When it comes to roofing, ensuring proper protection against water damage is essential for the longevity and integrity of any structure. One crucial component that plays a significant role in safeguarding roofs is the drip edge. In the construction industry, the demand for drip edges has surged, leading to the development of efficient manufacturing solutions like the drip edge roll forming machine. This article delves into the world of drip edge roll forming machines, exploring their functionality, benefits, key features, working process, selection criteria, industry applications, and future trends.
Understanding Drip Edge in Roofing
What is Drip Edge?
Drip edge is a metal flashing installed along the edges of roofs to prevent water from seeping into vulnerable areas, such as the fascia, eaves, and roof decking. It acts as a barrier, directing water away from the structure and preventing damage caused by leaks, rot, and mold growth.
Importance of Drip Edge in Roofing
The inclusion of a drip edge in roofing systems offers several advantages. It helps to protect the underlying roof structure by preventing water infiltration and redirecting it away from the fascia. Additionally, a drip edge assists in maintaining the integrity of the roof’s shingles or other roofing materials, reducing the risk of premature deterioration and improving overall longevity.
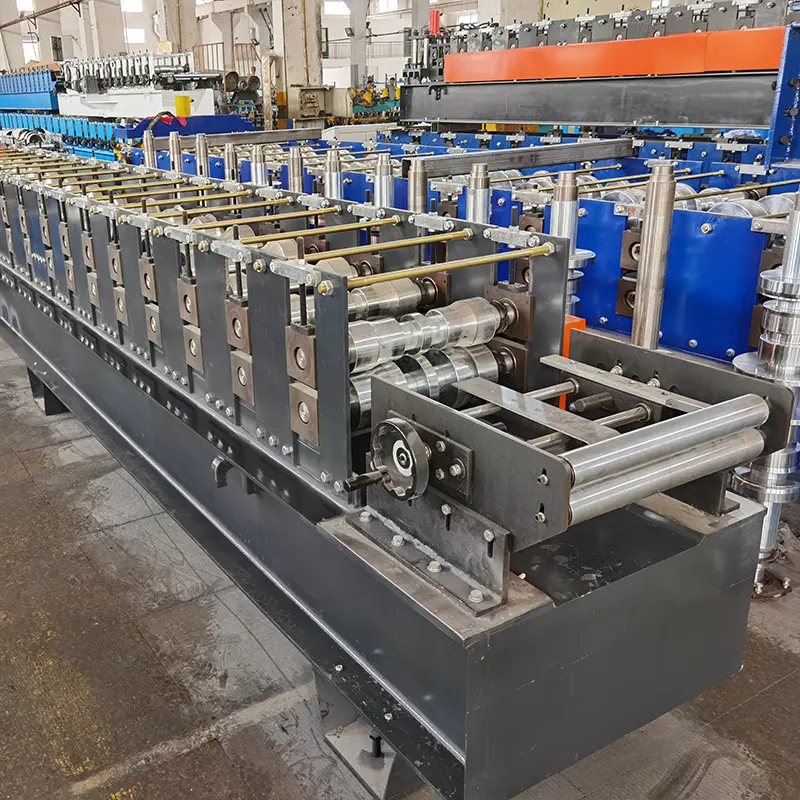
The Role of Drip Edge Roll Forming Machine
Definition and Functionality of Drip Edge Roll Forming Machine
A drip edge roll forming machine is a specialized piece of equipment designed to automate the production of drip edges. It utilizes a roll forming process to shape metal coils into precise and consistent profiles. This machine eliminates the need for manual labor and streamlines the manufacturing process, resulting in increased efficiency and productivity.
Benefits of Using Drip Edge Roll Forming Machine
The utilization of a drip edge roll forming machine offers several benefits for manufacturers and contractors in the roofing industry. Firstly, it allows for the production of drip edges in large quantities, meeting the demands of various construction projects. Secondly, the machine ensures uniformity and precision in the dimensions and shape of the drip edges, guaranteeing consistent quality throughout the manufacturing process. Lastly, it reduces labor costs and minimizes material wastage, making it a cost-effective solution for drip edge production.
Key Features of a Drip Edge Roll Forming Machine
To provide the best results, a drip edge roll forming machine incorporates several key features. These features contribute to its performance, durability, and versatility in manufacturing processes.
Precision and Accuracy
A high-quality drip edge roll forming machine is engineered to deliver precise and accurate profiles consistently. It incorporates advanced control systems and sensors that monitor and adjust the forming process, ensuring dimensional accuracy and preventing variations in the final product.
Customizability and Versatility
Drip edge roll forming machines offer the flexibility to produce various drip edge profiles. With adjustable settings and tooling, manufacturers can easily switch between different profiles, catering to diverse customer requirements. This adaptability allows for customization and innovation in roof design and construction.
Durability and Efficiency
Drip edge roll forming machines are constructed with durable materials and components, designed to withstand heavy production loads and long operational hours. The machines are built for efficiency, minimizing downtime and maximizing output while maintaining consistent quality.
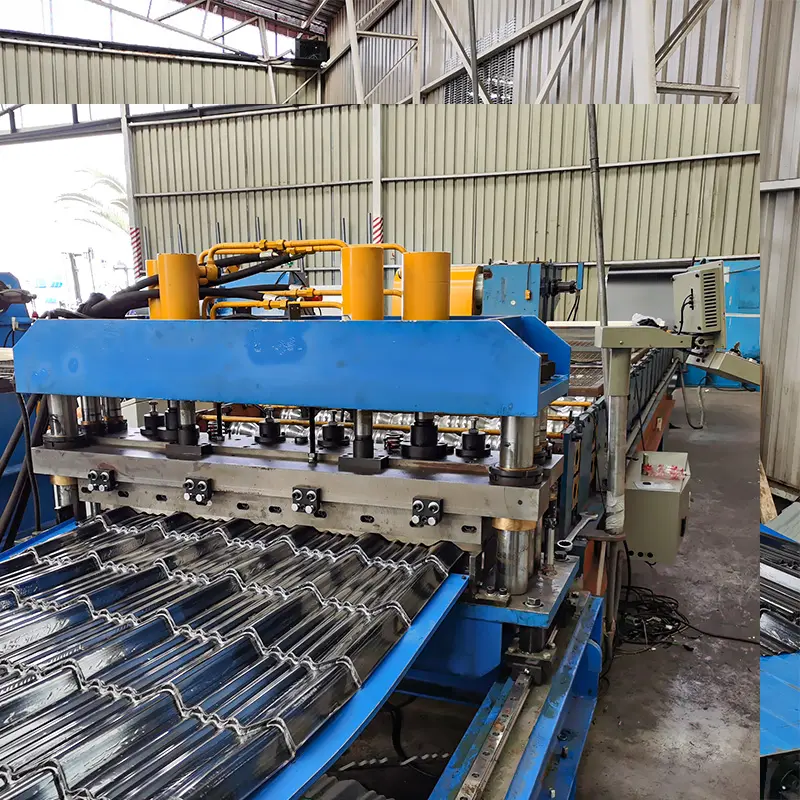
How a Drip Edge Roll Forming Machine Works
A drip edge roll forming machine follows a step-by-step process to transform metal coils into finished drip edges.
Step 1: Material Loading
The process begins with loading the metal coil onto the machine’s decoiler. The coil is securely held and fed into the roll forming section of the machine.
Step 2: Roll Forming Process
The metal coil passes through a series of rolling stations, where it is gradually shaped into the desired drip edge profile. Each station contributes to the forming process, gradually bending and shaping the metal until it reaches its final shape.
Step 3: Cutting and Shearing
Once the desired length of the drip edge is achieved, the machine employs a cutting mechanism to shear the profile from the coil. This ensures precise and accurate dimensions while minimizing material wastage.
Step 4: Output and Stacking
The finished drip edges are then discharged from the machine and stacked for packaging or further processing. The machine’s control system monitors the production output, allowing for seamless workflow and easy integration with downstream operations.
Stay tuned for the second part of the article, which continues with Factors to Consider When Choosing a Drip Edge Roll Forming Machine.
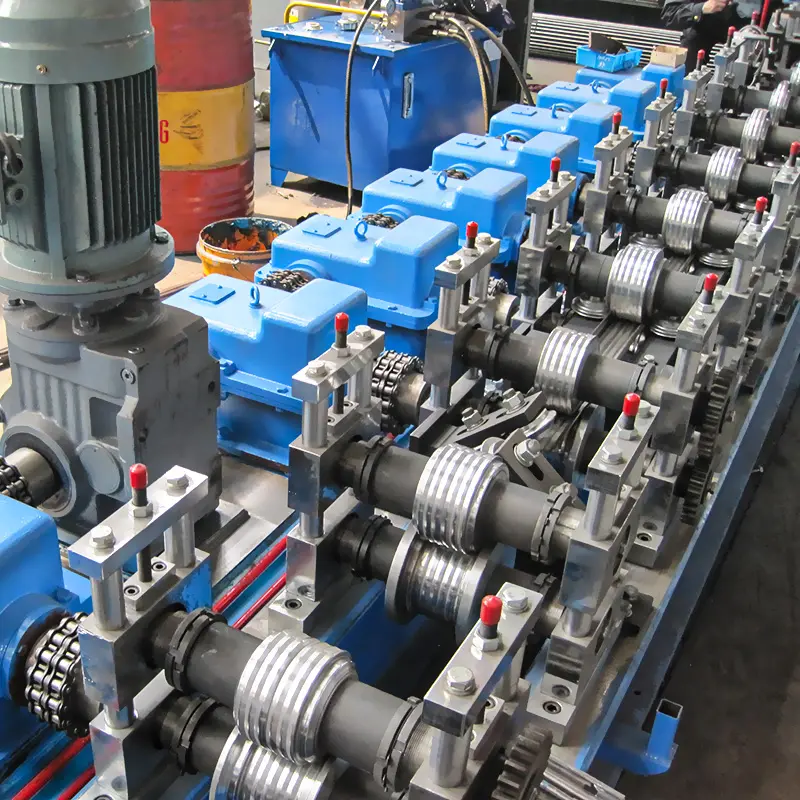
Factors to Consider When Choosing a Drip Edge Roll Forming Machine
When selecting a drip edge roll forming machine for your roofing manufacturing needs, several crucial factors should be taken into account.
Production Capacity
Consider the required production volume for your business. Opt for a machine that can handle the projected workload while maintaining efficiency and consistent quality. A high-capacity machine may be necessary for larger construction projects, while a smaller machine could be sufficient for smaller-scale production.
Material Compatibility
Ensure that the drip edge roll forming machine is compatible with the materials you intend to use. Different roofing materials may require specific machine configurations and tooling to achieve the desired profiles accurately.
Machine Dimensions and Flexibility
Evaluate the physical dimensions of the machine and ensure it fits within your manufacturing facility. Additionally, assess the machine’s flexibility in producing various drip edge profiles. A versatile machine will allow you to adapt to changing market demands and expand your product offerings.
Automation and Control System
A modern drip edge roll forming machine should have advanced automation and a user-friendly control system. Features like touchscreen interfaces, automatic profile changeovers, and remote monitoring enhance productivity and ease of operation.
Advantages of Using a Drip Edge Roll Forming Machine
Increased Production Efficiency
Drip edge roll forming machines streamline the manufacturing process, significantly reducing production time compared to manual methods. With high-speed forming capabilities, the machine can produce a large number of drip edges in a short period, meeting tight project deadlines.
Consistent Quality and Precision
Thanks to automated processes and advanced control systems, drip edge roll forming machines ensure consistent quality and precision in each manufactured piece. This consistency minimizes material waste and ensures that every drip edge meets industry standards and customer expectations.
Cost-effectiveness and Time-saving
By automating the production process, drip edge roll forming machines minimize labor costs and decrease material wastage, making the manufacturing process more cost-effective. Moreover, the reduced production time means quicker project completions and faster turnaround for customers.
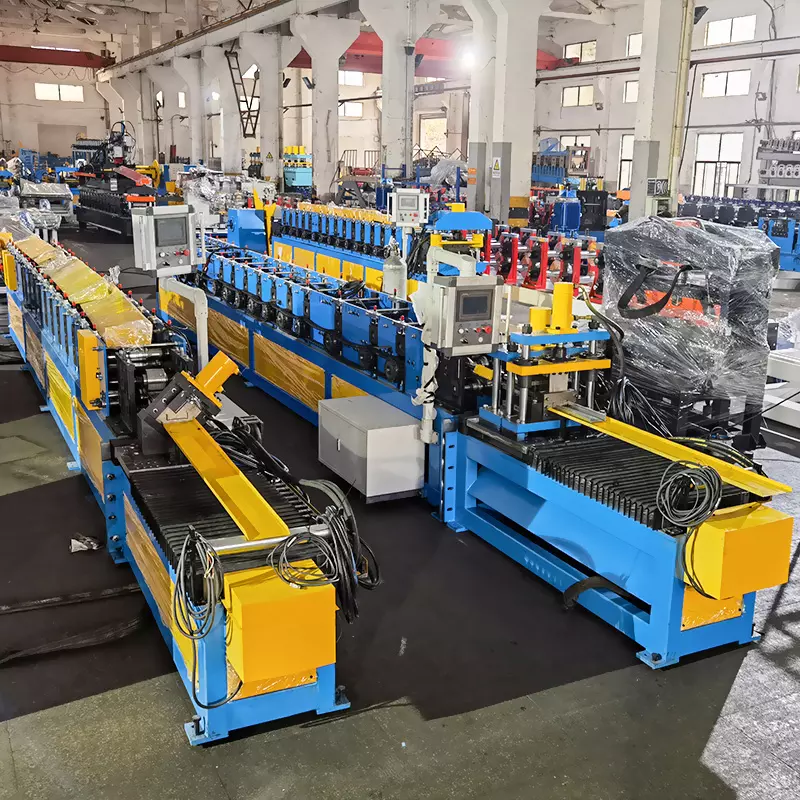
Maintenance and Care Tips for Drip Edge Roll Forming Machines
Regular Cleaning and Lubrication
To maintain the optimal performance of the machine, regular cleaning and lubrication of essential components are necessary. This ensures smooth operation and reduces the risk of wear and tear on the machine’s moving parts.
Inspection and Repair
Regular inspection of the machine allows early detection of any issues or wear. Prompt repair and replacement of worn-out parts prevent costly breakdowns and ensure continuous production.
Operator Training and Safety Measures
Proper training of machine operators is essential to ensure safe and efficient operation. Implementing appropriate safety measures reduces the risk of accidents and injuries in the workplace.
Industry Applications of Drip Edge Roll Forming Machines
Residential Roofing
In residential construction, drip edge roll forming machines play a vital role in manufacturing the drip edges used to protect the roofs of houses and other residential structures. The machines contribute to the overall quality and durability of the roofing system.
Commercial Roofing
For commercial buildings and establishments, drip edge roll forming machines are utilized to produce drip edges that safeguard the roofing against water damage. The efficiency of the machines is especially beneficial for large-scale commercial projects.
Industrial Roofing
In industrial settings, where large roofs require robust protection, drip edge roll forming machines are indispensable. These machines ensure the consistent supply of high-quality drip edges for industrial roofing applications.
Future Trends and Innovations in Drip Edge Roll Forming Machines
Advanced Control Systems
Advancements in control systems will lead to even greater precision and automation in drip edge roll forming machines. Smart technologies will optimize the forming process and provide real-time data for analysis and improvement.
Integration of Artificial Intelligence
The integration of artificial intelligence will revolutionize drip edge roll forming machines, allowing them to adapt to various roofing materials, profiles, and customer specifications automatically. This level of intelligence will enhance overall productivity and flexibility.
Enhanced Material Handling Capabilities
Future machines may feature improved material handling systems, reducing manual intervention and increasing the efficiency of coil loading and unloading processes.
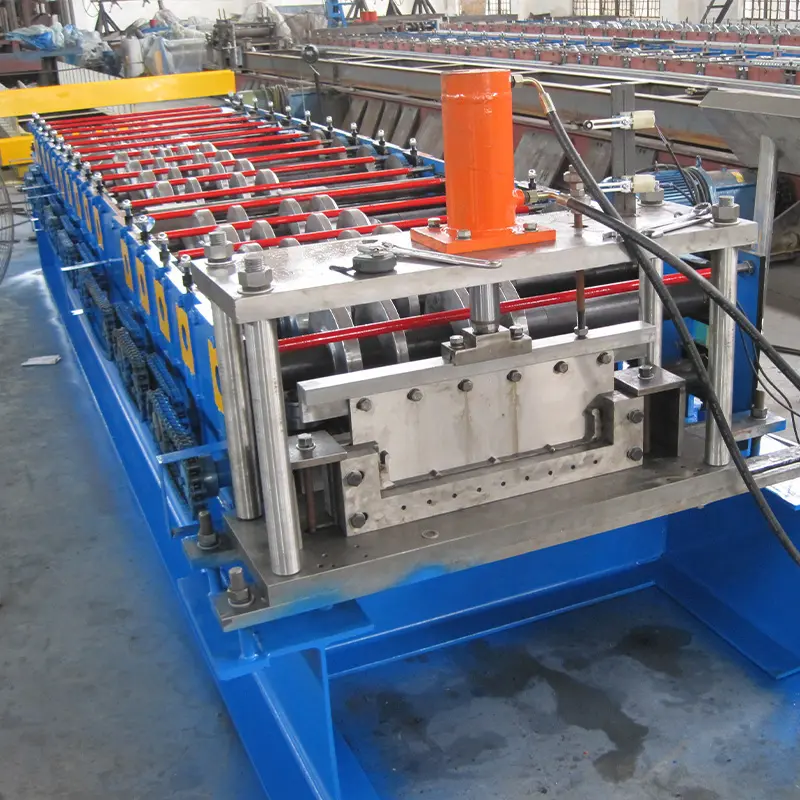
निष्कर्ष
Drip edge roll forming machines have revolutionized the roofing industry, providing efficient, cost-effective, and precise manufacturing solutions for drip edges. By automating the production process, these machines ensure consistent quality, increased productivity, and time-saving advantages. Manufacturers and contractors can benefit from incorporating drip edge roll forming machines into their operations, providing superior protection for roofs and enhancing their reputation in the market.
FAQs
Q1: Can a drip edge roll forming machine produce different profiles?
A1: Yes, most modern drip edge roll forming machines are designed to be versatile, capable of producing various drip edge profiles to suit different roofing requirements.
Q2: What materials can be used with a drip edge roll forming machine?
A2: Drip edge roll forming machines can work with various materials, including galvanized steel, aluminum, and stainless steel, depending on the specific requirements of the roofing project.
Q3: How long does it take to set up and operate a drip edge roll forming machine?
A3: The setup time varies depending on the complexity of the drip edge profile and the operator’s familiarity with the machine. Once set up, the machine operates continuously, significantly reducing production time.
Q4: Are drip edge roll forming machines suitable for both small and large-scale production?
A4: Yes, drip edge roll forming machines are suitable for both small and large-scale production. They can be tailored to match the production volume required by different roofing projects.
Q5: Can a drip edge roll forming machine be customized according to specific requirements?
A5: Yes, manufacturers often offer customization options for drip edge roll forming machines to meet specific customer needs and preferences.