परिचय
In the world of metal fabrication, the use of advanced machinery has significantly transformed the manufacturing process. One such machine that has gained immense popularity is the aluminium roll forming machine. This article dives into the details of aluminium roll forming machines, exploring their functionality, benefits, applications, and various types. Additionally, it provides insights into important factors to consider when choosing an aluminium roll forming machine, maintenance tips, troubleshooting techniques, safety precautions, industry trends, and selecting a reliable manufacturer.
What is an Aluminium Roll Forming Machine?
An aluminium roll forming machine is a specialized piece of equipment used in the metal fabrication industry to shape flat sheets of aluminium into desired profiles. It employs a continuous bending process, where the aluminium sheet is passed through a series of rollers, gradually forming it into the desired shape. The machine utilizes a combination of pressure, tension, and precise control to achieve accurate and consistent results.
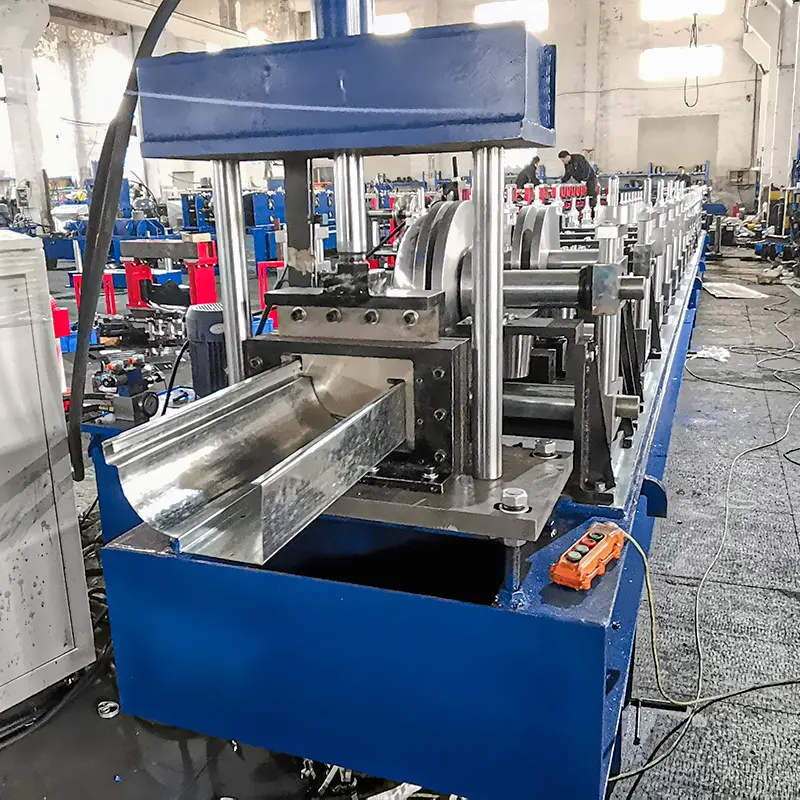
How Does an Aluminium Roll Forming Machine Work?
The working principle of an aluminium roll forming machine involves several essential components. First, the machine receives a flat aluminium sheet, usually in coil form, which is then fed into the machine. The sheet passes through a series of rollers, each designed to gradually bend the material to the desired shape. These rollers are precisely positioned and adjustable, allowing for the creation of complex profiles.
As the sheet progresses through the rollers, it undergoes incremental shaping, with each roll applying pressure and bending the material further. The machine’s design ensures that the aluminium sheet retains its structural integrity while undergoing the forming process. To maintain accuracy, the machine may incorporate sensors and feedback mechanisms that detect any deviations and make necessary adjustments.
Benefits of Using an Aluminium Roll Forming Machine
Using an aluminium roll forming machine offers several advantages over traditional fabrication methods. These include:
- Cost Efficiency: Aluminium roll forming machines streamline the production process, reducing labor costs and material waste. The continuous forming process minimizes the need for manual intervention, leading to higher productivity and lower overall production costs.
- Versatility: Aluminium roll forming machines can create a wide range of complex profiles, catering to diverse industry requirements. Whether it’s simple shapes or intricate designs, these machines provide flexibility in meeting specific project needs.
- Consistency and Accuracy: With precise control over the shaping process, aluminium roll forming machines ensure consistent results, maintaining tight tolerances throughout the production run. This level of accuracy is crucial, especially for applications that demand high-quality finished products.
- Time Efficiency: The continuous operation of aluminium roll forming machines enables faster production cycles compared to other forming methods. This time-saving advantage is particularly beneficial when dealing with large production volumes.
- Material Optimization: Roll forming minimizes material waste by utilizing the entire length of the aluminium coil efficiently. The ability to form complex profiles from a single sheet maximizes material usage and reduces scrap.
- Strength and Durability: Aluminium roll forming enhances the strength and durability of the finished products. The process work-hardens the material, resulting in profiles with excellent structural integrity and resistance to deformation.
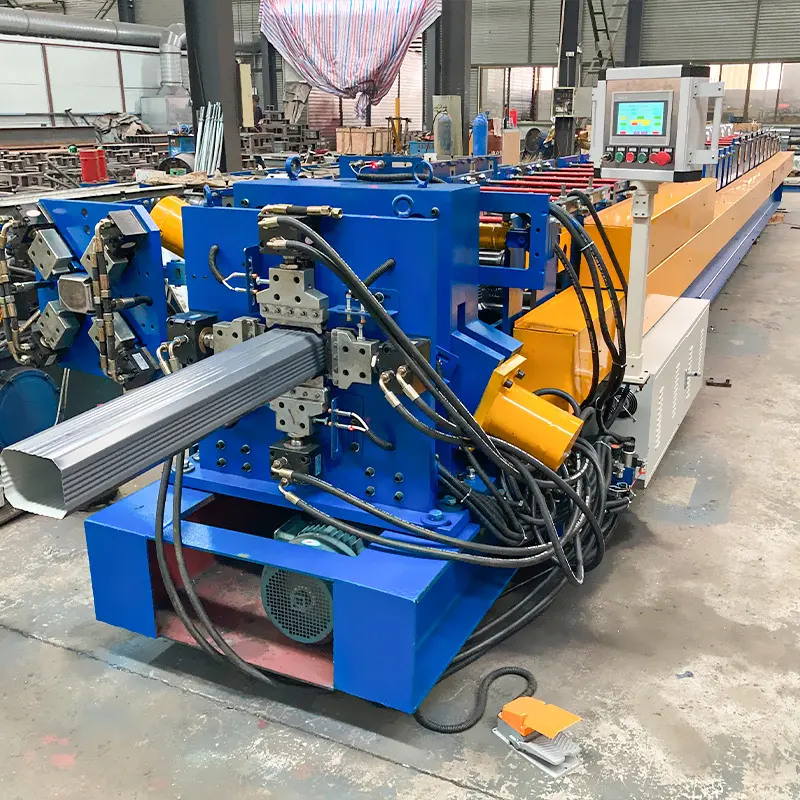
Types of Aluminium Roll Forming Machines
Aluminium roll forming machines come in various types, each suited for specific applications. The key types include:
Single-Station Roll Forming Machine
The single-station roll forming machine is a basic configuration consisting of a single set of rollers. It is suitable for simpler profiles with limited variations.
Continuous Roll Forming Machine
The continuous roll forming machine incorporates multiple sets of rollers arranged in a sequence. It can produce complex profiles with varying shapes and sizes.
Duplex Roll Forming Machine
The duplex roll forming machine is equipped with two sets of rollers, allowing for the simultaneous forming of two profiles. This type of machine offers increased productivity and efficiency.
Custom Roll Forming Machine
Custom roll forming machines are designed specifically for unique or highly specialized profiles. They are tailored to meet specific industry requirements and can be highly automated.
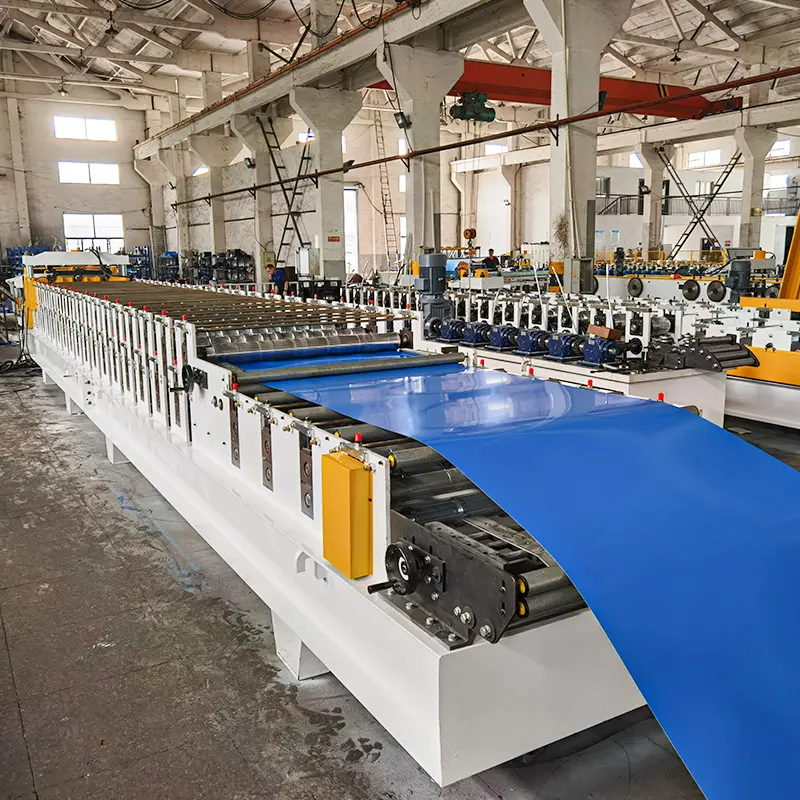
Applications of Aluminium Roll Forming Machines
Aluminium roll forming machines find extensive use in various industries due to their versatility and efficiency. Some common applications include:
- Construction: Aluminium roll-formed profiles are widely used in the construction industry for applications such as roofing, cladding, framing, and curtain walls. The lightweight yet sturdy nature of aluminium makes it ideal for these applications.
- Automotive: Aluminium roll-formed components are used in the automotive industry for body panels, trims, and structural parts. The high strength-to-weight ratio of aluminium provides fuel efficiency and improves overall vehicle performance.
- Appliances: Aluminium profiles produced by roll forming machines are utilized in the manufacturing of appliances such as refrigerators, air conditioners, and washing machines. The corrosion-resistant properties of aluminium make it a suitable choice for these applications.
- Furniture: Roll-formed aluminium profiles are commonly used in the furniture industry for items such as frames, shelves, and decorative trims. The ability to create intricate designs and shapes makes aluminium a popular choice.
- Electronics: Aluminium roll-formed parts are employed in the electronics industry for housing components, heat sinks, and structural supports. The excellent thermal conductivity of aluminium assists in dissipating heat effectively.
- Energy and Renewable Resources: Aluminium profiles find applications in the energy sector for solar panel frames, wind turbine components, and electrical enclosures. The lightweight nature of aluminium aids in installation and reduces energy consumption.
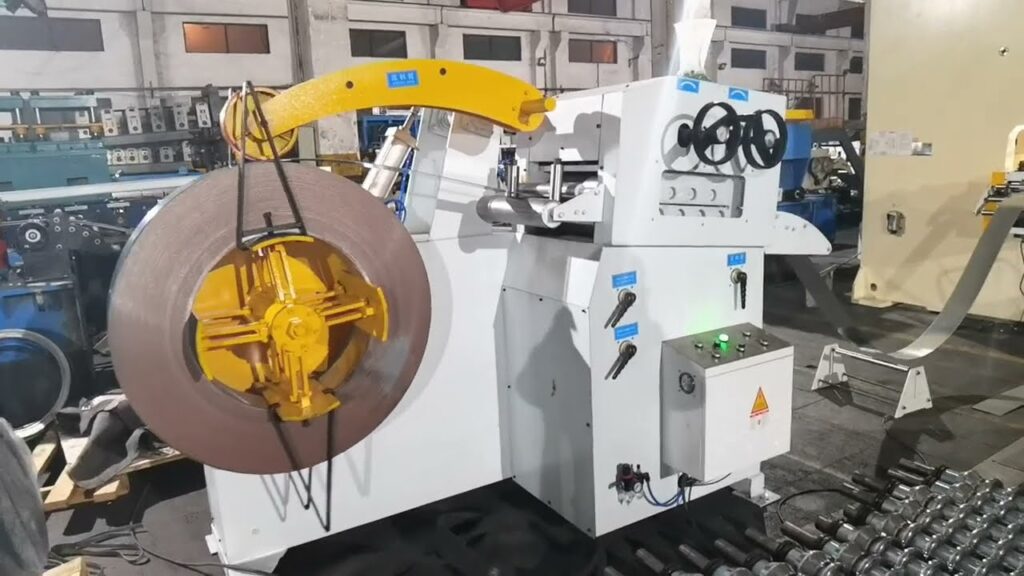
Factors to Consider When Choosing an Aluminium Roll Forming Machine
When selecting an aluminium roll forming machine for your specific needs, several factors should be taken into account:
Material Thickness and Strength
Consider the range of material thicknesses and strengths that the machine can handle. Ensure that the machine is capable of forming aluminium sheets of the desired gauge and hardness for your intended applications.
Profile Complexity
Evaluate the machine’s capabilities in terms of forming complex profiles. Determine if it can accommodate the intricate shapes and designs required for your specific projects.
Production Volume
Consider the production volume you expect to achieve. Choose a machine that can meet your desired output and production speed requirements. High-volume production may require machines with higher automation levels.
Customization Options
If your projects require unique or specialized profiles, opt for a machine that offers customization options. This ensures that the machine can be tailored to meet your specific needs.
Automation Level
Evaluate the level of automation offered by the machine. Higher automation levels increase efficiency and reduce the need for manual intervention, resulting in improved productivity.
Cost
Consider your budget constraints and weigh the machine’s features, capabilities, and long-term benefits against the initial investment cost. It’s essential to find a balance between affordability and quality.
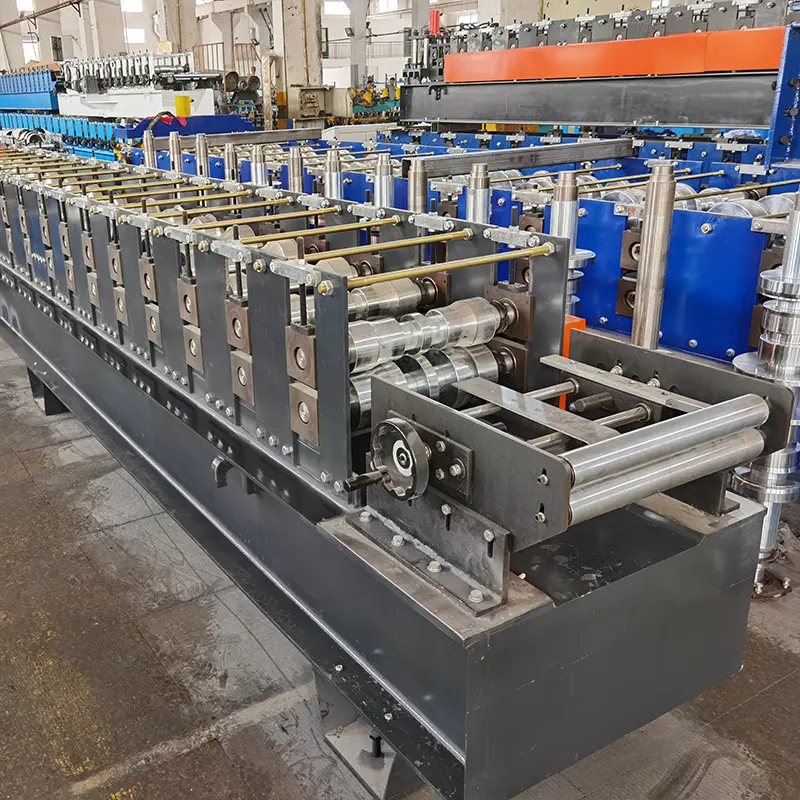
Maintenance and Care for Aluminium Roll Forming Machines
To ensure optimal performance and longevity of your aluminium roll forming machine, regular maintenance and care are crucial. Here are some maintenance tips:
- Routine Inspections: Regularly inspect the machine for any signs of wear, loose components, or abnormalities. Address any issues promptly to prevent further damage.
- Lubrication: Follow the manufacturer’s guidelines for lubricating the machine’s moving parts. Proper lubrication reduces friction, extends component life, and ensures smooth operation.
- Cleaning: Keep the machine clean and free from debris, dust, or metal shavings. Regularly remove any accumulated residue to maintain optimal performance.
- Alignment and Calibration: Periodically check and adjust the machine’s alignment and calibration to ensure accurate and consistent forming results.
- Operator Training: Provide comprehensive training to operators to ensure they understand the machine’s operation, safety protocols, and maintenance procedures.
Common Issues and Troubleshooting
While aluminium roll forming machines are highly reliable, occasional issues may arise. Here are some common problems and their troubleshooting steps:
Material Jamming
- Issue: The aluminium sheet gets stuck or jams during the forming process.
- Troubleshooting: Check for any obstructions, misaligned rollers, or improper tension settings. Clear the jammed material, realign the rollers, and adjust the tension as necessary.
Uneven Forming
- Issue: The formed profiles exhibit variations or irregularities in shape or dimensions.
- Troubleshooting: Verify the roller alignment, material feeding mechanism, and pressure settings. Adjust and calibrate as needed to ensure uniform forming.
Excessive Noise or Vibration
- Issue: The machine produces loud noises or excessive vibrations during operation.
- Troubleshooting: Inspect the machine for loose or worn-out components. Tighten any loose connections, replace damaged parts, and ensure proper machine balance.
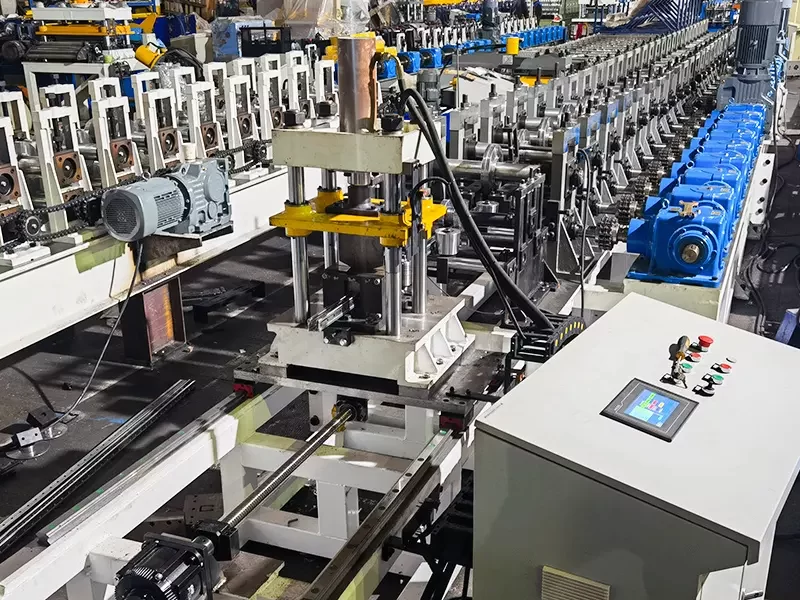
Safety Considerations for Operating an Aluminium Roll Forming Machine
Operating an aluminium roll forming machine requires adherence to strict safety protocols. Here are some important safety considerations:
- Training and Certification: Ensure that operators are properly trained and certified in operating the machine and following safety procedures.
- Protective Equipment: Provide operators with appropriate personal protective equipment (PPE), including safety glasses, gloves, and hearing protection.
- Machine Guarding: Install safety guards and barriers to prevent access to moving parts and mitigate the risk of accidents.
- Emergency Stop: Equip the machine with an easily accessible emergency stop button to immediately halt operations in case of emergencies.
- Regular Inspections: Conduct routine inspections to identify and address any safety hazards or potential risks.
Industry Trends and Innovations in Aluminium Roll Forming Machines
The aluminium roll forming machine industry is continually evolving, driven by technological advancements and market demands. Some notable trends and innovations include:
- Advanced Control Systems: Integration of advanced control systems and automation technologies, such as programmable logic controllers (PLCs) and human-machine interfaces (HMIs), for enhanced precision and productivity.
- Quick Changeover: Development of quick-change tooling systems that allow for faster profile changeovers, reducing downtime and increasing production efficiency.
- Energy Efficiency: Implementation of energy-saving features, such as regenerative drives and optimized power consumption, to reduce environmental impact and operating costs.
- Digitalization and Data Analytics: Utilization of data-driven insights and predictive analytics to optimize machine performance, improve product quality, and enhance overall production processes.
- Customization Capabilities: Advancements in machine design and technology that enable highly customized solutions, catering to unique customer requirements and diverse industry applications.
Choosing a Reliable Manufacturer for Aluminium Roll Forming Machines
Selecting a reputable and reliable manufacturer is crucial when investing in an aluminium roll forming machine. Consider the following factors:
- Experience and Expertise: Look for manufacturers with extensive experience in designing and manufacturing roll forming machines. Check their track record and customer reviews.
- Customization and Flexibility: Choose a manufacturer that can provide customized solutions tailored to your specific needs, ensuring the machine meets your unique requirements.
- Quality and Performance: Assess the quality of the machines produced by the manufacturer. Look for certifications and industry standards compliance to ensure reliable performance.
- After-Sales Support: Inquire about the manufacturer’s after-sales support, including technical assistance, spare parts availability, and warranty coverage.
- Customer References: Request customer references and testimonials to gain insights into the manufacturer’s reputation and customer satisfaction.
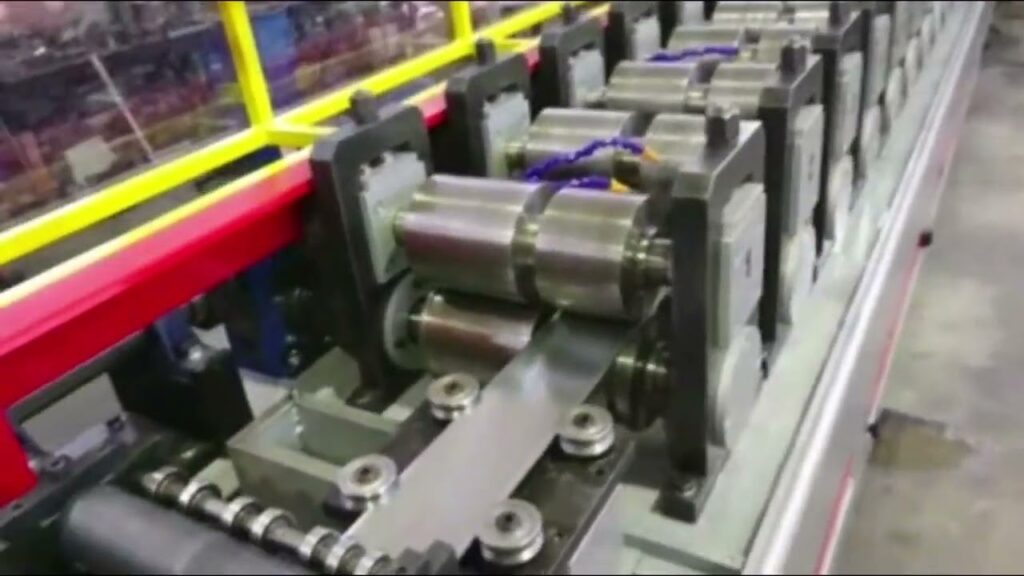
निष्कर्ष
Aluminium roll forming machines have revolutionized the metal fabrication industry, offering cost-efficiency, versatility, and high-quality production. By understanding the working principle, benefits, types, applications, and maintenance requirements of these machines, you can make informed decisions when incorporating them into your manufacturing processes. Remember to prioritize safety, consider industry trends, and choose a reputable manufacturer to ensure optimal results and a competitive edge in the market.
FAQs
Q1. Can aluminium roll forming machines form other metals besides aluminium?
Yes, depending on the machine’s design and specifications, aluminium roll forming machines can also form other metals such as steel, stainless steel, copper, and more.
Q2. How long does it take to change the profile on an aluminium roll forming machine?
The time required to change the profile on an aluminium roll forming machine varies depending on the complexity of the profile and the machine’s design. Quick-change tooling systems have reduced changeover times significantly.
Q3. Are aluminium roll-formed profiles suitable for outdoor applications?
Yes, aluminium roll-formed profiles are commonly used in outdoor applications. Aluminium’s corrosion resistance and durability make it a suitable choice for various weather conditions.
Q4. Can I automate an aluminium roll forming machine for higher productivity?
Yes, many aluminium roll forming machines offer automation options, such as material feeding systems, length measurement, and cutting mechanisms. Automation can significantly enhance productivity and efficiency.
Q5. What kind of training is necessary to operate an aluminium roll forming machine?
Operators of aluminium roll forming machines require comprehensive training on machine operation, safety protocols,maintenance procedures, and troubleshooting techniques. Training should cover topics such as material handling, roller adjustment, machine setup, and quality control measures. It’s important to ensure that operators are well-versed in safety practices and understand the specific requirements of the machine they will be operating.