परिचय
In the construction industry, efficient and accurate manufacturing processes are crucial to ensure the quality and durability of building components. One such process is the roll forming technique, widely used for creating roof panels. A roof panel roll forming machine plays a vital role in this process by producing consistent, high-quality roof panels in a cost-effective manner. This article will explore the various aspects of roof panel roll forming machines, including their advantages, types, selection factors, operation steps, maintenance tips, troubleshooting, safety precautions, and future trends.
What is a Roof Panel Roll Forming Machine?
A roof panel roll forming machine is a specialized piece of equipment used to transform flat metal coils into finished roof panels with a specific profile and shape. It operates by passing the metal coil through a series of rolls and dies, gradually forming the desired panel shape. The machine can produce roof panels of different lengths, thicknesses, and profiles, allowing for customization to meet specific project requirements.
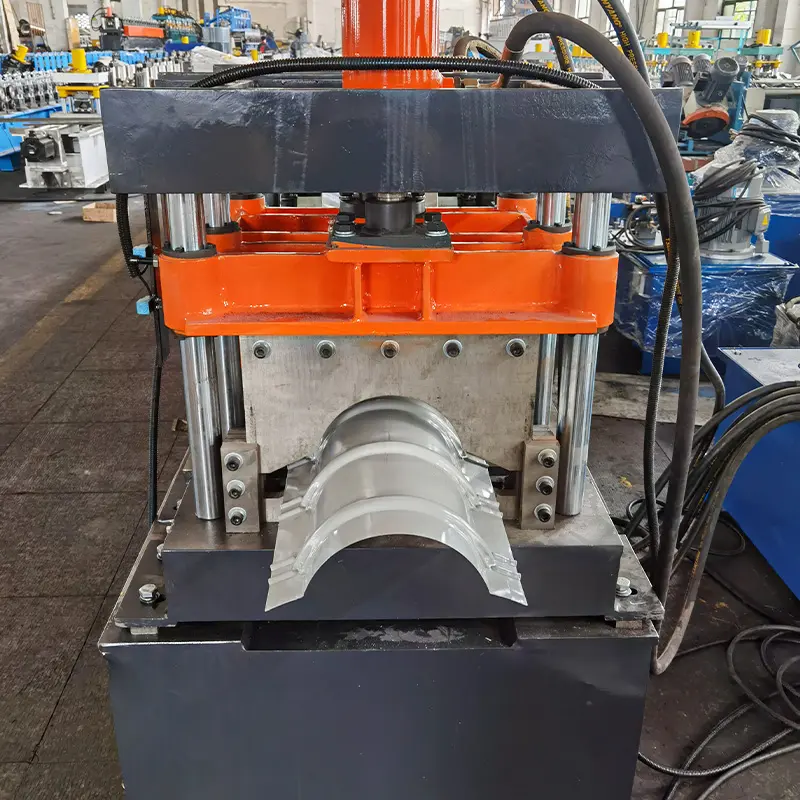
Advantages of Using a Roof Panel Roll Forming Machine
Cost Efficiency
One of the primary advantages of using a roof panel roll forming machine is its cost efficiency. By automating the panel manufacturing process, the machine reduces labor costs and increases production speed, resulting in significant cost savings for manufacturers. Additionally, the machine minimizes material waste, as it precisely cuts the panels to the required length, reducing scrap and optimizing material usage.
Customization Options
Roof panel roll forming machines offer a wide range of customization options. Manufacturers can easily adjust the machine settings to produce roof panels of different lengths, widths, and profiles, allowing for versatility in design and meeting diverse customer requirements. This flexibility makes the machine ideal for both standard panel production and custom projects.
गति और दक्षता
Compared to traditional manual methods, roof panel roll forming machines offer exceptional speed and efficiency. Once set up, the machine can continuously produce roof panels at a high rate, significantly increasing productivity. The automated process ensures consistent panel quality and precise dimensions, eliminating human errors that may occur with manual fabrication.
Durability and Quality
Roof panels manufactured using roll forming machines exhibit excellent durability and quality. The machine applies consistent pressure and precision forming techniques, resulting in uniform panel thickness and accurate profiles. The panels are free from deformations, ensuring a tight fit during installation and improved weather resistance.
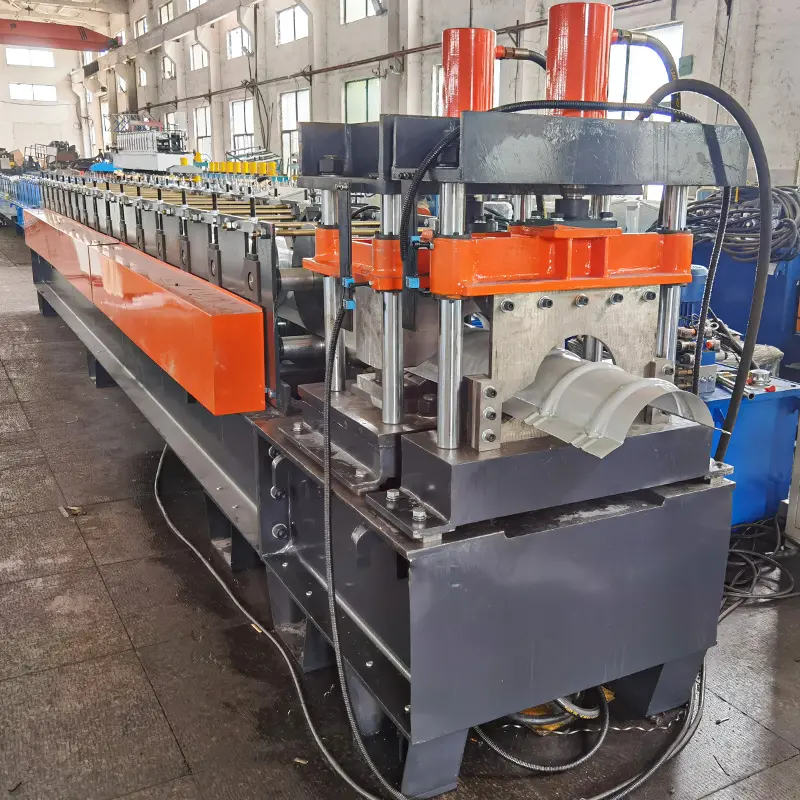
Types of Roof Panel Roll Forming Machines
There are different types of roof panel roll forming machines available, each designed for specific manufacturing requirements. The following are the most common types:
Single-Layer Roll Forming Machines
Single-layer roll forming machines are the simplest type and are suitable for producing single-profile roof panels. They have a single set of rolls and dies, allowing the production of panels with a uniform shape and thickness.
Double-Layer Roll Forming Machines
Double-layer roll forming machines can produce two different profiles simultaneously. These machines have two sets of rolls and dies, enabling the manufacturing of two distinct roof panel designs. They are ideal for projects requiring multiple profiles or when production efficiency is crucial.
Multi-Layer Roll Forming Machines
Multi-layer roll forming machines are the most versatile type, capable of producing three or more profiles simultaneously. These machines feature multiple sets of rolls and dies arranged in a stacked configuration. They are highly efficient for large-scale projects that require different panel profiles.
Factors to Consider When Choosing a Roof Panel Roll Forming Machine
When selecting a roof panel roll forming machine for your manufacturing needs, several factors should be taken into consideration. These factors will help ensure that you choose a machine that is compatible with your production requirements and offers the best return on investment. Here are the key factors to consider:
Material Compatibility
Different roof panel roll forming machines are designed to work with specific types of materials, such as galvanized steel, aluminum, or stainless steel. It is crucial to choose a machine that is compatible with the material you intend to use. Consider the material’s thickness, strength, and other characteristics to ensure that the machine can effectively process it.
Production Speed
The production speed of a roof panel roll forming machine plays a significant role in determining your manufacturing capacity. Evaluate the machine’s speed capabilities and consider your desired production volume. Choose a machine that can meet your output requirements without compromising on quality.
Machine Flexibility
Flexibility is essential, particularly if you anticipate manufacturing different roof panel profiles or accommodating future design changes. Look for a machine that offers easy adjustments and quick changeover capabilities. This will allow you to switch between different panel profiles efficiently and minimize downtime.
Cost and ROI Analysis
Consider the initial investment cost of the machine and assess its long-term return on investment (ROI). While it may be tempting to opt for a cheaper machine, it’s crucial to balance cost with quality and productivity. Evaluate the durability, reliability, and maintenance requirements of the machine to determine its overall value for your business.
After-Sales Support and Service
Choose a reputable manufacturer or supplier that provides excellent after-sales support and service. This includes technical assistance, spare parts availability, and maintenance training. A reliable support system ensures that your machine stays operational, minimizing downtime and maximizing productivity.
Steps in the Roof Panel Roll Forming Process
The roof panel roll forming process involves several steps, each contributing to the successful manufacture of high-quality panels. Understanding these steps will give you insight into the machine’s operation and the overall production process. Here are the key steps involved:
Material Loading
The process begins with loading the metal coil onto the machine. The coil is mounted on a decoiler, which feeds the material into the roll forming machine. Proper alignment and tension control are critical at this stage to ensure consistent material feeding throughout the process.
Forming Stations
The metal coil passes through a series of forming stations, where rolls and dies gradually shape the material into the desired roof panel profile. Each forming station applies specific bending, curving, or embossing actions to transform the flat coil into a formed panel. The number of forming stations depends on the complexity of the panel profile.
Cutting and Shearing
After the panel profile is formed, the machine incorporates a cutting or shearing mechanism to trim the panel to the required length. Precise cutting ensures uniform panel dimensions and eliminates excess material waste.
Stacking and Packaging
Once the panels are cut to size, they are conveyed to a stacking and packaging area. Stacking systems can be manual or automated, depending on the machine’s configuration and production volume. The stacked panels are then packaged and prepared for storage or transportation.
Maintenance and Care Tips for Roof Panel Roll Forming Machines
Proper maintenance and care are essential to ensure the longevity and optimal performance of your roof panel roll forming machine. Regular maintenance activities will help prevent downtime and costly repairs. Here are some maintenance tips to keep in mind:
Regular Cleaning and Lubrication
Clean the machine regularly to remove debris, dust, and accumulated residues. Lubricate moving parts, such as gears, bearings, and rollers, according to the manufacturer’s recommendations. Proper lubrication reduces friction and wear, ensuring smooth machine operation.
Inspection and Repair
Regularly inspect the machine for any signs of wear, damage, or misalignment. Address any issues promptly to prevent further damage or production disruptions. Keep spare parts readily available to facilitate quick repairs when necessary.
Operator Training
Train machine operators on proper operating procedures, safety protocols, and routine maintenance tasks. Well-trained operators can identify and address minor issues, ensuring efficient machine performance and reducing the risk of accidents.
Common Challenges and Troubleshooting Tips
While roof panel roll forming machines are designed for efficient and reliable operation, occasional challenges may arise. Here are some common challenges and troubleshooting tips to help you overcome them:
Material Jamming
Material jamming can occur if the coil feeding mechanism or forming stations are not properly adjusted. Check for obstructions or misalignment and readjust the machine accordingly. Regular cleaning and lubrication can also help prevent material jamming.
Misalignment and Skewness
Misalignment and skewness can lead to panels with uneven profiles or dimensions. Check the alignment of the forming rolls, guides, and cutting mechanisms. Make adjustments as necessary to ensure accurate panel formation.
Uneven Thickness or Width
Uneven panel thickness or width can result from improper roll pressure or worn-out rolls. Monitor the roll forming pressure and replace worn-out rolls promptly. Regularly calibrate the machine to maintain consistent panel dimensions.
Electrical or Mechanical Malfunctions
Electrical or mechanical malfunctions can occur due to component failure or improper wiring. Regularly inspect the machine’s electrical connections, motors, and control systems. Address any malfunctions immediately to prevent further damage and ensure operator safety.
Safety Precautions for Operating a Roof Panel Roll Forming Machine
Safety should be a top priority when operating a roof panel roll forming machine. Follow these safety precautions to protect operators and maintain a safe working environment:
Protective Gear and Clothing
Ensure that operators wear appropriate personal protective equipment (PPE), including safety glasses, gloves, ear protection, and steel-toe boots. Protective clothing should be worn to prevent entanglement with moving parts.
Proper Machine Guarding
Install adequate machine guarding to prevent accidental contact with moving components. This includes safety covers for forming stations, cutting mechanisms, and other hazardous areas.
Emergency Stop Systems
Equip the machine with easily accessible emergency stop buttons or switches. These systems should immediately halt machine operation in case of an emergency or potential danger.
Regular Safety Training
Provide comprehensive safety training to machine operators and maintenance personnel. Regularly conduct safety refresher courses to ensure everyone remains aware of best practices and potential hazards.
Future Trends and Innovations in Roof Panel Roll Forming
The field of roof panel roll forming continues to evolve, with ongoing advancements in technology and design. Some future trends and innovations to watch for include:
- Integration of automation and robotics for increased efficiency and productivity.
- Enhanced control systems with real-time monitoring and data analysis capabilities.
- Development of eco-friendly materials and sustainable manufacturing processes.
- Introduction of 3D printing technologies for rapid prototyping and customized panel designs.
As technology continues to advance, the roof panel roll forming industry will witness further improvements in speed, accuracy, and sustainability.
निष्कर्ष
A roof panel roll forming machine is an invaluable asset in the production of high-quality roof panels. Its efficiency, customization options, and cost-saving benefits make it an essential investment for manufacturers in the construction industry. By considering the factors discussed in this article and adhering to proper maintenance and safety practices, you can maximize the machine’s performance and ensure long-term success in panel manufacturing.
FAQs (Frequently Asked Questions)
1. How long does it take to set up a roof panel roll forming machine?
The setup time for a roof panel roll forming machine varies depending on the complexity of the panel profile and the operator’s experience. Generally, it takes a few hours to properly adjust the machine, including changing the rolls and dies, setting up the cut-off system, and fine-tuning the parameters for the desired panel dimensions.
2. Can a roof panel roll forming machine handle different thicknesses of materials?
Yes, most roof panel roll forming machines are designed to accommodate a range of material thicknesses. By adjusting the roll forming pressure and the gap between rolls, the machine can effectively handle different material thicknesses within its specified range.
3. Are there any safety precautions specific to operating a roof panel roll forming machine?
In addition to the general safety precautions mentioned earlier, there are a few specific precautions to keep in mind when operating a roof panel roll forming machine. These include:
- Avoiding loose clothing or jewelry that can get caught in moving parts.
- Ensuring that the machine is properly grounded to prevent electrical hazards.
- Regularly inspecting and maintaining the hydraulic or pneumatic systems to prevent leaks or malfunctions.
- Following lockout/tagout procedures when performing maintenance or repairs.
4. Can a roof panel roll forming machine produce panels with custom designs or patterns?
Yes, a roof panel roll forming machine can produce panels with custom designs or patterns. By incorporating additional roll sets, embossing rollers, or punch stations, the machine can create unique profiles, patterns, or perforations on the panels. This allows for greater design flexibility and customization.
5. How often should a roof panel roll forming machine undergo maintenance?
Regular maintenance is essential to keep a roof panel roll forming machine in optimal condition. It is recommended to follow the manufacturer’s maintenance schedule, which typically includes daily, weekly, monthly, and yearly tasks. Daily maintenance may involve cleaning and lubrication, while more extensive tasks like roll inspection or replacement may be done on a monthly or yearly basis. Regular maintenance helps prevent breakdowns, extends the machine’s lifespan, and ensures consistent panel quality.