
- High production speed and efficiency.
- Consistent panel quality and accuracy.
- Versatility in panel profiles and sizes.
- Reduced labor costs and manual intervention.
- Suitable for both large-scale and custom production.
- Applications:
- Construction industry for roofing, wall cladding, and floor decking.
- Automotive industry for manufacturing body panels.
- Industrial sector for producing enclosures and panels for machinery.
Maintenance Tips for Panel Roll Forming Machines
Maintaining panel roll forming machines helps ensure their optimal performance:
- Regular Inspections:Regularly inspect the machine for signs of wear, misalignment, or damage. Address any issues promptly to prevent downtime.
- Cleaning:Keep the machine clean from dust, debris, and metal shavings, as these can affect the machine’s precision.
- Greasing and Oil Changes:Follow manufacturer guidelines for greasing and changing oils in the machine’s moving parts. This prevents friction and extends the machine’s lifespan.
Considerations When Choosing a Panel Roll Forming Machine
Selecting the right panel roll forming machine requires careful consideration:
- Panel Requirements:Determine the types of panels you need to produce, including profiles, sizes, and material thicknesses.
- Material Compatibility:Ensure the machine can work with the types of metal you plan to use, whether it’s steel, aluminum, or other alloys.
- Automation Level:Consider the level of automation you need, from basic manual controls to advanced computerized systems.
Troubleshooting Common Issues in Panel Roll Forming Machines
Despite their efficiency, panel roll forming machines can encounter various issues. Here are some common problems and possible solutions:
- Irregular Panel Profiles:Issue: Panels coming out with inconsistent profiles or dimensions. Solution: Check for misaligned rollers, worn tooling, or material feed issues. Address these problems to ensure proper panel shaping.
- Material Jamming:Issue: Metal sheets getting stuck or jammed in the machine. Solution: Inspect the decoiler and feeding mechanisms for any obstacles. Ensure proper tension and alignment of the metal coil.
- Excessive Noise and Vibration:Issue: Unusual noise and vibrations during operation. Solution: Check for loose components, worn bearings, or misaligned parts. Tighten or replace as needed to reduce noise and vibration.
- Inaccurate Cutting:Issue: Panels being cut too short or too long. Solution: Adjust the cutting or shearing system’s settings to ensure accurate panel lengths.
- Material Deformation:Issue: Material getting bent or warped during the roll forming process. Solution: Review material specifications and machine settings to ensure compatibility. Properly calibrate the machine for the specific material.
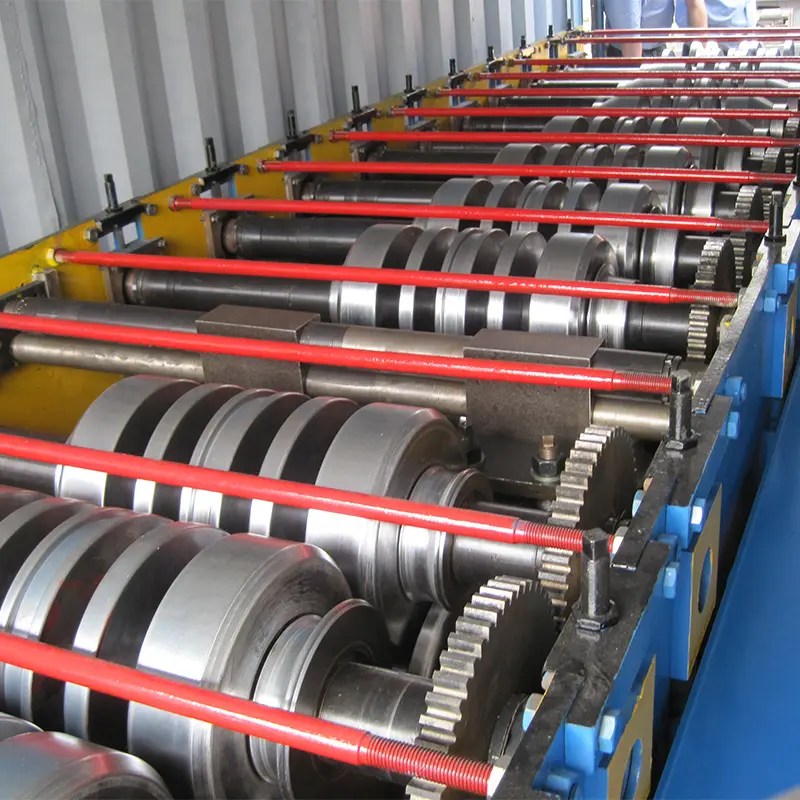
Maintenance Schedule for Panel Roll Forming Machines
A regular maintenance schedule is essential for the longevity and consistent performance of panel roll forming machines:
- Daily Checks:
- Inspect rollers for signs of wear.
- Check for any unusual noise or vibrations during operation.
- Ensure proper lubrication of moving parts.
- Weekly Tasks:
- Clean the machine from dust, debris, and metal shavings.
- Verify alignment of rollers and tooling.
- Monthly Maintenance:
- Perform more detailed inspections of electrical systems.
- Grease and oil moving parts as needed.
Increasing Efficiency with Panel Roll Forming Machines
To maximize the efficiency of panel roll forming machines, consider these strategies:
- Optimized Tooling Design:Custom tooling can enhance the machine’s capabilities, allowing for the production of intricate and unique panel profiles.
- Integration with Other Processes:Integrate the roll forming process seamlessly with other manufacturing stages to streamline production and minimize downtime.
- Data Monitoring and Analysis:Implement data monitoring systems to track production metrics, identify trends, and optimize machine settings.
Exploring Future Trends in Panel Roll Forming
The future of panel roll forming machines holds exciting possibilities:
- Advanced Automation:Continued advancements in automation will lead to even faster production speeds and improved accuracy.
- Material Innovation:Machines will adapt to work with a broader range of materials, including composites and advanced alloys.
- Smart Manufacturing:Integration with IoT technology will enable remote monitoring, predictive maintenance, and real-time production adjustments.
Table Summary
Step | Topic |
---|---|
Step 1 | Common Questions about Panel Roll Forming |
Step 2 | Working Principles of Panel Roll Forming |
Step 3 | Maintaining and Troubleshooting |
Step 4 | Safety Measures for Operating |
Step 5 | Advantages and Applications |
Step 6 | Maintenance Tips |
Step 7 | Considerations When Choosing a Machine |
Step 8 | Troubleshooting Common Issues |
Step 9 | Maintenance Schedule |
Step 10 | Increasing Efficiency |
Step 11 | Future Trends in Panel Roll Forming |
सामान्य प्रश्न
Q1: What is a panel roll forming machine?
A1: A panel roll forming machine is an industrial equipment used to shape metal sheets into desired panel profiles.
Q2: What types of panels can be produced?
A2: Panel roll forming machines can produce roofing, wall, floor decking panels, and more, with various profiles and sizes.
Q3: How does roll forming compare to other methods?
A3: Roll forming offers consistent quality, automation, and suitability for long panels, distinguishing it from stamping or press braking.
Q4: What materials can be used?
A4: These machines work with metals like steel, aluminum, and copper, both coated and uncoated.
Q5: What are the key components of a machine?
A5: Components include decoilers, leveling units, rollers, tooling, and cutting systems.