Definition and operation of roll forming and press brake machines
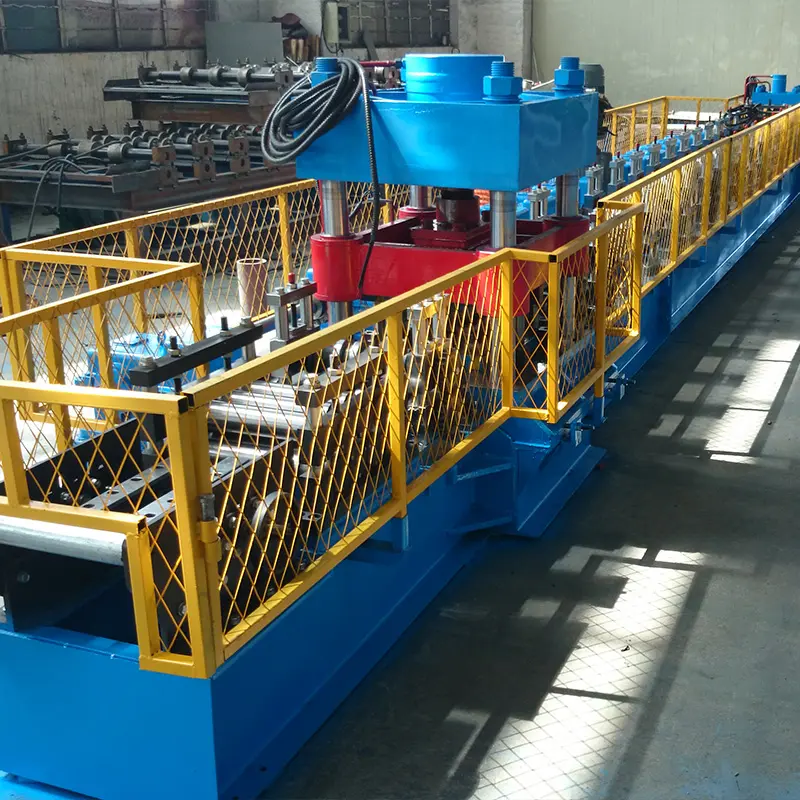
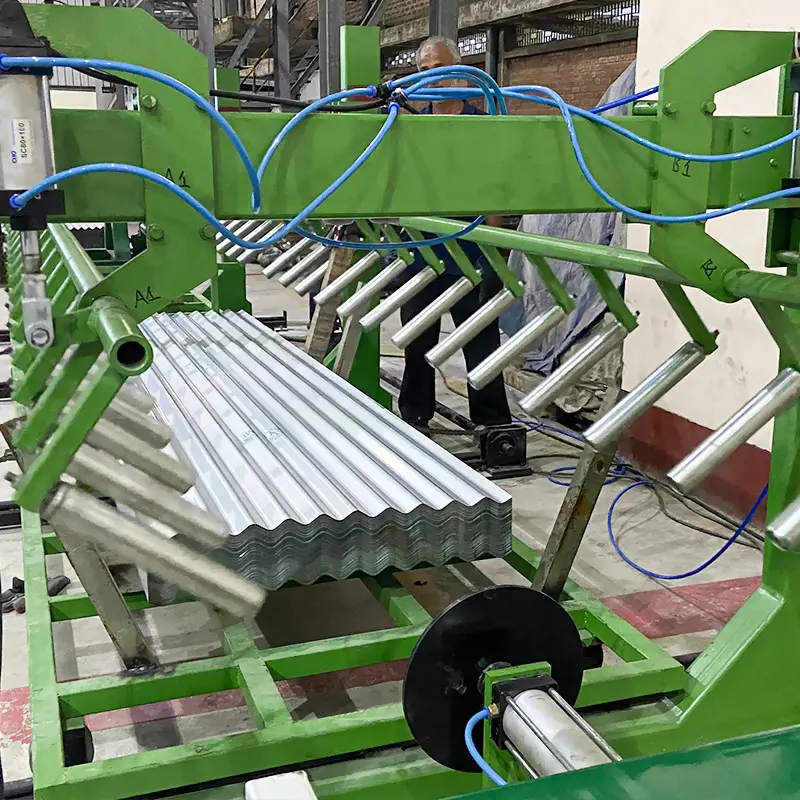
Roll forming and press brake machines are both commonly used in the metalworking industry to shape and form metal sheets into desired shapes and sizes. Here’s a brief explanation of each machine and how they work:
Roll forming is a continuous process of bending metal strips or sheets into specific shapes by passing them through a series of rollers. The rollers are designed with progressively larger contours that gradually bend and form the metal strip into the desired shape. The machines can create complex shapes and profiles, and are commonly used in the production of components for the construction, automotive, and appliance industries.
Press brake machines:
ए press brake is a machine tool used to bend and form metal sheets into various shapes, such as angles, channels, and boxes. The machine uses a hydraulic or mechanical press to apply a force onto the metal sheet and bend it into the desired shape. Press brake machines can handle a wide range of materials and thicknesses, and are commonly used in metalworking shops for applications such as metal forming, metal cutting, and metal punching.
In summary, roll forming machines use a series of rollers to continuously bend metal strips into desired shapes, while press brake machines use a hydraulic or mechanical press to bend and form metal sheets into various shapes.
Advantages and disadvantages of roll forming
-
विद्युत कैबिनेट फ्रेम रोल बनाने की मशीन
-
दीन रेल रोल बनाने की मशीन
-
केबल सीढ़ी रोल बनाने की मशीन
-
पीवी माउंटिंग ब्रैकेट सी शेप प्रोफाइल रोल बनाने की मशीन
-
केबल ट्रे रोल बनाने की मशीन
-
पीवी माउंटिंग ब्रैकेट रोल बनाने की मशीन (एचएटी / ओमेगा प्रोफाइल)
-
पीवी माउंटिंग ब्रैकेट जेड शेप प्रोफाइल रोल बनाने की मशीन
-
सौर बढ़ते अकड़ चैनल रोल बनाने की मशीन
-
स्ट्रट चैनल रोल बनाने की मशीन
Roll forming machines offer several advantages and disadvantages to consider before deciding if they are the right choice for your specific needs. Here are some of the benefits and drawbacks of using the machines:
Advantages of roll forming:
- High Efficiency: the machines can produce complex shapes and profiles quickly and continuously, making them highly efficient for high-volume production runs.
- Consistent Quality: the machines are known for their ability to produce consistent, high-quality parts with tight tolerances and minimal variation.
- Minimal Material Waste: the machines typically produce minimal scrap material, which can help reduce material costs and waste.
- Low Labor Costs: the machines are highly automated and require minimal manual labor, which can help reduce labor costs.
Disadvantages of roll forming:
- High Setup Costs: the machines can be expensive to set up and require specialized tooling, which can be costly and time-consuming to design and manufacture.
- Limited Flexibility: the machines are best suited for high-volume production runs of consistent shapes and profiles. They may not be suitable for small production runs or custom projects.
- Limited Material Thickness: the machines are typically best suited for thin-gauge materials and may not be suitable for thicker materials.
- Limited Design Options: the machines are limited in their ability to produce complex designs and shapes.
In summary, the machines offer high efficiency, consistent quality, minimal material waste, and low labor costs, but they may have high setup costs, limited flexibility, limited material thickness, and limited design options.
Advantages and disadvantages of press brakes
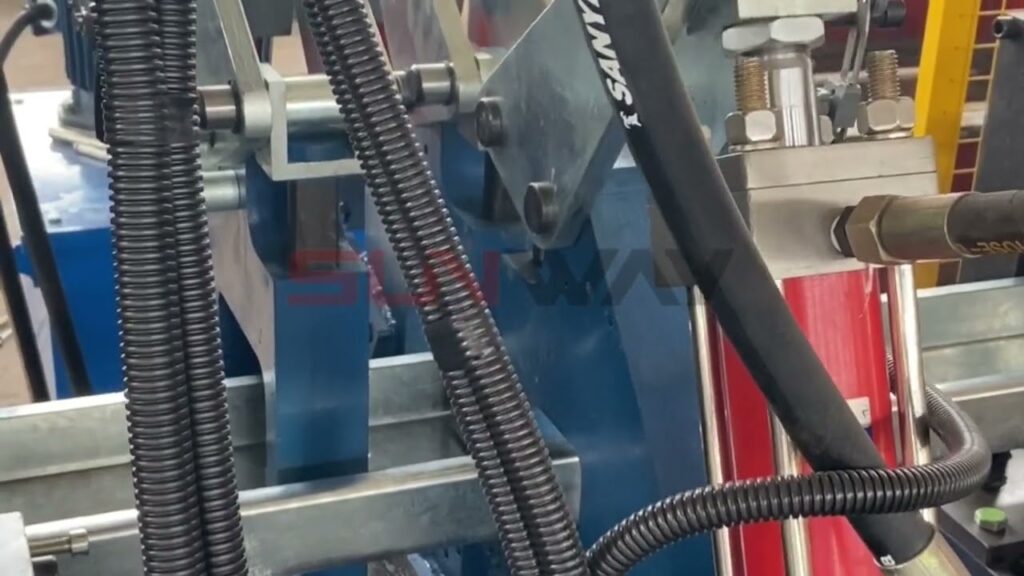
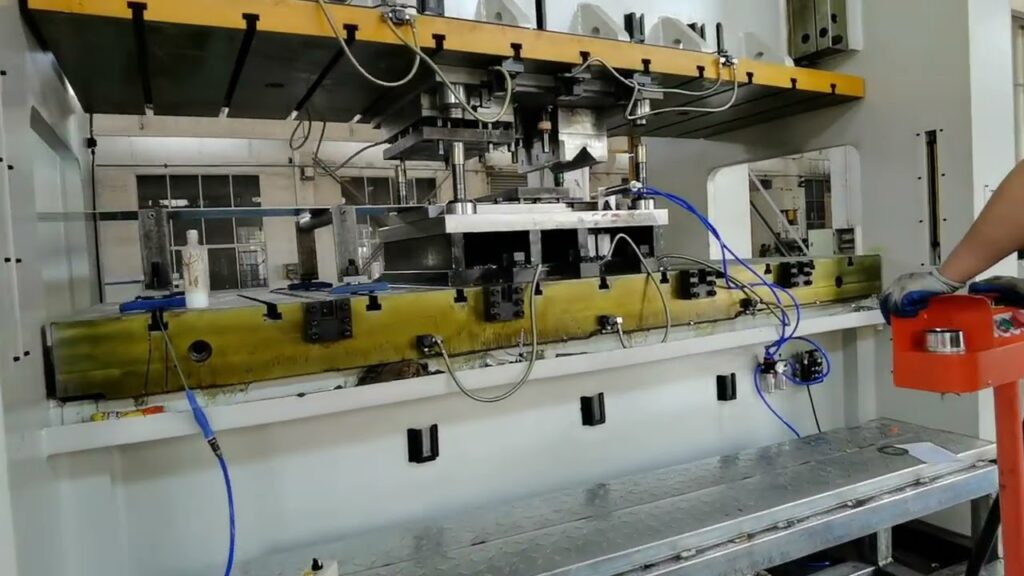
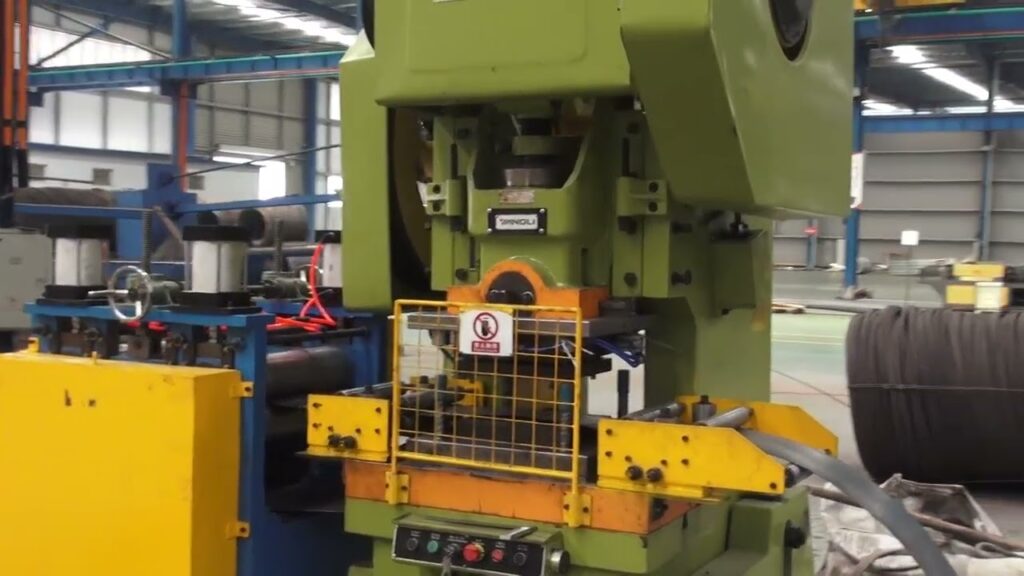
Press brake machines offer several advantages and disadvantages to consider before deciding if they are the right choice for your specific needs. Here are some of the benefits and drawbacks of using press brake machines:
Advantages of press brakes:
- Versatility: Press brake machines can handle a wide range of materials and thicknesses, making them suitable for a variety of applications.
- Customization: Press brakes can be used to create custom shapes and profiles, making them ideal for small production runs and custom projects.
- Flexibility: Press brakes are more flexible than roll forming machines and can produce a wider variety of shapes and profiles.
- Cost-Effective: Press brake machines are often more affordable than roll forming machines, making them a cost-effective choice for small to medium-sized businesses.
Disadvantages of press brakes:
- Efficiency: Press brakes may not be as efficient as roll forming machines, as they require more manual labor to set up and operate.
- Material Waste: Press brakes can produce more scrap material than roll forming machines, which can increase material costs and waste.
- Inconsistent Quality: The quality of the parts produced by a press brake machine can vary more than those produced by a roll forming machine.
- Space Requirements: Press brake machines typically require more space to operate than roll forming machines.
In summary, press brake machines offer versatility, customization, flexibility, and cost-effectiveness, but they may be less efficient than roll forming machines, produce more material waste, have inconsistent quality, and require more space to operate.
Applications of roll forming & press brakes
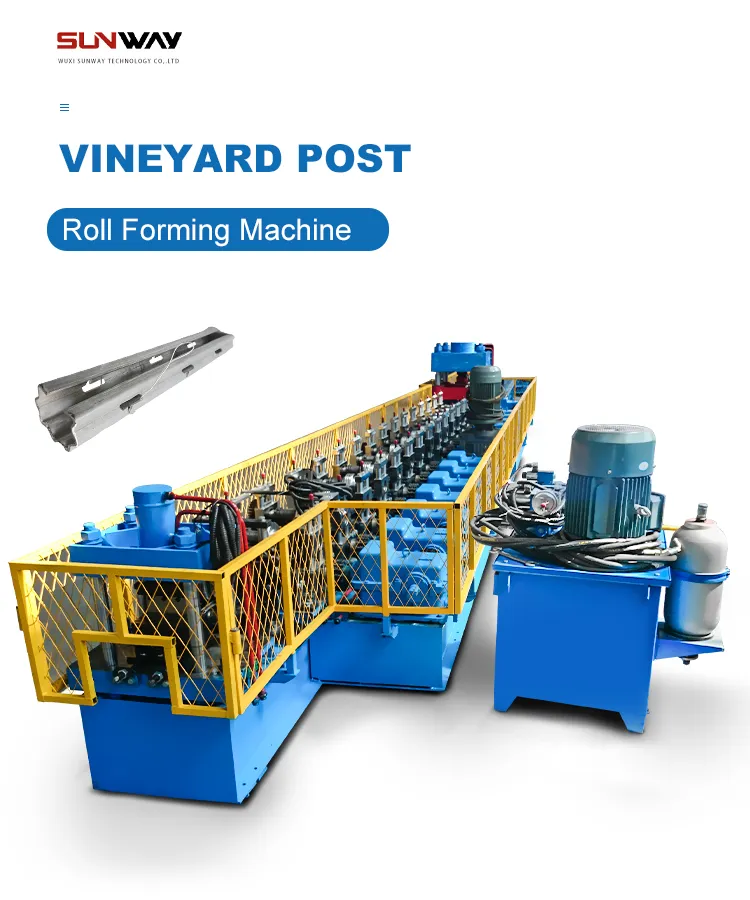
Roll forming and press brake machines are used in various applications in the metalworking industry. Here are some of the specific applications where these machines are commonly used:
Applications of roll forming machines:
- Automotive Industry: the machines are used to produce components such as door frames, seat tracks, and bumper beams for automobiles.
- Construction Industry: the machines are used to produce components such as metal roofing and siding, window frames, and gutters for buildings.
- Appliance Industry: the machines are used to produce components such as refrigerator door frames, oven racks, and washer/dryer components for household appliances.
- Shelving and Storage Industry: the machines are used to produce components such as metal shelves, storage racks, and filing cabinets.
- Solar Panel Industry: the machines are used to produce components such as racking systems and mounting brackets for solar panels.
Applications of press brake machines:
- Metal Fabrication: Press brake machines are used in metal fabrication shops to create custom shapes and profiles for various applications.
- Metal Enclosures: Press brake machines are used to create metal enclosures for electrical equipment, machinery, and other industrial applications.
- Metal Brackets: Press brake machines are used to create metal brackets for a variety of applications, including automotive, aerospace, and construction.
- Signage Industry: Press brake machines are used to create metal signs for various applications, such as building signage, directional signage, and safety signage.
- Furniture Industry: Press brake machines are used to create metal frames for furniture, such as tables, chairs, and shelving.
In summary, roll forming machines are commonly used in the automotive, construction, appliance, shelving and storage, and solar panel industries, while press brake machines are commonly used in metal fabrication, metal enclosures, metal brackets, signage, and furniture industries.
Factors to consider when choosing between roll forming and press brake machines
When deciding whether to use roll forming or press brake machines for a specific application, there are several factors to consider. Here are some of the key factors to keep in mind:
- Production Volume: Roll forming machines are ideal for high-volume production runs of consistent shapes and profiles, while press brake machines are more suitable for small to medium-sized production runs and custom projects.
- Material Type: Roll forming machines are typically best suited for thin-gauge materials, while press brake machines can handle a wide range of materials and thicknesses.
- Required Precision: Roll forming machines are known for their ability to produce consistent, high-quality parts with tight tolerances and minimal variation, while press brake machines may have more variation and require more manual labor to achieve the desired precision.
- Available Space: Roll forming machines typically require less space to operate than press brake machines, which can be important for businesses with limited space.
- Tooling Costs: Roll forming machines can have high tooling costs, as specialized tooling is required for each profile or shape produced, while press brake machines can use standard tooling for a wider range of shapes and profiles.
- Design Complexity: Roll forming machines are limited in their ability to produce complex shapes and designs, while press brake machines can create custom shapes and profiles.
In summary, when choosing between roll forming and press brake machines, it’s important to consider factors such as production volume, material type, required precision, available space, tooling costs, and design complexity. By carefully considering these factors, businesses can make an informed decision about which machine is best suited for their specific needs.