परिचय
In the ever-evolving construction industry, innovative technologies have paved the way for more efficient and cost-effective roofing solutions. One such groundbreaking invention is the metal roof roll forming machine. This article delves into the world of metal roof roll forming machines, exploring their functionality, advantages, types, components, applications, and future prospects.
मेटल रूफ रोल बनाने की मशीन क्या है?
At its core, a metal roof roll forming machine is an advanced piece of equipment designed to transform metal coils into perfectly shaped roofing panels. The process involves passing the metal coils through a series of rollers that gradually shape and cut the metal to the desired profile. These machines can create a variety of roofing panel profiles, including corrugated panels, standing seam panels, and ribbed panels, among others.
How Does a Metal Roof Roll Forming Machine Work?
The working principle of a metal roof roll forming machine is ingeniously simple yet highly effective. The machine typically consists of a decoiler, a roll forming unit, a cutting system, a control panel, and a stacker. The process begins with the decoiler feeding the metal coil into the roll forming unit. As the coil passes through the rollers, it undergoes precise shaping according to the chosen profile. The cutting system then trims the formed panel to the required length, while the control panel oversees the entire process. Finally, the stacker neatly collects and bundles the finished panels for easy handling and transport.
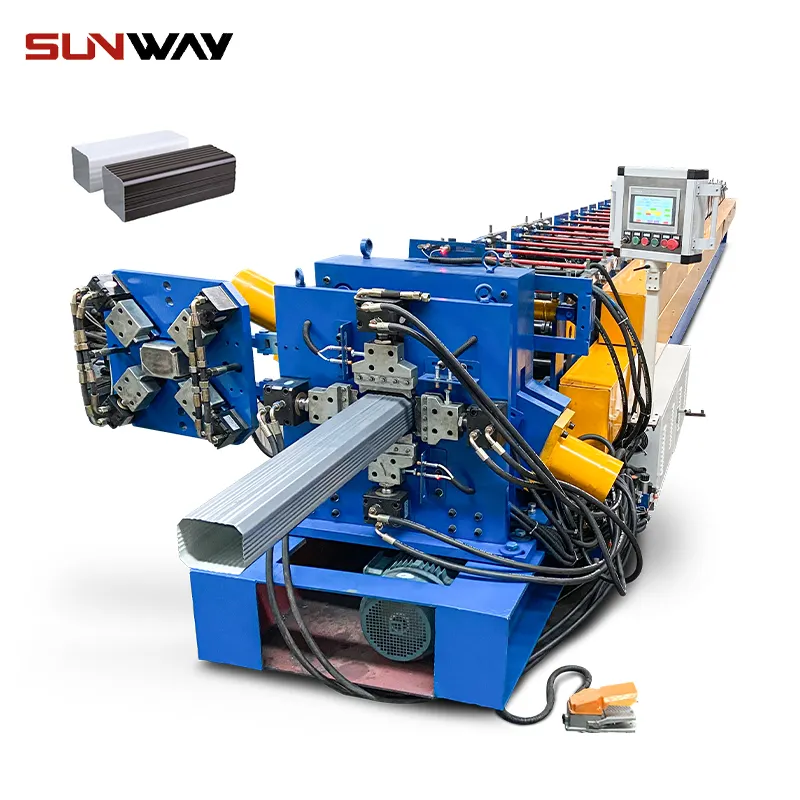
Advantages of Using a Metal Roof Roll Forming Machine
Cost-Effectiveness
Metal roof roll forming machines offer significant cost advantages over traditional roofing manufacturing methods. The automation and high production speeds minimize labor costs, and the efficient use of materials reduces waste, making it an economically viable choice for both manufacturers and consumers.
Efficiency and Productivity
With rapid production capabilities, metal roof roll forming machines can churn out large volumes of roofing panels in a short time. This efficiency ensures timely project completion, meeting tight construction deadlines without compromising quality.
Customization Options
Flexibility in design is a hallmark of metal roof roll forming machines. Manufacturers can easily switch between different profiles and shapes, catering to diverse customer preferences and project requirements.
Durability and Longevity
Metal roofing panels produced by roll forming machines are renowned for their exceptional durability and longevity. They can withstand harsh weather conditions, resist corrosion, and require minimal maintenance, providing long-term value to property owners.
Types of Metal Roofing Materials Used in Roll Forming Machines
Metal roof roll forming machines are versatile and compatible with various types of metal materials. The most commonly used materials include:
Steel Roofing
Steel is the most popular choice for metal roofing due to its strength, affordability, and wide range of coating options, protecting against rust and enhancing aesthetics.
Aluminum Roofing
Aluminum offers lightweight roofing solutions with excellent corrosion resistance, making it ideal for coastal and marine environments.
Copper Roofing
Copper is a premium roofing material known for its distinctive appearance and exceptional longevity, developing an attractive patina over time.
Zinc Roofing
Zinc roofing combines durability with environmental sustainability, as it is a 100% recyclable material with a long lifespan.
Components of a Metal Roof Roll Forming Machine
A typical metal roof roll forming machine consists of several essential components, each playing a crucial role in the production process:
डेकोइलर
The decoiler is responsible for holding and feeding the metal coil into the roll forming unit. It ensures a continuous supply of material during the production cycle.
Roll Forming Unit
The heart of the machine, the roll forming unit, contains a series of rollers that shape the metal coil into the desired roofing profile. The number and arrangement of rollers determine the complexity of the profiles that the machine can create.
कटिंग सिस्टम
After the metal coil is formed into the desired profile, the cutting system accurately trims the panel to the required length, ensuring precision and consistency.
Control Panel
The control panel acts as the brain of the machine, overseeing the entire production process. Operators can input parameters, monitor operations, and make adjustments as needed.
Stacker
The stacker collects and bundles the finished roofing panels, streamlining the packaging and transport process for ease of use.
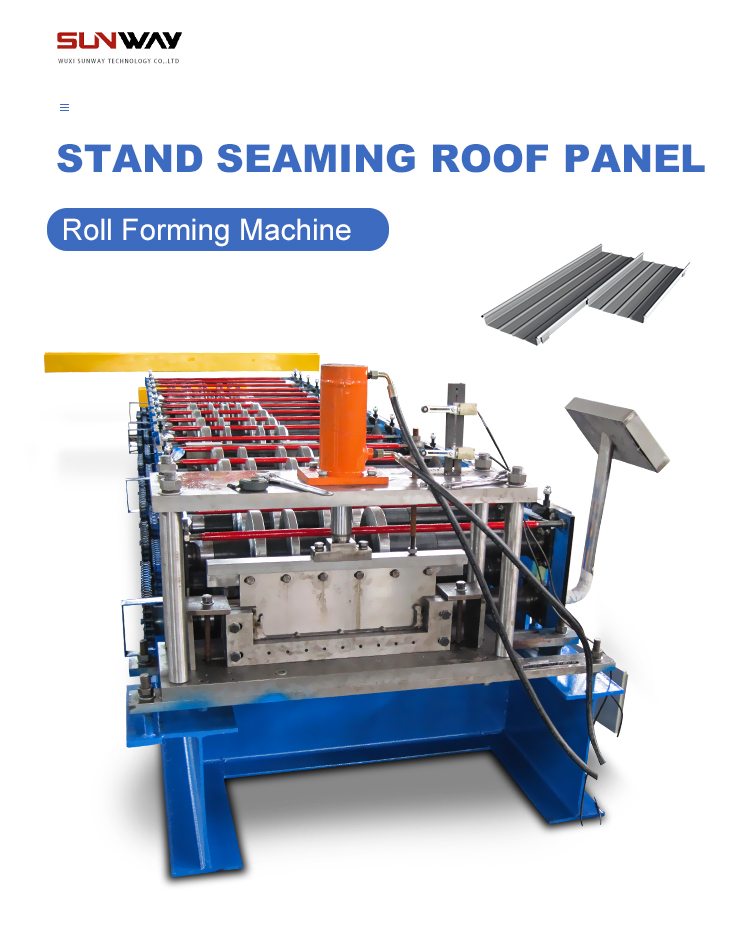
Different Profiles and Shapes Produced by Metal Roof Roll Forming Machines
Metal roof roll forming machines are incredibly versatile, capable of producing various roofing panel profiles and shapes. Some of the most common profiles include:
Corrugated Panels
Corrugated panels are popular for their strength and affordability. The distinctive ridges provide excellent structural support and are often used in
Standing Seam Panels
Standing seam panels are characterized by raised seams that interlock to create a sleek, modern appearance. They are known for their exceptional weather resistance and are often chosen for commercial and high-end residential projects.
Ribbed Panels
Ribbed panels feature pronounced ribs or ridges running parallel along the length of the panel. These panels offer enhanced structural integrity and are commonly used in industrial and agricultural applications.
Custom Profiles
Metal roof roll forming machines can be customized to create unique and custom profiles, allowing architects and builders to unleash their creativity and design one-of-a-kind roofing solutions.
Factors to Consider When Choosing a Metal Roof Roll Forming Machine
Selecting the right metal roof roll forming machine is a crucial decision for any manufacturer or contractor. Several factors should be taken into account:
Production Capacity
Assess the required production capacity to determine the size and speed of the machine. Higher production capacities may require larger machines with advanced automation features.
Material Compatibility
Ensure that the machine is compatible with the desired metal roofing materials, as different materials may require specific adjustments and tooling.
Automation and Technology
Modern roll forming machines often come with automation and advanced technology, which can improve efficiency and reduce human errors during the production process.
Budget and Cost Considerations
Set a budget and consider the overall cost of the machine, including installation, maintenance, and training. Balance the features and capabilities with the available budget.
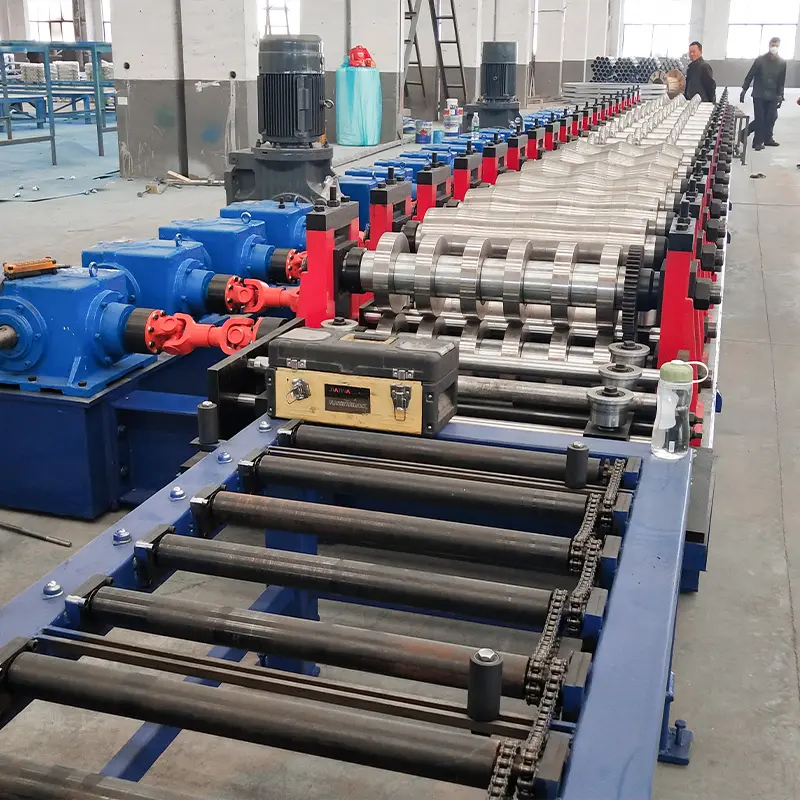
Maintenance and Care for Metal Roof Roll Forming Machines
To ensure the longevity and optimal performance of a metal roof roll forming machine, proper maintenance and care are essential:
Regular Inspections and Cleaning
Regularly inspect the machine for any signs of wear, damage, or misalignment. Keep the machine clean and free from debris that could impact its performance.
Lubrication and Preventive Maintenance
Follow the manufacturer’s guidelines for lubrication and perform preventive maintenance at scheduled intervals to prevent breakdowns and ensure smooth operation.
Troubleshooting Common Issues
Train operators in troubleshooting common issues and provide them with the necessary tools and knowledge to address minor problems promptly.
Safety Precautions When Operating a Metal Roof Roll Forming Machine
Safety is paramount when operating any industrial machinery, and metal roof roll forming machines are no exception. Implement the following safety precautions:
Training and Operator Knowledge
Ensure that all operators receive thorough training on how to use the machine safely and effectively.
Personal Protective Equipment (PPE)
Mandate the use of appropriate personal protective equipment, including gloves, safety glasses, and hearing protection.
Machine Guarding
Install adequate machine guards to protect operators from moving parts and potential hazards.
Emergency Stop Procedures
Ensure that emergency stop buttons are easily accessible and that operators are familiar with their location and usage.
Applications of Metal Roofing Panels
Metal roofing panels produced by roll forming machines find a wide range of applications across various industries:
Residential Roofing
Metal roofing panels are increasingly popular in residential settings due to their longevity, energy efficiency, and aesthetic appeal.
Commercial and Industrial Roofing
The durability and cost-effectiveness of metal roofing panels make them a preferred choice for commercial and industrial buildings.
Agricultural Buildings
Metal roofing provides robust protection for agricultural buildings, ensuring the safety and well-being of livestock and equipment.
Architectural Projects
Architects often opt for metal roofing panels to achieve unique and striking designs in architectural projects.
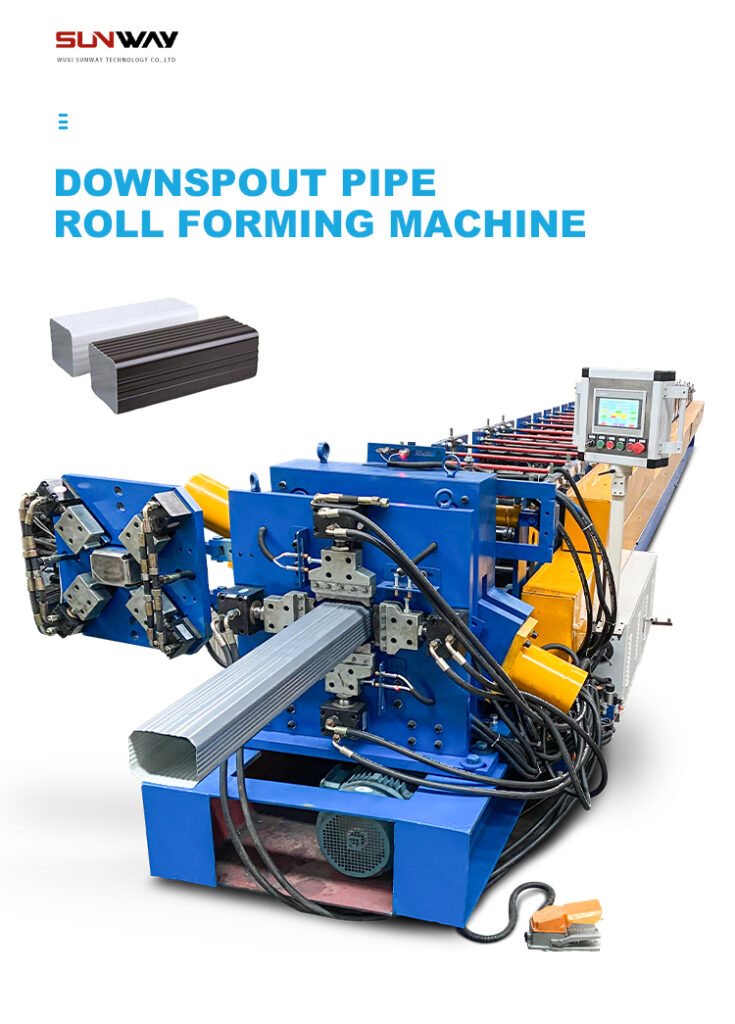
Future Trends in Metal Roof Roll Forming Technology
As technology advances, metal roof roll forming machines are poised for further innovation:
Automation and Robotics Integration
Automation and robotics integration will enhance production efficiency and reduce manual labor requirements.
Eco-Friendly Materials and Processes
The industry will likely witness a shift towards eco-friendly materials and sustainable manufacturing practices.
Advanced Profile Design and Customization
Advancements in design software and technology will allow for even more intricate and customizable roofing profiles.
Case Studies: Success Stories of Metal Roof Roll Forming Applications
Real-world examples demonstrate the power and impact of metal roof roll forming technology:
Green Energy Initiatives
Metal roofing panels have been incorporated into renewable energy projects, such as solar panel installations, to promote sustainability.
Disaster Relief Efforts
Metal roofing panels have played a vital role in providing quick and reliable shelter solutions during disaster relief efforts.
Urban Development and Sustainability
Metal roofing panels are a key component in urban development projects aimed at creating energy-efficient and sustainable communities.
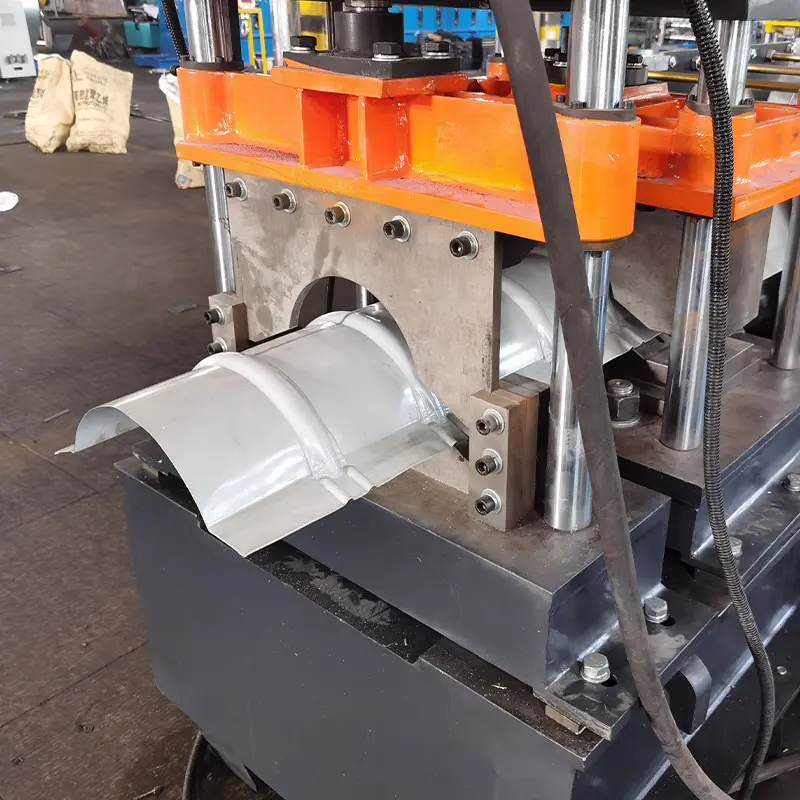
निष्कर्ष
Metal roof roll forming machines have revolutionized the roofing industry, offering cost-effective, efficient, and customizable solutions for various applications. From residential to commercial, from standard profiles to custom designs, these machines have opened up new possibilities for architects, builders, and property owners alike. As technology continues to advance, the future of metal roof roll forming machines looks even more promising, with sustainable materials, automation, and advanced profile design on the horizon.
Whether it’s enhancing the energy efficiency of buildings or providing disaster relief, metal roofing panels produced by roll forming machines will continue to shape the way we build and protect our structures for years to come.
FAQs
1. Are metal roofing panels more expensive than traditional roofing materials?
Metal roofing panels may have a higher upfront cost than some traditional materials, but their longevity and energy-saving properties make them a cost-effective choice in the long run.
2. Can metal roofing panels withstand severe weather conditions?
Yes, metal roofing panels are highly durable and can withstand harsh weather conditions, including strong winds, heavy rains, and hailstorms.
3. Can metal roofing panels be customized to fit unique architectural designs?
Absolutely! Metal roof roll forming machines can be programmed to create custom profiles, offering endless design possibilities for architects and builders.
4. What is the average lifespan of metal roofing panels?
With proper installation and maintenance, metal roofing panels can last for 50 years or more, outlasting many traditional roofing materials.
5. Is it possible to retrofit existing buildings with metal roofing panels?
Yes, metal roofing panels can be retrofit onto existing buildings, providing a cost-effective and durable roofing solution.